期刊《Journal of the European Ceramic Society》近期上线了由南华大学学者合作发表的关于增材制造的最新研究文章“Research progress on crack formation mechanism and inhibition strategy for ceramic additive manufacturing(陶瓷增材制造裂纹形成机理及抑制策略研究进展)”。
裂纹形成是陶瓷增材制造(CAM)过程中的常见问题。该文综合比较了间接陶瓷增材制造(DCAM)和直接陶瓷增材制造(IDCAM)技术的成形特点。总结了CAM中微观和宏观裂纹的形态和空间分布特征。分析了IDCAM在成形、烧结和冷却等不同工艺阶段的裂纹形成机制,主要从应力分布和能量释放的角度讨论了DCAM中的裂纹形成机制。全面总结了抑制裂纹的方法,包括工艺参数、辅助能量场和材料成分。提出了CAM中裂纹研究的挑战和可能的未来趋势。
陶瓷材料由于具有耐高温、耐腐蚀和良好的化学稳定性等特点,被广泛应用于机械、化工、电子、航空航天、生物医学等工业领域。传统的陶瓷加工技术,包括注射成型、干压成型、凝胶注射成型等,对模具的依赖性很强,无法满足集成化、复杂化、精密化陶瓷产品快速制造的要求。增材制造技术基于离散堆叠原理,根据预先设计的三维实体模型,将一系列离散材料按预定轨迹逐层堆叠,从而制造出物理零件。与传统的陶瓷加工技术相比,陶瓷增材制造(CAM)技术打破了传统陶瓷加工过度依赖模具的局限,无需模具即可快速生产出完全个性化的陶瓷零件,结构设计自由度高,并被认为是构成工业4.0的众多颠覆性技术之一。CAM技术具有材料利用率高、生产周期短、成型精度高、表面质量好等优点,可实现形状复杂的单件、小批量陶瓷零件的定制化生产。然而,由于陶瓷的固有特性和CAM工艺的特点,成形件存在气孔、裂纹等典型成形缺陷。
图1.光固化技术原理图 (a)SLA工艺示意图;(b)DLP过程示意图
图2. 选择性激光烧结工作原理图
图3. 送粉直接成型技术工作原理图 (a)喷嘴工作位置示意图;(b)沉积系统和成型示意图
CAM工业应用滞后的主要原因是成形缺陷过多和成形质量差。其中,裂纹缺陷严重影响陶瓷件的力学性能,是该技术向工业实用化推进的最大障碍。目前,现有的CAM裂纹缺陷研究主要集中在实验方法的裂纹形貌和抑制上。根据是否需要进行后处理,CAM技术可分为间接陶瓷增材制造(IDCAM)和直接陶瓷增材制造(DCAM)。对于IDCAM,裂纹缺陷主要是在后续的高温脱脂和烧结过程中产生的。在高温脱脂过程中,生坯发生剧烈的体积收缩,进而在烧结件表面或内部产生裂纹缺陷。对于DCAM,陶瓷材料在可见光或近红外光范围内的低热震性、弱致密化和低光吸收使得该技术制备氧化物陶瓷仍然极具挑战性。在陶瓷粉末与高能量密度激光束的强相互作用下,陶瓷粉末在极短时间内经历高温熔化和冷却凝固过程,由此产生的高温梯度和冷却速率导致复杂的相变和微观结构变化。此外,这个过程不可避免地会产生热应力、收缩应力和内应力。在这些应力的耦合作用下形成不均匀的应力场,容易在样品表面或内部产生不同的微观和宏观裂纹缺陷。
图4. IDCAM陶瓷中的裂纹
图5. DCAM陶瓷裂纹 (a~c)微裂纹;(d~e)宏观裂纹
图6. 陶瓷零件的气体释放过程及裂纹分布
该文从形态特征、形成机理和抑制方法三个方面对IDCAM和DCAM工艺产生的裂纹缺陷进行了系统的总结和分析。针对IDCAM,分析了成形、脱脂和烧结阶段裂纹缺陷的形态特征和形成机制。对于DCAM,主要从微观和宏观角度描述裂纹形貌特征。着重综述了应力场作用下的裂纹形成机制。讨论了晶界界面能、原子键结合能、孔隙表面自由能与裂纹缺陷之间的科学关系。抑制裂纹的方法从工艺参数、辅助能量场和材料成分三种不同的策略进行综合总结。最后,提出了CAM中裂纹研究的挑战和可能的未来趋势。
图7. (a)相变收缩微裂纹; (b)硅基陶瓷微裂纹形貌
图8. (a)晶间裂纹; (b)孔隙破裂导致裂纹形成过程示意图
图9. (a)激光直接成形熔池热成像; (b)熔池凝固收缩示意图
CAM技术已成为制造先进陶瓷的主要途径,但裂纹缺陷已成为限制其应用的主要障碍,也成为CAM技术最重要的研究方向和需要解决的关键问题。本文系统分析了不同CAM工艺中裂纹缺陷的特征和形成机理,并对裂纹抑制方法进行了综合探讨。主要结论可归纳如下:
(1) 详细阐述了IDCAM和DCAM技术的工艺原理,并系统地比较了各自在成形精度和力学性能方面的优缺点。分辨率高达10nm的IDCAM技术可生产出具有高成型精度和出色表面质量的零件。但是,高温脱脂和烧结过程中有机物的热解容易导致密度低,容易导致陶瓷件密度低和严重的裂纹缺陷。DCAM技术可以实现成型和烧结工艺一体化。但其快速加热和快速冷却的特性容易产生热残余应力,导致成形件产生变形、裂纹、分层等成形缺陷和表面质量差。
(2) 总结了不同CAM工艺裂纹的形态和空间分布特征。IDCAM工艺的裂纹缺陷分为形成裂纹和烧结裂纹。成型裂纹在坯件内呈横向、横向分布,而烧结裂纹则在坯件内部或表面杂乱分布。DCAM中的裂纹缺陷主要分为微观裂纹和宏观裂纹,裂纹分布呈现出明显的规律性。微裂纹集中在晶界和孔隙周围。铺粉DCAM的宏观裂纹主要位于相邻扫描轨迹的交叉点和沉积层的顶部区域。送粉DCAM宏观裂纹的特点是中间裂纹多而密,两侧长裂纹,传播深度大。
(3) 详细分析了CAM中裂纹的形成和演化机理。IDCAM中的形成裂纹主要是由浆料固化产生的收缩拉应力引起的。IDCAM中的烧结微裂纹主要来源于烧结颈、晶界和相变颗粒的断裂。在有机物热解产生的局部压应力、高温烧结产生的热应力、冷却凝固产生的收缩应力的耦合作用下,形成的微裂纹从宏观裂纹继续扩展。烧结件。DCAM中的微裂纹主要来源于晶界、内部孔隙和相变颗粒。在温度梯度引起的热应力、冷却凝固引起的收缩力、凝固区位移约束引起的约束应力等内应力的耦合作用下,微裂纹扩展形成宏观裂纹。
(4) 全面总结了工艺参数、辅助能量场和材料成分等裂纹抑制方法。在IDCAM工艺中,激光功率和孵化距离是成形阶段裂纹抑制的关键参数。IDCAM高温热处理过程中,合适的升温速率和保温时间有助于样品整体受热均匀,从而降低热梯度引起的热应力。在DCAM工艺中,合理匹配激光功率和扫描速率,可以显着降低陶瓷粉末吸收的能量,从而降低零件的内应力。引入辅助能量场可以调节熔池的流动,释放熔池中形成的热应力。通过优化材料成分,可以改善材料的热物理参数,从而实现晶粒细化和增韧,从而提高裂纹萌生和扩展的阻力。
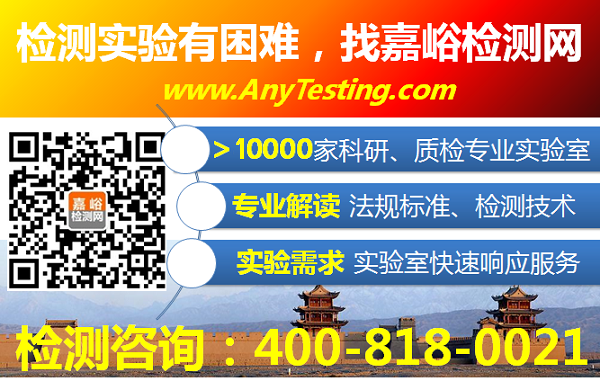