摘要:针对汽车方向盘发泡过程产生的主要缺陷导致产品发泡一次性合格率低的问题,文章提出一种通过质量工具找出影响发泡过程的关键因子,并使用回归分析对因子进行一一有效性验证。采取实验设计的方法,围绕上述关键因子的优化及标准化作业的实施,做了固定发泡过程的各个因子的工艺窗口及现场标准化控制的工作,并提供了一套提升方向盘发泡一次合格率的理论,达到了降低汽车方向盘发泡过程中主要缺陷比例、提高产品发泡一次性合格率的效果。
关键词:方向盘;发泡;实验设计;回归分析;合格率提升
汽车方向盘(Steering Wheel, SW)作为汽车内饰零件的重要组成部分,主要承担着车辆行驶转向控制、行驶方向的控制等功能。随着汽车智能化和电子化的发展,越来越多的功能也不断集成在方向盘上,如电子影音控制、智能控制、人机智能交互、主动安全预警、离手检测等[1]。所以方向盘零件不但作为功能件,同时也不断发展成车辆人工控制的中枢,作为最终消费者关注的重点区域。因此,消费者对于零件的功能表现、外观变现更加关注,对于方向盘生产过程的控制也提出了更加严格的要求[2]。
横置发动机模块化平台(Modular Querbaukasten,MQB)是大众集团研发的,该平台广泛运用于大众、奥迪、斯柯达和西雅特等大众品牌中,车辆级别分布广泛,从A00级到B级,需要兼顾不同消费者的外观和功能要求[3]。在零件的生产过程中,方向盘零件出现表面皮纹浅、不可见区域的飞边、多料、表面的平整度、缩孔等问题,随着外观标准不断加严,对于生产过程的控制,零件合格率都有较大的挑战。
本文对MQB平台中Lavida PA方向盘的生产过程进行分析研究,运用失效模式及效果分析(Failure Mode and Effect Analysis, FMEA)、6SIGMA[4]、回归分析、实验设计[5]等方法,寻找发泡过程中影响合格率的关键因子,并分析因子对于结果的关键影响,各因子之间的交互作用,通过建立数学模型,拟合数学表达式,寻找因子的最优解。最终定义因子的范围并进行标准化控制。
1、方向盘发泡过程主要缺陷
在实际的生产过程中,发现在方向盘本体的发泡过程中,最主要的缺陷分别为缩孔(发泡量不足本体存在孔洞,如图1所示),花纹不清(表面光滑花纹不能清晰显示,如图2所示),堵排气孔料(发泡排气孔堵塞表面有片状余料,如图3所示),拉料(零件从模具中取出时存在粘粘导致大块缺料,如图4所示)等,以上4种缺陷为最主要的过程缺陷,是方向盘发泡合格率不达标的主要原因。
图1 缩孔
图2 花纹不清
图3 堵排气孔料
图4 拉料
2、各类缺陷的主要成因
2.1 主要的缺陷类型的关键因子分析
针对以上提及的4种缺陷,通过分析供应商给出的生产过程流程图,确认问题产生的关键位置,同时,使用FMEA和鱼骨图等工具,寻找到与之显著相关的9个因子。从发泡过程的输入端到输出端,确认全过程的人、机、料、法、环等生产要素,如图5所示。
采用鱼骨图的方法,对于缺陷的形成原因和主要因子进行分析,如图6所示。
同时,使用潜在失效模式及影响分析(Poten- tial Failure Mode and Effects Analysis, PFMEA)工具,按照发泡过程严重度、频度和探测度对于众因子进行筛选,找出风险系数值(Risk Priority Number, RPN)最高的9个因子,如表1所示,并在后续进行一一验证和建模分析。
图5 发泡过程流程图
图6 花纹不清鱼骨图分析
表1 FMEA因子分析矩阵
2.2 关键因子影响数学模型归纳
综合以上的分析结论,找出了基于严重度、基于成品合格率的9个因子,对于因子的相关性和影响程度,通过数学模型分析的方法进行验证。以方向盘发泡的合格率作为输出项,因子的不同变化范围作为输入项,对各因子进行多项式回归分析,结果如图7—图15所示。
图7 自由泡密度的拟合线图
图8 原料循环搅拌时间的拟合线图
图9 原料温度的拟合线图
图10 脱枪距离的拟合线图
基于以上的拟合线图分析,二次模型较好地拟合了数据,通过检查此图,可以发现数据随机地散布在回归线周围,表明不存在系统失拟;通过图表分析,可以建立良率与相关因子的数学表达式,拟合曲线全部处在95%的置信区间内,且R-Sq(描述数学表达式完整描述系统的程度)均在85%以上,9个因子对于良率的影响如上图数学表达式所示,将在下一改善阶段中进行改善。
图11 模枪压力的拟合线图
图12 模枪距离的拟合线图
图13 脱枪角度的拟合线图
图14 脱枪距离的拟合线图
图15 料比对拉料的拟合线图
3、改善对策
基于上一步的数学分析,确定了不同因子对于良率的影响关系,能够确认随着因子范围的变化,良率会随之变化;对于多因子共同影响的缺陷,我们通过实验设计进行验证,寻找该因子的相互影响以及因子的最优解。
3.1 缩孔缺陷的全因子验证
根据前面所述的因子分析矩阵,对于缩孔缺陷,涉及的因子有自由泡密度、发泡料的搅拌时间以及模温;对于缩孔的3个参数,进行3因子2水平的全因子实验,寻找因子间的交互作用和最优解。具体如表2所示。
表2 缩孔因子矩阵表
通过上述方法,根据实验设计结果,可以确认不良率的主效应图和交互作用图,以及3个因子的最优解,如图16、图17所示。
图16 缩孔因子的主效应图和交互作用图
图17 缩孔多因子最优解立方图
从立方图看,自由泡密度150 g/cm2,搅拌时间60 min,料温30 ℃,对于缩孔的良率影响最小。
数学模型:
Y(缩孔不良率)=-3.595 00+0.240 000×自由泡密度+0.234 167×搅拌时间+0.490 000×料温-0.000 158 33×自由泡密度×搅拌时间-0.000 325×自由泡密度×料温-0.000 433 3×搅拌时间×料温
3.2 花纹不清的全因子验证
在PFMEA矩阵中,对于花纹不清的主要因子是脱模剂喷枪距离和脱模剂喷枪压力,同样进行2因子2水平的全因子试验设计进行验证,如表3所示。
表3 花纹不清因子矩阵表
同3.1,进行多因子交互实验验证及试验设计得出2因子的主效应图和交互作用图和因子最优解,如图18、图19所示。
图18 花纹不清因子的主效应图和交互作用图
从立方图可以看出,模枪距离25 cm,模枪压力0.4 MPa,对于花纹不清的不良率影响最小。
Y(花纹不清不良率)=-0.365 000+1.325×模内漆枪压力+0.014 000 0×模枪距离-0.050 000 0×模枪压力×脱枪距离
图19 花纹不清多因子最优解立方图
3.3 堵排气孔料缺陷全因子验证
同3.1及3.2,按照上述PFMEA的因子矩阵,设计对于堵排气孔料的全因子实验进行验证,如表4所示。
表4 堵排气孔因子矩阵表
进行因子实验,得出不良率的实验结果,因子交互作用图及主效应图以及因子的最优解如图20、图21所示。
图20 堵排气孔料因子的主效应图和交互作用图
从立方图看,脱枪角度90度,料比0.65对于排气孔堵得不良影响最小。
Y(堵排气孔不良率)=-0.946 93+0.007 049 63×脱模剂喷枪角度+0.015 816 7×料比-0.000 121 481×脱模枪角度×料比。
图21 堵排气孔料多因子最优解立方图
3.4 拉料缺陷全因子验证
同3.1,3.2及3.3,选取关键因子进行试验设计和验证,如表5所示。
表5 拉料因子矩阵表
进行因子实验,得出不良率的实验结果,因子交互作用图及主效应图以及因子的最优解如图22、图23所示。
从立方图看,脱枪距离25 cm,脱枪角度45度,料比0.65对于拉料的不良率影响最小,其数学表达式:
图22 拉料因子的主效应图和交互作用图
Y(拉料不良率)=-2.141 29+0.041 108 3×脱枪角度+0.072 969 7×脱枪距离+0.032 343 3×料比-0.001 845 40×脱枪角度×脱枪距离-0.000 624 667×脱枪角度×料比-0.001 129 33×脱枪距离×料比+0.000 002 800 0×脱枪角度×脱枪距离×料比。
图23 拉料多因子最优解立方图
综上,通过以上4个实验设计,分别对于不同的缺陷类型重新定义了各因子的最优解,通过数学表达式找到了各个因子的工艺窗口,同时对优的工艺参数进行标准化,如表6所示。
表6 因子工艺参数矩阵表
同时,对于发泡现场的工艺过程控制,重新定义了标准化的操作方法,如表7所示。
表7 标准化作业优化矩阵表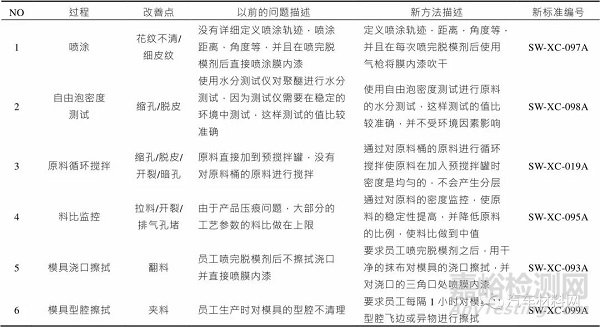
通过上述的因子优化及标准化作业的实施,对项目的发泡过程进行长期监控,其合格率由原有的96.8%提升至98.1%,如图24所示。
图24 方向盘发泡合格率确认表
4、总结
文章找出了影响发泡的关键因子和各因子的最优解,通过数学表达式找到了各个因子的工艺窗口,同时对优的工艺参数进行标准化。提供了一套提升方向盘发泡一次合格率的理论,达到了降低汽车方向盘发泡过程中主要缺陷比例、提高产品发泡一次性合格率的效果。
对于方向盘零件的发泡过程,主发泡料能够实现精准投放和控制,但是另外其他物料,如脱模剂,膜内漆等,需要人工手动喷涂,并通过上述的实验设计定义相关的参数才能获得理想效果。未来,关于此类发泡过程,行业内正在发展的是自动喷涂,通过计算机和机械手的合作,按照设定的喷涂角度,喷涂时间,喷涂压力保证模内漆和脱模剂喷涂到位,从而避免人工带来的影响。
同时在发泡前,需要对方向盘模具进行手工打磨,由于方向盘造型的问题,当前仍然无法实现自动打磨,对于发泡效率和最终的打磨的结果无法保证,正在发展的趋势是使用柔性自动打磨机对于发泡模具进行自动打磨,保证表面清洁度。
参考文献
[1] 黄安华.浅谈汽车的转向系统[J].农业装备与车辆工程,2014(1):7-10.
[2] 和琳,刘文思,高婷婷.中国汽车零部件行业发展研究[J].汽车实用技术,2021, 46(16):189-191.
[3] 董志清,史荣华.驾驶员气囊撕裂线外观改善研究[J].汽车实用技术,2020,45(18): 57-60.
[4] 马逢时,刘传冰.六西格玛管理统计指南[M].北京:中国人民大学出版社,2010.
[5] 闵亚能.实验设计(DOE)应用指南[M].北京:科学教育出版社,2012.
来源:期刊《汽车实用技术 》;作者:谭 杰,徐永康,刘 真,汤龙彪,米双年(上汽大众汽车有限公司长沙分公司)
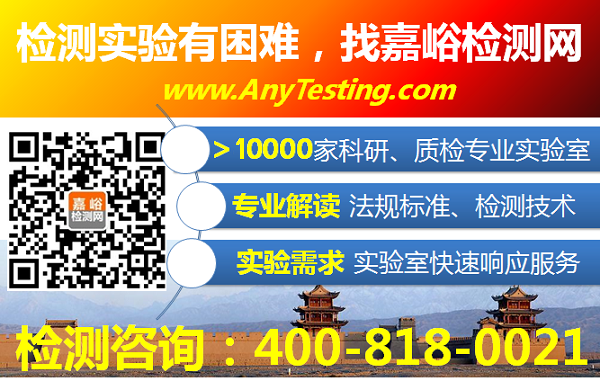