涡流检测是建立在电磁感应原理基础上的一种无损检测方法,通过检测工件内感应电流的变化情况,可以得到材料的电导率、磁导率、形状、尺寸等参数的变化情况,以发现工件中的缺陷。涡流检测的优点有:不与被检件接触、无耦合介质、检测快速等,且涡流检测更易实现在线检测,有利于对产品进行质量追溯及过程控制,在一定程度上可避免人为引起的误差。锻钢冷轧辊涡流检测技术多采用探头式(放置式)线圈进行自比式检测,即比较同一被检工件的不同部分。工件几何参数的变化较小,对线圈阻抗的影响较小,若被检部位存在裂纹,线圈会感应出急剧变化的信号,从而达到检测目的。
研究人员对不同规格的试样进行涡流检测,采用硬度测试、化学成分分析、金相检验、残余应力测试等方法对不同涡流信号位置进行分析,并对锻钢冷轧辊中涡流检测技术的应用进行探讨,研究结果可为科学试验、工业生产提供可靠的数据支撑。
1、试验材料与方法
1.1 试验材料
选取3个不同规格试样,同时进行锻造、球化退火、调质及淬火处理,试样1~3的规格(直径×长度)分别为400mm×1500mm,550mm×1600mm,550mm×1800mm,Cr元素的质量分数分别为3%,5%,6%。
1.2 试验方法
采用不同的淬火工艺对试样1~3进行磨削处理,使试样表面粗糙度≤0.8μm。采用涡流探伤仪对试样进行涡流检测,标定涡流信号点,对信号点进行硬度测试、化学成分分析、金相检验、残余应力测试。
2、试验结果
试样1~3的涡流检测结果如图1所示,其中红色区域为涡流超标信号。试样1~3的计算信号区面积分别为45,86,67cm2。
2.1 硬度测试
标记出涡流信号所在的试样表面位置,采用里氏硬度计对试样1~3信号区及正常区进行硬度测试,结果如表1所示。由表1可知:试样1~3均存在涡流软点信号区,且涡流信号区均存在硬度偏高现象。
2.2 化学成分分析
采用直读光谱仪对试样1~3信号区及正常区进行化学成分分析,结果如表2示。由表2可知:试样1~3不同区域的化学成分均相差不大,说明涡流信号的产生与试样的化学成分无明显关系。
2.3 金相检验
采用光学显微镜对试样1~3信号区及正常区进行显微组织观察,结果如图2所示。试样1~3信号区及正常区的晶粒度评定结果如表3所示。由图2和表3可知:试样1~3各区域显微组织均为正常的回火隐晶马氏体+点、粒状碳化物+少量残余奥氏体,且信号区与正常区的晶粒度无明显差异。
2.4 残余应力测试
采用应力测试仪对试样1~3信号区及正常区进行表面残余应力测试,结果如表4所示。由表4可知:试样1~3各部位均为压应力状态,即钢中晶面间距随压应力的增大而减小,信号区的应力高于正常区域,说明信号区晶面间距减小的程度更加明显,进而使材料的电导率升高。涡流检测是在工件中产生涡电流的过程,因此,可以建立涡流与应力的对应关系。说明材料电导率的分布与涡流信号存在相关性,涡流检测技术可以评估残余应力的大小。
3、综合分析
轧辊涡流检测信号受到材料残余应力的影响,结合实际生产中的工艺过程可以判断:表面淬火过程中感应线圈电流磁场转变过程会导致局部区域出现加热充分、碳化物溶解、奥氏体化充分等现象,使材料表面晶粒尺寸变大、表面硬度增加。
目前试样1~3均已完成了10个以上的轧制周期,使用过程中未发生任何影响轧制板面的异常现象,且在试样使用过程中,涡流信号随轧辊直径的增大而迅速降低(见图3)。说明该类涡流信号主要分布在轧辊近表面,与表面淬火应力的分布有高度的对应性,进一步证实了轧辊涡流检测信号与材料的残余应力有关。
4、结论及建议
轧制前的轧辊涡流信号为淬火过程中的工件表面残余应力分布不均所致,且随工件合金含量的增加,其残余应力差值逐渐增大。该类涡流信号不会造成任何轧辊使用异常,且涡流信号在使用初期的5~8个周期内会迅速降低至较低水平。
目前,锻钢冷轧辊并无行业统一的涡流检测控制标准,因此,在锻钢冷轧辊使用维护过程中,各轧线应该根据不同轧制工况、现场检测设备的型号特点,制定不同的管控要求。
作者:张大伟,罗昌,王文明
单位:宝钢轧辊科技有限责任公司
来源:《理化检验-物理分册》2023年第9期
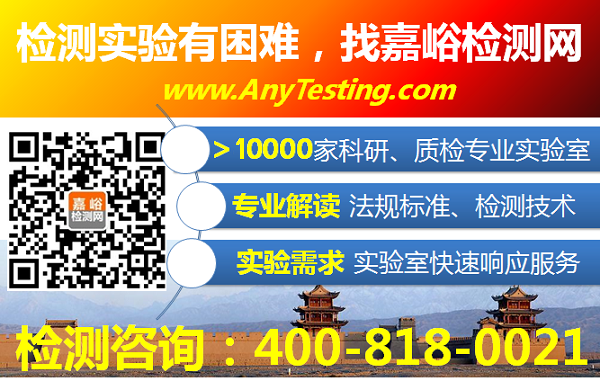