摘要:为了研究不同汽车制动盘特性对摩擦与噪声性能的影响,分别采用车削制动盘和磨削制动盘,匹配相同配方的摩擦片,在制动性能台架上研究了摩擦性能和蠕动噪声性能,并采用实车测试了蠕动噪声性能。结果表明:当制动盘表面特性为杂乱无章的磨削条纹时,摩擦副表现出较高的摩擦因数,摩擦片前期磨损较大,蠕动噪声相对较差;当制动盘表面特性为同心圆形式的车削条纹时,摩擦副的初始摩擦因数相对略低,摩擦片前期磨损较小,蠕动噪声较好;随着摩擦副的制动次数增加,两者的差异逐渐减小。通过微观分析进一步研究了摩擦磨损机制:磨削盘对应的摩擦片,切削磨损占主导地位,摩擦片表面无法形成均匀的摩擦面,而车削盘与摩擦片贴合性好,可以快速形成稳定而连续的摩擦面。
关键词:制动盘;摩擦材料;蠕动噪声;摩擦因数;磨损性能
引言
汽车制动噪声,根据其噪声频率范围和频率分布的集中程度大致可以分为:低频/高频尖叫(1~3 kHz/4~16 kHz),呻吟(moan)噪声(<1 kHz),蠕动(creep groan)噪声(<500 Hz)等[1-3]。
所谓蠕动噪声,是指在极低的车速和较低的制动压力下发生的一种低频振动噪声。常见的工况为自动挡车型的起步瞬间[3-4],在车辆即将发生位移时,来自摩擦副的制动力和车辆起步扭矩的驱动力同时作用,摩擦片与制动盘的摩擦界面发生黏-滑运动。这种黏-滑振动通过车辆悬架系统和车身船体到车内,驾驶员同时感知到噪声与车身的振动,这种现象就被称为蠕动噪声[2,4]。
对于蠕动噪声的发生机制,一般认为是由于摩擦副在滑移面上产生的黏-滑运动,进而发生明显的振动噪声[4-10]。而这种黏-滑运动是由于摩擦副的动摩擦因数(μk)和静摩擦因数(μs)的差异(Δμ)过大导致的。近年来,国内外学者在黏-滑机制研究、蠕动噪声等方面做了大量研究,取得了众多成果[11-18] 。
张立军等[11]研究了蠕动颤振发生时的振动和悬架变形特征,提出了“弓形效应理论”并通过试验证明了弓形效应对于起步蠕动颤振具有一定的影响,同时发现制动力分配因数对于起步蠕动颤振现象具有显著的影响。Yoon等[14]研究了摩擦副在不同法向正压力载荷及滑动速度下的摩擦因数波动性能。研究结果表明,黏-滑振动幅度随着摩擦副受到的法向载荷增大而增大,而随着摩擦副滑动速度增大而降低。Fuadi等[15]设计了一种卡钳-滑板装置,并研究了黏-滑现象的影响因素。研究结果表明,蠕动噪声在如下条件下可以被消除:①结构刚度与摩擦副接触刚度比大于40;②低频黏-滑指数大于400。Jang等[16]研究了酚醛树脂、硅酸锆、摩擦粉、岩棉等原材料对动静摩擦因数的影响。研究结果表明:硅酸锆、钢棉和酚醛树脂会增大动、静摩擦因数差异,而腰果壳油摩擦粉、芳纶纤维、岩棉等材料则可以降低动、静摩擦因数差异。他们基于研究成果得出了最优配方组合,获得了最小动、静摩擦因数差异的配方材料。
然而,过往研究往往集中在摩擦片材料方面,或者通过车身结构方面,而对于摩擦副重要组件——制动盘对蠕动噪声的研究很少有报道。本文采用不同表面特性的制动盘匹配相同配方的摩擦片,对摩擦副的蠕动噪声、摩擦因数以及磨损性能等方面进行了深入研究,探讨了不同工况下的摩擦磨损机制,对摩擦副开发提供了良好的指导意义。
1、试验设计
本文采用的摩擦片是由成熟的NAO(无石棉有机型)摩擦材料配方生产而得。摩擦材料的主要组分见表1。摩擦片的生产过程采用常规的摩擦片制程生产,其工序主要包括混料、压制、固化、机加工、烧蚀等,摩擦片型号基于现有某中型SUV的量产产品。
表1 摩擦材料的主要组分
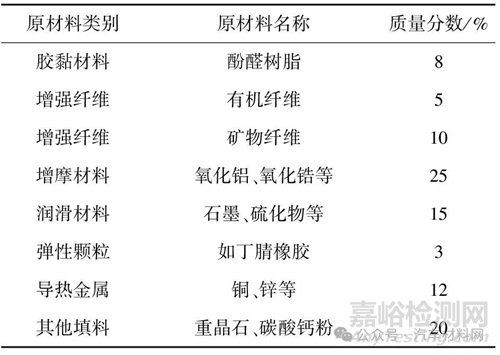
本研究采用的制动盘为某OEM车型的量产产品,其原始加工状态为磨削方式,加工纹路为杂乱的发射状,磨削制动盘表面状态及加工纹路示意如图1所示。为了研究不同制动盘表面状态的性能,对制动盘进行车削加工处理,得到同心圆型加工纹路,车削制动盘表面状态及加工纹路示意如图2所示。
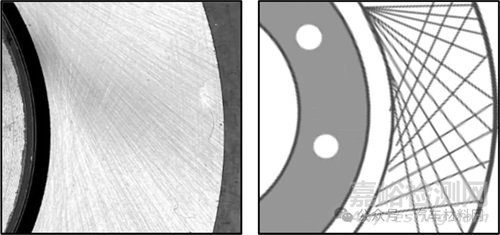
图1 磨削制动盘表面状态及加工纹路示意
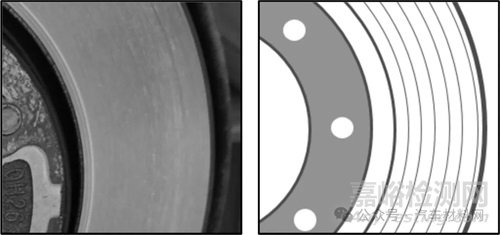
图2 车削制动盘表面状态及加工纹路示意
对蠕动噪声进行实车测试,测试程序为:摩擦副安装完成后,首先做0 km坡道蠕动噪声测试。然后在规定的城市路线上进行日常驾驶、制动,使摩擦副逐步磨合。为了保证两组制动盘测试结果的一致性,本测试严格规定了磨合过程中的行车路线,每天行驶里程为100 km,每天制动次数约80次。每次的制动工况为:初速度约为60 km/h,约0.2 m/s2的减速度,末速度约为20 km/h。为了排除温度及湿度等气候因素,测试选择在气温和大气湿度都比较稳定的秋季(10月)进行。
每天磨合完成后,于次日早晨分别在平地和20%坡道上做冷态起步噪声评价。连续进行5 d不间断测试,总计摩擦里程为500 km。冷态坡道起步噪声评价方式为:挂D挡,缓慢松开制动踏板,于驾驶员头枕位置,采集音频分贝值,连续进行10次测试后取其平均分贝值记录。
对蠕动噪声的台架模拟测试,测试程序为:首先采用SAE J2522 AK-Master (Issued 2014—6)的测试程序进行磨合,磨合完成后进行蠕动噪声测试。蠕动噪声测试原理为:控制驱动扭矩为恒定值,缓慢降低制动压力,在制动压力降低到一定值后,摩擦开始出现缓慢滑移,驱动扭矩在控制扭矩值附近产生波动,对扭矩波动绝对值进行求和,得到的数值越小,意味着起步过程产生的黏-滑运动幅度小,则蠕动噪声表现越好。
采用Link 3900台架研究产品的摩擦磨损性能,摩擦因数评价运行程序为SAE J2522 AK-Master (Issued 2014—9),磨损性能评价的运行程序为SAE J2707A,并采用LEICA125体式显微镜对摩擦副表面状态进行研究。
2、结果与讨论
2.1 蠕动噪声整车测试
图3是两种制动盘匹配相同的摩擦片在平地和20%坡道上的蠕动噪声。蠕动噪声结果显示,车削制动盘的蠕动噪声总体上低于磨削制动盘,但是无论是哪种制动盘,在平地上的蠕动噪声均较20%坡道上好。
图3 两种制动盘匹配相同的摩擦片在平地和20%坡道上的蠕动噪声
图4为车辆在平地和坡道上的受力分析。当车辆处于平地起步时,车辆前进的驱动力来自于发动机的初始输出力F1,相应的摩擦界面将形成与之相近的制动力f≈F1。而当车辆处于坡道上时,除了发动机的初始输出力F1,还有来自车身自重在坡道方向上的分量GX,相应的摩擦界面将形成与之相近的制动力f≈F1+GX。因此在坡道上起步时,摩擦界面的动、静切换产生的能量更大,导致蠕动噪声较大。
图4 车辆在平地和坡道上的受力分析
对比两种制动盘的蠕动噪声可见,车削制动盘的结果明显优于磨削制动盘。这是因为车削盘的条纹与摩擦方向一致,有利于摩擦副快速进入磨合状态,因而产生的黏-滑振动能量较小。
此外,随着磨合里程数的增加,蠕动噪声逐渐降低并保持平稳,且两者差异也逐渐减小。主要原因是:随着不断的摩擦,摩擦副的有效接触面积逐渐增大,摩擦界面的贴合性越来越好。因此黏滑振动的幅度也随着降低,以致蠕动噪声逐渐得到改善并保持稳定。
2.2 蠕动噪声台架测试
为了更加客观反映蠕动噪声发生时的界面行为,在台架进行300次磨合制动后测试模拟蠕动噪声得到扭矩波动值总和如图5所示。图中结果显示,模拟坡道测试记录的扭矩波动值的总和为800~1 200 N·m,显著大于模拟平地的300~400 N·m。而车削制动盘产生的扭矩波动值之和显著低于磨削制动盘,在平地模拟测试中,车削制动盘产生的扭矩波动值总和比磨削制动盘低17%;而在20%坡道模拟测试中,两者差异达到了22%。以上结果意味着,使用车削制动盘可以显著降低起步过程中的制动扭矩波动,即摩擦副将具有更好的蠕动噪声性能,这一结果与实车测试结果具有良好的一致性。
图5 台架模拟蠕动噪声的扭矩波动值总和
图6和图7分别为台架模拟蠕动噪声测试后的制动盘和摩擦片。车削制动盘的外观光滑平整,原始的车削纹路变小,产生了一些制动摩擦纹路,总体比较平整光滑。而磨削制动盘表面依然可以看到原始的发散状的加工纹路,且出现了两条暗色的同心圆。进一步观察摩擦片的显微镜照片,车削制动盘所用的摩擦片表面形成了连续、光滑的摩擦面,而磨削制动盘所用的摩擦片表面相对粗糙,摩擦膜并未形成整体。由此可见,车削制动盘的条纹与摩擦方向一致,有利于摩擦界面尽快进入良好的贴合状态,因此在蠕动噪声上产生了显著的差异。
图6 台架模拟蠕动噪声测试后的制动盘
图7 台架模拟蠕动噪声测试后的摩擦片
2.3 摩擦性能
图8是两种制动盘分别匹配相同的摩擦片得到的SAE J2522 AK-Master摩擦因数。由图可以看出,该摩擦材料配方的摩擦因数整体比较稳定,在不同的压力、速度和温度下,均体现了良好的稳定性,平均摩擦因数为0.38~0.40。根据SAE J2522名义摩擦因数计算方式,两种状态的制动盘,在匹配相同的摩擦材料配方,两者的名义摩擦因数分别为0.383和0.385,且在各个测试章节中,均有一致的变化趋势。
图8 SAE J2522 AK-Master摩擦因数
两者的差异(图8的柱状图)主要体现在第1至第4.5章节,采用车削制动盘的初始摩擦因数,略低于磨削制动盘的初始摩擦因数,两者差异为负值。造成这个差异的原因是磨削盘表面杂乱的条纹,增大了制动盘的粗糙度,与摩擦片表面容易形成较多的接触点。而车削制动盘表面纹路为同心圆形式,与制动盘的转动方向一致,因此不利于摩擦片表面与制动盘的咬合。但是,随着制动次数的不断增加,制动盘表面的加工纹路逐渐消失,被摩擦产生的制动划痕所替代,因此当程序进入第4.4章节后,两种制动盘在的摩擦因数逐渐接近一致。
2.4 磨损性能
对不同种类的制动盘,采用SAE J2707A的程序研究了摩擦副的磨损性能,如图9所示。由图可以看到,磨削制动盘对应的摩擦片在第1至第3章节的磨损量,均高于用车削制动盘的摩擦片,这与其前期摩擦因数较高的结果是一致的。
图9 采用两种制动盘的磨损性能
微观上看,制动盘表面的加工纹路是具有一定深度的沟槽,这些沟槽不断与摩擦片摩擦、切割,从而产生摩擦因数和摩擦副的磨损。两种制动盘的摩擦界面微观示意如图10所示,车削制动盘的纹路与摩擦方向一致,有利于摩擦片和制动盘的磨合,在摩擦界面上较快地形成稳定连续的摩擦面。而磨削制动盘不仅有摩擦平行方向,还有垂直方向的沟槽,这些垂直方向的沟槽对摩擦片表面有较大的切削作用,因此其摩擦因数相对较高,但同时也加大了摩擦片的磨损。这种条件下,摩擦片表面的磨损机制为切削磨损,即摩擦片表面在硬度较大的制动盘表面的切削作用下产生摩擦犁沟,从而造成摩擦片表面的材料从基体上脱落。磨削盘表面垂直方向的纹路,使制动盘表面难以形成连续的摩擦面,从而使摩擦片的磨损量相对较大。随着制动次数的增加,摩擦界面都达到了较高的有效接触面积,因此两种制动盘的摩擦因数差异和磨损差异都越来越小,直至基本一致。
图10 两种制动盘的摩擦界面微观示意
3、结论
本文采用一种成熟的摩擦材料配方,研究了不同表面特性的制动盘性能。基于本研究的数据,得到以下结论:
(1)车辆蠕动噪声受车辆状态影响较大,当车辆处于坡道上,由于摩擦力需要平衡发动机的初始输出力和车辆自身重力分量,因此车辆在坡道上会表现出更加恶劣的蠕动噪声性能。
(2)具有同心圆加工纹路的车削制动盘,其加工纹路与摩擦方向一致,因而摩擦片表面较快地形成连续的摩擦面,因此其蠕动噪声性能较好。
(3)具有发射状态加工纹路的磨削制动盘,由于加工条纹形成了垂直于摩擦方向的沟槽,这些沟槽对摩擦片形成了较大的切削作用,摩擦片的磨损机制主要为切削磨损,因此磨削盘的前期摩擦因数和磨损量相对较大。同时,这些垂直方向的沟槽使摩擦片表面难以形成连续的摩擦膜,不利于摩擦因数稳定,因此起步噪声性能相对较差。
(4)随着制动次数的增加,两种制动盘在摩擦因数、磨损性能以及蠕动噪声方面的差异均逐渐减小。
(5)基于本实验结果,在摩擦副开发过程中,可以根据实际需求,选择相应表面特性的制动盘。
参考文献:
[1]李东.乘用车制动噪声及解决方法[J].内燃机与配件,2021(19):129-130.
LI D.The brake noise and relative solutions on passenger car[J].Internal combustion engine &parts,2021(19):129-130.
[2] 张立军,郑一兵,孟德建,等.汽车制动器摩擦颤振综述[J].同济大学学报(自然科学版),2016,44(3):420-426.
ZHANG L J,ZHENG Y B,MENG D J,et al.Literature survey of friction induced automotive brake groan[J].Journal of Tongji University(natural science),2016,44(3):420-426.
[3] AKAY A.Acoustics of friction[J].The journal of the Acoustical Society of America,2002,111(4):1525-1548.
[4] FUADI Z,MAEGAWA S,NAKANO K,et al.Map of low-frequency stick-slip of a creep groan[J].Proceedings of the institution of mechanical engineers,Part J:journal of engineering tribology,2010,224(12):1235-1246.
[5] BRECHT J,HOFFRICHTER W,DOHLE A.Mechanisms of brake creep groan[C]//Proceedings of SAE Technical Paper Series.Warrendale,PA,United States:SAE International,1997:3405-3411.
[6] ABDELHAMID M K.Creep groan of disc brakes[C]//Proceedings of SAE Technical Paper Series.Warrendale,PA,United States:SAE International,1995.
[7] FILIP P,RHEE S K.Contribution to the understanding of “stick-slip” friction and creep-groan phenomena in automotive brake materials[C]//Proceedings of EuroBrake 2020 Technical programme.Stansted,UK:FISITA,2020.
[8] LEE W K,JANG H.Moisture effect on velocity dependence of sliding friction in brake friction materials[J].Wear,2013,306(1/2):17-21.
[9] GAUTERIN F,GROCHOWICZ J,HAVERKAMP M,et al.Creep groan—phenomenology and remedy[J].ATZ worldwide,2004,106(7):15-18.
[10] ASHRAF N,BRYANT D,FIELDHOUSE J D.Investigation of stick-slip vibration in a commercial vehicle brake assembly[J].The international journal of acoustics and vibration,2017,22(3):326-333.
[11] 张立军,张频捷,孟德建.汽车盘式制动器蠕动颤振试验与理论分析[J].汽车工程,2016,38(9):1132-1139.
ZHANG L J,ZHANG P J,MENG D J.Tests and theoretical analysis of creep groan in vehicle disc brake[J].Automotive engineering,2016,38(9):1132-1139.
[12] KIM S J,CHO M H,CHO K H,et al.Complementary effects of solid lubricants in the automotive brake lining[J].Tribology international,2007,40(1):15-20.
[13] CHO K H,JANG H,HONG Y S,et al.The size effect of zircon particles on the friction characteristics of brake lining materials[J].Wear,2008,264(3/4):291-297.
[14] YOON S W,SHIN M W,LEE W G,et al.Effect of surface contact conditions on the stick-slip behavior of brake friction material[J].Wear,2012,294/295:305-312.
[15] FUADI Z,ADACHI K,IKEDA H,et al.Effect of contact stiffness on creep-groan occurrence on a simple caliper-slider experimental model[J].Tribology letters,2009,33(3):169-178.
[16] JANG H,LEE S J,FASH J W.Compositional effects of the brake friction material on creep groan phenomena[J].Wear,2001,251:1477-1483.
[17] GWEON J H,JOO B S,JANG H.The effect of short glass fiber dispersion on the friction and vibration of brake friction materials[J].Wear,2016,362/363:61-67.
[18] PARK C W,SHIN M W,JANG H.Friction-induced stick-slip intensified by corrosion of gray iron brake disc[J].Wear,2014,309(1/2):89-95.
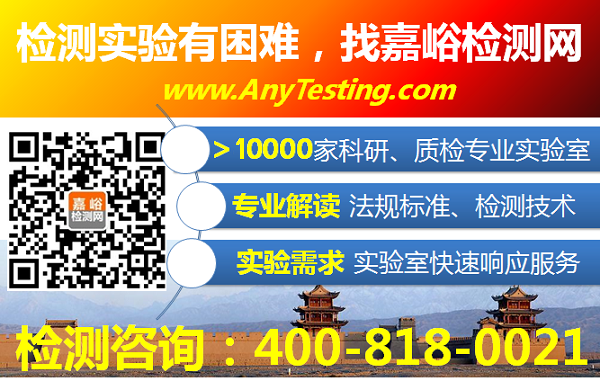