结构工程师和产品设计师不断寻找方法,使他们的设计更坚固,同时降低重量和材料成本。新材料代替旧材料可以在一定程度实现降本增效的目的,但要想实现显著的改变,必须从产品、结构(原理),加工等几方面共同发力才会带革命性变化。
吃穿住行是人类最基本的需求,很多的结构性变革是从建筑开始的,如过去的砖石砌体建造发展到当今的钢筋混凝土浇筑,极大地节约材料并提升了建造速度。
帮助人类快速移动的汽车结构发展也经历了一系列的变革,如小轿车从梁+非承重式车身发展到承重式车身,承载式车身同时承担了遮风避雨和承重的功能,因此结构就更加紧凑,用料更加节省,再加上各种轻量化设计,整车的重量也要小很多,所以相比于非承载式车身更省油,更适合家用。
但传统的制造工艺将数百个单独的钣金冲压件焊接起来,形成一个完整的车身,而此种生产成本还是比较大的,每一个冲压件都需要以下设备:
1个分切机(切下合适宽度的轧制钣金)
1个开卷机(在冲压前将轧制的金属压平)
2个或更多冲压模具(深拉最多4个甚至5个或6个)
1个或更多的机器人物料搬运工
但实际上,所有冲压设备和相关工装不仅需要投资,还会占用车身车间大量的厂房面积。你可以看到,仅仅是制造组装车身所需的冲压件就需要大量的资本投资,但还没有完成。这些部件中的每一个都需要安装到位(用夹具、粘接焊),然后焊接多达1500到2000多次,以创建一个完整的一体结构。但这种方法的麻烦还不止于此。由于结构是分段建造的,每个单独的部分都有自己的尺寸和位置公差,即不但要控制单独部件本身的误差,并且要特别注意部件与部件之间配合公差,这无形中给生产增加了更大的成本。
另外,多个接点就增加一分失效风险,而将相邻的两个或更多的部件合并为一个部件无疑会极大地降低由于连接所带来的风险。任何连接都是不完美的,现实中的大多数失效都是从连接点先开始的,如我们走在天桥上,天桥的钢结构锈蚀首先从焊缝开始。另外这种集成化可降低尺寸误差,而且可以增加部件的整体刚性。
图 1 连接接头往往是失效的发源
而这种集成化方法在其他行业也屡试不爽,如建筑的预制桥梁,笔记本电脑一体化机身等。
图 2 预热混凝土梁
通过上篇铝合金车身制造发展的介绍,我们可以明显感受到,在Tesla Model Y之前,车身部件的集成化趋势,无论是挤压件还是铸件的尺寸都逐渐大型化。但Tesla却大胆的将集成化发挥到极限,正如上面的特斯拉图表所示,最初的Model 3(左边)需要超过170块不同的金属片,并进行1600多次焊接。在奥斯汀工厂生产的新一代Y型车只用前后两个一体化铸件取代了这些部件。
图 3 Model 3 (左)与Model Y(右)
一体化压铸技术绝对是压铸技术的新变革,通过将原本设计中需要组装的多个独立的零件经重新设计,并使用超大型压铸机一次压铸成型,直接获得完整的零部件,实现原有功能。汽车的传统制造工艺,主要包括冲压、焊装、涂装、总装等4个环节。一体化压铸技术是对传统汽车制造工艺的革新,可以让车身轻量化,节省成本,提高效率,缩短供应链,整车的制造时间和运输时间缩短,减少人工和机器人,提升制造规模。
减轻重量:双碳背景下,轻量化是汽车行业发展的大趋势。一体化压铸的应用有助于轻量化的实现,铝合金综合性价比突出,是汽车轻量化的首选材料,随着一体化压铸技术的发展,铝合金压铸在车身与底盘结构件以及电池壳体上的应用有望逐步提升,从而提升铝合金压铸的单车价值量。
提高效率:与现有生产工艺相比,一体化压铸通过简化生产工序提升节拍,从而提高生产效率。大型压铸机一次压铸加工的时间不足两分钟,80-90秒即可完成,每小时能完成40-45个铸件,一天能生产1000个铸件。如果采用传统加工工艺,冲压加焊装70个零件组装一个部件,至少需要两个小时,必须多线并进,才能满足生产节奏。
降低成本:很明显,一体化压铸技术的应用,可以大大的减少生产成本,从前需要10台设备、20个工人、数十道工序才能完成的产品,使用一体化压铸技术后,一台设备、三个工人就能完成,工序省了大半,仅需引入大型压铸设备和开发大型模具,这些是一次性投入可重复使用。从长远利益来看,可以减少大量不必要的人力物力的浪费。特斯拉应用一体化压铸的后地板,制造成本相比原来下降了40%。
提升性能:一体压铸极大减少了连接接头的数量,这无疑会给构件的整体性能带来极大的提升,如增加尺寸精度,增加整体的刚性,而降低由于接头引入而带来的接头失效风险等。
任何事物都具有两面性,具有优点的同时也不可能没有缺点:
更高的门槛:高端的技术的实施是在高端的材料、高端的设备及精确工艺水平支撑下来完成的,前期需要经过大量的研发人力、时间及经费的投入,所以往往入场门槛都比较高。
一荣俱荣一损俱损:一体化压铸技术,在增加结构刚度的同时,也失去相应的灵活性。就如当年蓸操将战舰首尾相连后,虽然得到了得到稳定且结实如钢板一样的平台,但却失去了灵活性,当黄盖的火船冲过来时,只能挺身向火。同样Tesla的一体化结构,当受到损坏需要维修时的成本也是比较大的。
2、一体化压铸的技术
之所以说一体化压铸是一项革命性创新,因为它的确是一种想前人不曾想或不敢想的技术突破,为什么这么说,我们从设备、材料、工艺及模具几方面讨论一下:
2.1 设备方面
一体化压铸对压铸机的锁模力有较高要求,压铸机有定制设计与开发的技术壁垒以及相对较高的资本支出。一体化压铸技术对设备压力需求比普通压铸设备提升了一个数量级,从以前的千吨级别提升到万吨级。
在特斯拉提出大型一体化压铸工艺前,行业压铸机锁模力吨位停滞在 5000吨以内,主要用于生产发动机 底壳、变速箱底壳、前后门框、车门等尺寸质量相对较小的车身零部件。对比之下, 作为车架结构的地板总成,在尺寸与质量上均大于上述零部件。加之,车架对于乘客的安全保护起到关键作用,质量要求均高于其他零部件,因而加大压铸整体车身的难度。其中,以生产难度相对较小的后地板总成为例,采用一体化压铸技术生产后地板总成,需要锁模力在 6000吨 以上的铸造机进行生产。而质量要求更高的前地板则需要约 8000吨 的铸造机,尺寸更大的中底板和电池壳需要 12000吨 以上的铸造机。
图 4 不同车身部件压铸压力需求
除了压铸机定制设计与开发的技术壁垒之外,一体化压铸机价格较高,需要大批量生产带来的规模效益,来分摊压铸机和模具的综合成本。
目前具备此类超大型压铸机生产能力的厂商主要有瑞士布勒、力劲科技及其子品牌IDRA、海天金属、伊之密等。
2.2 材料
2.2.1 材料重要性
产品性能由结构(原理)、材料及加工技术共同决定,材料是决定设计及加工能够顺利执行的重要因素,马斯克在2015年挖走了苹果铝合金材料专家查尔斯 · 库曼(Charles Kuehmann),此人绝对是铝合金研究领域里的顶尖人士,不但在苹果任职过,而且还有航天航空材料研究背景,所以同时任Tesla和SpaceX的材料副总,可以说为Tesla和SpaceX的产品发展都做出了重要的贡献。
对合金材料配方成分进行锁定,多为下游客户合作前置条件。压铸材料体系很多,但并不都适合一体化压铸技术。铝合金材料的主成分、核心成分、微量元素种类及含量含量对材料的抗拉强度、 屈服强度、延伸率、流动性等性能会产生重大影响。可以说一体化压铸技术的苛刻要求使得合金材料的配比窗口并不是很宽泛,各研究机构都在争先开发并申请材料专利,已授权专利必然对后入场者突破形成较大阻碍,因为整车厂为避免专利纠纷,对材料的资格审查也较为严格,倾向于选择获得专利保护的厂商材料。新玩家需开发新的铝合金配方,并获得专利,此为进行整车前期试验和认证的门槛。
2.2.2 一体化压铸技术对材料要求
铝合金铸造材料及压铸材料有很多,但一体化压铸有其自身特点,对压铸材料提出更多及更加苛刻的要求:
流动性好:
铸造时的冷却速度快,而且浇口设计狭窄,所以要求合金具有高流动性,可以提高压铸时之充填能力,所以,通常铝合金中的Si含量较高,可以拥有较佳的流动性。
避免黏模发生:高压铸造,必须以高压的方式将金属熔液喷入模穴中,因此防止金属熔液与模具黏着,避免影响填充金属的流动性,铝合金中含有Fe的成分较高可以避免黏膜的产生;但是被当作不纯物的Fe含量较高,促使硬脆板状(brittle plate)a-AlFeSi的生成,或在Mn中存在其他复杂金属间化合物(intermetallic),容易使得铸件变脆及延伸率下降。
常温下有足够强度,以利生产薄壁件。
免热处理:一体化压铸件不能进行热处理,这主要由两方面决定。一是铝合金熔液被高速打入型腔,很难不卷入一些气体,在固态时被卷入气体以原子形态存在,当受热会发生扩散结合为气体分子,会在部件内部或表面产生孔隙,影响部件的性能。另一方面对于传统铝合金而言,热处理是保障压铸零部件机械性能的一种重要手段。由于一体化压铸件的产品外形太大,热处理过程易引起汽车零部件变形、尺寸变化和表面缺陷是不可避免。虽然通过一些整形手段可以改善一定的尺寸精度和缺陷,但也会造成废品率的增加,导致加工成本上升。一体化压铸需开发一款材料与之配合,即不用热处理仍能得到具有应有的强度和韧性材料,满足车身的需求。
2.2.3 一体化压铸铝合金体系
国内外企业包括美国美铝、德国莱茵、特斯拉、上海交大、蔚来汽车、立中集团等都在开发推广免热处理材料,免热处理材料让一体压铸成为可能。
免热处理合金采用的技术路线主要为铝硅及铝镁两大系列,铝硅系列为主流。合金主要通过加入Mg、Cu等形成固溶强化、弥散强化。另外通过引入微量的元素,如锶Sr,RE(rare earth,稀土元素,包括Sc钪、Er铒、Ce铈、Y钇等)对材料进行优化,千万不要忽视这百分之零点零几的含量,真的很神奇变质效果,虽然一体化压铸的冷却速率很高,会得到较细小的晶粒,但对于材料的热稳定性,防止晶粒粗化都有很好的效果。
表1列举了一些用于非热处理压铸结构件的合金名称及其化学成分。
表1 免热处理压铸铝合金成分配比
元素
|
Castasil 37
|
Aural6
|
C611
|
Tesla 1
|
Tesla 2
|
SJTU-Al-Mg-Si-Mn
|
Si
|
5.5-10.5
|
9.5-11.5
|
4.0-7.0
|
6.5-7.5
|
6-11
|
2.0-3.6
|
Cu
|
0.05
|
0.02
|
-
|
0.4-0.8
|
0.3-0.8
|
-
|
Mn
|
0.35-0.6
|
0.3-0.7
|
0.4-0.8
|
0.3-0.7
|
0.3-0.8
|
0.6-0.9
|
Mg
|
0.06
|
0.15
|
0.15-0.25
|
0.1-0.4
|
0.1-0.4
|
6.0-8.0
|
Fe
|
0.15
|
0.1-0.25
|
0.15-0.2
|
0.4
|
0.5
|
-
|
Sr
|
0.01-0.015
|
0.01-0.015
|
0.01-0.015
|
0.01-0.03
|
0.01-0.05
|
-
|
Ti
|
-
|
0.04-0.15
|
0.1
|
0.15
|
0.15
|
0.15-0.2
|
Zn
|
0.07
|
0.03
|
-
|
-
|
-
|
-
|
RE
|
Mo, Zr
|
-
|
-
|
含V,Cr
|
含V,Cr
|
|
德国莱茵金属公司开发出Al-Si系和Al-Mg系免热处理高强韧合金,如Castasil-37压铸铝合金。该合金不含Mg,因此不具备时效硬化效应,同时增加了Mo和Zr来进行弥散强化。该合金的力学性能和不同Mg含量有关。然而基于莱茵菲尔德公司的研究,提高Mg元素的含量会影响铸件铸态下力学性能的热稳定性,表现为在一定温度环境下服役过程中屈服强度会逐渐增加,因此Castasil 37将Mg元素含量上限定义为0.06%。
麦格纳公司开发两款非热处理压铸合金,Aural 6 合金(即 375,类似 Castasil 37)与 Aural 5 合金(即 374,类似 C611)。Aural 6 合金与 Castasil 37 相比以 少量的 Mg 替代 Mo 和 Zr 从而获得一定的强化效果。Aural 5 合金与 C611 基本一 致,在铸造后和涂装烘烤前良好的塑性与自然时效稳定性可以满足车身结构件的 SPR 连接要求,涂装烘烤后强度会进一步提升,此外还可以满足 205℃下 1h 的 短周期热稳定性以及 150℃下 1000h 的长周期热稳定性要求。
美国铝业公司产品为EZCAST系列C611免热处理AI-Si系压铸铝合金,由美国铝业在上世纪90年代开发成功,应用在奥迪A8的全铝车身上。Si含量较低,合金内含一定的 Mg 元素导致其并非严格意义上的非热处理材料, 其屈服强度可通过进行 T5 热处理或 T85(涂装烘烤处理)提升2。C611 系列具 有极佳的流动性,可制造形状复杂且要求高性能的结构部件,如减震塔、横梁、 电池托盘、框架、电动机外壳等,已经被欧美许多压铸厂家广泛地应用于薄壁结 构件(例如减震塔)的生产许多年。国内蔚来汽车宣布成功将 C611 EZCast™合 金运用于一体化压铸件,帅翼驰国内独家代理美国铝业的 C611 合金,为该项目的联合合作伙伴。
马斯克在2015年挖走了苹果铝合金材料专家——查尔斯 · 库曼,开发出了新的免热处理铝合金配方,解决了免热处理的难题。特斯拉在其 Model Y 车型上首次使用 6000 t 大型压铸机制造铝合金一体化压铸后部下车身,目标合金在铸造态的屈服强度和极限冷弯角应分别大于135MPa和24°,由于铸件的巨大尺寸还要求合金具有极好的流动性能。研究发现,在压铸条件下,Si含量在6%以上时,继续增加Si含量并不会明显改善流动性,反而会引起共晶硅相增加从而影响合金的韧性,该合金控制Si含量同时满足流动性和韧性的要求。通常情况下,添加Cu元素可以提升强度,但是降低塑韧性,该合金通过控制Cu/Mg比例以利于析出AlCuMgSi相取代Mg2Si和Al2Cu相来实现强度提升的同时不会引起塑韧性的明显下降。此外,该合金中添加了Sr进行变质处理,添加V元素析出球状的AlFeSi(Mn+V)相,减少了片状的富铁相,均有利于材料韧性的提升,同时也能够容忍更高的Fe杂质含量。
SJTU-Al-Mg-Si-Mn合金是上海交通大学开发的一种非热处理压铸合金,其目的是在保持材料良好韧性的前提下提升屈服强度。对于Al-Mg-Si-Mn合金,随着Mg含量的增加,材料的屈服强度增加,延伸率下降明显。因此该合金在增加Mg、Si元素的含量并调控相对比例的同时,添加Ti、Zr、V合金改善组织,并引入Re/Ca 复合变质对共晶硅进行细化,获得屈服强度>180MPa,延伸率>10%的力学性能。类似地,SJTU-Al-Mg-Cu-Mn合金引入Cu元素进行强化,同时引入Y、Er、Ce 稀土元素来细化 Al2CuMg相,获得屈服强度>180MPa,抗拉强度>320MPa,延伸率>8%的高强高韧的综合力学性能。目前的Al-Si系和Al-Mg系合金普遍具备中等的强度与韧性,随着铝合金压铸结构件的集成化与轻量化需求的不断提升,新型压铸合金的开发应朝着提升屈服强度或韧性,同时具有良好的铸造流动性的方向发展。
2.3 工艺及模具
一体化压铸对模具材料强度及韧性要求非常高,要求具有抗冲击韧性和回火稳定性、良好的导热和抗疲劳性、热膨胀系数小、抗高温氧化性。压铸需要高速充型与高速凝固,在温度、真空度、成型方案、工艺参数及后处理要求都很高,一体化技术对于模具的要求更复杂。一体压铸需要大型的模具,模具设计要考虑排气、集渣,均匀冷却等因素,需要仿真技术模拟充型过程,避免出现热孤岛,否则会在零件冷却收缩过程中产生缩松孔和裂纹缺陷。模具设计厂家必须具备压铸充型模拟分析能力。这种大型的模具国内只有几家能做,比如广州型腔、宁波臻至、飞旺、北仑赛维达、象山合力,北仑臻致等。一般单件的生产节拍可以控制在100-120s,每天两班倒11+11h,一台压铸机年产能大概15万套,一套模具每年可以支撑6-8万套产能,每套模具单价接近1,000万元。
一体化压铸是一个非常复杂的过程,不但包括合金融化处理,包括模具温度控制及脱模剂的喷涂,包括压铸模式及压铸参数,每阶段都需要精确的控制。如对于合金融化和处理,融化过程中需要采用高纯电解金属配料以避免金属杂质污染;熔炼时为防止金属液氧化及偏析,需要快速熔化,熔化后需要对铝液除氢、除渣净化处理,除气时间10~15 min,需要精确控制熔化温度及保温时间,不宜过长以避免变质剂的烧损。
参考文献
1. 一体化压铸技术应用前景研究,来自 <https://www.auto-testing.net/news/show-115745.html>
2.一体化压铸是什么, 来自 <https://mp.weixin.qq.com/s?__biz=MzAwNjA3MjExMQ==&mid=2247499317&idx=1&sn=799698dbaab99106dd058c5556a2ff2e&chksm=9b104c75ac67c563a2b89821c563619de69c7139e8797a362d9ba395ba61344a5b57fff12249&scene=27>
3.汽车一体压铸专题分析:一体压铸方兴未艾,推动车身制造变革,来自 <https://view.inews.qq.com/a/20221031A0632600>
4. Tesla 专利: “Die Cast Aluminum Alloys for Structural Components,”
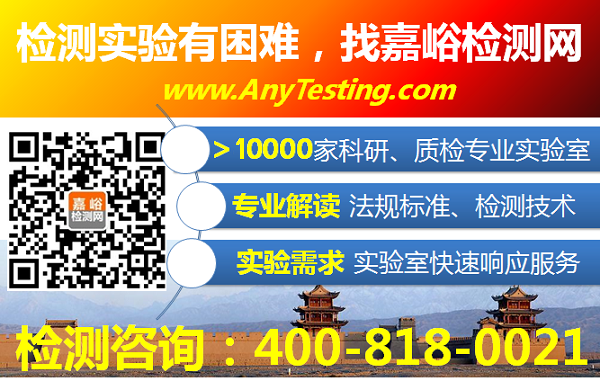