摘 要 汽车作为重要的交通工具,在家庭出行等方面发挥着重要的作用。现阶段,随着人们生活质量的提升和对生活品质的更高追求,其对汽车的性能等有了新的要求。为了满足大众的需要,汽车企业积极进行汽车设计与开发,不断地在材料、设计方式等方面狠下功夫。现如今,汽车轻量化成为汽车设计的主要方向,而汽车轻量化目标的实现必须要完成材料的创新,因此要在汽车车身结构构件开发的应用过程中积极寻找具有轻量化目标和质量化标准要求的材料。热塑性复合材料与传统的材料相比性能更加优越,且可以达到汽车轻量化目标,所以其在目前的汽车车身结构构件应用开发方面已有应用。文章就热塑性复合材料在汽车车身结构件上的应用开发进行分析,以期为相关学者提供参考。
关键词 热塑性复合材料;汽车车身结构构件;
在技术持续发展的大环境下,我国的汽车产业获得了飞速的发展。总结现阶段我国汽车产业的持续发展,其面临的主要问题为能源安全与节能减排。现如今,国家出台了一系列的政策与法规,目的是要对汽车的能耗以及排放指标等进行限制,而要真正地解决汽车能耗问题,还是要从汽车轻量化入手。碳纤维复合材料的机械性能十分优异,且其抗疲劳性能要明显地优于金属的密度条件,所以在汽车轻量化实践中碳纤维材料应该作为首选[1]。
对目前的市场进行总结,90%以上的汽车在使用碳纤维复合材料的时候利用的是热固性树脂体系,这类材料在后续回收利用等方面存在着问题,而热塑性碳纤维复合材料则可以很好地解决这一问题。连续纤维增强热塑性复合材料的机械性能更加的突出,且目前已经实现了成型。不过受到工艺特性的限制,一些特殊结构的成型要求还没办法满足。在现阶段的该问题解决中,主要采用的是注塑成型的方式,但是这种方式成型的制品机械性能并不理想。模压工艺和注塑工艺有各自的优势,如果将其进行结合,并以连续纤维增强热塑性复合材料作为骨架,然后通过注塑成型的方式来进行复杂结构的成型,这样,热塑性复合材料在汽车车身构件中的利用会更加的显著。
1、 热塑性复合材料
要在汽车车身构件设计开发的过程中充分利用热塑性复合材料,首先需要对热塑性复合材料有全面的认知和了解。就定义而言,所谓的热塑性复合材料指的是以热塑性树脂作为基体,以各种纤维为增强材料而制成的复合材料。对热塑性复合材料的类别划分进行分析,按照树脂基体和复合之后的性能,热塑性复合材料主要分为两大类:(1)高性能复合材料,其以优良纤维增强高性能热塑性树脂,比如碳纤维、芳纶纤维、聚苯硫醚等均属于高性能复合材料,这类材料的比强度和比模量较高,能够在200℃以上长期使用[2]。(2)通用型复合材料,其指的是以玻纤及制品增强一般通用的热塑性树脂,比如目前广泛使用的PP、PE、PVC 等均属于这一类材料。
在实践中要强调热塑性复合材料的有效利用,还需要对热塑性复合材料的特性进行了解。就目前的实践研究来看,热塑性复合材料具有6 大特性:(1)其密度小,强度高,机械性能更加优越。(2)具备性能可设计性。和热固性复合材料进行比较,热塑性树脂的种类更多,能够选择的区间更大,所以其具有更好的设计性。另外,热塑性复合材料的物理、化学性能可以基于具体的要求通过合理的材料选择和工艺利用来实现。(3)耐热性好。热塑性复合材料的耐热性一般维持在100℃左右,不过在用玻纤增强后热塑性材料的使用温度会极大地提升。现如今在实践中利用的高性能热塑性复合材料,其耐热能够达到250℃以上[3]。(4)耐化学腐蚀性。复合材料的耐化学腐蚀性和基体材料的特性是有密切关系的,耐腐蚀性比较好的热塑性树脂种类是比较多的,所以在实践中可以选择耐腐蚀性比较好的热塑性树脂作为基体材料,这样,热塑性复合材料的耐化学腐蚀性会显著提升。(5)电性能。复合材料的电性能与树脂基体、增强材料的性能有关,所以在实践中可以基于使用要求来进行性能设计。(6)加工性能。热塑性复合材料的工艺性能要明显地优于热固性复合材料,而且其能够实现多次成型,还可以实现废料的回收利用。
2、热塑性复合材料在汽车车身结构件上的应用开发
从上文分析的结果来看,热塑性复合材料的优势是十分突出的,其在汽车车身结构件上的应用开发势必会解决汽车轻量化问题,所以积极讨论热塑性复合材料的具体应用与开发,这对于实践问题的解决有积极的指导意义,以下是结合实践对热塑性复合材料的应用开发总结。
2.1 模压-注塑座椅横梁的选材设计
以某中型汽车为例进行分析,其车座的横梁主要由三部分构成,分别是前座椅前横梁、前座椅后横梁以及后座椅横梁。就前座椅后横梁为例进行分析,其主要构成为3 部分,具体为横梁本体、左侧加强件以及后侧的加强件。该零件的结构为传统钣金结构,即3个独立的钣金件被焊接在了一起,同时利用螺接的方式实现与座椅的连接,其是比较典型的车身梁类结构,其总质量为1.85kg。
对模压-注塑混合结构进行分析,其为了让模压层和注塑层之间的界面性能得到保证,在模压区域和住宿区域需要选用相同的树脂体系。对常用的一些热塑性树脂进行分析,部分材料的流行性是比较差的,其无法满足注塑成型过程中充模的具体要求,而且材料成本偏高,所以不再考虑范围[4]。对流动性能比较好的材料进行对比分析,PA6 所具有的性价比最高,而且在性能等各个方面均能够满足汽车零部件的实际需要,所以PA6 可以作为首选的树脂材料。
在增强纤维的选择方面,主要常用的有玻璃纤维与碳纤维。从成本角度进行考虑,玻璃纤维的价格比较低,不过其拉伸模量也比较低。相比于玻璃纤维,碳纤维的强度以及模量都非常高,不过其价格太高,所以其目前还不符合汽车成本控制的要求。对不同纤维增强复合材料的性能进行对比,玻纤增强PV6 的拉伸强度要远远高于原来的钣金件,但是其拉伸模量却不足钢材的三分之一。基于等刚度设计条件,将零部件的厚度增加至原来钣金厚度的3 倍以上,这虽然能够解决拉伸模量的问题,但是却无法满足轻量化需要。这个时候考虑碳纤维,一切问题可以迎刃而解[5]。需要注意的是,碳纤维的成本过高,所以也不是最优方案,可以考虑通过结构筋的形式进行零部件的性能提升,基于此,较大程度地替换连续纤维增强PV6 材料,可以达到减重降本的目标。基于具体的目标,在刚度条件满足的情况下将零部件的主材料选择为PV6,并混合部分碳纤维增强PV6 材料,这样可以使零部件的整体刚度获得提升。在材料确定之后利用玻纤-PV6 注塑筋做局部的刚度补充,这样可以将模压-注塑座椅横梁的选材方案进行确定。
2.2 模压-注塑座椅横梁的结构设计
对模压-注塑座椅横梁结构设计进行分析,其主要包括了集成设计、变厚度设计和连接结构设计,以下是具体的内容。
首先是集成设计。对原始的座椅横梁钣金件进行分析可知其主要为横梁主体、左侧加强件和右侧加强件,同时还包括了2 个焊接螺母以及1 个焊接加强版。对各个部件之间的连接方式进行分析,其为焊接。当改变为模压-注塑复合材料结构之后,原来需要单独制作的6 个零部件会变被简化为1 个零部件。在进行注塑的时候,螺母可以预埋在零部件上[6]。分析集成设计,横梁上部为模压结构,其主要的作用和荷载,同时与周围的零部件做连接。横梁的下部为注塑结构,其是对零部件刚度的一种补强。
其次是变厚度设计。对复合材料座椅横梁做变厚度设计,主要的做法是将在复合材料结构使用之后增加铺层的厚度,实现性能要求的满足。在横梁的中间区域,主要构成是横梁本体,其为单层钢板结构,刚度比较低,所以可以减少铺层的厚度,这样能够达到材料质量降低与成本控制的目的[7]。通过变厚度设计对复合材料横梁的总体质量进行剂量,其只有1.23kg,和原来的钣金件相比,减重达到了30%以上。
最后是连接结构的设计。在替换为复合材料之后,座椅横梁无法和地板以及周边的零部件做焊接,所以采用胶粘的方式。对胶粘这种连接方式进行分析,其不仅在满足零部件结构连接性能方面有比较好的效果,在复合材料与钢材的界面隔离方面也有不错的作用,其能够有效地降低CFRP 和钢材接触部分发生电化学腐蚀风险[8]。另外,胶层还能够发挥协同作用,这对于车体内部的噪声降低等有积极意义。
3、 热塑性复合材料在汽车车身结构件上的应用开发
热塑性复合材料在汽车车身结构件上的应用开发具体获得了哪些效果,还需要通过试验分析进行比较。就目前的部分试验结果来看,其效果主要体现在如下方面。
3.1 汽车开发的成本控制问题
在汽车研发的过程中,成本高居不下一直困扰着汽车企业。对汽车研发进行分析,在整个过程中,材料的选择和利用对成本控制有重要的影响。传统的钣金件结构在汽车成本控制方面有效果,但是钣金件的利用却难以满足目前的汽车设计轻量化目标。碳纤维复合材料在汽车生产中的利用不仅可以将汽车零部件的整体性能进行提升,还能够实现汽车轻量化目标,但是碳纤维复合材料的成本过高,超过了企业的成本控制标准[9]。基于汽车成本控制和轻量化目标的实现,强调热塑性复合材料的利用,并重视模压-注塑成型方式的具体利用,这样,在一般的热塑性复合材料中进行少量的碳纤维增加便可以增强零部件的整体性能,同时还可以实现轻量化目标。可以说,热塑性复合材料在汽车成本控制方面的效果是显著的。
3.2 汽车性能效果
对利用热塑性复合材料设计开发的汽车车身结构件的具体性能进行检测,从检测的结果来看,结构件的各方面性能和钣金件的各方面性能存在着比较大的差异,而且明显是利用热塑性复合材料设计开发的汽车车身结构件性能更加优越,这说明热塑性复合材料的优势是非常明显的,而且其产品的性能优势也是非常显著的,这为热塑性复合材料在汽车工业中的广泛推广和利用打下了坚实的基础[10]。
3.3 材料处理方面
在汽车车身结构件生产加工的过程中,受工艺等影响,不可避免地会出现一些废弃材料。这些废弃材料如果能够实现有效回收和利用,那么其便可以“变废为宝”。对热塑性复合材料的具体使用进行分析,这类材料和热固性复合材料相比,其固化周期更短,而且更容易收集,所以在实践中,热塑性复合材料能够实现集中的回收再利用,对于解决废弃物等问题有积极意义,这对于汽车企业的成本控制工作也有显著效果[11]。
综上所述,现阶段的试验表明热塑性复合材料的性能是十分优越的,所以其在交通、航天等领域有着十分重要的应用。结合目前的交通行业发展实践,立足于汽车的轻量化目标实现对热塑性复合材料的开发和利用,尤其是在汽车车身结构件设计和开发的过程中,强调热塑性复合材料的利用,并对比热塑性复合材料的实际应用效果,这可以为材料的持续推广和使用提供参考与指导,从而使热塑性复合材料的应用价值获得更好的发挥。
参考文献:
[1] 傅刚辉.连续纤维增强热塑性复合材料生产工艺及应用进展[J].合成树脂及塑料,2022,39(05):74-76,81.
[2] 高亮,贾伟,石峰晖,等.反气相色谱法测定聚醚醚酮的表面性质及在提升热塑性复合材料层间性能中的应用[J/OL].复合材料学报,2022,40(0):1-12.
[3] 冯冰涛,王晓珂,张信,等.连续碳纤维增强热塑性复合材料制备与应用研究进展[J].中国塑料,2022,36(07):165-173.
[4] 周长汶,咸家玉,王培毅,等.短切纤维不同短切长度在热塑性复合材料中应用研究[J].玻璃纤维,2022(03):30-33.
[5] 马全胜,李俊含,田思戗.热塑性复合材料的成型工艺及其在航空器中的应用[J].化工新型材料,2022,50(06):263-266,271.
[6] PEGGY MALNATI.短切碳纤维增强配混料扩大了热塑性复合材料的应用范围[J].现代塑料,2022(01):34-36.
[7] 刘彬,安卫龙,倪楠楠.国外热塑性复合材料工程应用现状[J].航空制造技术,2021,64(22):80-90.
[8] 段瑛涛,王智文,栗娜,等.热塑性复合材料在汽车车身结构件上的应用开发[J].汽车工艺与材料,2020(04):14-18.
[9] 李三平,杨正.连续碳纤维增强热塑性复合材料的性能优势及应用举例[J].中国新技术新产品,2019(20):64-65.
[10] 谌广昌,姚佳楠,张金栋,等.高性能热塑性复合材料在直升机结构上的应用与展望[J].航空材料学报,2019,39(05):24-33.
[11] 张超,黄勇.聚丙烯腈基碳纤维增强热塑性复合材料成型工艺及应用[J].医药工程设计,2021,42(01):59-63.
作者:蔡伟达1,周 松2,付延涛1,陆 禺1(1.无锡瑞来新材料科技有限公司,江苏 无锡 214000; 2.西北工业大学民航学院,江苏 太仓 215400)
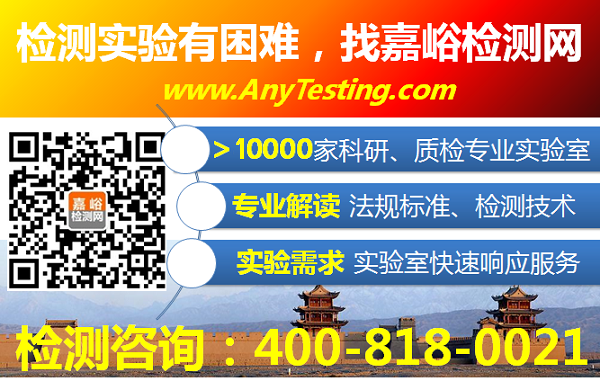