引言
LNG模块化工厂的作业环境一般为高纬度寒冷靠海陆地,常年气温低多积雪,现场维护成本较高,因此对钢结构的表面防腐要求较高,如高温涂层多采用免维护的热喷铝涂层、常规涂层修补的表面处理也多采用喷砂来保障施工质量。
相较LNG等工业建造常采用的喷砂表面清洁技术,激光清洁是利用表面杂质、氧化层吸收激光能量后发生振动、气化、剥离,达到清洁金属表面的目的,具有更加清洁、可控、高效等优势。本文尝试在LNG模块建造过程中用激光清洁代替喷砂处理现场涂层破损区域表面和热喷铝、热浸锌等特殊涂层表面污染物,测试清洁效果及涂层性能。
1.1理论模型
激光清洗是利用附着物吸收激光能量,极短时间内形成光热效应,附着物被电离形成等离子体,等离子体快速膨胀形成冲击波振动实现清洗的效果。当前国内外关于激光清洗的模型研究也提出了如气化剥离、相爆炸、烧蚀、瞬时热处理四种模型。
典型的激光清洗方法有干式、湿式激光清洗和等离子体冲击波。湿式激光清洗因表面存在液膜,导致清洁完后表面残留水分导致二次返锈,等离子体冲击波仅靠冲击波清洁,一般用于清洗表面亚微米或纳米级颗粒。干式激光清洗是目前大面积应用激光清洁的最佳选择。
1.2能量密度与能量分布
附着物剥离的能量阈值为清洗阈值,金属的清洗阈值一般在1.0-10.0J/cm2之间,有机物的清洗阈值一般在0.1-1.0J/cm2之间。能量密度只有达到对应的清洗阈值才能完成相应的清洗。
I=4p/fπd2 式(1)
式中:
I为光斑平均能量密度;d为光斑直径;p为激光的功率;f为脉冲频率。由式(1)可知,光斑平均能量密度与激光功率、脉冲频率有关,激光能量密度受激光器本身限制有最大值。
单模脉冲激光器所激发的光斑能量呈高斯函数分布,可称为高斯光斑,如图1所示。高斯光斑能量分布特点在于光斑中心的能量密度较高,四周的能量密度较低,这种能量分布特点可使设备的光斑平均能量密度低于清洗阈值时,因光斑中心处能量密度超过金属的清洗阈值而达到清洗效果。
图1 单模脉冲激光器光斑能量分布模拟
2、实验部分
2.1 清洗设备
实验采用波长λ=1064nm的单模脉冲光纤激光器,相关参数如下:最大功率200W,光斑直径0.25 mm,脉宽350 ns,最大扫描速度20 000 mm/s,填充间距0.01~1.00 mm,扫描宽度5~200 mm,光斑最大平均能量密度为3.06 J/cm2。
2.2 实验应用项目
表1列出了所开展的具体应用实验。
表1 激光清洁应用实验
2.3 性能与表征
针对激光清洁后的表面,施工涂层需进行涂装常规性能检测,具体指标如表2所示。
表2 涂装常规性能检测
激光清洁后的金属表面微观形貌观察,采用手持式数字显微镜(Inskam-316,Inskam公司)实时观察放大50倍清洁效果。
3、结果与讨论
3.1 清洗效果
图2给出了针对热浸锌、不锈钢、热轧钢、涂层破坏后四种表面的清洁效果。
图2 激光清洁效果:1)热浸锌;2)不锈钢;3)热轧钢;4)涂层破坏
激光清洁可有效清除热浸锌、不锈钢表面附着的铁锈、有机胶带、胶质物、记号笔标记等,清洁后基材表面呈均匀网纹布形貌,观察放大50倍后微观形貌可见点状光斑移动形成的点状线性密排,无遗漏位置,实测处理后基材温度升高小于15 ℃,表面无明显氧化现象。
激光清洁去除热轧钢表面的原始致密氧化层后,基材外观呈均匀网纹布形貌,观察放大50倍后微观形貌可见点状光斑移动形成的点状线性密排,无遗漏位置,实测处理后基材温度升高33℃,颜色呈轻微氧化的淡黄色。
激光清除涂层破坏后锈蚀的同时,实现了周边完好涂层的坡口拉毛,基材表面呈均匀条纹形貌,未焊接、打磨区域清除铁锈、烧糊涂层后表面可见原涂层施工时喷砂形成的不规则形貌,观察放大50倍后微观形貌证实,表面微观形貌为喷砂形成不规则山地形貌与点状光斑移动形成点状线性密排的组合形貌。
3.2 表面状态检测
针对热浸锌、不锈钢、热轧钢及涂层破坏后锈蚀采用激光清洁后检测表面数据指标见表3。
表3 表面状态检测
热浸锌、不锈钢及热轧钢经激光清洁后表面粗糙度均达到40μm左右;涂层破坏后锈蚀的钢板因表面经喷砂处理过,原始粗糙度在75-100μm左右,激光清洁后测得表面粗糙度为87 μm,结合3.1中微观形貌表分析,可视为还原了初次喷砂后的表面粗糙度。
各试样的盐分测试结果均远低于常规涂装要求的25mg/m2,清洁度均达到1级标准。因无激光清洁相关表面处理等级评定标准,参考传统清洁方式的目测检验标准SSPC-VIS-1(喷砂)/SSPC-VIS-3(打磨),目测激光清洁后表面的处理等级达到SSPC SP 10/SSPC SP 11标准要求,理论上可替代喷砂/打磨用于钢材的表面处理。
3.3 涂层附着力及耐腐蚀性研究
对上述四个样品进行涂装后测试涂层附着力,测试结果见表4。
表4 涂层附着力测试结果
涂层附着力测试结果表明,激光清洁后表面可实现涂层的牢固附着。浸锌涂层清洁时因需要避免锌层的破坏,激光清洁次数较少,表面粗糙度较低,涂层附着力低于其他试样。涂层破坏后二次锈蚀钢板经激光清洁后还原了原始喷砂粗糙度,较高的粗糙度也提供了较好的涂层附着性能,涂层附着力明显高于其他试样。将试样放入中性盐雾环境运行480 h,观察表面状态及腐蚀情况,详见表5。
表5 盐雾试验情况
盐雾试验数据分析表明,各试样经长时间盐雾试验后表面涂层防护性能仍较好,激光清洁满足LNG模块建造过程中防腐涂层对表面处理的要求。
3.4 现场应用效果
针对LNG模块建造现场常规需要喷砂/打磨的位置,进行激光清洁替代的实际应用测试,应用效果见表6。
表6 现场应用效果
针对现场小管线焊道表面,常规焊道表面处理常采用喷砂,围挡防护、设备准备等前期准备工作较多,效率低且存在周边污染、破坏情况,激光清洁可有效避免此类问题,现场激光清洁测试结果表明激光清洁可有效清除表面锈蚀,同时实现一定的表面粗糙度,满足替代喷砂的可行性。
4、结 语
综上所述,本文通过采用较高功率的单模脉冲光纤激光器,对金属表面实现了很好的清洁效果,清洁度达到1级,表面盐分残留普遍控制在10mg/m2,可在金属表面实现40μm左右的可控粗糙度。激光清洁涂层破损后二次锈蚀区域可还原初次喷砂形成的表面形貌,粗糙度达到87μm,整体表面处理等级达到SSPC SP10/SSPC SP11,附着力测试和盐雾试验证明激光清洁后表面具有良好的涂装性能。
LNG建造现场存在大量涂层修补点,这些修补点位置狭小很难采用喷砂或打磨进行高质量表面处理,激光清洁在LNG建造现场的涂层修补、清洁方面具有操作简单、无死角、深度可控等优势,可有效代替喷砂/打磨,提高小面积涂层修补的施工质量。
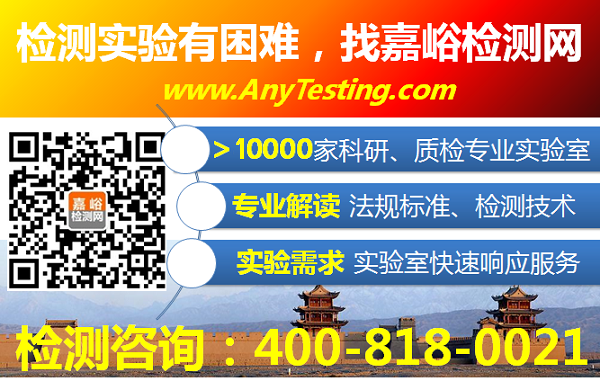