摘要:从纯电动汽车的续航里程理论计算公式着手,得出续驶里程与电池特性、电机、电控系统效率、整车设计参数,以及附件能量消耗有直接关系;然后结合AMESim仿真软件理论计算和台架数据验证,对微型纯电动汽车各关键因素如电池、电驱系统效率、整车设计数等参数进行续航敏感度分析,得出各项因素对续航的具体影响值;最终基于当前行业内的技术普及水平,提出了具有高性价比的微型纯电动汽车提升续航的技术路径,用于指导现阶段微型纯电动汽车续航里程性能的快速开发,缩短开发周期和降低开发成本。
关键词:续航里程;动力电池;电驱系统;控制策略
近年来,由于能源紧缺危机加剧,且面临比较严重的环境污染问题,我国相继推出了一系列鼓励发展新能源汽车的政策,新能源汽车尤其是纯电动汽车飞速发展。但是随着纯电动汽车的增多,充电基础设施建设、快充技术等问题日益显现,纯电动汽车续航里程的高低直接影响客户的主观体验和购买需求。对企业来说,若采用增加电池电量的方式可提高续航里程,单车成本也会水涨船高,对于价格敏感的微型纯电动汽车而言反而降低了产品核心竞争力。本文从整车、电池、电机、控制策略四个方面,应用仿真软件对影响续航里程的各项因素进行定量分析,分析在相同续航里程下的低成本关键技术,解决成本和性能这一主要矛盾。
1、 续航里程
1.1 续航里程概念
续航里程是指汽车在动力蓄电池完全充电的状态下,以一定的行驶工况连续行驶的最大距离[1]。为了评价电动汽车的续驶里程,我国已制定了电动汽车评价国家标准《电动汽车能量消耗量和续驶里程试验方法》(GB/T 18386)。
1.2 续航里程理论计算
根据汽车理论,当纯电动汽车以速度v0等速行驶时,假设驱动系统参数都为稳态,纯电动汽车的续驶里程可按式(1)计算。此外,在一定工况内或者用户驾驶时,汽车还会存在加速、减速和等速工况,从而导致式(1)分母项需要额外增加加速阻力和坡道阻力。
(1)
式中,S为续驶里程,m;CZ为电池组容量,Ah;UZ为电池组电压,V;ξsoc为蓄电池放电深度,%;ηd为蓄电池放电效率,%;ηe为电机及控制器整体效率,%;ηt为传动系统效率,%;ηa为汽车附件能量消耗比例系数;v0为车速,km/h;m为整备质量,kg;g为重力加速度,取9.8 m/s2;f为滚阻系数;Cd为风阻系数;A为迎风面积,m2。
2、 续航里程影响因素
从式(1)可以得出,续驶里程与电池特性、电机电控系统效率、整车设计参数,以及附件能量消耗有直接关系,下文将对各项关键参数进行详细分析。
2.1 提高动力电池电量
影响续航里程最主要的因素是动力电池,包括电池组容量和电压、放电深度和放电效率。电池总电量与汽车续航里程成正比,电池放电效率、放电深度越高,电池可用电量越多,汽车续航里程也越大。另一方面,增加电池电量会直接导致整备质量也增大,所以行业内也把比能量(Wh/kg)作为衡量动力电池的重要指标,电池的比能量越大,单位质量的电池可利用的能量越多。
提高动力电池电量,虽然会增加续航里程,但是会直接导致整车成本上升。以某目标车型为例,整备质量约1 000 kg,续航目标为300 km,整车参数见表1。
表1 某纯电车基本参数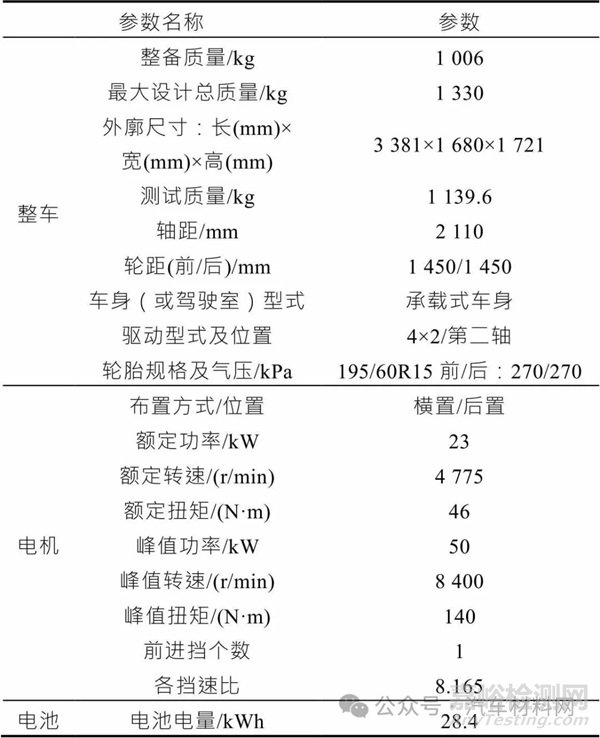
当前动力电池电量28.4 kWh,为达成续航目标,需要增加4 kWh,按当前行业动力电池成本 1 250元/kWh,则整车成本需要增加约5 000元,对于竞争激烈的微型纯电动车型市场,产品竞争力将会大打折扣,显然单独靠提高动力电池电量性价比较低。
2.2 提高驱动系统效率
如图1所示,驱动系统主要是指动力电池到车轮端的电能转换成动能的过程,由式(1)可知,续航里程与电机电控整体效率、传动系统效率成正比,通过AMESim仿真软件对某1 000 kg纯电动车型计算可知,当系统效率每提升1%,续航里程可增加3 km。
图1 驱动系统输入及控制图
2.2.1提高电机电控整体效率
目前行业内电机控制器效率一般为97%左右,驱动电机效率参差不齐,范围从80%到98%不等,对电动车用驱动电机而言,大部分运行点集中在转速4 000 r/min以内,如图2所示,这就要求电机不仅要在额定状态下具有较高的输出效率,而且要求具有很宽的高效率区[2]。
图2 CLTC工况中驱动电机运行点分布
驱动电机的类型可分为直流电机、异步电机、永磁同步电机和开关磁阻电机,由于永磁同步电机功率因素和峰值效率较高,被各大主机厂普遍采用。近年来扁线电机技术成为行业内争相竞逐的热点,在全球统一轻型车辆测试循环(World Light Vehicle Test Cycle, WLTC)工况,扁线电机比传统圆线电机的转换效率高1.12%;在全域平均下,两者效率值相差2%,在市区工况(低速大扭矩),两者效率值相差10%。因此,扁线电机中低速效率高,更适合于中国城市路况,然而在具备诸多优势的同时,也同样存在劣势,比如设计难度、工艺制造难度、更易损耗等,这也是其尚未大规模应用的原因[3]。
另一方面,传动系速比设计也可以影响电机运行点的位置,在电机运行点不同位置具有不同的电机效率进而可以影响到整车续航里程,如图3所示,所以在满足电动车爬坡和最高车速的前提下,可以通过调整不同速比提高续航里程。
图3 某车型速比与续航的关系
2.2.2提高传动系效率
传动系统效率损失的表现为存在机械内阻,一般通过摩擦损失转化为热量散失,因此,提高传动系效率也可有效提升续航里程。以某车型为例,优化后的续航里程贡献见表2。
表2 传动系对续航里程的影响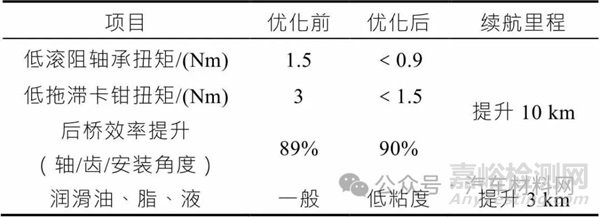
2.3 优化整车设计参数
整车参数主要影响车辆的行驶阻力,其中整备质量与滚动阻力、加速阻力、坡道阻力都成正比例关系,迎风面积和风阻系数主要影响空气阻力。
2.3.1整车轻量化技术
为比较某车型整备质量对续航里程的影响,将整备质量按25 kg步长,应用AMESim仿真软件逐个计算某车型在不同质量下的续航里程变化,如图4所示。结果表明质量每减少25 kg,续航里程可增加3~4 km。
图4 质量对续航的影响
行业内的车身轻量化技术主要包括应用新材料、新结构设计和先进制造工艺。新材料采用铝镁合金、工程塑料和碳纤维等,如特斯拉前期Modle 3为全铝合金车身结构,奥迪汽车也很早就开发了全铝合金车身技术[4]。
新结构设计就是在保障车身整体强度的前提下,利用钢塑一体化结构设计原理,在传统钣金技术的基础上,加入高强度的工程塑料,达到车身减重的目的。
先进制造工艺的典型代表是以特斯拉、比亚迪为首的CTC(Cell To Chassis)或CTB(Cell To Body)的车身一体化技术,该工艺把电池包做成底盘,目的是提升电池的能量密度增加车内的乘坐空间从而减少零部件数量,节省成本的同时也给整车减轻重量。
2.3.2减小风阻系数
据国外统计数据表明,对于一般轿车,空气阻力消耗的能量平均占总能耗的17%,对于皮卡车,由于尾部气动分离严重,其空气阻力消耗的能量又比普通轿车大6%。由于市面上车型的长、宽、高参数并不会发生太大变化,所以减小风阻系数成为降低整车空气阻力的主要措施。
同样,为比较某车型风阻系数对续航里程的影响,将风阻系数按每0.005步长,应用AMESim仿真软件逐个计算某车型在不同风阻系数下的续航里程变化,如图5所示。结果表明风阻系数每减少0.005,通过仿真计算得出目标车型每个测试循环能耗降低0.01~0.03 kWh/100 km,即续航里程可增加1.5~1.6 km。
图5 风阻系数对续航的影响
国内应用风洞试验或计算流体动力学(Com- putational Fluid Dynamics, CFD)技术已经比较成熟,通过优化挡风玻璃角度、优化前保造型、安装底盘封板、低风阻后视镜、低风阻轮毂、隐藏门把手都能有效减小风阻系数。
2.3.3应用低滚阻轮胎
由式(1)可知,轮胎滚阻系数f也直接影响了续航里程,低滚阻轮胎可以有效降低整车滚动阻力,以某车型台架试验为例,原轮胎采用8.3‰,改用6‰轮胎后,续航里程可提升10 km。
2.4 降低附件能量消耗
根据国标GB/T 18386测试纯电动汽车续驶里程时,会保持空调、音响娱乐、雨刮、电动助力转向(Electric Power Steering, EPS)系统等用电器关闭,只维持工况基本用电需求,但是此时,冷却风扇、仪表以及各控制模块仍会供电,部分主动安全功能及相关硬件(摄像头等)默认开启,由此会增加低压功耗,最大会导致行驶里程下降约4.4%,即能耗有4.4%优化潜力。
2.5 优化整车控制策略
整车控制策略优化一种方式是通过控制油门踏板与负荷的关系曲线使电池、电机工作在高效区间,需要根据电池的放电特点和电机Map图得到其高效工作区域,然后不断调整油门踏板与负荷的关系,使其达到续航里程最优的状态[5]。另一种方式是增大能量回收强度来实现,如图6所示,强回收模式表示在续航测试中减速时基本不需要制动踏板制动,而利用滑行能量回收达到制动,而弱回收在减速过程中需要踩制动踏板,通过制动能量回收。
图6 滑行回收Map
同时,在制动能量回收阶段设置充电功率时,在高电池剩余电量(State Of Charge, SOC)下,电池在90%左右的充电能力能适当放开;在低SOC下,制动能量回收能尽可能包含多一些回收点,从而提高整个循环过程中的回收能力,电池端回收率从23%提升到了28%,续航里程增加了12 km。
3、 各关键技术成本分析
由于整车控制策略可通过软件标定迭代优化,基本不需要增加成本,所以首先推荐增大能量回收强度、优化油门踏板与负荷的关系(会牺牲驾驶性);减小风阻系数可通过前期造型设计优化,虽然有一定技术门槛,但基本不增加成本;降低附件能耗可以通过控制某些电器在测试过程中主动休眠来实现,此时不会增加成本,但是随着车辆电气化、智能化趋势,面临一定挑战;应用低滚阻轮胎对续航提升比较明显,而提高电机传动效率、整车轻量化、提高电机电控整体效率,由于上文提到的行业成熟度的原因,成本也逐步增加,可作为后备选项;最后直接提高电池电量,成本最高,同时还会直接导致整备质量也增大,对于微型纯电动车性价比较低。
表3 各关键技术成本分析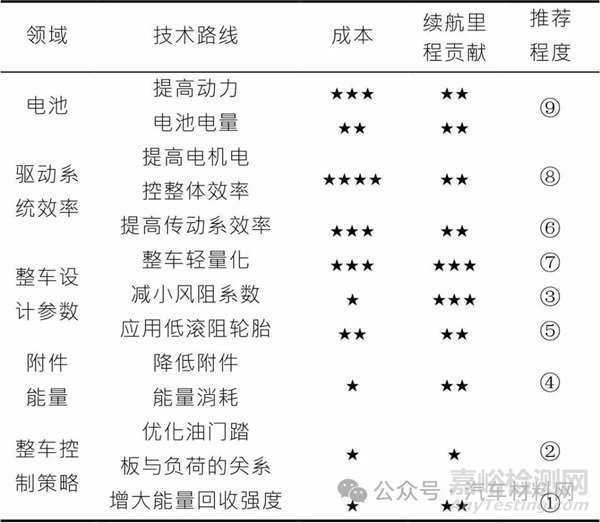
根据技术成熟度、行业发展情况,以及综上所述续航里程贡献,若从微型纯电动汽车产品性价比角度出发,当前阶段推荐按表3所示技术路径提升续航里程。
4、 结论
本文基于纯电动汽车理论公式推导,对影响续航里程的各项因素进行逐一分析,并利用AMESim仿真软件和台架数据,分析各参数对续航里程的敏感度,节约了大量时间和人力;另一方面,基于当前动力蓄电池技术限制,在成本尚未体现出成本优势的前提下,提出了性价比高的技术路径,为微型纯电动汽车开发提供了指导建议。
参考文献
[1] 唐金龙,费为伟.提升纯电动客车续航里程的策略研究与仿真[J].新能源汽车,2020(22):14-16.
[2] 王春生,王学超,孙浩.新能源汽车续航里程影响因素分析[J].汽车工程师,2017(4):40-42.
[3] 杨秀玲,乔华,王娟.基于AVL-Cruise的电动汽车续航里程优化方法[J].新能源汽车,2020(11):21-23.
[4] 王志鹏.提高纯电动汽车的续航里程的策略[J].新能源汽车,2019(6):11-13.
(相关交流群,扫码添加微信!)
来源:《汽车实用技术》
作者:何卫1, 高丽仙2, 张雪1(1上汽通用五菱汽车股份有限公司;2柳州孔辉汽车科技有限公司)
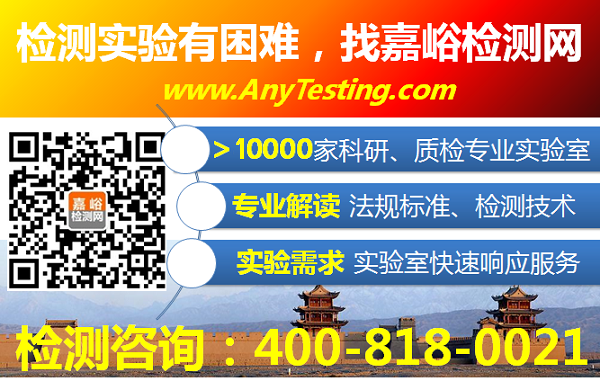