采用激光熔覆技术在42CrMo钢表面制备出厚度超过3mm的含硼高强韧铁基合金涂层(S1涂层),研究了该涂层的显微组织及其轴承滚道服役性能,并与商用高硬度M2涂层进行了对比。结果表明:S1涂层与基体之间结合良好,组织由马氏体基体相和岛状共晶强化相M3C型碳化物组成;S1涂层的平均硬度约为883HV,是 M2涂层的1.1倍。在许用接触应力试验中,S1涂层表面的压痕深度均小于滚动元件直径的10-4,表现出稳定且优异的抗塑性变形能力;S1涂层轴承心部的理论最大剪切应力为377.38MPa,低于M2涂层轴承心部(392.03MPa),远低于轴承材料的剪切屈服应力(459MPa),表现出较好的静载荷承载能力。S1涂层的滚动接触疲劳寿命为2.66×107周次,是M2涂层的2倍。
1、试样制备与试验方法
1.1 试样制备
试验原料为采用真空气雾化法自制的 Fe-C-B-X合金粉末以及M2粉末,其中 M2粉末的化学成分与M2高速钢相似。2种粉末的粒径均为53~150μm,形貌近似球形,如图1所示。试验用基板为风电轴承中常用的调质态42CrMo低合金高强钢,尺寸为150mm×70mm×15mm,使用前进行精磨,酒精清洗并吹干。激光熔覆前,将粉末放入100℃烘箱中保温2h。将采用激光熔覆制备的Fe-C-B-X合金涂层记作S1涂层,对比涂层为采用相同工艺制备的商用M2涂层。
采用大功率半导体激光熔覆系统进行多层多道激光熔覆试验,设计涂层厚度大于3mm。该系统的主要设备包括半导体激光器、六轴联动机械臂、气动送粉器及自主研发的同轴送粉喷嘴。经工艺优化后S1涂层与 M2涂层的激光熔覆工艺参数为激光功率 2kW、扫 描 速 度 3mm·s-1、送粉速率10g·min-1、离焦量0、激光光斑直径7.2mm、搭接率40%,原料粉末通过载流气氩气吹入熔池,且采用氩气对熔池进行保护,气体流量为9L·min-1。
1.2 试验方法
采用场发射扫描电子显微镜(SEM)及 透射电子显微镜(TEM)对涂层截面的微观形貌进行观察,TEM测试试样制备步骤如下:沿涂层水平方向切取尺寸为10mm×10mm×0.7mm的薄片,通过机械磨抛使其厚度减薄至70μm以下,然后采用冲片机获得直径为3mm的薄片,并对其进行电解双喷及离子减薄从而制备出厚度小于100nm的薄区。在SEM图像中测量涂层的高度H,基体熔深h,计算涂层的稀释率η,计算公式为
采用维氏硬度计对涂层截面的显微硬度进行测试,测试间距为0.2mm,试验载荷为4.9N,保载时间为15s。按照GB/T 7314—2017,采用万能材料试验机对涂层的压缩性能进行表征,试样取自涂层,取样方向沿激光熔覆方向,试样尺寸为ϕ2mm×4mm,压缩方向与熔覆方向平行,加载速度为0.5mm·min-1。采用滚动接触疲劳试验机对涂层试样进行室温滚动接触疲劳试验,试样为外径40mm、内径16mm、宽5mm的圆环,试验转速为200r·min-1,外加载荷为3000N,冷却方式为油冷,对磨材料为淬火态GCr15钢。采用液压式万能材料试验机对涂层试样进行许用接触应力测试,试样尺寸为75mm×45mm×30mm,其中涂层厚度超过3mm,试验过程中采用尺寸为ϕ35mm×35mm滚柱对试样进行加载,根据GB/T 4662—2012,滚子轴承的最大许用接触应力Smax为4000MPa,则可计算得到滚柱最大负载,即许用接触应力测试最大加载载荷为260kN;滚柱最大负载Q的计算公式为
每个试样进行5次静载荷许用接触应力测试,采用白光干涉仪对涂层表面压痕深度进行测量,并采用扫描电镜对试样的横截面进行观察。若涂层的压痕深度小于0.0001D(3.5μm),则涂层满足轴承静载荷承载要求。
2、试验结果与讨论
2.1 宏观形貌与显微组织
由图2可知,S1涂层和M2涂层均与基体结合良好,且涂层的厚度都超过了3mm,分别为3.54,3.44mm。S1涂层与基体结合界面平滑,稀释率小于5%,而M2涂层与基体结合界面呈波浪状,稀释率大于20%。
由图3可见,S1涂层和M2涂层的显微组织都由马氏体基体和晶间强化相组成,其中S1涂层中的晶间强化相与基体组织形成了岛状共晶组织。由TEM明场像及相应的选区电子衍射花样可知,S1涂层中的晶间强化相主要为M3C型碳化物。M2涂层中晶间强化相的形貌与S1涂层相似,也与基体之间形成共晶结构,共晶形貌为花瓣状,强化相类型为M2C型碳化物。与S1涂层相比,M2涂层中的共晶强化相尺寸明显减小。产生该现象的原因主要是在S1涂层中添加了少量的硼元素。硼元素在铁液中的固/液两相分配系数远小于1,在凝固过程中硼元素在晶界处发生偏析,提高了碳元素在铁液中的活度,使得碳化物更易在晶界处析出,因此S1涂层中共晶强化相尺寸较大,含量较高。
2.2 静载荷承载能力
2.2.1 涂层表面塑性变形
由图4可知,S1涂层和M2涂层的平均压痕深度分别为3.12,3.29μm,满足轴承的静载荷承载能力。然而,在第3次和第4次测试过程中,M2涂层的压痕深度均超过3.5μm,分别为3.57,3.51μm。S1涂层的压痕深度都低于3.5μm,说明与M2涂层相比,S1涂层表现出更加稳定且优异的抗塑性变形能力。一般只有当静载荷超过轴承表面的屈服强度时,其表面才会发生塑性变形,从而留下永久压痕。LAI等通过有限元模拟等方法建立了轴承表面塑性压痕深度的预测模型,如下:
由式(4)可知,在最大许用接触应力相同的条件下,涂层的塑性压痕深度取决于涂层的屈服强度,屈服强度越高则涂层的塑性压痕深度越浅。S1涂层的压缩屈服强度较高,超过了3500MPa,大于M2涂层的压缩屈服强度(3000MPa左右),因此S1涂层的平均塑性压痕深度低于M2涂层。
由图5可见,许用接触应力试验后,S1涂层中不存在裂纹,而M2涂层中存在横向裂纹和边缘裂纹,且裂纹主要沿晶界扩展并止于马氏体之中。这是由于施加的静载荷超过M2涂层的屈服强度,使涂层产生塑性流动,而塑性流动一般以拉应力的形式对靠近基体处涂层的亚表面及涂层的边缘造成损伤,从而产生裂纹。M2涂层的屈服强度与塑性均低于S1涂层,因此仅在M2涂层中发现裂纹。在接触应力的作用下,M2涂层的表面出现由塑性变形引起的层状撕裂,其中塑性变形区域的深度超过3μm。然而S1涂层表面未观察到明显的塑性变形,这主要是由于S1涂层中含有大量尺寸较大的共晶碳化物,当承受较大的接触应力时,大块的共晶碳化物可以有效支撑涂层基体组织,从而防止其发生塑性变形。与S1涂层相比,M2涂层中共晶碳化物的含量较低,且尺寸细小,不能有效抵御涂层基体的塑性变形,因此涂层表面发生层状撕裂。
2.2.2 轴承心部损伤
轴承的静载荷承载能力除了需要考虑轴承表面的塑性变形外,还需要考虑轴承的心部损伤。前者是为了保证轴承的平稳运行,而后者则是确保轴承滚道的完整性,避免形成心部挤压故障。静载荷会使壳心界面处产生较高的剪切应力,当界面处硬化层的最大剪切应力超过心部材料的剪切屈服应力时,心部材料会产生塑性流动,从而引起心部材料的损伤。一般轴承的静载荷承载能力取决于硬化层的深度,硬化层深度不足会导致轴承心部损伤。当轴承表面硬化层的硬度低于58HRC(660HV)时,随着轴承表面硬度的降低,轴承的静载荷承载能力下降。因此,一般轴承的硬化层表面硬度应超过660HV。随着硬化层深度的增加,其硬度逐渐降低至510HV,然后迅速降至心部材料的硬度,一般将硬度超过510HV区域的深度称为轴承的有效硬化深度;心部损伤可能发生的部位通常位于有效硬化深度的110%处,即心部材料硬度的起始位置。由图6可知,S1涂层的平均硬度约为883HV,是M2涂层(785HV)的1.1倍。由于S1涂层与M2涂层的硬度均超过660HV,满足表面硬化层硬度要求。S1涂层与M2涂层的有效硬化深度分别为5.16,4.92mm。
为了预测轴承心部的承载能力,对最大许用静载荷条件下轴承心部承受的最大剪切应力τ进行计算,其计算公式为
式中:ζ为与无量纲深度z/b有关的函数;z为有效硬化深度的110%;b为接触面的半宽,接触面近似为矩形。
式(5)中∑ρ取0.05726,le取35mm,Q为260kN,对于S1涂层和M2涂层,z分别为5.68,5.41mm,计算得到z/b分别为4.73,4.51,则ζ分别为0.103,0.107。将上述参数代入式(5),计算得到S1涂层和M2涂层轴承心部的理论最大剪切应力分别为377.38,392.03MPa。根 据JB/T 10705—2007,轴承套圈一般采用符合GB/T3077—1999规定的42CrMo钢制造,其抗拉强度约为1080MPa。研究表明,材料的剪切屈服应力约等于抗拉强度的0.425倍,因此42CrMo钢的剪切屈服应力为459MPa,远高于最大许用静载荷在激光熔覆S1和M2涂层轴承心部产生的理论最大剪切应力。因此,激光熔覆表面强化的轴承不会因静载荷作用而发生心部损伤,且激光熔覆S1涂层轴承心部的理论最大剪切应力较小,因此表现出较好的静载荷承载能力。
2.3 滚动接触疲劳性能
S1涂层的平均滚动接触疲劳寿命为 2.66×107周次,是M2涂层(1.30×107周次)的2倍。由图7可知,S1涂层和M2涂层的疲劳失效形式均主要为整体分层,大面积的涂层从基体表面剥落,其中剥落区域呈近椭圆形状,其长轴平行于滚动方向,而短轴垂直于滚动方向。该现象的产生主要是由于在循环载荷的作用下涂层与基体界面处产生较大的剪切应力,造成裂纹在界面处萌生与扩展,最后导致涂层与基体分离。S1涂层表面非整体分层区域还存在轻微的磨损,表面发现少量浅磨痕,未观察到麻点、剥落坑等疲劳失效特征。与S1涂层相比,M2涂层表面存在明显的塑性变形痕迹以及剥落坑,表明M2涂层除了发生整体分层失效外,还发生点蚀及剥落失效。
由图8可见:M2涂层整体分层区域底部的基体表面相对平坦,存在少量表面裂纹及较浅的起皮,表明在剪切应力作用下大块的涂层从基体表面直接剥落,涂层与基体之间的结合强度相对较低;S1涂层整体分层区域底部的基体表面存在大量的黏附剥离块,形成层状形貌,表明涂层与基体之间的结合强度较高。S1涂层非整体分层区域相对光滑,表面只有少量轻微的磨削纹理。与S1涂层相比,M2涂层表面磨削纹理数量增多,深度增大,同时表面存在明显的塑性变形痕迹。产生该现象的原因主要与涂层表面的硬度有关。S1涂层表面的硬度接近900HV,M2涂层的表面硬度约为800HV,而滚动接触疲劳的对磨试样的表面硬度约为830HV,因此试验后M2涂层表面存在较深的磨削纹理,而S1涂层表面的磨削纹理较浅。
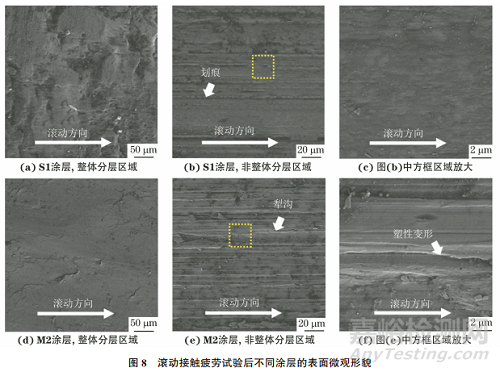
涂层表面的高硬度可以有效地抵抗疲劳循环造成的表面损伤,并在疲劳载荷的重载下改善涂层的滚动接触疲劳性能。由图9可知,S1涂层剥落坑中仅发现基体组织,表明涂层与基体之间发生整体分层,而未从基体表面剥落的涂层中没有出现表面塌陷及疲劳裂纹。M2涂层剥落坑的微观形貌与S1涂层相似,在剥落坑中仅存在基体组织,说明涂层与基体间发生整体分层;在未完全剥落的M2涂层中出现涂层压碎、表面坍塌及疲劳裂纹等现象。M2涂层中增强相含量较少、尺寸较小,不能作为强化骨架有效支撑马氏体基体,因此涂层在疲劳重载下发生塌陷。此外,由于滚动接触疲劳的接触应力较大,而M2涂层的硬度较低,因此滚动接触疲劳试验后涂层截面中存在明显的塑性变形、表面裂纹和起皮以及剥落损伤。与M2涂层相比,S1涂层中大量的大尺寸共晶增强相能够有效支撑马氏体基体,防止其在疲劳载荷下发生坍塌,因此S1涂层表现出优异的滚动接触疲劳性能,未观察到明显的塑性变形、裂纹及剥落等现象。
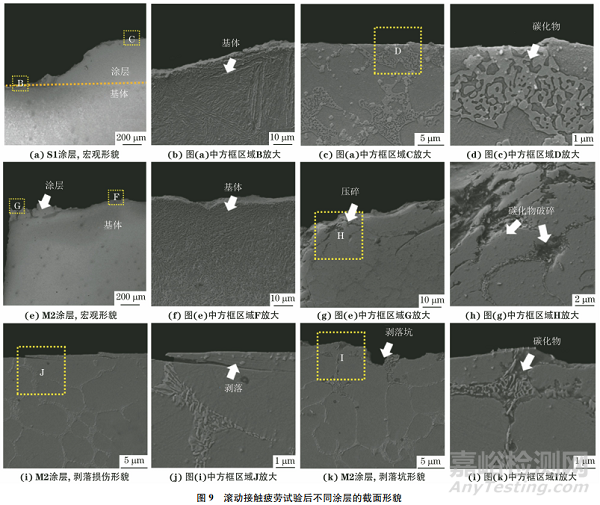
3、结 论
(1)激光熔覆自主研发的Fe-C-B-X 合金粉末制备的高强韧铁基合金涂层(S1涂层)的厚度为3.54mm,涂层与基体间结合良好,结合界面平滑,稀释率小于5%,而激光熔覆商用M2粉末制备的M2涂层与基体结合界面呈波浪状,稀释率大于20%;S1涂层的显微组织由马氏体基体相和岛状共晶强化相组成,其中共晶强化相主要为M3C型碳化物,而M2涂层则由马氏体基体相和花瓣状共晶强化相组成,强化相类型为M2C型碳化物,且S1涂层的共晶强化相尺寸较大,数量较多。
(2)S1涂层的平均硬度约为883HV,是M2涂层的1.1倍。在最大接触应力为4000MPa的许用接触应力试验中,S1涂层表面的压痕深度均小于滚动元件直径的10-4,表现出稳定且优异的抗塑性变形能力;激光熔覆S1涂层轴承心部的理论最大剪切应力为377.38MPa,低于激光熔覆M2涂层轴承心部(392.03MPa),远低于轴承材料40CrMo钢的剪切屈服应力(459MPa),S1涂层表现出更好的静载荷承载能力。
(3)S1涂层具有优异的滚动接触疲劳性能,其疲劳寿命(2.66×107周次)是M2涂层的2倍,失效形式主要为整体分层失效。S1涂层的高硬度以及其中存在的大量大尺寸共晶强化相可以有效地防止其在疲劳载荷下发生坍塌,从而提升滚动接触疲劳性能。
引用本文:
冯育磊,冯悦峤,冯凯,等.激光熔覆高强韧铁基合金涂层的组织及其轴承滚道服役性能[J].机械工程材料,2023,47(5):118-126.
Feng Y L, Feng Y Q, Feng K, et al. Microstructure of High Strength and Toughness Fe-based Alloy Coating by Laser Cladding and Its Bearing Raceway Service Performance, 2023, 47(5): 118-126.
DOI:10.11973/jxgccl202305017