摘 要:阐述了铝/镁合金压力铸造、挤压铸造和消失模铸造等特种精密铸造技术的最新研究进展。研究表明:高真空压铸可以显著提高铝/镁合金压铸件的致密性,实现铝/镁合金压铸件热处理强化,进一步提高铝/镁合金压铸件的性能。充氧压铸技术适用于制备高致密、高强铝合金压铸件。半固态压铸和铸锻双控成形技术也是制备高致密、高强度铝/镁合金压铸件的新方法,未来有较大应用潜力。铝/镁合金挤压铸造技术可显著提高金属熔体充型、补缩能力,实现高压凝固和少量塑性变形,提高铸件的致密性和力学性能。铝/镁合金真空低压、振动和压力消失模铸造技术可以提高金属液充型能力、细化组织、提高组织致密性,明显提高铸件力学性能。真空低压消失模壳型铸造技术可以解决普通消失模铸造易出现的孔洞、增碳和夹杂等缺陷,以及浇不足和浇注温度高等问题,是一种生产复杂薄壁高质量铝/镁合金精密铸件的新方法。
关键词:铝/镁合金;特种精密铸造技术;压力铸造;挤压铸造;消失模铸造
1、序言
铝合金、镁合金是工程应用中密度较小的金属结构材料,具有比强度和比刚度高、导热性好、尺寸稳定、减振降噪能力突出、电磁屏蔽性好,以及优异的铸造、切削加工性能,且易于回收,广泛应用于航空航天、汽车、通信电子和军工等领域[1,2]。随着上述行业的迅速发展,新一代飞机、高推重比航空发动机、机载设备、汽车零部件以及新一代武器装备对其结构重量要求十分苛刻,要求零部件大量采用轻质铝合金、镁合金材料,零部件的结构也向整体化、复杂化和精密化的方向发展,因此对大型复杂薄壁铝合金、镁合金精密铸件的需求越来越大、性能要求越来越高[3,4]。
铝/镁合金精密铸件通常采用砂型铸造、金属型铸造、压力铸造、挤压铸造、消失模铸造等铸造技术进行生产[5-7]。铝/镁合金材料在铸造过程中具有吸气严重、氧化燃烧加剧、补缩困难等问题,导致铝/镁合金充型困难、致密性差、力学性能偏低等问题,尤其对于大型复杂薄壁铝/镁合金精密铸件,上述问题更为突出,压力铸造、挤压铸造、消失模铸造等特种精密铸造技术对解决上述问题具有一定优势。本文将阐述铝/镁合金压力铸造、挤压铸造和消失模铸造等特种精密铸造技术的最新研究进展,以期为铝/镁合金精密铸件成形提供一定参考。
2 铝/镁合金压力铸造技术
压力铸造具有成形精度高、生产效率高、铸件力学性能良好等优点,越来越广泛地应用于汽车零部件制造领域[8,9]。然而,由于普通压力铸造是熔体在高压、高速下快速填充模具型腔,型腔中的气体来不及排出,从而在铸件内部易形成气孔等缺陷,因此压铸件通常无法进行固溶热处理及焊接加工,这严重阻碍了压铸件的更广泛应用。为了解决此问题,目前国内外有两个途径:一是改进现有设备,特别是对三级压射机构的压射机,控制压射速度、压力,控制模型内的气体卷入数量;二是发展特殊压铸工艺,如真空压铸、充氧压铸、半固态压铸等[10]。下面介绍几种压力铸造的新技术和方法。
2.1 高真空压铸技术
高真空压铸是在普通压铸的基础上,采用辅助的高真空控制系统、真空泵、真空截止阀等装置,在金属液填充模具型腔之前,将型腔中的气体抽出,使模具型腔中形成较高的真空度,并保持至填充结束[8,10]。
在高真空压铸过程中,型腔处于真空状态,紊流的金属液不再会卷入气体形成气孔,从根本上消除了压铸零件气孔的成因。因此,铸件含气量得到降低,气孔率下降,致密度提高;铸件的整体力学性能得到改进,抗拉强度、伸长率、硬度和密度均有所提高;同时可以满足热处理、焊接及耐压试验等要求。高真空压铸工艺一般要求压射过程中型腔有效真空压力<5kPa,以大幅度减少铸件中气孔的存在,满足后续热处理及焊接工艺的要求[9,10]。
高真空压铸的关键是能在很短的时间内获得高真空。为此,必须在铸型结合处建立良好的密封系统,在真空建立时有阻止金属液流入真空管道的真空闭锁阀。其中,最为关键的核心装备是真空截止阀和真空压铸控制系统。真空压铸用真空截止阀具有的功能是能够迅速排除模具型腔内的气体,并在排除型腔气体后能及时关闭分离抽真空系统与模具,以防止金属液进入真空抽气管道造成堵塞。
华中科技大学研发了NHVDC 型压铸用多向抽真空装置,是一种可以同时在型腔、压室和模架三个方向上抽真空的真空压铸辅助装置。相比传统的单一从型腔抽真空,该系统装置提高了抽气效率。上海交通大学王雪杨等[11]研究了真空压铸镁合金减振塔的组织和性能,表明压铸AE44镁合金减振塔沿厚度方向微观组织分为3个区域,细晶层由细小α-Mg和共晶组织组成;缺陷带分布在试样两侧,相对于其他区域,缺陷带内共晶组织体积分数较高;中心区域α-Mg主要有细小等轴晶和大块枝晶两种形貌,大块枝晶形成在压室内,且主要分布在中心区域。此外,减振塔的平均抗拉强度最小值为215MPa、最大值为232MPa,波动较小;伸长率在8.4%左右。
图1所示为高真空压铸件和普通真空压铸件对比照片。图2所示为通用汽车公司生产的铝减振塔铸件和镁门内铸件。图3所示为特斯拉公司采用先进压铸技术生产的大型铝铸件。
图1 高真空压铸件和普通真空压铸件对比
图2 通用汽车公司生产的铝/镁合金铸件
图3 特斯拉大型铝铸件
未来,压力铸造技术的研究将集中在铝/镁合金铸件的发展,以实现更薄壁(接近1mm)、更大铸件生产,通过合金开发、先进的工艺仿真和优化以及优化使用真空通道真空压铸过程的水模拟试验等技术手段[1]。
2.2 充氧压铸技术
充氧压铸是将干燥的氧气充入压室和压铸模型腔,以取代其中的空气和其他气体,其原理如图4所示。当铝合金压入压室和压铸模腔时与氧气发生化合生成Al2O3,形成均匀分布的Al2O3小颗粒(直径在1μm以下),从而减少或消除了气孔,提高了压铸件的致密性。这些小颗粒分散在压铸件中,占总质量的0.1%~0.2%,不影响机械加工。充氧压铸仅适用于铝合金[10]。
图4 充氧压铸工艺原理
由于充氧压铸消除或减少了压铸件内部的气孔,因此铝合金强度可提高10%、伸长率增加1.5~2倍,压铸件可进行热处理;且Al2O3有防腐蚀作用,充氧压铸件可在200~300℃的环境下工作;与真空压铸相比,充氧压铸的结构简单、操作方便、投资少。但充氧压铸也有以下局限性。
1)必须使用胶体石墨系列的水溶性脱模/润滑剂或固体粉末。
2)氧气置换和除去水分的时间稍长。
3)对压射室及冲头要防止粘模及吃入飞边。
4)铸造合金中Fe、Mn含量要适当。
5)在熔液与氧气完全反应下,铸造条件优化较难[10]。
KANG等[12]对充氧压铸技术与传统压铸技术制备的Mg-Al系合金进行对比,发现充氧压铸技术可使氧原子和镁原子结合为氧化镁,在压力和流动条件下呈弥散分布,为α-Mg提供形核质点,从而细化Mg-Al系合金晶粒尺寸;此外,Mg-Al系合金铸件中气孔缺陷也明显减少。
2.3 半固态压铸技术
半固态铸造成形是在液态金属凝固过程中进行搅拌,使普通铸造凝固易于形成的树枝晶网络骨架被打碎而形成分散的颗粒状组织形态,从而制得半固态金属浆料,然后将其铸成坯料或压成铸件[13]。半固态铸造成形技术可分为半固态流变压铸和半固态触变压铸,如图5所示,其原理如图6所示。
图5 半固态铸造成形过程
图6 半固态流变压铸成形原理
李东南等[14]研究了半固态流变压铸AZ91D合金的组织与性能。研究表明,半固态压铸使α-Mg从枝晶态转变为颗粒状,使得半固态流变压铸AZ91D合金的抗拉强度和伸长率分别从138MPa和3.2%提升到185MPa和4.6%。图7所示为采用半固态铸造成形的零件。
图7 半固态铸造成形零件
2.4 铸锻双控成形技术
铸锻双控成形技术是针对压铸、重力铸造存在的铸造缺陷而提出的一种成形方法。它是将铸造和锻造两种成形方式先后在同一模具、同一生产过程一次完成零件的生产,其成形过程如图8所示 [15,16]。
图8 铸锻双控成形示意
铸锻双控成形的效率高,既能成形铸造合金又能成形变形合金,成形过程中短时保压静置时间的长短能够决定制件被锻造时的状态,静置时间较短时,制件处于液态,经锻造制件的合金组织更加致密;静置时间较长时,制件合金处于固态,经锻造合金内部组织发生了明显的塑性变形,制件的力学性能相对于铸件有明显的提高,其性能接近于锻件。该成形方法不仅能解决压铸不能生产厚壁件、力学性能低且不能热处理强化的缺点,又能解决重力铸造效率和力学性能低等缺点[17,18]。
李伟东等[15]研究了锻造压力对铸锻复合成形A356铝合金铸锻件组织及性能的影响。当锻造压力为120MPa时,未经热处理的铸锻件的抗拉强度和伸长率分别为216MPa、16.7%;当锻造压力为60MPa时,经T6热处理的铸锻件的抗拉强度最大值能达到320MPa,伸长率为11.6%。李广德等[19]研究了浇注温度和锻造压力对铸锻复合成形AZ80Ce 镁合金汽车转向控制臂显微组织和力学性能的影响,发现随浇注温度升高或锻造压力增大,试样的冲击吸收能量逐渐增大,晶粒逐渐变小、均匀,显微组织逐渐改善。图9所示为铸锻双控成形镁合金轮毂零件。
图9 铸锻双控成形镁合金轮毂零件
3、 铝/镁合金挤压铸造技术
挤压铸造技术(Squeeze Casting),也称液态模锻(Liquid Die Forging),是一种将一定量金属熔液直接注入开式的金属模膛内,随之封闭模膛,对其施以静压力,以实现流变充填、高压凝固和少量塑性变形,最终获得优质制件的金属加工过程[20]。它兼具铸造和锻造优点的短流程、高效、近净成形技术[21]。挤压铸造压力可提高金属熔体充型、补缩能力,对合金的铸造性能要求较低、选材范围广,适用于大部分铸造和变形合金,近年来尤其在铝合金和镁合金材料上得到了广泛应用。
依据挤压铸造过程中所施加压力的作用方式,挤压铸造工艺主要分为直接挤压铸造和间接挤压铸造两大类[22,23],如图10所示。
图10 挤压铸造工艺的分类
直接挤压铸造类似于锻造工艺,挤压力直接作用在金属液上,压力传递路程短,液态金属承受的等静压大,高压凝固效应显著,一般适于形状不太复杂的厚壁铸件。间接挤压铸造是在挤压冲头的作用下使金属液通过浇道充型[24]。
间接挤压铸造工艺大致与压铸工艺接近,但其挤压力较大、充型速度相对较小,制件形状由合模后形成的型腔来保证。冲头的作用将液态金属挤入型腔。金属液充填结束后,维持一段保压时间,此时压力通过余料端和内浇口金属,将压力传递至制件上。由于传递压力有限,其适用于批量大、形状较复杂或小尺寸零件的生产[25]。
陈露等[26]研究了重力铸造和挤压铸造成形工艺和热处理工艺对Mg-5Zn-2.5Cu-0.4Zr热物理性能的影响。挤压铸造相比重力铸造对于合金的热导率有小幅提升,从128.22W/(m•K)提升至130.35W/(m•K),但热膨胀系数从22.03×10-6K-1升高至23.39×10-6K-1。挤压铸造和T1热处理共同作用能够实现热导率和热膨胀性能的同步优化。SHASTRI等[27]研究了重力铸造、挤压铸造和高压压铸3种铸造工艺对AZ91合金组织和性能的影响规律。挤压铸造工艺可明显细化枝晶臂间距,改善析出相形貌,减少缩松、缩孔等缺陷,显著提高镁合金的致密性。
随着挤压铸造技术的快速发展,一些挤压铸造新技术不断出现,如双重挤压铸造、半固态挤压铸造等。其中,双重挤压铸造结合了间接挤压铸造和直接挤压铸造工艺的特点,依靠间接挤压工艺成形毛坯,采用直接挤压工艺压实铸件,可生产内部组织致密、形状及尺寸精确的较复杂铸件。半固态挤压铸造是将含有球晶或近球晶固相的固液混合物在凝固温度范围内进行挤压铸造,可分为流变挤压铸造和触变挤压铸造。图11所示为挤压铸造成形的铝合金和镁合金零件。
图11 挤压铸造零件
4、 铝/镁合金特种消失模铸造技术
铝/镁合金特种消失模铸造技术,是为了解决铝/镁合金普通消失模铸造过程中充型浇注、氧化燃烧、针孔等问题,提高消失模铸造零件的性能,目前正在研究开发以下几种特种消失模铸造技术。
“与经销商共同做大做强、携手经销商让更多农民增收致富。”哈尔滨禾硕农业科技发展有限公司总经理唐春雨表示,2018年后,禾硕农业把“专业的农化服务+移动互联网+精细化运作+禾硕商学院”的价值营销框架呈现在经销商面前。通过熟悉当地市场、增加客户粘度、提供专业化管理方法和依靠团队作战等方式,禾硕农业不仅营造了禾硕农业一家人的企业氛围,同时也让合作伙伴认可了禾硕的一家人文化。未来,禾硕农业还将不断强化内功,做大做强,进一步用专业创造价值、用服务去改变农业。
4.1 真空低压消失模铸造技术
真空低压消失模铸造技术是将真空消失模铸造与低压铸造有机地结合起来,综合了低压铸造与真空消失模铸造的技术优势,在可控的气压下完成充型过程,大幅提高了合金的充型能力;与压铸相比,设备投资小、成本低、铸件可热处理强化;而与砂型铸造相比,铸件的精度高、表面粗糙度值低、生产率高、性能好;在反重力作用下,直浇口成为补缩短通道,浇注温度的损失小,液态合金在可控的压力下进行补缩凝固,合金铸件的浇注系统简单有效、成品率高、组织致密;需要的浇注温度低,适合于多种有色合金浇注成形[28,29]。其原理如图12所示。
图12 真空低压消失模铸造工作原理
图13所示为采用两种不同消失模铸造工艺获得的电动机壳体(最小壁厚2.5mm)铸件。从图13可看出,采用真空低压消失模铸造可成形出形状完好、轮廓清晰的镁合金电动机铸件,而采用重力消失模铸造时,铸件不能完全充型,出现了严重的浇不足缺陷[30]。
图13 不同铸造工艺获得电动机壳体镁合金铸件对比
4.2 压力消失模铸造技术
压力消失模铸造技术是消失模铸造技术与压力凝固结晶技术相结合。其原理是在带砂箱的压力罐中,浇注金属液使泡沫模气化消失后,迅速密封压力罐,并通入一定压力的气体,使金属液在压力下凝固结晶成形的铸造方法。这种铸造技术的特点是能够显著减少铸件中的缩孔、缩松及气孔等铸造缺陷,提高铸件致密度,改善铸件力学性能。压力下凝固时,外力对枝晶间液相金属的挤滤作用以及使初凝枝晶发生显微变形,可大幅提高冒口补缩能力,使铸件内部缩松得到改善;加压凝固还会使氢析出需更高的内压力才能形核形成气泡,抑制针孔的形成,同时压力增加了气体在固相合金中的溶解度,使可能析出的气泡减少[31,32]。其原理如图14所示。
图14 压力消失模铸造原理
图15所示为外加压力对试样孔隙率和密度的影响规律。从图15可看出,当外加压力达到0.5MPa时,ZL101铝合金消失模铸件的针孔基本消失。压力继续提高,铸件密度提高趋缓。
图15 外加压力对ZL101试样孔隙率和密度的影响规律
图16所示为不同外加压力对ZL101铝合金抗拉强度与伸长率的影响。随着外加压力的增大,试样的抗拉强度、伸长率逐渐提高。当0.5MPa压力下凝固的ZL101铝合金试样与常压下消失模铸造试样比较,抗拉强度从137MPa提高到了177MPa,提高33.9%。
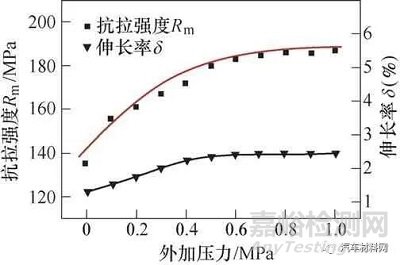
图16 外加压力对ZL101试样抗拉强度与伸长率的影响
4.3 振动消失模铸造技术
在消失模铸造过程中施加一定频率和振幅的振动,使铸件在振动场的作用下凝固。由于消失模铸造凝固过程中对金属液施加了振动,振动力使液相与固相间产生相对运动,从而使枝晶破碎,增加液相内结晶核心,使铸件最终凝固组织细化、补缩提高,力学性能改善。该技术可利用消失模铸造中现成的紧实振动台,通过振动电动机产生的机械振动,使金属液在动力激励下生核,达到细化组织的目的,是一种操作简便、成本低廉、无环境污染的特种消失模铸造新方法[33,34]。消失模铸造振动凝固试验台如图17所示。
图17 消失模铸造振动凝固试验台
图18所示为750℃浇注时不同振动频率ZL101铝合金消失模铸造振动凝固与无振动的金相组织比较。在ZL101铝合金消失模凝固过程中进行不同频率的垂直振动,组织明显细化。
图18 750℃浇注时不同频率ZL101消失模铸造振动凝固与无振动金相组织比较
图19 不同振动频率下试样抗拉强度、伸长率和硬度的变化
4.4 消失模壳型铸造技术
以消失模铸造的泡沫模为原型,结合熔模铸造的制壳技术结壳,经失模、焙烧后装箱填砂,进行精密铸造成形。该技术结合了泡沫模的低成本、收缩小、尺寸设计灵活及熔模铸造高精度型壳等优点,由于浇注前脱去了泡沫模,避免了消失模铸造因泡沫模分解带来的气孔、夹杂等缺陷,以及泡沫模气化吸热而引起的过高浇注温度问题,同时使金属液的充型能力进一步提高。该技术不仅解决了普通消失模铸造易出现的气孔、夹杂等缺陷,还能保证铸件具有较高的尺寸精度和表面粗糙度,以及良好的内在质量和成品率[35,36]。
JIANG等[37,38]研发了一种新的真空低压消失模壳型铸造新技术,它将“消失模铸造精密泡沫模样成形”“熔模精密铸造制壳技术”“真空低压铸造成形”等多项精密铸造技术有机结合起来,可实现复杂薄壁铝/镁合金精密铸件的高质量成形,其工艺流程如图20所示。
图20 真空低压消失模壳型铸造工艺流程
真空低压消失模壳型铸造采用高密度、高精度及表面光整的泡沫模样做母模,在其表面结壳2~3次形成复合涂层,经失模、烘烤等工序形成陶瓷型壳,再结合真空消失模铸造或真空低压消失模铸造成形,即可获得复杂薄壁铝合金、镁合金精密铸件。消失模壳型铸件浇注过程如图21所示。
图21 消失模壳型铸件浇注过程
5、 结束语
1)高真空压铸可显著提高铝/镁合金压铸件的致密性,实现铝/镁合金压铸件热处理强化,进一步提高铝/镁合金压铸件的性能。充氧压铸技术适用于制备高致密、高强铝合金压铸件。半固态压铸和铸锻双控成形技术也是制备高致密、高强度铝/镁合金压铸件的新方法,未来有较大应用潜力。开发出适合铝/镁合金压力铸造的合金材料体系及其热处理工艺和压力铸造新技术是铝/镁合金压力铸造今后研究的主要内容和发展方向。
2)铝/镁合金挤压铸造技术可显著提高金属熔体充型、补缩能力,实现高压凝固和少量塑性变形,提高铸件的致密性和力学性能。开发适于挤压铸造工艺的铝合金、镁合金材料体系,探索铝合金、镁合金压力下凝固行为和组织演变规律,掌握挤压铸造合金成分-工艺-组织-性能关系是铝合金、镁合金挤压铸造未来发展趋势和研究重点。
3)真空低压消失模壳型铸造新工艺在浇注前脱去了泡沫模样,避免了泡沫模在浇注过程中分解带来的孔洞、增碳和夹杂等缺陷;另外,金属液在真空、压力和振动的作用下充型和凝固,金属液的充型和补缩能力大幅度增强,是一种适合生产复杂薄壁高质量铝/镁合金精密铸件的新方法。开发出适合铝/镁合金消失模铸造的合金、涂料、热处理和成形新工艺等技术,是铝/镁合金消失模铸造今后研究的主要内容和发展方向。
参考文献:
[1] LUO A A,SACHDEV A K,APELIAN D.Alloy development and process innovations for light metals casting[J].Journal of Materials Processing Technology,2022,306:117606.
[2] SONG J F,CHEN J,XIONG X M,et al.Research advances of magnesium and magnesium alloys worldwide in 2021[J].Journal of Magnesium and Alloys,2022(10):863-898.
[3] 兰乔,刘保良,常治宇,等.轻合金铸造技术发展历程与展望[J].铸造技术,2021,42(2):141-152.
[4] ZHU Z,SHI R H,KLARNER A D,et al.Predicting and controlling interfacial microstructure of magnesium/aluminum bimetallic structures for improved interfacial bonding[J].Journal of Magnesium and Alloys,2020,8(3):578-586.
[5] 贾海龙,丁家源,查敏,等.镁合金压力下凝固技术研究进展[J].当代化工研究,2022(20):148-151.
[6] 潘帅,付莹,王玉,等.铝合金半固态成形技术研究进展[J].稀有金属材料与工程,2022,51(8):3110-3120.
[7] L I G Y,J I A N G W M,G U A N F,e t a l.Microstructure,mechanical properties and corrosion resistance of A356 aluminum/AZ91D magnesium bimetal prepared by a compound casting combined with a novel Ni-Cu composite interlayer[J].Journal of Materials Processing Technology,2021,288:116874.
[8] 杨少锋,王再友.压铸镁合金的研究进展及发展趋势[J].材料工程,2013(11):81-88.
[9] 樊振中,袁文全,王端志,等.压铸铝合金研究现状与未来发展趋势[J].铸造,2020,69(2):159-166.
[10] 樊自田,蒋文明,魏青松,等.先进金属材料成形技术与理论[M].武汉:华中科技大学出版社,2019.
[11] 王雪杨,李子昕,胡波,等.真空压铸镁合金减震塔的组织和性能[J].特种铸造及有色合金,2022,42(4):467-472.
[12] KANG S W,KANG H,BAE D H.Microstructure and mechanical properties of a die-cast Mg-9Al alloy containing oxygen atoms[J].Materials Letters,2018,219:16.
[13] YANG B,YU X,WANG L Y.New HPDC Mg-RE based alloy with exceptional strength and creep resistance at elevated temperature[J].Materials Science and Engineering A,2022,840:921.
[14] 李东南,吴和保,吴树森.半固态AZ91D镁合金组织与性能研究[J].中国机械工程,2006(13):1421.
[15] 李伟东,王顺成,郑开宏,等.充型速度及锻造压力对铸锻复合成形A356铝合金制品的组织与性能的影响[J].材料研究与应用,2013,7(1):31-36.
[16] 徐静,王顺成,郑开宏,等.启锻时间对铸锻复合成形2014铝合金组织与性能的影响[J].特种铸造及有色合金,2016,36(12):1253-1257.
[17] 熊禹,吉泽升,徐丽娟,等.铸锻复合对ADC12铝合金显微组织和性能的影响[J].特种铸造及有色合金,2017,37(2):214-217.
[18] 王丽萍,叶霞.铸锻复合成形6063铝合金的工艺优化[J].锻压技术,2018,43(8):90-96.
[19] 李广德,王瑛,李伟伦.铸锻复合成形工艺参数对镁合金汽车转向控制臂性能的影响[J].热加工工艺,2021,50(21):91-93.
[20] 贾海龙,周文强,王思清,等.高性能挤压铸造铝合金研究进展[J].特种铸造及有色合金,2020,40(11):1187-1194.
[21] 吉泽升,张永冰,姜博,等.铝合金挤压铸造的研究进展及其在汽车轻量化上的应用[J].铸造工程,2020,44(2):39-45.
[22] 张树国,杨湘杰,郭洪民,等.流变挤压铸造成形技术与装备研究[J].特种铸造及有色合金,2017,37(10):1074-1077.
[23] 贾海龙,张梦娜,杨铭,等.挤压铸造镁合金研究进展[J].中国材料进展,2021,40(10):772-784.
[24] 邢书明,邢若兰.液态模锻(挤压铸造)技术研究与应用进展[J].常州大学学报(自然科学版),2021,33(5):1-7.
[25] 姜巨福,李明星,王迎.铝合金挤压铸造技术研究进展[J].中国有色金属学报,2021,31(9):2313-2329.
[26] 陈露,李建鹏,吴树森,等.成形工艺及热处理对Mg-5Zn-2.5Cu合金热物理性能的影响[J].铸造,2022,71(1):17-21.
[27] SHASTRI H,MONDAL A K,DUTTA K,et al.Microstructural correlation with tensile and creep properties of AZ91 alloy in three casting techniques[J].J ournal of Manufacturing Processes,2020,57:566-573.
[28] 樊自田,董选普,黄乃瑜,等.镁、铝合金反重力真空消失模铸造方法及其设备:ZL 02115638.7[P].2002-12-04.
[29] LI J,ZHAO Z,FAN Z,et al.Study on typical hole defects in AZ91D magnesium alloy prepared by low pressure lost foam casting[J].China Foundry,2013,10(4):232-236.
[30] 蒋文明,樊自田.镁合金消失模铸造新技术研究[J].铸造,2021,70(1):28-37.
[31] 赵忠.振动压力下铝(镁)合金消失模铸造组织性能研究[D].武汉:华中科技大学,2010.
[32] 李旋.振动压力对铝合金消失模铸造组织及性能的影响研究[D].石家庄:河北科技大学,2014.
[33] 冯清梅,谭建波,孙高钢.振动频率对消失模铸造AlSi9Mg组织及性能影响[J].特种铸造及有色合金,2018,38(7):64-69.
[34] 肖伯涛.振动消失模铸造铸铁合金的组织及性能特征[D].武汉:华中科技大学,2013.
[35] 彭乔元.AZ91D镁合金消失模壳型铸造工艺研究[D].长沙:中南大学,2013.
[36] 谭海林,赖春明,周家林,等.消失模-壳型复合铸造AZ91D镁合金的凝固组织与性能[J].铸造,2015,64(9):846-850.
[37] JIANG W M,FAN Z T,LIAO D F,et al.A new shell casting process based on expendable pattern with vacuum and low-pressure casting for aluminum and magnesium alloys[J].International Journal of Advanced Manufacturing Technology,2010,51(1-4):25-34.
[38] JIANG W M,FAN Z T,CHEN X,et al.Effects of mechanical vibration and wall thickness on microstructure and mechanical properties of AZ91D magnesium alloy processed by expendable pattern shell casting[J].Metallurgical and MaterialsTransactions A,2015,46(4):1776-1788.
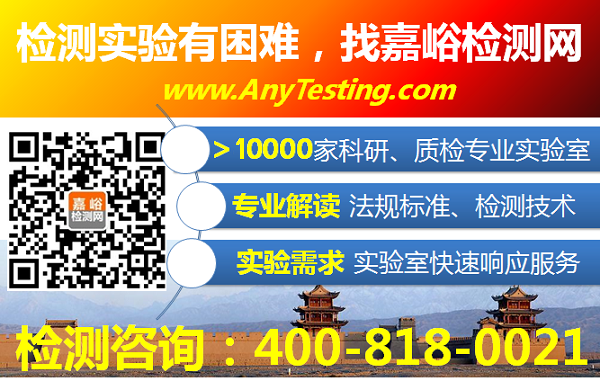