为提高产品的耐腐蚀性能,航空航天、船舶、核工业、汽车、机械等行业广泛应用不锈钢材料。随着机械工业的发展,普通的不锈钢已不能满足强度需求,超高强度马氏体沉淀硬化不锈钢得到了研发和应用。一般采用表面钝化的方式对强度较高的不锈钢进行腐蚀防护处理。经钝化后,不锈钢表面生成复合膜,膜层至少有内、外两层,内层富含 Cr、Mo或Ni等元素,外层为富Fe层。表面钝化工艺类型较多,采用不同钝化工艺得到的钝化膜结构和成分有所不同。
超高强度马氏体不锈钢的强度较高,对氢脆敏感,材料的强度越高,氢脆敏感性越大,钢的氢脆敏感性不仅与强度有关,还与组织中的第二相、晶粒度、微观结构缺陷、合金元素等有关。复合添加Nb、Ti、Cu等元素,并配合适当的热处理,可使材料析出纳米相,显著提高材料的抗氢脆能力。氢元素的扩散系数较小,材料的氢脆敏感性也较低,当材料的氢元素扩散系数较大时,高强度不锈钢的零断面收缩率对应的临界氢元素含量可低至0.0000008%(质量分数)。晶界、位错、晶界上的第二相、板条束尺寸大的组织单元及应力集中区域等都易导致氢元素富集,并引发氢致开裂。钢的氢脆敏感性还与材料脆性、零部件残余应力等因素有关。
某超高强度沉淀硬化不锈钢弹簧在电镀过程中发生氢脆断裂。研究人员采用一系列理化检验方法分析了弹簧断裂的原因,以避免该类问题再次发生。
1、理化检验
1.1 宏观观察
弹簧断口的宏观形貌如图1所示。由图1可知:断口由两个明显不同的区域组成,Ⅰ区断口粗糙,目视可见许多反光的小刻面,有收敛于弹簧内径表面的裂纹扩展棱线,呈线源特征,弹簧起裂区表面无划伤等机械损伤;Ⅱ区断口颜色发灰,可见源自Ⅰ区断口的裂纹扩展棱线,断口边缘呈剪切唇特征。
1.2 氢元素含量测试
选取同批次原材料进行氢元素含量测试,试样尺寸(直径×长度,下同)为4mm×5mm。将原材料进行钝化处理,并对钝化后的试样进行氢元素含量测试,钝化后试样尺寸分别为5mm×5mm(未去除表层)和4mm×5mm(去除表层)。接着对试样进行除氢处理,并对除氢后的试样进行氢元素含量测试,除氢后试样的尺寸分别为5mm×5mm(未去除表层)和4mm×5mm(去除表层)。钝化和除氢处理方法如表1所示,氢元素含量测试结果如表2所示。由表2可知:原材料中未检测出氢元素,钝化后和除氢后试样中均可检测到一定含量的氢元素,除氢后氢元素含量有所降低。
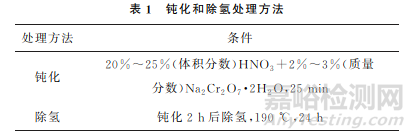
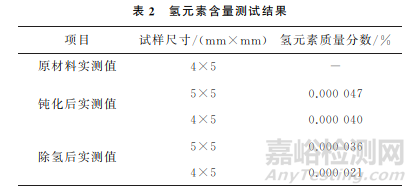
1.3 金相检验
在断裂弹簧断口附近截面上取金相试样,采用光学显微镜对试样进行观察,结果如图2所示。由图2可知:弹簧无明显脱碳现象,无过热、过烧组织,试样的显微组织未见异常,组织均匀,裂纹沿晶扩展,扩展过程中裂纹出现树枝状分叉。
1.4 硬度测试
在断口附近垂直钢丝轴向的截面取样,对试样进行硬度测试,测试结果的平均值为50.4HRC,满足标准要求(≥47HRC)。
1.5 扫描电镜(SEM)及能谱分析
起裂部位断口SEM形貌如图3所示。由图3可知:断口可见收敛于边缘的裂纹扩展棱线,未见明显缺陷,断口呈沿晶断裂形貌,有二次裂纹,沿晶面上有较多的微观颗粒相,少部分晶面呈鸡爪痕特征,断口无腐蚀形貌。
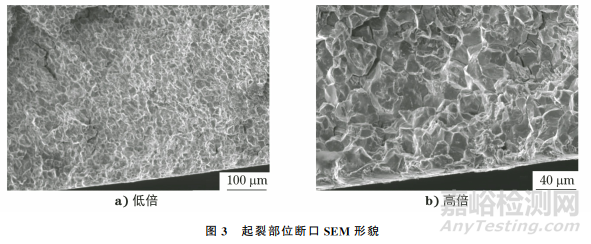
弹簧断口中部的SEM形貌如图4所示。由图4可知:断口Ⅰ区为沿晶断裂区,微观形貌与起裂区附近基本一致,Ⅰ区和Ⅱ区之间没有明显的过渡区,无腐蚀等其他特征;Ⅱ区为韧窝断裂区,断口边缘有剪切唇,为终断区。
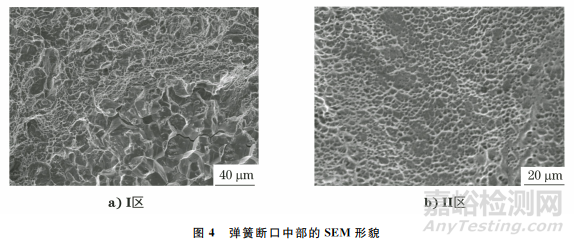
断口的能谱分析位置如图5所示,分析结果如表3所示。由表3可知:断口Ⅰ区和Ⅱ区的化学成分基本一致。
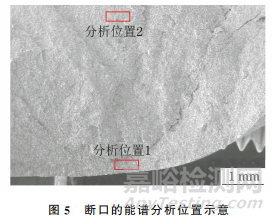
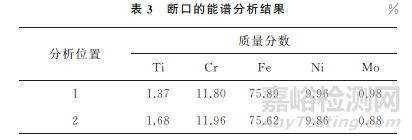
2、综合分析
由上述理化检验结果可知:弹簧宏观断口粗糙,有明显的颜色分区,裂纹起裂于Ⅰ区弹簧表面,终断于Ⅱ区弹簧表面。断口Ⅰ区有裂纹扩展棱线,呈线源特征,裂纹源区未发现材料缺陷,微观断口呈沿晶断裂形貌,为脆性开裂。断口Ⅱ区呈韧窝断裂形貌,终断区有明显的剪切唇形貌,为韧性过载断裂。
断口Ⅰ区和Ⅱ区的形貌特征存在差异,说明断口Ⅰ区和Ⅱ区的断裂机制不同。Ⅰ区裂纹较长,沿晶扩展,在扩展过程中出现明显的分叉,裂纹头部尖锐,断口可见鸡爪痕形貌特征,并无腐蚀形貌,Ⅰ区断口符合氢致开裂特征。Ⅱ区是裂纹在Ⅰ区的基础上扩展形成的,裂纹扩展过程中,弹簧承受载荷的实际截面积不断减小,且裂纹前沿存在应力集中,当应力超过弹簧的强度极限后,弹簧会发生过载断裂。
组织不均匀、成分偏析等情况均会导致材料在服役环境中发生断裂。该弹簧表面无脱碳现象,弹簧的组织、化学成分未见异常,说明该弹簧的组织均匀、无合金元素偏析现象。Ⅰ区和Ⅱ区的化学成分基本一致、断口衔接自然、无腐蚀等特征。说明该弹簧的强度、组织和化学成分不是导致弹簧Ⅰ区发生脆性开裂的主要原因,该弹簧可能在生产或使用过程中存在渗氢现象。
弹簧经表面钝化处理后,材料中可检测出少量的氢元素。经190℃,24h除氢处理后,氢元素含量去除率约为23%,氢元素含量有所降低,但材料中仍残留了一定量的氢元素。钝化处理后,去除表层和未去除表层试样的氢元素含量测试结果相差不大;除氢处理后,去除表层和未去除表层试样的氢元素含量测试结果相差较大。说明除氢过程中,材料内部的氢元素向外扩散,除氢后,残余的氢元素主要富集在材料表层。
弹簧在使用过程中一直处于受力状态,弹簧内侧钢丝表面受到的应力较大,氢元素在应力作用下向高应力处聚集。氢元素不断富集在内侧表层的晶界和晶界上第二相处,使晶界脆化,在应力作用下,弹
簧内侧表面萌生氢致脆性微裂纹。弹簧内部残留了少量的氢元素,且微裂纹尖端存在应力集中,当裂纹尖端的应力强度超过氢脆起裂临界值时,微裂纹进一步沿晶脆性扩展。裂纹越深,裂纹尖端对应力变化越敏感,当氢致裂纹扩展到一定深度后,弹簧工作应力瞬时变大,从而导致剩余截面发生过载断裂。
3、结论及建议
超高强度马氏体沉淀硬化不锈钢弹簧在钝化过程中存在渗氢现象,在应力作用下,弹簧内侧萌生氢致脆性微裂纹,裂纹不断扩展,最终导致弹簧发生过载断裂。
建议适当提高除氢热处理的温度,并延长除氢时间,进一步去除材料中的氢元素。采用适当的热处理工艺,降低材料的氢脆敏感性。
作者:闫富华,李伟,樊伟刚,张亚梅,张跃
单位:庆安集团有限公司
来源:《理化检验-物理分册》2024年第1期
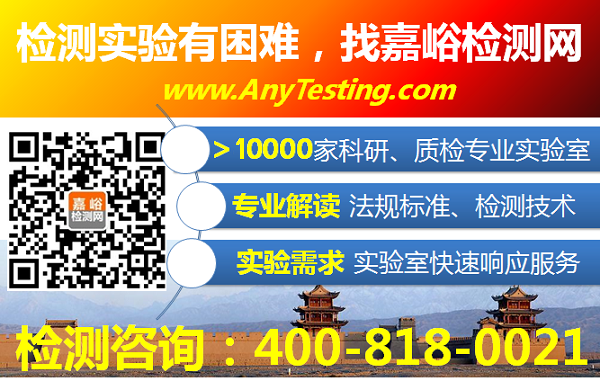