经渗碳、淬火和低温回火的齿轮类零件在磨削后会发现有浅裂纹,称作磨削裂纹。对有磨削裂纹的 20CrMnMo钢齿轮进行了化学成分分析、金相检验和硬度测定,以揭示产生磨削裂纹的原因。结果表明,齿轮的磨削裂纹是磨削过程中产生过高的磨削热所致,与热处理工艺无关。
磨削加工是齿轮生产的必要环节,在机械行业中被广泛应用。经渗碳淬火回火后的零件在磨削时常出现磨削裂纹,这些裂纹不仅影响齿轮的外观,还严重影响质量。磨削裂纹的深度一般较浅,方向与磨削方向垂直,呈网状分布。引起磨削裂纹产生的原因有很多,如成分偏析、非金属夹杂、网状碳化物、磨削量、砂轮硬度及粒度等。当工件表层的残余拉应力超过材料的抗拉强度时,便会产生磨削裂纹。通常采用磁粉法、荧光法和酸浸法进行检测。
太原重工生产的20CrMnMo 钢齿轮经过渗碳 (930 ℃)+淬火(830 ℃)+回火(180 ℃)后,在磨削加工过程中磨齿机进行余量分配时共磨削十二刀,第七刀发现磨齿机电流突然增加,经检查发现齿面有裂纹,磨齿机粗磨每次排刀0.02 mm, 每刀分六冲程磨削。
1、理化检验
宏观观察
通过对齿轮齿面裂纹进行宏观观察、磁粉探伤和酸浸试验,确定裂纹形态。图1(a) 为齿轮的宏观形貌,图1(b) 为从齿轮上切割下的单齿齿面裂纹形貌,从图1(b) 中可以看出裂纹呈线状分布,其分布形态为从齿顶至节圆上部呈龟甲状,并且在裂纹下端靠近齿根部位有明显的焦黑状条纹,裂纹方向垂直于磨削方向。
图1 20CrMnMo 钢齿轮(a) 及其表面裂纹(b)
化学成分及夹杂物分析
化学成分分析:根据图纸要求,该齿轮为20CrMnMo 钢,为确认材质是否符合要求,采用 PMI-MASTER PRO 光谱分析仪对齿轮的化学成分进行检测,结果见表1。从 表1可以看出P 含量略微超标,但仍位于上限偏差范围内,基本符合20CrMnMo 钢化学成分范围要求,其化学成分满足要求。
表1 20CrMnMo 钢齿轮化学成分(质量分数,%)
非金属夹杂物分析:为了判断锻件组织是否合格,根据要求对锻件的高倍夹杂情况进行分析,结果如表2所示。高倍非金属夹杂物按 GB/T 10561-2005《钢中非金属夹杂物的含量的测定》评定。结果表明,齿轮锻件纯净度合格,满足要求。
表2 高倍非金属夹杂物分析
显微组织及硬度
显微组织:对本体进行解剖,取下齿形试样,分别对齿顶、裂纹面节圆、裂纹处及齿根处进行显微组织观察,所用设备为 Axiovert40MAT 金相显微镜,依据 JB/T 6141.3-1992《重载齿轮渗碳金相检验》进行检验,工件组织要求1~3级,结果如表3所示。
表3 组织检测结果
图2分别为20CrMnMo 钢齿轮齿顶马氏体及残留奥氏体、齿顶碳化物及心部组织形貌,与标准图谱对照后,发现齿顶马氏体及残留奥氏体3级,为细针马氏体及30%残留奥氏体,齿顶碳化物为细颗粒状碳化物,心部组织3级,为低碳马氏体加少量游离铁素体。
裂纹面节圆处组织为马氏体及残留奥氏体,3 级,属于细针马氏体和30%残留奥氏体,并存在轻微的二次淬火组织,碳化物1 级,为细颗粒状碳化物,组织满足要求,没有超标现象。
图2 失效齿齿顶的马氏体和残留奥氏体(a)、齿顶的碳化物(b) 和心部组织(c) ×500
图3为裂纹处组织,为淬火马氏体。齿根处组织是马氏体及残留奥氏体,3 级,为细针马氏体加 30%残留奥氏体,碳化物1 级,为细颗粒状碳化物,组织均满足要求。
为了更加清楚地观察裂纹处组织,对裂纹处进行组织检测。试样沿齿面并垂直于裂纹方向切割,尺寸为20 mm×20 mm×20 mm。
在磨齿过程中,局部进刀量过大,导致接触面温度急剧上升,组织奥氏体化,在冷却液的作用下表面产生淬火现象,硬度上升,此为工件经过渗碳淬火后,经历的第二次淬火,次表层由于得不到及时冷却,会在表层传来的递减的热量下被回火,硬度下降。
图4为裂纹经抛光后的形貌,图5为裂纹腐蚀后的形貌,从图中可以看到裂纹处出现白亮区,为淬火马氏体,判定为二次淬火组织。
图4 抛光后裂纹形貌 ×50
图5 浸蚀后裂纹形貌 ×50
观察裂纹处组织发现,组织有白亮色和暗黑色两个不同区域,采用显微硬度计对两区域的硬度进行检测,结果如图6所示。从图中可以看出黑色区域硬度值明显偏低,白亮区域硬度值为67.8 HRC 和暗黑色区域硬度值51.8 HRC。
图6 近裂纹处硬度不同的区域 ×500
硬度检测:对渗碳淬火后齿轮的硬度进行检测,所用设备为 HM-221 半自动显微硬度计,依据 GB/T 9450- 2005《钢件渗碳淬火硬化层深度的测定和校核》进行检测,结果如表4所示。从表中数据可以看出,渗碳淬火后齿轮的硬度满足技术要求(58~62 HRC)。
表4 失效齿轮不同部位的硬度/HRC
2、磨削裂纹的产生原因与预防措施
裂纹产生原因
根据上述所作检测可以得出:材料的化学成分 (见表1)及纯净度(见表2)满足要求,由此排除了锻件本身的质量问题。
工件渗碳淬火后,组织中存在的残留奥氏体过多、网状碳化物等,会导致磨削过程中产生裂纹。网状碳化物会使齿面硬度增大,在磨削过程中,砂轮与磨削面接触后造成磨削区温度迅速升高,易产生二次淬火,残留奥氏体转变为马氏体时易使磨削区内应力增大。对工件本体解剖后分析齿顶、节圆、齿根等处的显微组织(见表3),各处的组织均满足要求,排除网状碳化物及马氏体残奥超标造成开裂。
在磨削过程中,如果齿面硬度偏高,在砂轮与齿面接触的瞬间,磨削区的温度会迅速升高,可能出现局部过热现象,表层被二次淬火,次表层被回火,使显微组织发生变化,由于各组织的比容不同,在二次淬火后会在表面产生残余拉应力,一旦拉应力大于材料本身的抗拉强度,便会在齿面产生磨削裂纹。对齿顶、节圆、齿根等处使用显微硬度计由外至内硬度检测(见表4),工件的表面硬度以及硬度降均能满足要求。
由以上结果可以排除工件渗碳淬火质量不良产生磨削裂纹的可能。
工件磨削时,由于砂轮与工件之间的相对运动,必然导致工件表面温度的急剧升高,不同的温度梯度,导致的裂纹形态也不同。当工件表面温度达到 100 ℃时,因表面马氏体分解,使表面承受拉应力而开裂,裂纹形态与磨削方向垂直且相互平行。当温度达到300℃以上时,表面产生第二次收缩,使表面拉应力超过脆断抗力而出现龟裂现象(2),如图2所示。有时表面温度可能达到820~840 ℃或更高,如果冷却不充分,表面薄层重新奥氏体化,形成淬火马氏体,由组织应力和热应力导致出现磨削裂纹。
由图6结合表4裂纹处的硬度降可知,裂纹处的硬度降在第一点白亮区(64.3 HRC), 第二点黑色区(52.5 HRC)以及第五点正常区(60.3 HRC)呈开口向上的U 型曲线,与没有裂纹的正常区域的硬度降截然不同。
在磨削过程中齿面磨削区骤然受热,产生高温,表层小面积体积膨胀,组织奥氏体化,冷却液随之对其冷却,产生二次淬火,表面急剧收缩,硬度增高,次表层区域被回火,硬度降低。在表层冷却收缩的同时,由于冷却过慢,次表层仍处于膨胀状态,表面呈残余拉应力状态,随着磨削的进行,在齿面存在切向应力,由于次表层硬度降低,其抗拉强度随之降低,在残余拉应力与切向应力的作用下齿面出现裂纹。
综上所述,齿轮磨削裂纹是磨削工艺不当导致磨削过热所致。
预防措施
喷丸强化:喷丸强化是利用大量高速运动的丸粒冲击工件的表面,使工件表面受到挤压,发生冷塑性变形,形成表面压应力,这种压应力会抵消表面的一部分拉应力,从而有效降低了裂纹的产生机率。本厂风电产品要求强力喷丸,自装备强力喷丸机以来,风电产品未曾因磨削裂纹而报废。
热处理要求:对渗碳淬火工件,必须严格要求热处理工序,渗碳的最主要工艺参数是加热温度和保温时间,渗碳淬火温度经过多年实践已经没有太多变化,通过降低强渗扩散碳势,分别为1.20%~1.30%Cp→ 1.05%~1.15%Cp,0.80%~0.90%Cp→0.65%~0.75%Cp, 并适当延长扩散时间,此举既能保证工件表面硬度,同时降低表面碳含量及奥氏体含量,降低磨裂倾向。
渗碳淬火过程的畸变也是影响磨齿后裂纹的关键因素,如工件畸变较大,在磨齿分配余量时会出现在畸变较大区域进刀量大的现象,进刀量过大会造成局部过热,进而出现裂纹,因此必须严格控制,一般可以通过以下几种方式来控制淬火畸变量。
(1)碳钢和低合金钢淬火冷却到650 ℃之前,奥氏体还比较稳定,允许以较慢的速度冷却,以减少工件因内外温差而引起的热应力。在650~450 ℃ 范围,要求有足够的冷速(超过临界冷却速度),低于400℃特别在 Ms点以下缓慢冷却,以减少组织应力,防止过大的畸变和淬裂。根据以上理论设计如下方案:工件在淬火时,提高淬火油温度(≥90 ℃,经验所得),热油淬火,淬火油槽提前开始搅拌,使油温各处均匀,在工件入油时停止搅拌,入油一段时间(15~30 s, 经验所得)后再开始搅拌。
(2)设计淬火用工装。由于工件入油冷却过程中上下畸变不一致,为此,可以设计一套工装,在工件上下各放置一件,保证工件上下两端面的环境相同,畸变一致。本厂经过试验,效果已经稳定下来,以齿轮直径1~2 m, 齿宽≤0.15 m 的厚径比大于1:8的薄齿轮为例,渗碳淬火后上下端面的锥度绝对值控制在1 mm 以内,公法线锥变控制在0.3 mm 以内,根据后期磨齿反馈,未曾出现磨裂、齿面烧伤的现象。
磨削工艺:磨削裂纹产生的原因很多,但根本原因是磨削热,所以降低磨削热是解决磨削裂纹的关键。
首先,应采用湿磨法,利用冷却液来降低工件与砂轮在磨削点上的热量。
其次,选用合适的砂轮,砂轮的选择对磨削温度有重要影响,渗碳钢硬度高,砂粒易磨钝,为避免砂粒磨钝而产生磨削热,砂轮硬度应稍软一些,以便磨钝的砂粒及时脱落,减少与工件的摩擦力。同时在选用砂轮时,易选用砂粒较粗的,因为细砂轮容易被堵塞,磨削时产生热量较大,使工件表面容易出现烧伤及裂纹,砂粒粒度粗一些,冷却条件也可以改善,以减少工件的发热量。
再次,应严格控制磨削余量。若磨削余量留得过大,在高速磨削中会产生磨削热,从而导致磨削裂纹等多种缺陷的产生,因而应尽量减小磨削余量,在保证纠正工件畸变的前提下,余量越小越好,一方面可以降低成本,另一方面可以减小裂纹产生的可能性,保证淬硬层深度,提高齿轮承载能力。
最后,磨齿分配余量时应尽可能多分配,因为齿轮在热处理过程中必定会有一定的畸变,个别齿的余量相对会较大,若只分配几个齿则很难分配到最大余量处,那么在磨齿过程中有可能会因为余量大的齿面磨削量过大,而造成磨削裂纹。例如某齿轮在磨齿过程中共分配了7个齿,余量分配如表5所示。从表5 中可以看出,左齿面最大余量为 0.8200mm, 最小余量0.4455 mm, 最大量与最小量差值0.3745 mm。差值较大,且最大值不一定为整个齿轮上齿面的最大余量,可能会在磨削过程中造成部分齿面进刀量较大,局部磨削过热而产生裂纹。
表5 齿轮不同部位的磨削余量
3、结论
(1)齿轮化学成分检测结果表明,符合 20CrMnMo 钢材质要求,锻件纯净度合格。
(2)未受磨削影响的齿顶与齿根组织和硬度基本合格,节圆处表面硬度偏高,存在轻微的二次淬火白亮区,裂纹处存在严重的二次淬火白亮区,表面硬度偏高(67.8 HRC), 组织为淬火马氏体,次表层硬度骤降(51.8 HRC), 组织为回火马氏体,裂纹处的组织及硬度均出现异常情况。
(3)齿轮磨削裂纹是磨削工艺不当导致磨削过热所致。
(4)可以通过改善磨削工艺、提高热处理质量及采用喷丸等方法降低磨削裂纹的产生几率。
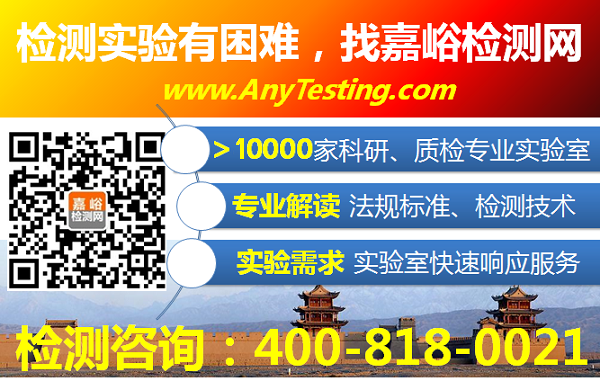