摘要:针对目前动力电池热管理存在的问题,论文提出一种热管辅助的分离式电池热管理系统,并搭建了动力电池散热温度特性实验平台,对动力电池热管理系统进行了实验研究,分析该系统对电池组温度及温差的控制作用。分别进行了动力电池热管理系统在动力电池以1 C、3 C、4 C和5 C等恒流放电条件下,以及不同的“放电-充电”循环工况下的散热性能。结果表明,与其他冷却方法相比,该系统具有更合适的工作温度,能更好地降低电池组内部的温度不平衡。即使在5 C的极高放电率下,最大温差也可以控制在5 ℃以内,而且可以大大改善单体电池内的温度不平衡。特别是在长时间运行的情况下,各循环的最高温度远低于基于传统相变材料冷却模式,系统的可靠性和性能得到了很大的提高。
关键词:热管理系统;电动汽车;分离式;动力电池;相变材料;热管
在环境污染和能源短缺的双重压力下,新能源汽车(尤其是电动汽车)因其高效的驱动系统和绿色能源,逐渐成为传统燃油汽车的替代选择,成为各国汽车产业的重要发展方向[1]。但新能源汽车车用动力电池在运行过程中会产生大量热量,热量的积累导致电池运行温度迅速升高,严重时可能导致整个动力电池系统永久性损坏或发生热失控引发起火爆炸等严重事故[2]。有效的热管理系统可以改善电池的工作环境,使电池在最佳的温度内工作,保证汽车的行驶性能和行车安全。相变材料在电池热管理的应用上潜力巨大,受到越来越多研究者的关注[3]。虽然很多学者对基于相变材料热管理系统进行了设计和研究,但在目前基于相变材料的热管理系统设计中,如图1(a)所示,通常把相变材料直接填充至电池之间或者电池周围的空隙里[4],这种方式可能产生填充在电池之间的相变材料泄漏,且不适用于大尺寸的动力电池系统等难题。这些问题需要设计创新的基于相变传热介质的热管理系统来解决。本文利用多孔泡沫金属和相变材料制作复合相变材料,建立一种热管辅助的分离式电池热管理系统,并基于搭建的实验平台对动力电池热管理系统的性能进行了系统的实验探索,并与自然对流冷热管理模式、强制对流冷热管理模式和传统基于相变材料(Phase Change Material, PCM)热管理模式进行对比,研究所提出的系统在电池组温度及温差的控制方面的性能。最后,为了进一步研究电池组在长时间运行工况下热管理系统的性能和可靠性,进行了“放电-充电”循环试验。
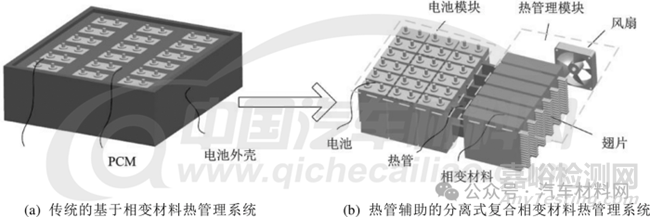
图1 传统电池组和分离式电池热管理系统图
1、 实验装置
1.1 电池组和热管理系统的搭建
图1(b)为设计实验室规模的电池组和热管理系统示意图,主要由电池组、热管、“泡沫铜-石蜡”复合材料、散热片和一个额外的风扇组成。其中电池组由18个容量为2.7 Ah的方形磷酸铁锂电池组成。热管理模块与电池组通过10根热管进行连接,热管的蒸发段夹在两个电池之间,冷凝器延伸到电池组外面与“金属泡沫-石蜡”复合相变材料紧密接触。通过这种方式,电池组中的热量被高效地传送到热管理模块,不需要将石蜡或其复合材料填充电池组内部。因此,可以最大限度避免由复合相变材料内导电物质引起的电池短路问题。为了减少热管与电池和泡沫金属材料之间的接触热阻,在其接触表面涂上一层高导热系数的导热胶,增强接触面处的热传递,因而在本研究中忽略接触热阻。以具有高潜热值的石蜡作为相变材料,利用热空气将固相石蜡熔化并渗透到泡沫铜孔隙中,制备“泡沫铜-石蜡”复合材料。泡沫铜中端安装有散热翅片和冷却风扇,必要时加强热管理模块与自然环境之间的对流传热,帮助释放相变材料的潜热。热管、石蜡、翅片、泡沫铜及其复合材料的物理性能如表1所示。
表1 热管、石蜡、翅片、泡沫铜及其复合材料的物理性能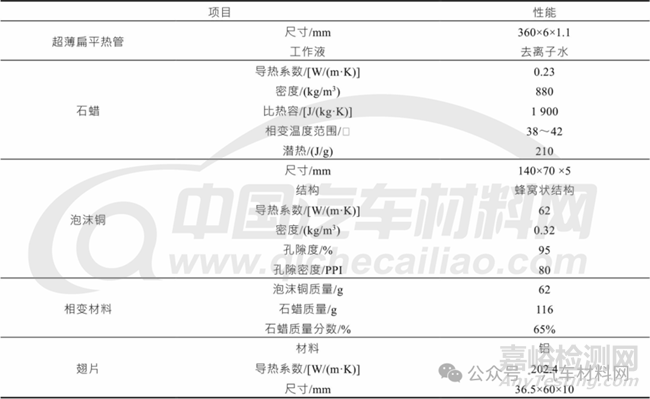
1.2 测试过程
为了评价所提出系统的热管理性能,进行了恒流放电单次实验和循环测试实验。如图1(b)小虚线方框所示,建立了一个有4个单体电池串联而成的电池组测量电池组的温度变化。在实验过程中,实验测试系统如图2所示,电池表面共安装36热电偶用于测量电池表面温度,1个额外的热电偶用于记录环境温度。温度数据通过数据采集仪每30 s采集一次并传输到计算机。高低温实验箱内的温度设置为30 ℃,用于模拟电池工作环境的温度。高性能电池检测系统用于控制电池模块在1 C、3 C、4 C和5 C倍率下进行放电。为了方便比较,表2给出了本文七种热管理模式的定义。
图2 实验系统图
表2 七种热管理模式的定义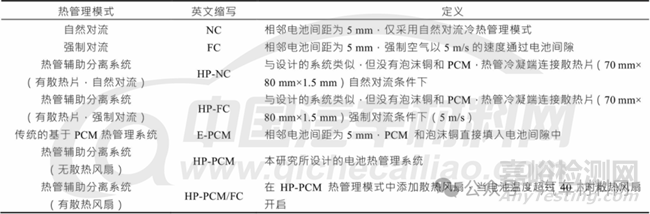
2、 实验结果与讨论
2.1 电池温度
图3显示了不同放电倍率下各热管理模式电池模块的最高温度随时间的变化。可以看到,当放电倍率增加到5 C时,自然对流和强制对流模式下的最高温度分别为65.8 ℃和56.2 ℃,远高于锂离子电池的最佳温度上限(约45 ℃)。在热管辅助分离系统(HP-NC和HP-FC)下冷热管理模式,由于热管的辅助,系统增加了自然对流和强制对流的散热面积,使这两种热管理模式下电池最高温度低于NC和FC模式,但散热效果不如基于传统PCM的热管理模式。对于本论文所提出的热管辅助分离式复合相变材料动力电池热管理系统(无散热风扇)热管理模式(HP-PCM),通过分离设计相变材料中的热量可以通过自然对流的方式逸散到自然环境中。因此,所提出的热管理模式可以进一步改善动力电池的工作热环境条件。在高达4 C和5 C的放电倍率下,电池的最高温度分别为43.8 ℃和48.5 ℃,超过散热风扇设定的运行温度40 ℃。此时,散热风扇的强制对流将相变材料中储存的热量散发到自然环境中,有效释放了相变材料的潜热,进一步提高了所提出的热管理系统的性能。如图3(c)和图3(d)所示,随着风扇的开启,电池组在4 C和5 C放电倍率下的最高温度分别为41.9 ℃和44.9 ℃,与基于传统PCM热管理模式(E-PCM)相比分别降低了4.5 ℃和7.6 ℃。结果表明,所提出的热管理系统为锂离子电池系统的温度控制提供了一种有效的解决方案,而辅助风扇的应用可以进一步提高热管理系统的性能。
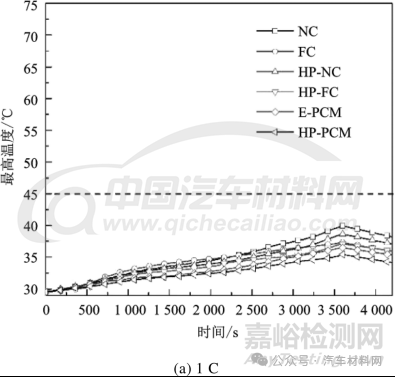
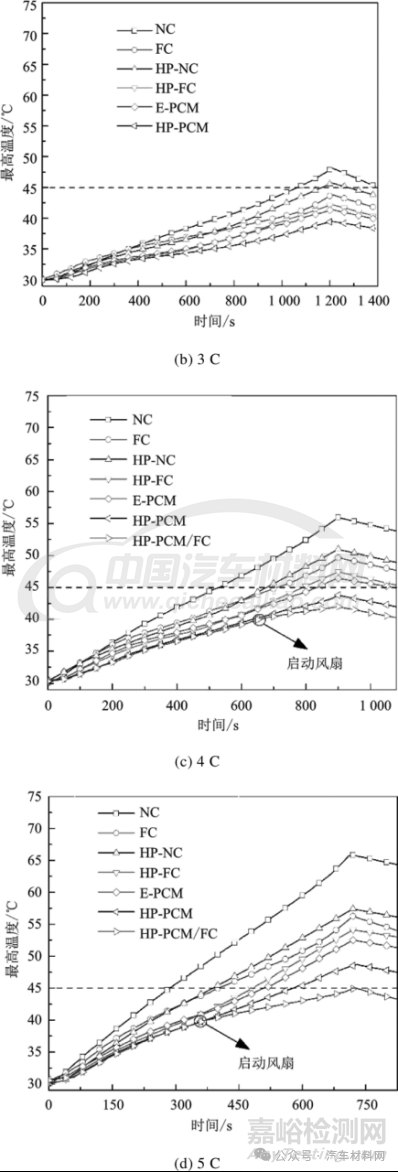
图3 不同放电倍率下不同热管理模式电池最高温度的变化情况
2.2 温度梯度控制
电池之间的温度分布不当也会降低电池模块中电池性能一致性,进而降低电池组的整体性能,有关研究表明,所有电池的温度必须保持在25~ 45 ℃的狭窄范围内,电池组中电池之间的最大温差应小于5 ℃[5]。图4显示了不同放电倍率下各热管理模式电池模块的最大温差,最大温差的计算公式如下:
∆Tmax,module=Tmax,module-Tmin,module (1)
式中,Tmax,module和Tmin,module分别为36个热电偶线测温点的最高温度和最低温度。从图4中可以看出,在低放电倍率下,7种热管理模式的最大温差无明显差异。在1 C放电倍率下,整个电池模块的最大温差均控制在1 ℃以内。随着放电倍率的增加,最大温差明显增大。在基于传统PCM的热管理模式(E-PCM)下,电池表面的热量传递主要取决于传导,而不是对流传热,当放电倍率为 3 C、4 C、5 C时,整个电池模块热管理模式的最大温差分别上升到2.2 ℃、3 ℃和4.2 ℃。在所提出的热管理系统(HP-PCM)中,电池产生的热量通过热管传递到外部环境,经相变材料吸收并储存热量。因而各电池表面的散热系数基本相同。在3 C、4 C和5 C放电倍率下,该系统整个电池模块的最大温差分别为2.1 ℃、2.7 ℃、3.6 ℃。与基于传统PCM热管理模式(E-PCM)相比,最大温差分别下降了0.1 ℃、0.3 ℃和0.6 ℃。即使在5 C的极高放电率下,整个电池模块的最大温差也可以控制在5 ℃以内(5 ℃被认为是电池模块内部最大温度偏差的上限)。在4 C和5 C的放电倍率下,散热风扇可以辅助散热,进一步降低电池的温度梯度,整个电池模块的最大温差分别为2.5 ℃和3.1 ℃。因此,所提出的热管理系统在控制整个电池模块最大温差方面具有较好的性能。
图4 不同放电倍率下电池的最大温差
2.3 循环测试
为了进一步分析所提出的热管理系统在电池组长时间运行工况下的热管理性能,进行了5个循环的1~5 C放电倍率的“放电-充电”循环试验。循环测试的充放电条件:首先将充满电的电池组以恒定的倍率(分别为1 C、3 C、4 C或5 C)放电,直到电压降至12 V;然后电池组以1 C倍率再次充满电,并开始下一次充放电循环测试,每组测试中电池组共进行5次放电充电循环。如图5(a)所示,在1 C放电倍率下电池组在两种热管理模式中均具有良好的散热性能。然而当放电倍率增加到3 C或更高时,可以看到两种热管理模式之间的热管理性能差异明显。另外,从图5(b)-图5 (d)可以看出,在随后的周期测试中E-PCM热管理模式下电池最高温度几乎不变。这些现象表明,对于E-PCM热管理模式,在循环测试第二次放电过程中所有石蜡已经完全融化,导致E-PCM热管理模式性能急剧下降,甚至失效,未能控制电池组的工作温度。HP-PCM热管理模式中,PCM散热模块是从电池组中分离出来的,分离设计可以有效地释放PCM的潜热,使电池组产生热量部分储存在相变材料中,部分通过相变材料无缝设计利用自然对流散失到环境中。因此,HP-PCM热管理模式可以为电池组在长时间运行条件下提供更有效的热管理。
另一方面,随着循环试验的进行,HP-PCM热管理模式中各循环的最高温度逐渐升高,这意味着系统中PCM的熔化率也在增加,因此,为了进一步提高系统的性能,可以在相变材料模块中使用一些额外的冷却方法。如图5(b)-图5 (d)所示,在3 C放电倍率第二个循环测试周期中加入散热风扇,可以辅助将电池温度从41.1 ℃、43 ℃、 43.7 ℃和44 ℃下降至40.5 ℃、41.5 ℃、41.9 ℃和42.2 ℃。随着放电倍率的增加,散热风扇在降低电池温度方面的性能逐渐提高,在4 C放电倍率下,5个循环周期温度分别下降了1.8 ℃、2.7 ℃、3.4 ℃、3.7 ℃和4 ℃,当放电倍率为5 C时,5个循环周期温度分别下降了3.9 ℃、5 ℃、6 ℃、5.9 ℃和5.5 ℃。因此,该电池热管理系统的分离设计可以很容易地与其他类型的散热方法结合使用,以进一步提高温度管理性能,特别是在长时间的高放电倍率工况下。
图5 不同放电倍率、不同热管理模式电池组在循环测试中的温度变化情况
3、 结论
利用实验室规模的电池组,在1 C、3 C、4 C和5 C恒流放电倍率和不同放电倍率的“放电-充电”循环工况下,对所提出的热管理系统进行了系统性能试验研究;并与自然对流、强制对流和基于传统PCM等热管理模式进行了对比。文章的主要结论如下:
1)在没有辅助风扇的情况下,在1 C、3 C、4 C放电倍率下电池组在所提出的热管理模式中最高温度均在45 ℃以下。虽然在极高的放电倍率下(如5 C放电倍率),电池组的最高温度高于所建议的最佳工作温度45 ℃,但与其他冷却方式相比,所设计的热管理系统提供了一个相对更优异的热管理性能。
2)在这些热管理模式中,所设计的电池热管理系统对电池组内温度分布的均温性控制效果最好。
3)所提出的电池热管理系统可以有效地释放相变材料的潜热,提高电池组在长时间运行工况下的热管理性能。在循环试验中,各循环的最高温度远低于传统基于PCM热管理模式,特别是在高放电率下。
4)辅助散热风扇的系统可以进一步提高所提出的热管理系统的性能,极大地改善电池的工作环境,特别是在长时间高放电倍率的工况下,为电池热管理的设计和优化提供理论指导。
参考文献
[1] 饶中浩.基于固液相变传热介质的动力电池热管理研究[D].广州:华南理工大学,2013.
[2] KIZILEL R,SABBAH R,SELMAN J R,et al.An Alter- native Cooling System to Enhance the Safety of Li-ion Battery Packs[J].Journal of Power Sources, 2009,194(2):1105-1112.
[3] ZHANG P,XIAO X,MA Z.A Review of the CompositePhase Change Materials:Fabrication,Characterization, Mathematical Modeling and Application to Perfor- mance Enhancement[J].Applied Energy,2016,43(12): 472-510.
[4] LAZRAK A,FOURMIGUÉ J F,ROBIN J F.An Inno- vative Practical Battery Thermal Management System Based on Phase Change Materials:Numerical and Experimental Investigations[J].Applied Thermal Eng- ineering,2018,128:20-32.
[5] LING Z,ZHANG Z,SHI G,et al.Review on Thermal Management Systems Using Phase Change Materials for Electronic Components,Li-ion Batteries and Pho- tovoltaic Modules[J].Energy,2014,31:427-438.
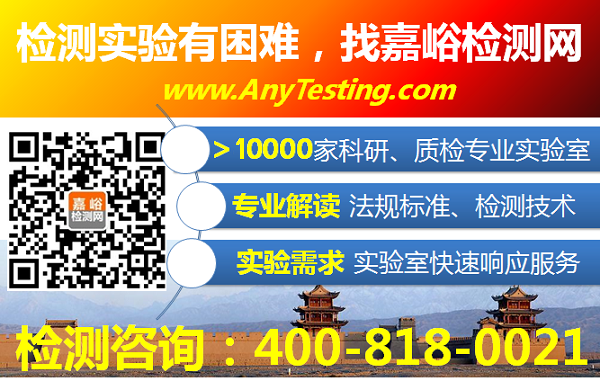