特种合金钢是用来制造各种应用于航天、航空、高铁等领域产品,其作为重大装备与构件制造材料基础,产品的失效分析又促进特种合金钢的发展。在以往失效分析中得到的信息能够准确的反馈到产品设计、制造和使用部门,再通过科学的分析、采取措施能够减少和避免失效情况再次发生。
一、失效分析概述
1、产品失效
失效分析:失效分析是判断产品的失效模式,查找产品失效机理和原因,提出预防再失效对策的技术活动和管理活动总和。
主要内容:明确分析对象,确定失效模式,研究失效机理,判定失效原因,提出预防措施 ,包括设计改进。
主要目标:模式准确,原因明确,机理清楚,措施得力,模拟再现,举一反三。
2、零部件失效
零部件失效:机械零件由于某种原因丧失预定的功能时,认为他完成了失效。零件的失效,特别是那些事先没有明显征兆的失效,往往会带来巨大的损失,甚至导致重大事故。对机械零件的失效进行分析,找出失效的原因,并提出防止或推迟失效的措施。
① 构件完全破坏,不能继续工作;
② 严重损伤,继续工作不安全;
③ 虽能安全工作,但不能起到满意的预期作用。
上述情况中任意一种发生均认为零件已经失效。失效分析对零件的设计、选用、加工以及使用有重要作用。
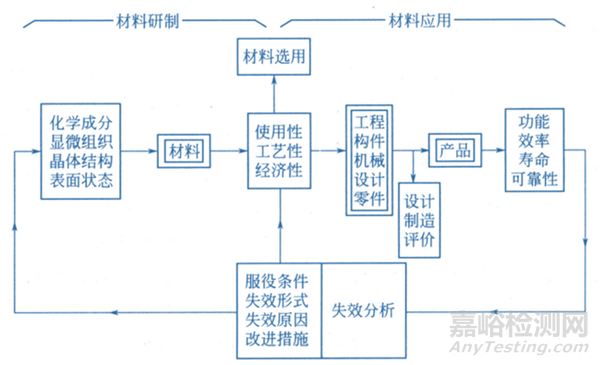
图1 失效分析与材料研制及应用
3、失效分析作用
能够作为材料选用与设计系统重要的反馈信息
作为产品可靠性和系统安全性重要技术基础
产品质量设计与管理必不可少的重要环节
维修工程理论依据与安全工程技术保证
产品全寿命周期的重要技术和理论支撑
4、失效分析思路
失效分析分为事前分析、事中分析和事后分析。
事前分析:主要采用如故障树分析法、事件时序树分析法和特征一因素图分析法等逻辑思维方法,其主要目的是预防失效事件的发生。
事中分析:主要采用故障诊断与状态监测技术,用于防止运行中的设备发生故障。
事后分析:是采用实验检测技术与方法,找出某个系统或零件失效的原因。通常所说的失效分析是指 的事后分析。
实际上,事前分析和事中分析必须以事后分析积累的大量统计资料为前提。
基于系统工程的角度分析一个复杂产品和所组成的系统,实际上是一个材料系统,产品材料失效及事故如图2所示,就飞机而言,由上万甚至几十万个零件组成,涉及几百种甚至上千种材料。对某一种失效零部件而言,机械零部件所处的具体小环境则是重要的外界环境条件。产品受到的环境作用不仅是单一某项作用,往往可能是出现不合理的工艺环境、自然环境和使用运行环境的结合、综合、协同作用,或者是合理的加工工艺制成的制品遭遇 自然环境和使用运行环境的结合、综合、协同作用。例如真空环境下,材料制件受到动载荷的循环作用可能导致疲劳损伤,事实上绝大多数承受动载荷的制件是在受到污染的空气环境下运行的,所出现的不是纯粹的疲劳而是腐蚀疲劳断裂,或者是污染介质加上接触摩擦循环应力所发生的接触腐蚀疲劳断裂;纯粹的摩擦比较少见,多为污染空气作用下的摩擦磨损、磨蚀;装配成产品的制件,不仅承载动应力也要承载静应力,或是承载摩擦应力,所以,危害性较大的腐蚀损伤,也多是应力和环境的协同作用的结果,即为应力腐蚀,或是腐蚀疲劳。
图2 材料失效模式及事故
5、失效模式及原因
失效原因的判断作为整个失效分析的核心和关键,可以确定失效机理、提出预防措施。
1) 失效模式
失效模式指失效的外在宏观表现形式和过程规律,一般可理解为失效的性质和类型。失效故障的表现形式称为失效故障模式,如疲劳断裂、磨损和腐蚀等。引起故障的机械的、物理的、化学的、生物的或其他的过程称之为失效故障机理。产品的故障按照其规律可以分为早期偶然故障与耗损渐变故障。早期偶然故障发生概率由产品本身的材料、工艺、设计所决定。耗损渐变故障是产品性能随时间的推移逐渐变化而产生的故障,如轴承由于使用磨损,性能逐渐退化,最终超过规定技术指标不能再用。
2) 失效原因
失效原因可分为确定原因和不确定原因。确定性失效原因应包括失效产生的具体力学参量或者具体的冶金工艺参数。不确定性原因在失效分析中由于分析对象的原始资料不全,或者由于分析手段的限制,只能对失效原因作出模糊的判断,而不能作出明确的界定。失效机理指失效的物理 、化学变化本质和微观过程可以追溯到原子、 分子尺度和结构的变化 。当然,失效机理也要表现出一系列宏观(外在的)的性能 、性质变化和联系。
二、特种合金钢失效原因
特种合金钢失效原因包括技术因素和管理因素两部分。管理因素则是设计错误、制造缺陷、维修不当和使用违规等过程由于管理失控所导致材料累积损伤、材料性能退化,最后导致材料失效。技术因素中主要有材料累积损伤、材料性能退化、材料复杂环境和材料原始缺陷四部分,如下图所示。
图3 特种合金钢失效原因
1) 材料累积损伤
材料累积损伤意味着产品出现完整性的破坏,产品不能满足其规定功能的要求,是产品失效的原因之一。材料的累积损伤失效模式及宏观表象见表1.
表1 累积损伤失效模式、失效原因和表象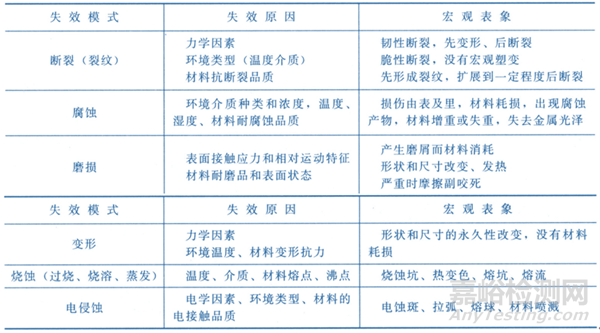
2) 材料性能退化的判据
特种合金钢性能在使用过程中由于外界条件的作用下可能发生退化。这种退化目视检查难以发现,需要通过专门的性能测试仪器检验方能知道材料性能是否退化。有些性能则必须通过破坏性的取样测试才能鉴定性能是否退化,一般在系统或装备设计时,对所需求的性能都规定了额定值或范围,当产品的这些性能不符合规定值时往往出现故障,而不能修复时则失效。因此,这些额定值或范围就是失效的判据。具有特殊性和隐性特征。
材料性能退化的同时,也呈现材料的累积损伤,就看两者谁先导致产品失效。材料某些性能的退化,并不一定表现为材料累积损伤,而材料的累积损伤也不一定表现为材料性能退化。材料性能退化和材料累积损伤同时出现,这时产品失效的宏观表象将更加丰富、清晰。
3) 材料复杂环境行为
材料环境行为 :特种合金钢的各种物理、化学过程,如屈服过程、断裂过程、导电过程、磁化过程、相变过程、氧化过程、腐蚀过程、溶解过程等,不同过程对应不同性能。
环境因素可归纳为物理环境 、化学环境、复合环境三种。
物理环境主要包括温度、传热介质、传热方式等热学环境和力学环境。
化学环境包括介质种类和浓度、温度、湿度、原子氧、催化剂、缓蚀剂、大气、土壤和海水等。
复合环境主要三种形式依次为复合物理环境、复合化学环境、复合物理化学环境。
特种合金钢累积损伤和性能退化所导致产品失效,都是与外界环境交互作用。不同的环境条件导致不同类型的材料累积损伤和不同类型的材料性能退化。
① 使用条件下材料的累积损伤往往集中在某些关键部位。如孔的应力集中处易产生疲劳裂纹、摩擦副表面易磨损、触点处易电侵蚀等。严格来讲,这些累积损伤集中部位材料结构已经发生变化,甚至发生质的变化 (如腐蚀产物等)。而表层剥蚀区域之外的材料,却依然保持原有的力学性能。
② 累积损伤集中发生在关键部位,但是相邻或相关部位的材料性能受到一定影响,发生性能退化。比如,孔边产生裂纹时,孔周附近的材料也承受了交变载荷,只不过载荷的幅值较小,根据迈纳累积损伤原则,它也受到一定比例的疲劳损伤。
③ 累积损伤择劣发生在薄弱部位,但整个材料各处或较大范围的性能也发生变化。比如,涡轮叶片过热、过烧使整个叶身材料发生性能退化,涡轮盘长期使用中超温、超转后,不仅盘径伸长,而且剩余疲劳强度和剩余持久强度都会明显下降。
材料的累积损伤都是基于材料结构的损伤,而材料结构的损伤不是一个自发过程,它以相应 的外界环境为条件。不同的材料结构损伤需要不同的外界环境条件。
4) 材料原始缺陷
导致产品失效的材料原始缺陷是主要材料设计、材料选用、加工制造时留下的原始缺陷,主要有两类:
一是成分、结构、组织特征的缺陷:
①形状、尺寸方面的 缺陷 ;
②材料冶金缺陷;
③加工工艺缺陷;
④热处理工艺缺陷;
⑤表面缺陷。
二是材料性能缺陷:
①物理性能不合格;
②化学性能不合格;
③复合使用性能不合格。
当材料存在上述两类缺陷时,可能存在以下3种情况 :
①当缺陷非常严重时,可立即导致产品失效,如淬火裂纹已超过临界疲劳裂纹尺寸时;
②当缺陷尚未超过材料失效的临界损伤尺寸时,则使用中很快发生累积损伤,导致产品早期失效;
③当性能不合格,但是仍能维持产品低水平运行时,加速材料性能的退化,导致产品早期失效。
三、特种合金钢失效分析
容易引起失效的服役条件有两种情况:
1)一种情况是设备在服役过程中受到超过设计要求的载荷作用,或者材料内部存在残余应力没有引起设计者注意,再累加上服役应力造成失效。
2)另一种情况是在设计时没有考虑到实际工况的某些恶劣环境的影响。如下图所示为失效分析的基本环节示意。
图4 失效分析的基本环节示意
1、失效形式
① 塑性变形受静载的零件产生过量的塑性(屈服)变形,位置相对于其他零件发生变化,致使整个机器运转不良,导致失效。
②弹性失稳细长件或薄壁筒受轴向压缩时,发生弹性失稳,丧失工作能力,甚至引起大的塑性弯曲或断裂。
③蠕变断裂受长期固定载荷的零件,在高温下工作时,蠕变量超出规定范围而处于不安全状态,严重时可能与其他零件相碰,造成断裂。
④磨损两相互接触的零件相对运动时,表面发生磨损。磨损使零件尺寸变化,精度降低,甚至发生咬合、剥落,而不能继续工作。
⑤快速断裂受单调载荷的零件可发生韧性断裂或者脆性断裂。
⑥疲劳断裂零件受交变应力作用时在比静载屈服应力低得多的应力下发生突然断裂,断裂前往往没有明显征兆。
⑦应力腐蚀断裂零件在某些环境中受载时, 由于应力和腐蚀介质的联合作用,发生低应力脆性断裂。
弹性失稳、塑性变形、蠕变和磨损等,在失效前一般都有尺寸的变化,有较明显的征兆,可以采取预防措施,从而避免断裂失效发生;低应力脆断、疲劳断裂和应力腐蚀断裂事前没有明显征兆,断裂突然发生而引发灾难性的后果。
2、影响失效的因素
① 材质冶金因素:材料的化学成分超标或存在标准中未予规定的微量有害元素;
② 表面完整性:表面完整性不符合要求或在使用中遭到破坏均会造成零件的力学性能、物理性能与化学性能下降,从而诱发裂纹在这些部位萌生。
③ 表层残余应力的类型、大小与分布:残余拉应力往往与外加应力叠加而促进断裂失效,残余拉应力提高应力腐蚀与氢脆等敏感性。
④ 应力集中:零件的几何形状设计不当或加工质量不符合要求或者表面出现腐蚀和磨损,均会导致应力分布不均,局部应力集中导致零件的实际抗力显著降低,疲劳断裂失效大多起源于零件的尖角、倒角、油孔、键槽及圆弧过渡处等。
⑤ 环境因素 :温度与介质引起抗力下降。温度升高会引起材料的疲劳抗力、 蠕变抗力等降低,温度的急剧变化会使零件抗热疲劳能力降低,低温会引起低温脆断等。
根据零件或构件破坏的特点、所受载荷的类型以及外在条件,机械零件失效的形式,可以分为4大类型:变形失效、断裂失效、表面损伤失效和复合失效。
图5 零件失效方式的分类
3、失效产生过程
特种合金钢零件或构件失效主要产生于设计、材料、加工和安装、使用、维护等六个过程。
图6 导致零件失效的主要产生过程示意
四、失效分析流程与方法
1、失效分析的方法及过程
1)失效分析方法主要是分为宏观和微观两个部分。
表 5-2 失效分析方法、功能以及应用
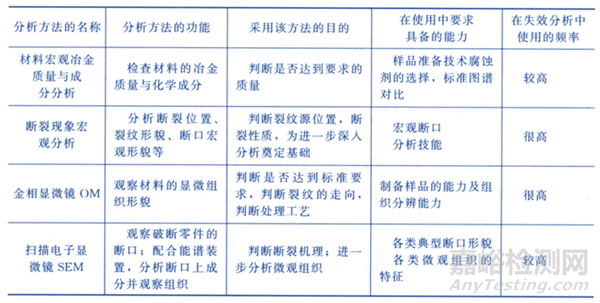
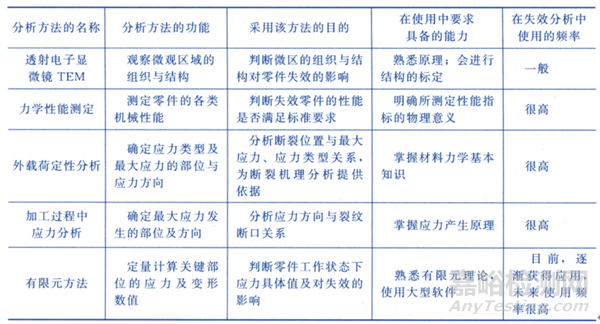
2)失效分析过程主要包括三部分失效实物、宏观检测分析、微观检测分析。
①失效实物
收集失效实物的各个零件和残片。尽量多地了解到失效零件的实际工作条件、使用过程和制造质量情况 。以轴承为例,具体包括以下的内容:轴承所服役的机器设备的工作状况、载荷和运行速度。
②宏观检查
零件尺寸精度测量和表面状态分析等宏观检查,是失效分析最重要的环节。以轴承为例,总体的外观检查,可了解轴承失效的概貌和损坏部位的特征,估计造成失效的起因,察看缺陷的大小、形状 、部位、数量和特征并确定截取的部位做进一步的微观检查和分析。
③微观分析
微观分析包括光学金相分析、电子显微分析、探针和电子能谱分析等。主要是根据失效特征区的微观组织结构变化和对疲劳源、裂纹源的分析为失效分析提供更充分的判据或反证,因而这一环节是非常重要的。
五、特种合金钢产品残余应力分析
残余应力是指没有外加负载的情况下存在产品内的应力 ,本质是产品内非均匀永久变形导致的。特种合金钢制零件或构件从原材料到最后成型经过一系列的热加工与冷加工过程,会产生各种残余应力,这些内应力如果不能及时消除,残留在零件或构件内部成为失效的内在重要原因。
1、残余应力分析
钢进行加工的工艺过程中,会同时产生组织应力与热应力,并且这两种应力的方向相反,在淬火过程中产生的残余应力是两种应力叠加的结果。目前已经有总结除分析残余应力的规律:
① 变形一般取决于冷却初期零件心部的应力状态,开裂一般取决于零件冷却后期表面应力状态。根据变形与开裂情况判断组织应力与热应力作用大小。
② 组织应力造成的残余应力在工件表面,最大残余应力方向是切向,如果形成裂纹为与轴的轴线平行的纵向裂纹,最大切向应力值随尺寸增加而增加。热应力造成的残余应力在工件心部,最大残余应力方向是轴向,如果形成裂纹为与轴的轴线垂直的横纵向裂纹,最大轴向应力值随尺寸增加而增加。
③ 组织应力与热应力均可以产生 3个方向的应力,即轴向、 切向与径向应力。它们存在位置相同但是作用方向相反,有互相抵消作用 。两种应力均有致裂与抑裂的双重作用。
④ 合成应力可以分成3类 :组织应力型、热应力型、过渡型。合成应力造成的最大残余应力在距工件表面一定深度的区域。最大残余应力由轴向组织应力与切向热应力的合成,形成的裂纹与轴的轴线成一定角度。角度越小表明组织应力作用越大,裂纹越接近表面;角度越大表明热应力作用越大,裂纹越接近心部。
2、表面处理后残余应力分布
经过表面处理技术的零件存在残余应力分布,揭示残余应力分布规律 ,有助于进行失效分析。
1)经表面淬火工件残余应力分析
对于表面淬火产生的残余应力分布是很复杂的,与材料的成分、工件尺寸 、硬化层深度、加热速度等多种因素有关,难 于精确地理论判断。利用总结出的规律进行分析:将硬化层认为是表面层 ,其余部分认为是心 部,见表 3
表 3 表面淬火过程中组织应力残余应力产生过程与分布特点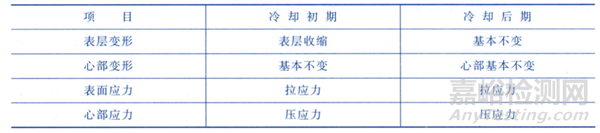
冷却初期:表面收缩受到心部抵制,热应力的特点表为拉应力 、心部压应力。组织应力与热应力相反,表面压应力 、心部拉应力。冷却后期由于心部冷却引起的应力反向问题。
热应力产生的残余应力分布特点是:表层拉应力而内层(或者说心部)是压应力。组织应力产生的残余应力分布特点是:表层压应力而内层拉应力。合成应力的特点与样品的直径和硬化层深度有很大关系。
如果样品的直径很大硬化层深度较浅,可以将表层看成是工件尺寸很小的零 件,当样 品尺寸很小时,合成残余应力的特点是组织应力型的,所以表面残余应力特点应该是压应力型。随着样品直径的减少,硬化层深度的增加,表面压应力 就会不断减少。
2)渗碳产生的残余应力分析
渗碳淬火产生的残余应力同样是复杂的,与渗碳层深度 、材料成分、渗碳层中含碳量、冷却速度等诸多因素有密切关系。采用圆柱样品进行整体淬火得出的一些基本规律进行分析。
热应力产生残余应力的特点应该与圆柱样品进行整体淬火类似,即表面压应力、心部拉应力。渗碳淬火后合成的残余应力是表面压应力,心部拉应力。渗碳层深度影响规律是随深度增加,表面残余压应力减少。样品直径影响规律是随直径 增加 ,表面残余压应力减少 。
3)氮化、氮碳共渗、渗金属产生的残余应力
氮化过程中并不伴随马氏体转变,产生应力的原因有两点:一是氮化过程中形成氮化层,氮化层的比容比基体材料大;二是氮化层的热膨胀系数比基体材料大。组织变化应力是在氮化过程中产生的, 可以用类似模型分析,结果见表 4。
表4 氮化后表面应力
4)热喷涂产生的残余应力
热喷涂产生的残余应力:主要是由在涂层制造过程中的加热和冲击能量作用的结果及基体与喷涂材料之间物理 、力学性能差别造成的,分热应力与淬火应力两种。
热应力是由于温度变化材料发生热胀冷缩,由于基体与涂层材料热膨胀系数不同从而产生残余应力 。淬火应力是由于单个喷涂颗粒快速冷却到基体温度,颗粒要收缩从而产生的应力 ,淬火应力均是拉应力。
热喷涂残余应力导致的失效形式主要有涂层 开裂 、翘曲和分层 。在实际情况下许多涂层的失效并不只是一种失效形式。该最大应力作用下,零部件不应该出现疲劳断裂,但是实际情况是零部件发生了疲劳断裂,因此认为估算出的最大应力值出现较大误差。
六、特种合金钢腐蚀疲劳失效分析
航空起落架、机翼大梁 、刹车轮毅 、涡轮盘、叶片等关键部件因腐蚀疲劳而导致早期断裂失效,有的甚至出现重大事故。腐蚀疲劳断裂是在腐蚀环境与交变载荷协同、交互作用下发生的一种综合失效模式。腐蚀产物是分析、判定失效零件工作环境和工作时间的重要依据。
腐蚀疲劳分析主要包括影响因素、断口形貌以及失效判据。
图7 腐蚀疲劳失效分析
1、影响因素
影响腐蚀疲劳断裂过程的相关因素有以下几种 :
①环境因素 :包括环境介质的成分、浓度、介质的酸度 (pH值)、介质中的氧含量、介质的电极电位以及环境温度等;
②力学因素 :包括加载方式、平均应力 、应力比、载荷 波形 、频率以及应力循环周数 ;
③特种合金钢冶金因素 :包括材料成分、强度、热处理状 态、 组织结构、冶金缺陷、夹杂物等 。
机械疲劳 、腐蚀疲劳和应力腐蚀三者之间的关系如图8所示。三者没有明显界限,在腐蚀疲劳裂纹的萌生阶段,腐蚀起了重要的作用 。腐蚀疲劳同样经历两个阶段:腐蚀疲劳裂纹 的萌生和腐蚀疲劳裂纹的扩展 。在腐蚀环境中,腐蚀疲劳裂纹的萌生不仅与应力及表面状态有关,而且与腐蚀和表面完整性 、腐蚀反应与应力状态之间的相互作用有关 。
图8 机械疲劳、腐蚀疲劳和应力腐蚀疲劳关系
2、断口形貌
腐蚀疲劳的断裂特征和一般疲劳断裂一样,腐蚀疲劳的断口上也有源区、扩展区和瞬断区,腐蚀疲劳断口有其独有的特征,主要表现在如下几方面:
①断口低倍形貌呈现出明显的疲劳弧线。
②腐蚀疲劳断 口的源区与疲劳扩展区一般均有腐蚀产物 ,通过微区成分分析,可以测定出腐蚀介质的组分及相对含量。断面上有腐蚀产物不是判定是否腐蚀疲劳断裂的唯一判据。
③腐蚀疲劳断裂一般均起源 于表面腐蚀损伤处(包括点腐蚀、晶间腐蚀、应力腐蚀等),因此,大多数腐蚀疲劳断裂的源区可见到腐蚀损伤特征。
④腐蚀疲劳断裂扩展区具有某些较明显腐蚀特征,如腐蚀坑、泥纹花样等。
⑤腐蚀疲劳断裂的重要微观特征是穿晶解理脆性疲劳条带。
⑥在腐蚀疲劳断裂过程中,当腐蚀损伤占主导地位时,腐蚀疲劳断口呈现穿晶与沿晶混合型。
⑦在频率很低的情况下,腐蚀疲劳断口呈现出穿晶解理与韧窝混合特征。
3、失效判据
在实际的产品失效分析中,判断腐蚀疲劳断裂失效的主要判据:
①产品是在交变应力和腐蚀条件下工作,交变应力的频率和应力比一般处在腐蚀疲劳区内。在液态、气态和潮湿空气中有腐蚀性元素;
②断裂表面颜色灰暗,无金属光泽,通常可见到较明显的疲劳弧线;
③断裂表面上存在有腐蚀产物和腐蚀损伤痕迹;
④疲劳条带多呈解理脆性特,断裂路径一般为穿晶,有时出现穿晶与沿晶混合型甚至沿晶型。
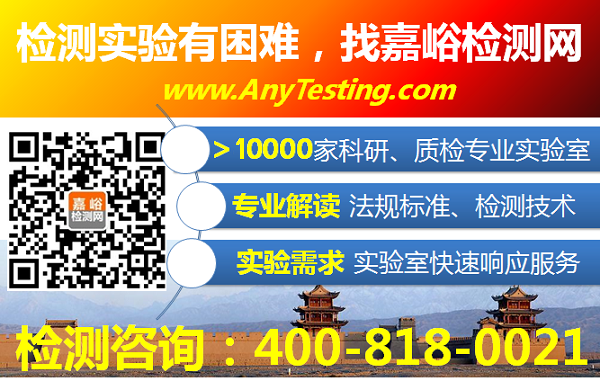