摘 要:为了实现汽车覆盖件轻量化,以某品牌汽车后座下内板为例,通过铝代钢完成轻量化设计,并进行冲压成形优化。采用等刚度和等强度完成铝合金板料代替钢板料校核,质量由1.24 kg减少至0.57 kg,实现了轻量化设计;采用正交实验完成变压边力、模具间隙、摩擦因数和冲压速度等4个因素对零件成形质量的影响分析,确定了最优工艺参数组合,并通过仿真实验验证工艺参数的有效性。该方案能够为汽车企业在覆盖件轻量化和成形质量优化方面提供一定的参考。
前言
随着汽车工业的大力发展,世界上汽车保有量不断增加,以之带来的汽车尾气排放和能源损耗越来越严重,给环境和能源带来严重的影响[1]。近年来,环保部门制订了一系列汽车节能环保标准,致力于汽车工业良性发展。据相关研究表明,汽车在行驶时能源消耗的80%是汽车车身质量,由此可知汽车轻量化是减少汽车能耗的重要途经[2-3]。目前,汽车轻量化主要有车身结构优化和汽车零件材料优化两种方法,汽车材料优化是汽车轻量化发展的趋势[4-5]。在材料优化中,铝合金材料具有轻质和节能的效果,同时也可以提高汽车的舒适性和安全性,所以在汽车轻量化中得到大量运用[6-8]。汽车覆盖件是汽车的重要组成部分,约占汽车总质量的40%[9],因此,覆盖件轻量化设计是汽车轻量化设计中一项重要的部分。本文以某品牌汽车后座下内板为例,对其进行轻量化设计和成形工艺参数优化。
1、 某汽车后座下内板铝代钢轻量化设计
1.1 轻量化设计的评价准则
汽车覆盖件轻量化设计的评价准则是通过结构优化或材料优化后,零件的性能与轻量化前一致或者更强。对于受力较大的汽车覆盖件或结构件在设计时需要确保足够的强度和刚度。后座下内板属于非对称、非标准件,其强度和刚度通过施加相同的位移约束和集中载荷进行评价,通过对加载点的位移及零件上的最大应力进行比较。零件的刚度I可通过公式(1)确定,零件的强度Q可通过应力分布公式(2)确定。

(1)
(2)式中:F为载荷,kN;x为最大位移,mm;A为面积,mm2。
1.2 基于等强度/刚度的铝代钢轻量化设计
图1为某品牌汽车后座下内板的设计图,原设计材料为冷轧钢板,材料牌号为B450LA,设计厚度为1 mm,本次轻量化目标材料为铝合金板,材料牌号为AA6009。原材料和目标材料的力学参数如表1所示。
表1 原材料与目标材料的力学参数
Tab.1 Mechanical parameters of raw materials and target materials
图1 某品牌汽车后座下内板的设计图
Fig.1 Design drawing of the lower rear seat inner panel of a brand car
使用目标材料AA6009代替原材料B450LA时,为保证零件的强度及刚度不发生变化,通过对强度和刚度进行校核确定目标材料的厚度。
1)等刚度的铝化轻量化设计是从弯曲刚度考虑零件的刚度,铝合金板材厚度按式(3)计算可得1.40 mm。
(3)式中:dAl为铝合金板料的厚度,mm;dst为钢板料的厚度,mm;Est为钢板料的弹性模量,GPa;EAl为铝合金板料的弹性模量,GPa。
2)等强度的铝板轻量化设计是从弯曲强度考虑零件的强度,铝合金板材厚度按式(4)计算可得1.34 mm。
(4)式中:σst为钢板料的屈服强度,MPa;σAl为铝合金板料的屈服强度,MPa。
由上述钢度和强度校核可知,铝合金AA6009厚度分别为1.40 mm和1.34 mm,为了同时满足刚度和强度要求,取厚度为1.40 mm。通过UG软件对两种不同材料的零件质量进行计算,采用钢为坯料的汽车后座下内板质量为1.24 kg,采用铝合金为坯料后座下内板质量为0.57 kg。由此可见,虽然零件由原来的设计厚度1.00 mm增加到1.40 mm,但由于铝的密度小于钢的密度,采用铝代钢后零件的质量并未增加,反而减轻了质量,实现了轻量化优化。
2、 汽车后座下内板铝合金冲压成形质量控制
2.1 有限元模型创建
将后座下内板设计模型导入Dynaform,通过Dynaform的模面工程确认冲压方向、完成工序补充面、压料面和实体拉延筋,并创建凹模模型,如图2所示。通过Dynaform的工具模块和坯料工程完成有限元模型创建,模型包括凹模、突模、压边圈和板料,如图3所示。
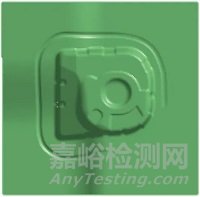
图2 后座下内板凹模模型
Fig.2 Rear seat lower inner plate concave die model
图3 后座下内板有限元模型
Fig.3 Finite element model of rear seat lower inner plate
2.2 成形优化方案设计
铝合金件的成形质量受模具结构、工艺参数及环境因素的影响,其中工艺参数在生产过程中更容易调整,是汽车覆盖件成形质量优化首选方案。工艺参数包括压边力、冲压速度、模具间隙和摩擦因数等参数。压边力在零件成形中起着重要的作用,过大的压边力会增加板料流动的阻性,造成板料发生开裂;而过小的压边力,则会增加材料的流动性,造成板料发生折皱。由于后座下内板形状复杂,且铝合金材料弹性模量较小,采用传统的恒定压边力无法满足成形质量要求,因此,本实验采用变压边力对零件成形质量进行优化。
选取变压边力、模具间隙、摩擦因数和冲压速度作为正交实验因素,以最大减薄率、最大增厚率和最大回弹量作为评价目标,构建4因素3水平正交实验,如表2所示。
表2 正交试验因素水平表
Tab.2 Table of orthogonal test factor level
2.3 实验结果分析
表3为根据正交实验原理设计L9(34)正交实验方案,并通过有限元仿真对最大减薄率、最大增厚率和最大回弹量结果的统计表。从表3可以看出,最大减薄率为8.25%~9.56%,均符合最大减薄率小于10%的设计要求;最大增厚率为3.92%~6.77%,方案3至方案6的最大增厚率超过最大增厚率小于5%的设计要求;最大回弹量为0.98~1.73 mm,方案4至方案6的最大回弹量超过最大回弹量小于1.5 mm的设计要求。
表3 正交试验结果
Tab.3 Orthogonal test results
极差分析是判断实验因素对评价目标影响程度的方法之一,广泛应用于正交实验分析中。表4、表5和表6分别是对最大减薄率、最大增厚率和最大回弹量进行极差分析的结果。从表4可知,影响汽车后座下内板的最大减薄率主次因素为:变压边力>模具间隙>冲压速度>摩擦因数,以最大减薄率为优化目标的最优工艺参数为Λ型变压边力,模具间隙1.44 mm,冲压速度1 000 mm/s,摩擦因数0.15。从表5可知,影响影响汽车后座下内板的最大增厚率为:变压边力>冲压速度>模具间隙>摩擦因数,以最大增厚率为优化目标的最优工艺参数为递减型变压边力,冲压速度1 000 mm/s,模具间隙1.44 mm,摩擦因数0.13。从表6可知,影响汽车后座下内板的最大回弹量主次因素为:变压边力>冲压速度>模具间隙>摩擦因数,以最大回弹量为优化目标的最优工艺参数为递减型变压边力,冲压速度1 000 mm/s,模具间隙1.40 mm,摩擦因数0.13。
表4 最大减薄率的极差分析
Tab.4 Range analysis of maximum thinning rate
表5 最大增厚率的极差分析
Tab.5 Range analysis of maximum thickening rate
表6 最大回弹量的极差分析
Tab.6 Range analysis of maximum rebound
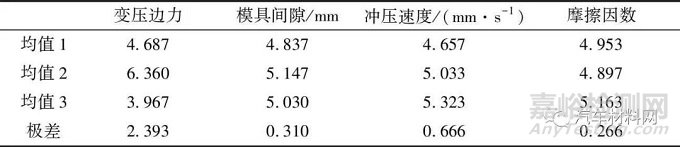
2.4 工艺参数多目标优化
由上述分析可知,根据不同评价目标的最优工艺参数组合不一致,为了使零件的最大减薄率、最大增厚率和最大回弹量同时达到最佳状态,需要对工艺参数进行多目标优化。根据零件最大减薄率≤10%、最大增厚率≤5%、最大回弹量≤1.5 mm的设计要求及正交试验因素,建立多目标优化模型如式(5)所示。利用Design-Expert软件的Taguchi实验将正交实验和多目标优化模型进行多目标求解,获得不同期望值的参数组合,如表7所示。表7中期望值最大参数组合为最优参数,获得最优工艺参数组合为:Λ型变压边力,模具间隙1.40 mm,冲压速度1 000 mm/s,摩擦因数0.11。
表7 Design-Expert多目标优化结果
Tab.7 Multi-objective optimization results of Design-Expert
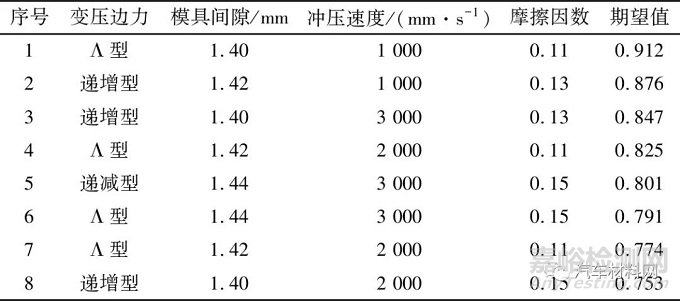
式中:h1为最大减薄率,%;h2为最大增厚率,%;c为最大回弹量,mm。
2.5 最优工艺参数成形仿真
将最优工艺参数通过dynaform软件进行成形仿真和回弹分析,获得零件成形极限图(图4)、零件修边后的厚度分布图(图5)及零件修边后的回弹分布图(图6)。从图4可以看出,零件绝大部分区域处于安全状态,有极少部位处于折皱趋势,零件整体成形质量较好,符合设计要求。从图5可以看出,零件最小厚度为1.271 mm,最大厚度为1.460 mm,计算得最大减薄率为9.21%,最大增厚率为4.23%,2个评价指标均在零件的设计允许范围内。从图6可以看出,零件回弹主要发生在零件边缘区域,最大回弹量位于左下角区域,最大回弹量为1.442 mm,未超过1.5 mm,符合零件的设计要求。
图4 零件成形极限图
Fig.4 Part forming limit diagram
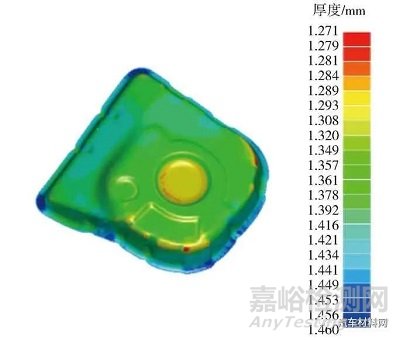
图5 零件厚度分布图
Fig.5 Part thickness distribution diagram
图6 零件回弹分布图
Fig.6 Part rebound distribution diagram
3、 结论
本文通过等钢度和等强度完成某品牌汽车后座下内板铝合金板材代替钢板材,质量由原来的1.24 kg减少至0.57 kg,有效实现了轻量化设计。通过正交实验和极差分析,分别获得影响最大减薄率、最大增厚率和最大回弹量的工艺参数主次关系,并完成工艺参数多目标优化,获得最优工艺参数组合。将最优工艺参数进行仿真实验,实验表明该零件成形质量良好,各指标均符合设计要求,验证了方案的可性性。本文的设计方案能够为企业在生产和设计中提供参考。
参考文献:
[1] 姜大乾.汽车尾气排放污染及控制处理研究[J].内燃机与配件,2021(19):171-172.
[2] FRANK C.Current trends in automotive lightweighting strategies and materials[J].Materials,2021,14(21):6631.
[3] 韩友国,刘向阳,吴洪涛,等.电动汽车前舱盖轻量化设计研究[J].汽车零部件,2022(7):5-8.
[4] 张娜,李海鹏,葛广跃,等.车身轻量化设计方法及应用[J].汽车实用技术,2022,47(10):179-183.
[5] 杨升,王佳,陈奇锋,等.商用汽车车桥轻量化设计思路与研究[J].汽车实用技术,2021,46(18):83-85.
[6] 胡珺辉.中美汽车轻量化技术对比分析与中方策略研究[D].武汉:华中科技大学,2019.
[7] 张欣,叶琳,冯薇丽,等.轻量化材料在商用车白车身的应用[J].汽车实用技术,2022,47(15):195-198.
[8] 张凯,苏小平,周大双.某铝合金后副车架的分析与轻量化研究[J].重庆理工大学学报(自然科学),2022,36(7):102-108.
[9] 黄娟,黄波,乔小兵,等.变形铝合金在汽车轻量化中的应用及挑战[J].汽车工艺与材料,2022(9):15-18.
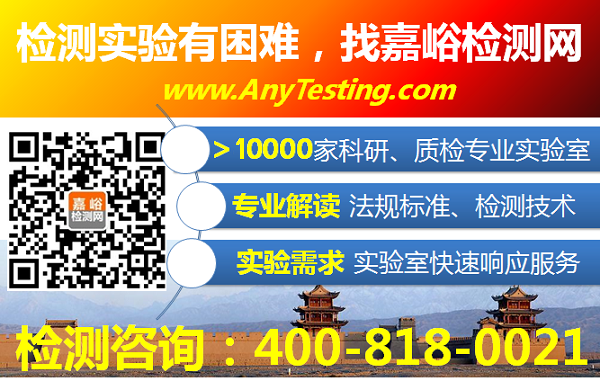