随着世界汽车保有量的持续增加,能源短缺、环境污染等一系列问题日益突出,节能、环保成为世界汽车工业有待解决的两大问题。
为应对这些问题,世界各国相继出台了严格的乘用车油耗与排放标准。面对节能减排的巨大挑战,如何降低汽车能耗以及缓解其所造成的环境污染,已成为汽车行业必须解决的难题。
“汽车轻量化”作为解决这一难题的关键技术之一,是现代汽车技术的重要发展方向。
汽车轻量化不仅能减少动力和动力传动系统的负荷,提高汽车动力性能,有效降低制动距离,而且能明显提高汽车行驶平稳性和舒适性。另外,车身的轻量化设计对提高汽车的经济性、环保性和动力性能有重要的现实意义。权威研究显示,汽车整车质量若降低 10%,其燃油效率可提高 6%~8%;当汽车整车质量每减少 100kg,百公里油耗可相应降低 0.3~0.6L,二氧化碳排放量亦可减少约 8~11g。
当前汽车车身轻量化的重要途径之一便是采用轻质高效的复合材料零部件。
复合材料是由两种或两种以上不同的材料,通过物理或化学的方式制备而成的具有优于自身组成材料特性的新材料。各种材料在性能上相互取长补短,产生协同作用,使最终成型的复合材料的综合性能优于原组成材料而满足各种不同的要求。
目前,市面上有不少厂家采用酚醛树脂、环氧树脂、不饱和树脂等热固性材料或相关的注塑成型产品来制作汽车相关零部件。这类热固性材料虽然密度小,质地较硬,能在一定程度上解决汽车轻量化、隔音降噪、降低能耗等问题,但由于其自身材料特性使得其所制成品皆为一次性成型产品,不具备回收性,对于汽车行业的长远发展来说其实是不利的。
因此,一种性能优越、质量比较小、可回收利用且成本低廉的热塑性复合材料(聚丙烯、尼龙、涤纶、聚氯乙烯、聚碳酸酯、 聚甲醛、聚苯乙烯等)被推广到汽车应用领域的最前沿。
长玻璃纤维增强聚丙烯复合材料(PP 复合材料)作为一种十分典型的热塑性复合材料,拥有韧性好、强度高、密度小、保存期长、可回收利用及价格低廉等优点。
长玻纤增强 PP 产品是一种改性塑料材料。该材料一般为长度 12 毫米或 25 毫米,直径 3 毫米左右的柱状粒子。在这种粒子中,玻璃纤维有着和粒子同样的长度,玻璃纤维的含量可以从 20% 到 70% 不等,粒子颜色可以根据客户要求进行配色。该粒子一般可以用于注射及模压工艺,可以生产结构件或半结构件,应用的领域包括汽车、建筑、家电、电动工具等等。
汽车工业的应用:前端框架、车身门板模块、仪表盘骨架、冷却风扇及框架、蓄电池托架等,用于替代增强 PA 或金属材料。
由于其较为广泛的应用面,关于 PP 复合材料的制作工艺与性能方面的研究工作变得尤为重要。针对不同的性能要求、产品结构、工艺特点等条件,PP 复合材料的制作要求充满了多样性。
一方面,若生产一般性的汽车相关零部件:下护板、座椅骨架、仪表盘等,则需要 PP 复合材料能为产品提供较高的美观性能和力学性能。另一方面,若生产汽车发动机底护板等隔音部件时,由于需要部件能够拥有一定的厚度与孔隙率,以保证底护板的降噪、隔音性能,则需要 PP 复合材料能够在一定程度上有效控制产品结构的孔隙率与疏密程度等。
由于热塑性复合材料一般都是在加热后进行流动成型的,针对不同的工艺特点,生产过程中成型设备加热温度、设备保温温度、设备加热时间、保温时间以及层合板材的预热温度、预热时间、生产过程中的温降冷却控制等工艺条件都是充满着变化的。
因此对于 PP 复合材料而言,优越的半成品制作工艺及成型工艺对于最终产品的制作工作来说,有着特别重大的意义。
由于玻纤增强聚丙烯复合材料在汽车领域日益广泛的应用,在汽车轻量化研究方向上十分具有潜力,与车用 PP 复合材料有关的产品性能、力学特性的研究工作也相当重要。
由于具有良好的抗冲击性、吸能性,使得 PP 复合材料被合理地应用到前防撞梁、吸能盒等重要的汽车零部件上,较优的拉伸、弯曲性能可有效提高仪表盘、座椅骨架、尾箱等车用零部件的安全可靠性,合理的板材疏密程度与较大的孔隙率能使汽车发动机底护板获得更好的隔音、降噪性能。
长玻纤增强PP的国内研究
作为一种新型复合材料,热塑性复合材料的发展起源于上世纪 80 年代,主要分为长纤维增强粒料(LFP)、玻璃纤维毡增强热塑性复合材料(GMT)、连续纤维增强预浸渍带 (MITT)等。
我国针对热塑性树脂基复合材料的研究起步相对较晚,开始于 20 世纪 80 年代末期,而到上世纪 90 年代中期,国家才开始将汽车用 GMT 复合材料的研究应用列为国家级相关的高科技计划项目。
自 2003 年以来,国内先后有多家科研院所、科研单位及企业开始进行 GMT 板材制备工艺的研究工作,其中华东理工大学以及个别企业的研究最为前列,其相关研究与实验产品已部分成功投产或得到实践应用。
总体来说,我国在热塑性复合材料领域的研究工作尚未取得显著性突破,与发达国家之间仍存在一定的差距。
长玻纤增强PP的发展现状
作为应用最为广泛的热塑性树脂基复合材料,玻纤增强聚丙烯复合材料的发展也到了相当高的成熟阶段,最为主要的就是三大类型中的 GMT 复合材料,GMT 复合材料最早问世于 20 世纪 60 年代,并于 20 世纪 80 年代发展起来。现如今已被各国各行业,如航空航天、建筑、汽车、医疗、化学电子等广泛地应用。
1999 年美国 Azdel 公司开发出一款新型的 SuperLite 轻质 GMT 板材,标志着轻量化 GMT 板材的真正面世。2003 年,瑞士同样制作出性能一致的轻质 GMT 板材 ——Symalite 板材。紧接着,2005 年,Owens-coming(欧文斯科宁)公司也公布了其公司的轻质 GMT 板材。
就目前而言,市面上品质最高、质量最好的 GMT 类 材料都以此三大公司生产的为主。我国 GMT 材料的发展由于起步相对较晚,在基础材料、工艺方法、设备研发上仍然落后于此类发达国家。
另外,随着纳米技术逐渐地引起人们的关注,与纳米技术有关的复合材料研究开发工作也成为新时代的研究热点。以纳米技术改性基体树脂,可使基体树脂的结晶形态和聚集态发生一定程度的改变,从而使之产生新的性能,能够有效克服传统材料韧性与刚性难以相容的矛盾,同时,也能大大提高材料的综合性能。
长玻纤增强PP在汽车上的应用
长玻纤增强聚丙烯作为一种热塑性树脂基复合材料,目前在车身上的应用现出快速发展的趋势。相关研究者、汽车制造者及立法者已将更多的目光投向轻量化复合材料在车身零部件上的应用。
此前的一些研究针对车身零部件制造,已采用纤维增强复合材料来取代传统金属材料。
早在上世纪 80 年代,ICI 公司就实现了长纤维增强热塑性粒料的工业化生产,随后 Ticona、RTP、北欧化 工等公司也开始相继成为长纤维增强热塑性粒料的生产商。长纤维增强热塑性粒料采用注塑成型加工为最终制品,由于其相较于短玻纤复合材料力学性能有明显改善,因此其开始大量应用于汽车车身。
Jeep 公司牧马人系列最早使用长玻纤增强聚丙烯材料作为车门护板及前端模块;Rieter 公司提供的长纤粒料应用于大众 PQ35 系列的前端模块;RKT 公司采用长玻纤增强聚丙烯材料进行发动机罩、隔音罩及前端模块的生产。
雷诺及通用汽车公司将一种片状模压料应用于乘用车的防撞梁中。诸多研究已将玻纤增强聚丙烯广泛应用于汽车零部件中,例如:车门、车身外板、地板、框架部分、电池检修门及座椅系统,其与传统金属部件相比质量可减少 40%~60%,与此同时却显示出相同甚至更好的性能。
Jeyanthi 等人通过实验及有限元数值仿真方法研究了复合材料防撞梁的碰撞过程,结果显示长玻纤增强热塑性复合材料防撞梁在侵入量及能力吸收方面有较好表现。
由于长纤维增强热塑性粒料的生产成本较高,而且在注塑成型时会造成纤维的严重断裂导致力学性能的降低,其应用受到了限制。
为了避免上述问题的出现,许多厂商开始对原材料及成型工艺进行改进。Azdel 公司首先推出中长玻璃纤维 毡增强聚丙烯片材,采用模压成型工艺以减少成型时纤维的断裂,来取代粒料进行车身制品的生产;Faurecia 公司采用长玻纤聚丙烯片材为标致汽车公司生产前端模块及底盘防护系统;大众途安系列采用长玻纤聚丙烯片材作为前端支架及扰流板;我国北京汽车生产的勇士军车也采用长玻纤聚丙烯材料作为发动机罩盖及左右翼子板。
长玻纤增强PP的制作方法
PP 复合材料是由 GF 与 PP 树脂复合而成的材料,由于 GF 与 PP 种类与结构状态的不同,其混合方法与混合类别有很大的差异,但归根结底,其制作工艺主要分为两大类:干法工艺与湿法工艺。本文主要介绍干法工艺,对湿法工艺不再进行赘述。
干法工艺一般也称为梳理工艺,是借用于无纺机械工艺发展而来的,其具体的制作方法主要分为两大部分:制毡部分和制板部分。
制毡部分主要包括:纤维的开包、开松、混合、梳理、成网、针刺及收卷等。
制板部分主要包括:毡材的表面处理、无纺布的布置与选型、加热熔融板压或辊压及裁边等。
传统的制毡部分主要步骤如下:
1 开包
市面上购置的纤维一般为袋装,且呈压缩状,需要经过开包机开包,使大部分的块状或团状纤维分解,离散成絮状或束状。然后再输送至下一道工序。
开包机的特点:开包机内安装有电子自动磅棉装置,能将不同的纤维按产品所需比例混合。
2 开松
经开包后的纤维只是解除了袋装中的压缩状,纤维整体上还是呈小块分布的,需经过开松工艺,使纤维分散至一定程度,再输送至下一道工序。开松机内装有钉耙式刺辊,能将开包后的化纤达到初步开松的目的,即:从大的纤维块、纤维团或纤维束变成较小的纤维块或纤维束。
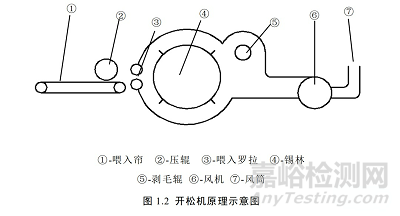
开松的原理:根据所制毡材的分散度要求,开松一般可分为预开松与精开松, 预开松一般采用刀片式(开松锡林上安装刀片)开松,精开松一般采用梳针钉板 (开松锡林上装有梳针)开松。
3 大仓混棉
大仓混棉是相对于部分将两种或两种以上的纤维混合制毡的工艺而言的重要工序,主要是完成各种纤维原料的混合、开松、储备等功能,要求在减少对纤维损伤的同时,又要使混合纤维达到均匀的絮状,并完成纤维原料的输送和均匀喂入。设备为大仓混棉箱。
大仓混棉原理:最简单的大仓混棉箱主要由平帘、斜帘、限厚辊和剥取辊等组成,纤维经输入风道输送至大仓混棉箱,自上开风口降落至平帘上(风道部分拥有一定的混合作用),再经斜帘往斜向上方向输送,由限厚辊限制输送纤维层厚度,纤维经剥取辊打乱、剥离斜帘,沉降于输出帘,供下一步梳理工序使用。其混合作用主要体现在风道中的气流输送过程,纤维于仓体中的气流吹落过程, 斜帘上限厚辊的转动使高于厚度部分的纤维在斜帘上反复翻滚混合以及剥取辊的离心力打乱混合作用。
4 梳理
梳理是整个制毡工艺中最为重要的工艺之一,梳理工艺的工艺质量直接影响着最终产品的质量。梳理的主要作用是对纤维进行进一步开松与除杂,将纤维梳理成束状、单丝状(单根纤维状态),大幅度提高纤维的分散性,梳理过程也能在一定程度上将多种纤维进一步混合,提高纤维层的混合均匀性。另外,对于结构上有杂乱不规则排布要求的纤网,梳理机还能配置杂乱装置(一般是杂乱辊),使其满足相关要求,杂乱结构的形成对于减小最终产品的纵横向强力比值差有一定的促进作用。梳理后的纤维一般由道夫凝聚,再经过斩刀的剥取作用,经网帘输送至下一步成网设备。
梳理的原理:经大仓混棉后的纤维,由平帘输送至梳理机喂入罗拉处,经罗拉喂入工作锡林,工作锡林上安装有工作辊与剥取罗拉(剥取辊——同复杂形式的开松机),两者的综合作用,能将纤维进行进一步打乱、分散,形成分散性较高的纤维层,最后经道夫输送至网帘至下一步成网工序。
传统的成网工艺主要分为四帘铺网、立式铺网等,其主要作用都是将梳理工序形成的纤维,均匀等厚地铺设成一定克重的纤维网层,再输送至下一道针刺工序。这一类的成网工艺应用得最为成熟与广泛,梳理机输出的纤维层是呈单方向分布的,四帘铺网与立式铺网都是直接将梳理机输出的纤维层往复式的铺设在成网帘上,所以所制纤维网一般纵横向力学性能相差较大。设备为四帘铺网机和立式铺网机。
6 针刺
经成网机成网后的纤维网是处于一种蓬松的大厚度状态,整体结构孔隙率大,需要对其进行机械加固以获得拥有一定强度的毡材。而最为常用的机械加固手段就是针刺,针刺一般是利用带有倒钩的刺针,将纤网中水平分布或斜方向分布的纤维利用倒钩刺入纤维层中心,使纤维改变原有的状态,纤维之间相互靠拢、缠绕。通过对纤网进行多次反复的机械针刺加固,使纤维与纤维互相紧密缠结而产生较大抱合力,并使纤网的密度提高,纤网的整体厚度也因此被压缩,形成既结实又有强力的基体材料。设备为针刺机。
7 切边收卷
将针刺后的基毡切除边角料并计量,按幅宽要求收卷成具有一定长度与重量的基毡。设备为收卷切边机。
毡材经收卷后即为完成了制毡部分的工艺。
另一部分为制板部分,传统的制板部分主要是三明治结构制板,即:将纯玻璃纤维按制毡部分工艺制作成玻璃纤维针刺毡(玻璃纤维针刺毡具有耐腐蚀、耐高温、减震、降噪、吸音、阻燃、尺寸较为稳定、伸长收缩率极小、强度高、成本低等优点。但其运行阻力高于一般的化纤高温滤材。玻璃纤维针刺毡现阶段主要是作为制造聚丙烯片材(GMT)和热塑性片状模塑料的增强材料),经一定的压力与温度的条件下,按所需玻璃纤维比例,复合树脂(PP 树脂)片材,压制成具有较高强度的复合式板材。
现阶段国内很多科研院所、高校以及生产厂家对干法工艺都做了一定的改进工作,但大体都不离开这两部分工艺。
长玻纤增强热塑性复合材料作为当今玻璃纤维增强材料的一个发展趋势,受到了国内外各大塑料改性生产厂商的高度重视,特别是长玻纤增强聚丙烯材料,由于其很高的性价比优势,更被业界所广泛看好。
目前这些厂商纷纷投入大量的人力、物力进行该类型材料的生产研发和市场开拓的工作。
综上所述,当 PP 复合材料应用于汽车行业时,一方面要求其能满足汽车相关零部件的强度、刚度、模量、安全及质轻等性能方面的要求和相关的法规与标准,另一方面考虑到成本控制,又要求其能在一定程度上简化、优化相关的半成品、成品的生产工艺。
因此,对于 PP 复合材料相关制作工艺及力学性能的相关研究工作相当重要,而对于其在汽车零部件上的应用也迫在眉睫。
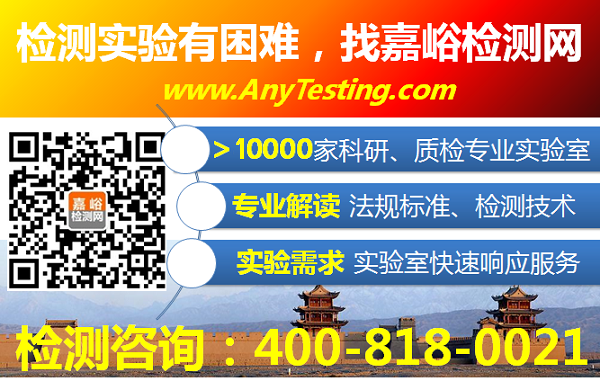