1、测试背景
客户汽车在行驶2万公里后发生故障,经检查发现驱动轴断裂,断裂位置为卡簧槽台阶处。客户送检失效样品进行检测分析,以期找出失效原因。
驱动轴材质为cf53,表面处理为中频淬火处理。
样品示意图
2、测试内容、设备及方法
测试环境:(23±5)℃,(40~80)%RH
3、测试结果
3.1断口宏观观察
小结:对驱动轴断裂位置进行宏观观察发现,断裂起始于卡簧槽台阶处,无明显塑性变形,台阶处无明显的R角,且侧壁可观察到明显刀纹;断面平齐,与轴线接近垂直,磨损较严重,裂纹源位置可观察到发散状条纹,芯部为最终断裂区。
3.2断口SEM形貌观察
小结:裂纹源A位置磨损较严重,断面凹陷处存在许多碎屑,边缘处可观察到两个缺口;边缘区域(B位置)可观察到呈冰糖状的晶粒,为沿晶脆性断裂;靠近边缘的C位置可观察到扇形解理与河流花样,为解理断裂;芯部区域(D位置)可观察到许多细小的韧窝,为韧性断裂。
3.3低倍组织观察
小结:从低倍组织照片可以看出,驱动轴组织分为淬硬层、过渡区、芯部与中心区四个区域;通过低倍组织测量,其淬硬层深度约为3.5mm。
3.4淬硬层深度测量
小结:参照GB/T 9450-2005,测试驱动轴的淬硬层深度约为3.5mm,与低倍组织中测量结果一致,且符合2.5~5.0mm的规格要求。
3.5夹杂物与金相组织观察
小结:
1. 纵截面切片可观察到较多长条状硫化物夹杂与少量球状氧化物夹杂,参照GB/T 10561-2005,采用A法进行夹杂物评级为A2,D0.5。
2. 驱动轴淬硬层组织为板条马氏体;过渡区组织为珠光体(部分为细片状索氏体)+少量铁素体;从芯部组织可以看出,驱动轴存在带状偏析,组织为珠光体+沿原奥氏体晶界呈网状分布的铁素体;中心区为粒状与片层状珠光体。
3.6化学成分分析
小结:以上所给成分均为质量百分比;参照客户提供的成分规格,驱动轴的化学成分符合cf53的规格要求。
3.7硬度测量
小结:以上所给硬度值均为3点测量结果之平均值;参照客户提供的技术要求,驱动轴的表面硬度与芯部硬度均符合规格要求。
4、测试结论及建议
结论:
综合以上测试分析,驱动轴卡簧槽无R角,且存在缺口缺陷,易造成应力集中,产生裂纹;驱动轴的芯部存在带状偏析,组织为珠光体+网状分布的铁素体,在一定程度上会影响驱动轴力学性能,降低驱动轴的使用寿命。
建议:
1. 卡簧槽台阶位置增加R角设计;
2. 改善加工工艺,避免加工缺陷(缺口、刀纹)的出现;
3. 改善热处理工艺,中频淬火前增加调质处理,改善组织偏析,提高轴的综合力学性能。
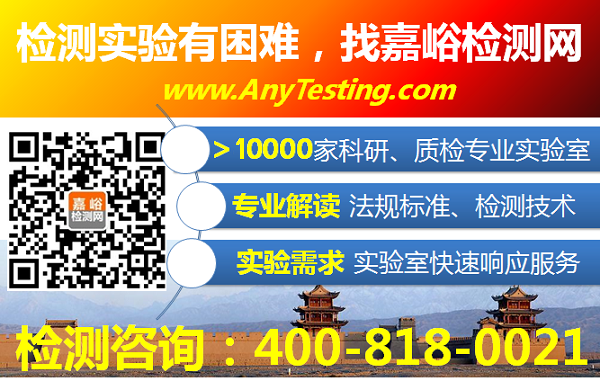