1、FMEA的由来和历史
FMEA(Failure Modes and Effects Analysis)是一种系统性的方法,用于识别和评估系统、产品或流程中的潜在故障模式和它们的影响。FMEA的发展可以追溯到20世纪20年代,最早是在军事和航空工业领域出现的,但它在不同行业中的使用逐渐扩展开来。
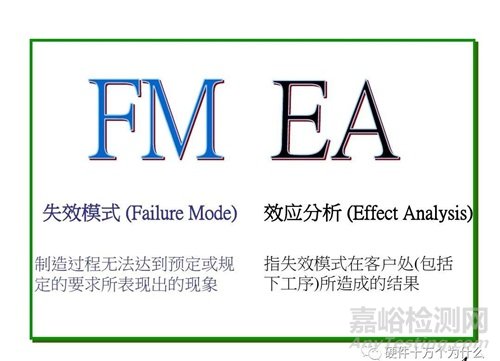
50年代初,美国第一次将FMEA思想用于一种战斗机操作系统的设计分析;
60年代中期,FMEA技术正式用于航天工业(Apollo计划);
1976年,美国国防部颁布了FMEA的军用标准,但仅限于设计方面。
70年代末,FMEA技术开始进入汽车工业和医疗设备工业。
80年代初,进入微电子工业。
80年代中期,汽车工业开始应用过程FMEA确认其制造过程。
1988年,美国联邦航空局发布咨询通报要求所有航空系统的设计及分析都必须使用FMEA。
1991年,ISO-9000推荐使用FMEA提高产品和过程的设计。
1994年,FMEA又成为QS-9000的认证要求。
以下是FMEA的发展历史的概要:
军事应用:FMEA最早是在美国军事领域应用的。它最初是在20世纪40年代末和50年代初,由美国军方的可靠性工程师和分析师开发和使用的。军事行业需要高度可靠的装备和系统,以确保战场上的效能和士兵的安全,因此FMEA被用于帮助识别和减轻潜在的故障风险。
航空航天应用:FMEA的早期应用也可以追溯到航空航天工业,特别是在美国国家航空航天局(NASA)的项目中。NASA使用FMEA来评估太空任务中的飞行器和系统的可靠性。
工业和汽车行业:FMEA的应用逐渐扩展到工业制造和汽车制造等领域。这些行业也面临着高度竞争和质量要求,因此FMEA成为了一种有用的工具,用于提高产品的可靠性和质量。
标准化和普及:FMEA方法逐渐标准化,并在不同行业中广泛传播。不同行业和标准组织制定了特定的FMEA标准和指南,以确保一致性和最佳实践。
我们做FMEA的目的是:
能够容易、低成本地对产品或过程进行修改,从而减轻事后危机的修改。
找到能够避免或减少这些潜在失效发生的措施;益处显而易见:
指出设计上可靠性的弱点,提出对策
针对要求规格、环境条件等,利用实验设计或模拟分析,对不适当的设计,实时加以改善,节省无谓的损失
有效的实施FMEA,可缩短开发时间及开发费用
FMEA发展之初期,以设计技术为考虑,但后来的发展,除设计时间使用外,制造工程及检查工程亦可适用
改进产品的质量、可靠性与安全性
总的来说,FMEA的发展是由于对产品和系统可靠性、安全性和质量的不断追求,以及对潜在故障和风险的关注。它的应用范围逐渐扩展,成为许多领域中质量管理和风险管理的重要工具。不同行业和组织根据其需求和要求继续发展和改进FMEA方法。
FMEA是“Failure Modes and Effects Analysis”的缩写,意为故障模式和影响分析。它是一种系统性的方法,广泛应用于各个行业,包括工程、制造业、医疗保健等,用于识别和优先考虑系统、流程或产品中潜在的故障模式。FMEA的主要目的是积极评估和减轻风险,以提高产品或流程的可靠性和安全性。
2、FMEA的流程
定义范围:确定要分析的系统、流程或产品,并为FMEA研究设定边界。
组建跨职能团队:组建一个成员来自不同领域专业知识的团队,以确保进行全面的分析。
识别组件和功能:列出正在分析的系统或流程的所有组件或功能。
识别故障模式:对于每个组件或功能,识别所有可能的故障模式。故障模式是组件或功能可能发生故障的方式。
确定影响:对于每个故障模式,评估对系统、流程或产品的潜在影响。考虑每个故障的直接后果和下游后果。
分配严重性评分:为每个故障模式的影响分配严重性评分。通常采用一个评分标尺(例如,1到10),较高的数字表示影响更严重。
识别原因:确定导致每个故障模式的根本原因或机制。了解原因有助于制定有效的预防措施。
分配发生率评分:估计每个故障模式发生的可能性。再次使用评分标尺(例如,1到10),较高的数字表示发生可能性更高。
分配检测率评分:评估在故障模式达到客户或产生重大影响之前能够检测到的可能性。使用评分标尺(例如,1到10),较高的数字表示检测能力较低。
计算风险优先数(RPNs):为每个故障模式的严重性、发生率和检测率评分相乘(RPN = 严重性 x 发生率 x 检测率)。这有助于确定哪些故障模式需要立即关注。较高的RPN表示更高的优先级。
优先考虑行动:集中关注RPN最高的故障模式。制定和优先考虑减轻这些风险的行动计划,考虑成本效益、可行性和资源等因素。
实施改进:将建议的行动付诸实践,以降低故障模式的风险。
审查和监控:持续审查和监控FMEA结果以及已实施行动的有效性。根据需要进行调整。
FMEA是风险管理和质量改进的有价值工具。它帮助组织在设计或流程规划阶段及早识别和解决潜在问题,最终提高产品的可靠性和安全性。
3、对电路做FMEA为什么觉得低效且效果不好
对电路进行FMEA(故障模式和影响分析)可能出现效率低和效果不佳的情况,这可能是由于以下一些原因造成的:
复杂性和规模:电路通常非常复杂,包含许多元件和互相关联的部分。在大规模电路中,识别潜在的故障模式和评估它们的影响可能非常耗时,并且难以捕捉所有可能的情况。
缺乏历史数据:在某些情况下,可能缺乏足够的历史数据来支持准确的FMEA分析。这可能导致基于猜测或假设进行评估,从而影响了分析的质量。
难以预测性能:电路的性能受到许多因素的影响,包括环境条件、电源变化等。这些因素可能在FMEA分析中难以准确地建模和预测。
复杂的故障模式:电路中的故障模式可以非常复杂,有时很难确定哪些故障可能会发生,以及它们的影响如何传播。这增加了FMEA的挑战性。
缺乏标准化:与其他行业相比,电路领域可能缺乏标准化的FMEA方法和工具。这可能导致不一致性和不适应的分析方法。
专业知识不足:有效的FMEA需要具备相关领域的专业知识和经验。如果团队成员缺乏必要的背景知识,分析的质量可能会受到影响。
过度谨慎:有时,在电路FMEA中可能会出现过度谨慎的情况,即过多关注较小的潜在故障,这可能导致资源浪费和不必要的成本。
为了提高电路FMEA的效率和效果,可以考虑以下方法:
集成自动化工具:使用计算机辅助工具来加速故障识别和影响分析,以处理大规模电路。
使用历史数据:如果可用,利用过去的故障数据和性能信息来支持分析。
增强专业知识:确保FMEA团队具备足够的专业知识和经验。
简化和优化过程:聚焦关键组件和最有可能发生严重故障的部分,以提高分析的实际价值。
与其他方法结合:考虑将FMEA与其他可靠性工程技术和质量管理方法结合使用,以获取更全面的信息。
最重要的是,FMEA应该被视为一个持续改进的过程,而不仅仅是一次性的任务。不断审查和更新FMEA分析以反映新的信息和经验可以帮助改进电路的可靠性和性能。
4、关于FIT故障注入测试
FIT故障注入测试通常被用作检验和验证FMEA(Failure Modes and Effects Analysis)的测试方法。FIT测试的主要目的是确保FMEA分析的准确性和系统的可靠性。
具体来说,FIT测试涉及故意向系统或组件注入故障、错误或异常,以验证系统是否能够正确识别、处理和应对这些故障情况。这些故障注入可以是软件错误、硬件故障、通信问题等。通过这种方式,FIT测试可以用来验证FMEA中识别的潜在故障模式和其影响,以及系统是否按照预期处理这些故障。
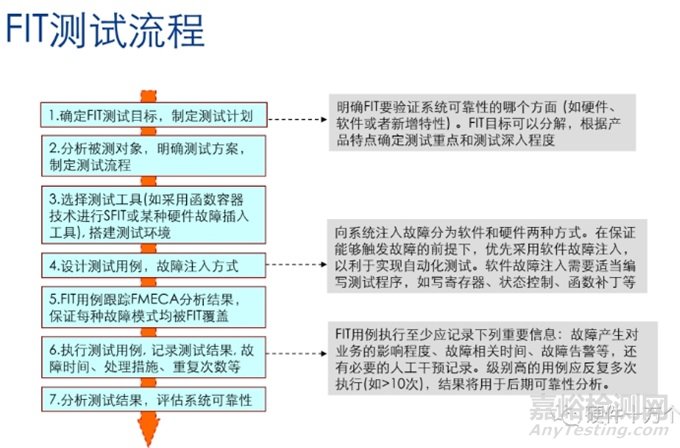
FIT测试的结果可以用来确认FMEA分析中的假设和估算是否准确,并验证系统是否满足可靠性和安全性要求。因此,FIT测试是FMEA的一种补充,用于确保FMEA分析的可信度,并确保系统在面对实际故障情况时的性能符合预期。
总之,FIT故障注入测试是一种有助于验证FMEA分析的有用方法,帮助企业确保其产品或系统在实际应用中的可靠性和安全性。
通过FMEA的设计过程中,仔细思考FIT测试的方法作为验收手段,是FMEA有效落地的重要手段。
5、FMEA如何执行
FMEA(Failure Modes and Effects Analysis)的基本思想包括"遍历性"和"系统性":
遍历性(Exhaustiveness):
遍历性是指FMEA的分析过程应该尽可能详尽地考虑所有可能的故障模式和其潜在影响。这包括对系统、产品或流程中的各个组件和功能进行全面的审查,以确保没有潜在问题被忽略。
系统性(Systematic):
系统性是指FMEA应该是一个有条不紊、有组织的方法,采用系统性的步骤来执行。这包括明确定义范围、组建跨职能团队、识别故障模式、评估影响、分配严重性、原因分析、发生率评估、检测率评估、风险计算等一系列有序的步骤。
通过遍历性和系统性,FMEA的目标是确保所有可能的故障模式都得到考虑,并且它们的风险和影响得到准确评估。这有助于组织识别和解决潜在的问题,降低故障风险,提高产品、系统或流程的可靠性和安全性。
总之,FMEA的基本思想是通过全面地、系统性地审查和评估潜在故障模式来预防和减轻潜在问题。这使得FMEA成为了质量管理和风险管理中的强大工具。
那么这两点在硬件设计的过程中是如何体现的呢?
FMEA的分析方法:
硬件法,从硬件的角度,对每个器件管脚输出分别去考虑故障模式、故障影响、检测补偿措施。(因为我们遍历了每一个器件、每一个器件的每一个管脚,所以这里体现了遍历性)
功能法,每个产品可以完成若干功能,而功能可以按输出分类。这种方法将输出一一列出,并对它们的故障模式进行分析。对应系统级、单板级分析。(此处按照功能和场景,对故障模式分别进行遍历和分析)。
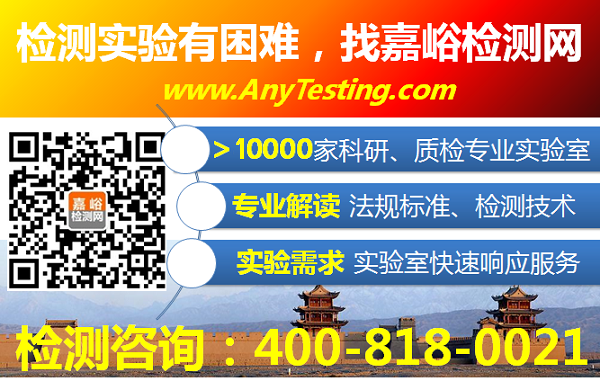