前言
目前全球都对汽车电动化发展普及持乐观态度,同时考量节能减排政策与禁售燃油车的风向,汽车业需要成本更低、分量更轻的材料,从而提升燃料经济性。美国法规将发布平均燃油标准,将该数值限定在54.5英里每加仑,相较于当前的35.5英里每加仑,该数值的增幅高达60%。
碳纤维复合材料有望成为汽车结构件轻量化材料主线。相较于钢材,碳纤维强度更高,分量也更轻,但其售价相对较贵。为便于未来大规模推广应用,需要研发符合机械及安全性能的经济型复合物,例如:聚丙烯及聚酰胺纤维等长碳纤维强化热塑性树脂等材料。
复合材料的特征和优势
强度高
高模量碳纤维复合材料强度可达钢的5倍,铝合金的4倍,钛合金的3.5倍以上。
抗疲劳性能好
常用的碳纤维增强复合材料的疲劳极限是其抗拉伸强度的70%~80%,而大多数金属材料仅能达到30%~50%。
减振性能好
复合材料结构件的自振频率高,同时复合材料中如加入高韧性的数值和橡胶基体还带有振动阻尼特性。
各向异性及性能可设计性
纤维复合材料的性能与纤维的排列方向、铺层次序和层数,以及成型方式都有关。通过设计与工艺的调整,可优化实现预定的功能要求。
耐磨、尺寸稳定性好
塑件得到了纤维的耐磨特性与尺寸稳定性。
综上可知高分子材料由于纤维的加入,一方面其机械性能会得到提升,但同时也会面临着纤维排列与预想不符、浮纤、孔洞、夹杂物、缝合线结合质量等缺陷问题。相较于普通塑胶材料(不含纤维),生产者判别复合材料制品是否合格,会更加复杂,需要全面检测其微观结构。
传统复合材料测试方法
通常分成破坏性试验和非破坏性试验(无损检测)。破坏性试验主要包括拉伸、冲击、压缩、弯曲、硬度等力学性能试验,会对测试件的性能和外形破坏,因此成为破坏性测试。而无损检测中,测试件性能和外观不变,仍具有使用价值。
常用的工业无损检测方法有射线检测、涡流检测、超声检测、太赫兹检测技术等等。以上原理均相似,利用光、电、声、磁等物理方式接触或穿透检测塑件,并回收特定信号进行解析,得到我们需要的数据,如尺寸、密度、均匀性、内部结构或缺陷等。尽管目前无损检测方法很多,但一般还不能做到在已知化学组成、制造过程及环境和载荷条件下准确预测出符合材料的剩余使用寿命。
无损检测促进碳纤维复合材料研发
当前碳纤维复合塑胶零部件的研发工艺,需结合考虑配件组装并进行测试,是一个周期长且繁琐的过程,延缓了车用碳纤维复合物的创新研发进程,同时从研发周期上降低了产品的成本效益。
通过模流分析软件,使用精准测试的含纤材料数据,可以预测成型塑件内纤维方向及纤维长度的分布。分析出来的模流结果再与无损检测结果进行比对,从而验证软件与建模的精度。以利用高精准度的计算机试模结果,在开发前端就能“观察“到塑件的内部结构进行优化,快速推进车用长碳纤维复合物的研发进程,实现成本降幅及性能增幅。
模流预测纤维排向分布
结语
随着塑料种类的增多,塑料生产技术的不断精进,在当下及日后的生产生活中,塑料将会发挥越来越大的作用。为了能高质量使用高分子材料,必须准确地掌握其物理力学性能及在线检测功能机理的技术。无损测量技术正好满足了这一技术要求,不仅仅是针对含纤复合材料,是促使所有塑料的传统测试方法发生根本性的变革,使塑料质量控制达到一个新的水平。
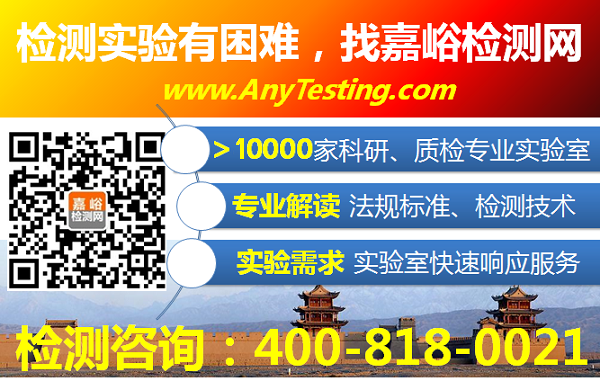