采用高温微动磨损试验机对Zr-4合金管进行切向微动磨损试验,通过改变法向载荷研究了试验温度(25,100,200,325℃)对不同运行工况(完全滑移区和部分滑移区)下微动磨损行为的影响。结果表明:在相同试验温度下完全滑移区的摩擦因数高于部分滑移区,不同运行工况下200,325℃时的摩擦因数更早达到稳定状态。在完全滑移区,合金的磨损机制包括磨粒磨损、氧化磨损和剥层,温度的升高对合金微动磨损程度的影响较大,325℃时的微动磨损程度最大;而在部分滑移区,磨损机制包括剥层、黏着磨损和氧化磨损,试验温度的升高对微动磨损程度的影响很小。在相同试验温度下,部分滑移区的微动磨损量远低于完全滑移区;试验温度的升高对完全滑移区微动磨损量的影响较明显,而对部分滑移区的影响不大。
1、试样制备与试验方法
试验材料选用Zr-4合金管,其外径为9.45mm,内径为8.03mm,长度为1m,弹性模量为9.54×104MPa,剪切模量为3.50×104MPa,抗拉强度为530MPa,屈服强度为350MPa,断后伸长率为28%。通过机械加工的方式将原料管切割成长度为15mm的管试样,经超声清洗后待用。
采用课题组自主研发的全模式高温微动磨损试验机进行切向微动磨损试验,具体设备如图1所示,上下试样均为Zr-4合金管,接触模式为点接触。在微动磨损试验过程中,通过音圈电机实施位移加载,伺服电作动缸施加法向载荷,并通过水平光栅位移传感器实时采集微动相对位移量,摩擦力随微动位移、循环次数的响应值由压电式载荷传感器进行实时采集,同时利用外接加热模块的温控器设定试验温度,并对试样进行提前加热完成高温试验。试验过程中的位移幅值为60μm,法向载荷分别为10,40N,试验频率为5Hz,试验温度为25,100,200,325℃,循环次数为20000周次。
试验结束后,通过摩擦力和法向载荷的比值来计算摩擦因数;采用扫描电子显微镜(SEM)对下试样磨痕区域的形貌进行观察;采用电子探针(EMPA)进行微区元素成分分析;采用白光干涉仪对下试样磨痕区域进行二维轮廓和三维形貌分析,并测量磨损面积及磨损量。
2、试验结果与讨论
2.1 摩擦特征曲线
由图2(a)可知,当位移幅值为60μm时,在不同试验温度和10N法向载荷下,试验合金的摩擦力-位移曲线的形状为平行四边形或椭圆形,说明在此参数下微动运行于完全滑移区。当试验温度从25℃升高至100℃时,最大摩擦力发生明显变化,曲线形状由平行四边形变为椭圆形,且曲线斜率先减小后增大,说明此时合金表面的接触刚度先减小后增大;随着试验温度的进一步升高,曲线形状又恢复为平行四边形。由图2(b)可知,当法向载荷为40N时,不同试验温度下的摩擦力-位移曲线均为直线形,此时微动处于部分滑移区,当试验温度升高至325℃时,曲线的面积增大,表明此时相对滑移量增加;随着试验温度的升高,曲线斜率先减小后增大,说明接触刚度先减小后增大。
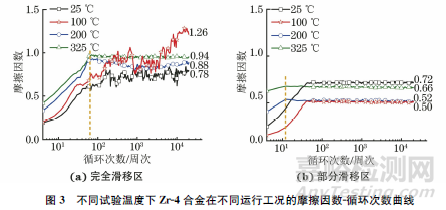
由图3可知:在完全滑移区,试验合金在25℃时的稳定摩擦因数最低(约为0.78);当试验温度升高至100℃时,从初始到300周次循环时摩擦因数迅速增大,在循环次数接近660周次时摩擦因数骤降,直到循环3500周次后摩擦因数又呈上升趋势,最大摩擦因数约为1.26;当试验温度为200,325℃时,摩擦因数很快达到稳定状态,稳定摩擦因数分别为0.88,0.94,但与325℃一直维持稳定的趋势不同,200℃时摩擦因数在200周次循环处略微降低,5000周次循环后又上升至稳定状态。可知,在完全滑移区,试验合金在25℃时的摩擦因数最低,这是因为温度升高会使合金表面附着物分解破裂,在一定程度上加速磨损,从而增大摩擦因数。在部分滑移区,试验温度为25,100℃的摩擦因数达到稳定状态所需要的时间较200,325℃下长;25℃时的稳定摩擦因数最高,为0.72,当试验温度升高至100℃时,稳定摩擦因数约为0.50,下降幅度达到31%,当试验温度继续升高至200,325℃时,法向载荷引起的塑性变形和瞬时高温使得接触材料熔化而发生焊合,造成摩擦因数又会有一定的升高,但摩擦因数较早达到稳定状态。对比发现,在相同试验温度下,部分滑移区的稳定摩擦因数均小于完全滑移区,且摩擦因数的变化较平稳。
2.2 磨痕损伤特征
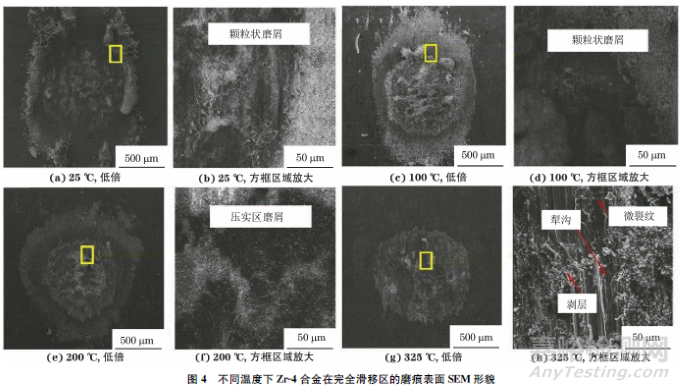
由图4可以看出:在完全滑移区,25℃下试验合金磨痕表面磨屑堆积严重,磨痕四周有大量细小颗粒状磨屑分布;当试验温度升高至100℃时,磨屑的堆积更为严重,磨屑被压实形成磨屑层,磨屑颗粒变细;200℃下磨痕边缘位置细小颗粒状磨屑减少,边缘与中心位置过渡处有微动滑移痕迹,并出现在基体表面,说明温度的升高导致磨屑的聚集程度增加,分散的磨屑减少,磨痕中心出现少量剥落坑和犁沟;当试验温度升高至325℃时,材料膨胀使得试样间接触紧密,磨屑无法及时排出接触区,边缘位置处观察不到磨屑,此时上下试样接触表面相对滑动,受高温影响磨痕区域出现材料的塑性流动特征,磨痕中心剥层严重,出现少量微裂纹以及较多的犁沟。
由图5可以看出,在部分滑移区,磨痕呈现出明显的中心黏着区和边缘滑移区,符合典型的部分滑移区微动损伤形貌特征。25℃时磨痕损伤轻微,黏着区和滑移区的界线不明显,磨屑堆积形成片状磨屑;当试验温度升高至100℃时,可以明显观察到黏着区和滑移区的界线,磨痕中心位置的黏着磨损加剧,有少量剥落坑形成;200℃时,边缘滑移区占比增大,黏着区有磨屑堆积现象,表面发生塑性变形和材料塑性流动;325℃时磨痕面积增大,损伤加剧,表面几乎观察不到颗粒状磨屑的存在。可知,完全滑移区的磨损机制为剥层、磨粒磨损和氧化磨损,温度的升高对合金微动磨损程度的影响较大,325℃下试验合金的微动损伤程度最大;部分滑移区则主要以剥层、黏着磨损和氧化磨损为主,随着试验温度的升高,试验合金的微动损伤整体变化不大。
2.3 磨痕表面微区成分
由图6可以看出:在完全滑移区,25℃下试验合金磨痕表面氧元素含量较高,锆元素含量低,未磨损区域则相反,氧元素在整个磨痕上呈现出沿位移方向分布的规律;100,200,325℃下磨痕区域氧元素含量明显较未磨损区域高,但锆元素含量的降低并不明显。
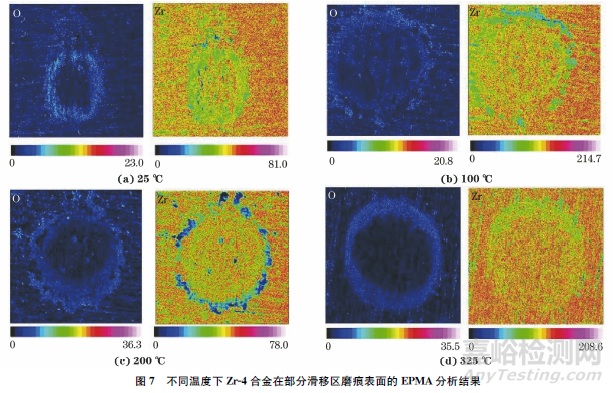
由图7可以看出:在部分滑移区,不同温度下试验合金磨痕表面氧元素的分布均呈现出明显的环状特征,即磨痕边缘形成了一个富氧、贫锆的环状区域;而磨痕中心为富锆、贫氧,且25,325℃时该现象最明显。这与部分滑移区中间黏着边缘滑移的特征相符。边缘由于摩擦磨损产生的活化作用,促进了氧化反应的进行,而中心由于未发生相对滑移,使得氧化现象并不显著。
2.4 磨痕轮廓及磨损量
由图8可知:在完全滑移区,25℃时试验合金磨痕在x方向的最大深度为13μm,磨痕宽度为750μm;100,200℃时磨痕表面有明显的凸起,且100℃时的凸起高度更大,这可能是由大量磨屑堆积造成的,磨痕宽度分别为460μm和655μm;当试验温度升高至325℃时,磨痕轮廓与25℃时相同,为明显的“U”形,但此时的磨痕在x方向的最大深度为40μm,为25℃时的3倍左右,同时磨痕的宽度最大,达到1000μm。在完全滑移区,温度的升高使试验合金表面软化严重,加重微动磨损的同时容易发生材料转移。
由图9可以看出:在部分滑移区,25 ℃时磨痕在x 方向的最大深度为9.5μm,凸起高度为7μm,磨痕宽度为515μm,此时上下试样接触区域的中间发生黏着;100℃时磨痕的最大深度仅为2.5μm,为25℃时的1/4左右,磨痕宽度为286μm;试验温度继续升高至325℃,磨痕的最大深度变化不大,宽度增至446μm。在部分滑移区,试验温度的升高使试验合金中间的黏着加剧,边缘的滑移减轻,但整体变化较小。
由图10可以看出:在完全滑移区,随着试验温度的升高,试验合金的磨损面积先减小后增大,325℃时的磨损面积最大,为1099098.624μm2,100℃时的磨损面积最小,仅为649255.04μm2,是325℃时的1/2;在部分滑移区,随着温度的升高,磨损面积相差较小,325℃的磨损面积最大,为237506.256μm2,100℃时的磨损面积最小,为179315.136μm2。在完全滑移区,325℃时的磨损体积最大,为3417417.728μm3,100℃时的次之,为3050682.624μm3,25℃和200℃时的磨损体积较小,约为100℃的1/2;在部分滑移区,25℃时的磨损体积最大,100℃时的磨损体积最小,为34607.856μm3,仅为25℃时的1/3。可以看出,在相同温度下,部分滑移区的微动磨损程度远低于完全滑移区。试验温度的升高对完全滑移区微动磨损程度的影响较明显,而对部分滑移区的影响不大。
3、结论
(1) 在完全滑移区,Zr-4合金在25℃时的摩擦因数最小,100℃时摩擦因数最大,200,325℃时的摩擦因数最早达到稳定状态;在部分滑移区,25℃的摩擦因数最大,随试验温度升高,摩擦因数先下降后增大,200,325℃时的摩擦因数最早达到稳定状态。在相同试验温度下,部分滑移区的摩擦因数均小于完全滑移区,且摩擦因数的变化较平稳。
(2) 在完全滑移区,Zr-4合金的磨损机制包括磨粒磨损、氧化磨损和剥层,温度的升高对合金微动磨损程度的影响较大,325℃时试验合金的微动损伤程度最大;在部分滑移区,磨损机制包括剥层、黏着磨损和氧化磨损,随着试验温度的升高,试验合金的微动损伤程度整体变化不大。
(3) 在相同试验温度下,部分滑移区的微动磨损量远低于完全滑移区。试验温度的升高对完全滑移区微动磨损量的影响较明显,而对部分滑移区的影响不大。
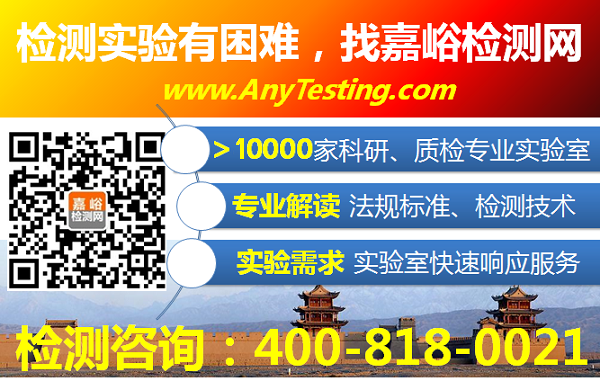