数控车床主轴组件的回转精度是影响机床加工精度的主要因素之一,而主轴轴承的稳定性对回转精度起到关键作用。轴承的服役工况复杂,机床主轴轴承的早期失效形式主要有:接触疲劳失效、断裂失效、腐蚀失效等。由于转动中的轴承受到循环载荷作用,因此各类机械轴承经常发生滚动接触疲劳失效。轴承的滚动接触疲劳损伤主要发生在轴承套圈的滚道表面或近表面。一般认为,轴承的滚动接触疲劳寿命与材料的自身性能和外部条件有关,自身性能主要包括材料的硬度、组织均匀性和夹杂物分布等,外部条件则主要指接触表面的粗糙度、清洁度以及轴承系统的润滑情况等。车床主轴轴承在实际应用中发生的早期失效常由轴承的自身性能和外部条件共同作用引起。
某公司的一台数控车床主轴在转速为500~1000r/min时存在异响,判断主轴轴承发生早期失效。该数控车床用于加工硬铝零件,常用的工作转速为6000~8000r/min,车床主轴轴承型号为7014AC,属于角接触球轴承。轴承套圈材料为GCr15钢,滚珠材料为SiC。李天夫、钟云飞等研究人员采用宏观观察、化学成分分析、扫描电镜(SEM)和能谱分析、金相检验、硬度测试等方法分析了轴承的损伤原因,以防止该类问题再次发生。
1、理化检验
1.1 宏观观察
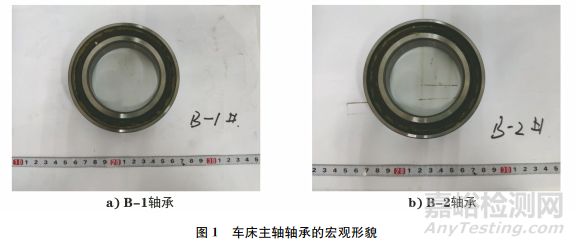
车床主轴轴承的宏观形貌如图1所示,两个轴承分别标记为B-1 和B-2,轴承外观无明显损伤。
在体视显微镜下观察B-1、B-2轴承的外圈和内圈滚道表面,结果如图2所示。由图2可知:失效轴承的外圈滚道表面损伤程度轻微,内圈滚道表面则可见明显的剥落坑。对轴承内圈滚道表面的典型损伤区域进行放大观察,可见B-1轴承内圈滚道表面的损伤面积较大,而B-2轴承内圈滚道表面的损伤面积相对较小。
1.2 化学成分分析
截取B-1轴承和B-2轴承试样,对其进行化学成分分析,由 GB/T 18254—2016《高碳铬轴承钢》可知,轴承材料的化学成分均符合标准要求。
1.3 扫描电镜和能谱分析
用扫描电镜对B-1轴承内圈滚道表面试样进行观察,结果如图3所示。由图3可知:内圈滚道表面的损伤面积较大,但深度很浅,为滚道表层的轻微损伤;滚道表面局部存在若干聚集分布的小剥落坑,剥落坑形状近似圆形,大剥落坑周围分布有若干小点蚀坑。
用扫描电镜对B-2轴承内圈滚道表面试样进行观察,结果如图4所示。由图4可知:B-2轴承内圈滚道表面损伤处呈不规则形状,损伤较深,边缘处为尖角局部存在若干沿直线排列的不规则损伤凹坑,凹坑边缘存在塑性变形痕迹,且凹坑之间有两条较深的犁沟。
选取B-1轴承表面剥落坑处和B-2轴承表面损伤处进行能谱分析,结果如图5所示。由图5可知:B-1轴承表面剥落坑内O元素含量较高,但B-2轴承表面损伤处的O元素含量明显高于B-1轴承表面,且凹坑内含有较多的Al元素和少量 Ti元素,Al元素和Ti元素为外来元素。
1.4 金相检验
在B-1、B-2轴承内圈切取金相试样,将截面抛光后,按照 GB/T 10561—2005《钢中非金属夹杂物含量的测定 标准评级图显微检验法》进行夹杂物评级,结果如表1所示,结果显示B-1、B-2轴承的夹杂物含量较低。
表1 轴承的夹杂物评级结果
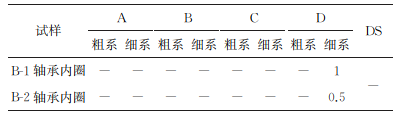
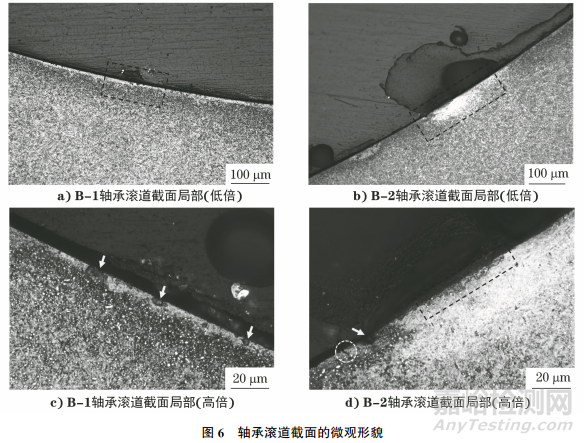
使用4%(体积分数)的硝酸乙醇溶液将金相试样腐蚀,然后利用光学显微镜观察截面局部的微观形貌。两个试样的滚道截面微观形貌如图6所示,由图6可知:B-1轴承表面均匀分布着一层极薄白亮组织,判定应为滚道表面摩擦热作用下产生的二次淬火组织,白亮层下方为深色的高温回火组织,滚道表面局部可见轻微剥落损伤,如图6a)中黑色虚线区域;B-2轴承滚道表面局部存在较深的半月形白亮二次淬火层,如图6b)中黑色虚线区域。B-1轴承的二次淬火层极薄且分布均匀,但B-2轴承的二次淬火层很厚且分布不均匀,说明B-1轴承表面发生的是正常滚动磨损,而B-2轴承的表面磨损程度不均匀,滚动体局部发生剧烈磨损。B-1轴承的表面剥落坑较浅且大小不一,呈连续分布,随着剥落坑面积逐渐变大,相邻的剥落坑之间互相连通,形成大面积表面剥落损伤;B-2轴承滚道表面剥落面积较小,可见与表面呈45°的接触疲劳短裂纹[图6d)中白色虚线区域],在二次淬火层表面存在较大面积的内部剥落[图6d)中黑色虚线区域]。两个试样中均含有细小的回火马氏体、残余奥氏体及颗粒状碳化物。
1.5 硬度测试
在B-1、B-2轴承套圈滚道表面随机选取3个位置进行硬度测试,测试结果如表2所示,根据JB/T 1255—2014《滚动轴承 高碳铬轴承钢零件热处理技术条件》,可知硬度均符合标准要求。B-1轴承套圈的硬度略低于B-2轴承;标准要求同一轴承套圈的硬度差应小于2HRC,其中B-1轴承的内圈硬度差超出标准值。
表2 轴承套圈硬度测试结果
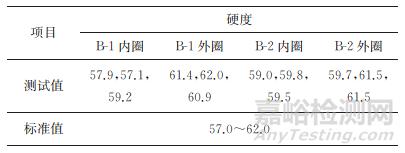
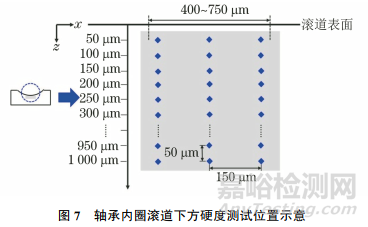
使用自动显微硬度计对轴承内圈滚道下方50~1000μm深度位置进行硬度梯度测试,每个测试深度取3个相邻点位进行测试,并对结果取平均值。轴承内圈滚道下方硬度测试位置如图7所示。
轴承内圈滚道下方硬度曲线如图8所示,结果显示B-1轴承的硬度略低于B-2轴承,且其不同点位的硬度波动较大,说明B-1内圈硬度分布不均匀。
2、综合分析
损伤主要集中在轴承内圈滚道表面,B-1轴承的损伤面积较大,但大部分为浅表层损伤,局部存在聚集型剥落,剥落坑形状规则,近似为圆形,大面积剥落坑边缘存在较多点蚀坑,为接触疲劳早期失效
的典型损伤形貌。截面的金相检验结果表明,滚道表面存在均匀分布的极薄二次淬火层,表明B-1轴承表面磨损程度较轻,无明显异常损伤。滚道表面存在若干较浅的小面积剥落坑。B-2轴承的损伤面积相对较小,但损伤较深,损伤凹坑分布比较集中。在凹坑边缘存在明显塑性变形,个别凹坑之间可见较深的犁沟,能谱测试发现损伤凹坑内 O、Al元素的含量较高,Ti元素含量较低。B-2轴承的损伤为硬铝碎屑进入轴承导致,铝屑进入接触表面发生磨粒磨损,在表面形成挤压凹坑,随着轴承的转动,在滚道表面形成较深的犁沟。B-2轴承的滚道表面存在接触疲劳短裂纹,局部表面存在较深的半月形二次淬火层,结合能谱分析结果可知,B-2轴承滚道表面的氧化程度明显高于B-1轴承。二次淬火组织主要为细小的马氏体,其硬度高、脆性大,在外力作用下极易发生开裂剥落,在B-2轴承的二次淬火层内部也观察到较大面积的剥落损伤。在循环载荷的作用下,表面硬度与金属表面塑性变形程度相关,B-1轴承的内圈滚道硬度较低,且硬度分布不均匀,促进了其浅表层损伤。
接触疲劳表面裂纹的萌生与扩展是接触件点蚀失效的主要原因。主轴轴承的转速很快,在循环载荷的作用下,滚道表面会萌生微小的接触疲劳裂纹,裂纹密度逐渐增大并互相连通,形成微区剥落,进而发展成点蚀剥落。点蚀坑处存在应力集中,在循环载荷的作用下,点蚀坑底部萌生新的接触疲劳裂纹,裂纹逐渐扩展,使点蚀坑不断加深,较多的点蚀坑发生聚集后,坑底的裂纹相互连通,逐渐形成大面积的剥落坑,引起接触疲劳失效。接触疲劳引起的表面剥落是一个循序渐进的过程。在接触疲劳作用早期,损伤主要为浅表层剥落损伤,对轴承滚道的表面粗糙度影响不大,通常不会使轴承运转异常,如B-1轴承内圈表面形成的接触疲劳损伤,但磨粒磨损引起轴承滚道表面形成较深的损伤凹坑,磨粒在滚动体的带动下使表面形成犁沟,这些损伤凹坑和犁沟使接触表面的粗糙度显著增大,破坏了润滑油膜的连贯性,导致滚动体运转受到阻滞,因此轴承在运转过程中出现异响。另外,磨损使接触区温度异常升高,局部组织发生转变,形成较深的二次淬火层,在循环载荷的作用下,表面更易萌生接触疲劳裂纹,形成较深的剥落。
3、结论与建议
(1)车床异响的原因为主轴B-2轴承发生磨粒磨损,导致滚道表面发生严重损伤,磨粒为加工零件产生的硬铝碎屑。
(2)建议加强切削碎屑的清理,或在轴承上添加防尘圈,避免外界异物进入引起轴承损伤。
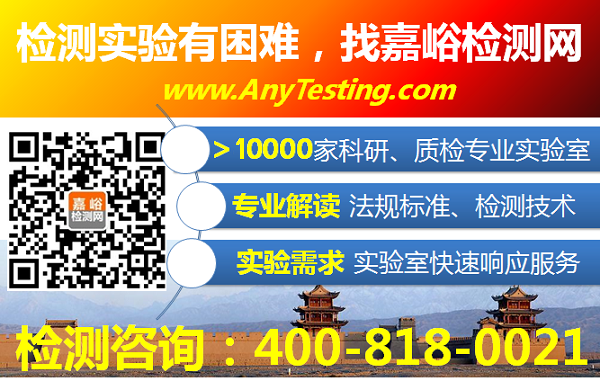