海洋资源的开发利用是解决能源问题的重要途径之一。海洋资源的勘探和开发离不开海洋工程装备。钛合金是一种具有优异耐海水腐蚀性能的结构材料,具有无磁性、无冷脆性,是非常理想的海洋装备制造材料,可解决深海装备普遍存在的浮力储备不足、结构安全可靠性欠佳等问题,可以很好地满足海洋工程应用的要求。然而,由于舰船用钛合金的服役工况较为复杂,在服役过程中不可避免地产生局部腐蚀、轻微划伤等表面缺陷。大量的研究和试验结果表明,钛合金表面质量和缺口会大大降低其使用性能。打磨态钛合金的板材表面存在大量微划痕,轻微的外物撞击可能会使其出现表面局部损伤,严重的会产生缺口,而缺口会改变构件在载荷下的应力分布。材料服役时,其缺口处易产生应力集中,导致裂纹过早萌生,最终缩短其使用寿命,给装备的服役带来极大的安全隐患。此外,实验室加工标准试样的表面状态要优于构件的实际状态,由标准试样测试出的材料性能与服役状态下的材料性能会有一定差距。钛合金的表面状态对其在深海高压环境下的力学行为有重要影响,目前已有很多学者研究了钛合金表面质量,如缺口、粗糙度对其静态拉伸性能及疲劳性能的影响。田伟等研究了不同缺口对TC17钛合金拉伸性能和低周疲劳性能的影响,应力集中系数越高,抗拉强度越高,但是疲劳寿命会在应力集中系数大于1.92时急剧下降。用弯曲力学性能评价表面敏感性的研究却少有报道。横向弯曲是一种较为常见的承载模式,弯曲力学性能是衡量设备安全可靠性的重要因素,尤其对于深海用装备结构材料,其服役过程中部分部位的承力甚至超过材料的屈服强度,失效模式多种多样,目前对于弯曲载荷下钛合金表面状态对材料强度、局部塑性变形行为的影响尚不明确。因此,研究表面状态对钛合金弯曲力学性能的影响对钛合金在深海装备主结构上的应用安全性具有重要意义。
针对Ti80合金板材的打磨划痕、缺口等表面缺陷,研究人员利用数字图像相关(DIC)方法研究了Ti80合金表面质量及缺口对其弯曲力学行为、局部变形行为的影响,并结合扫描电镜(SEM)以及电子背散射衍射技术(EBSD)分析该类表面缺陷在Ti80合金局部变形过程中的作用机制,为其在深海环境下的安全应用提供支持。
1、 试验材料与方法
试验材料为Ti80板材,显微组织为等轴α和板条α的双态组织(见图1)。为了分析不同表面状态对其力学性能的影响,设计了1#光滑表面抛光试样、2#原始表面试样以及3种缺口试样,试样厚度均为8mm,3#试样缺口深度为0.1mm,缺口曲率半径为0.1mm,4# 试样缺口深度为1mm,缺口曲率半径为0.05mm,5#试样缺口深度为1mm,缺口曲率半径为0.25mm,缺口试样结构如图2所示,缺口试样尺寸如图3所示。对5种类型试样进行三点抗弯强度测试,每种试样取2个。试验前在试样表面喷制随机分布的散斑标点,采用视频引伸计测量试样表面应变,可实现与试验设备同步采集数据。参考 YB/T 5349—2014 《金属材料 弯曲力学性能试验方法》进行三点弯曲试验,支点跨距为40mm,压辊直径为10mm,支辊直径为4mm,试验速率为2mm/min。试样断裂后,利用双束扫描电子显微镜对试样断裂侧面进行观察。
2、 试验结果与分析
2.1不同缺口试样的应力集中系数
利用有限元软件对缺口试样进行应力集中系数分析计算。首先,在软件中建立不同缺口尺寸的试样模型,定义材料为各向同性,弹性模量为116GPa,泊松比为0.3,采用Mises屈服准则,网格划分部分采用六面体网格,考虑到缺口处的应力集中,对缺口处网格进行了细化,单元类型为8节点的二次单元,模型一端固定,另一端施加弯矩,取远离缺口处截面为基准面,提交后得到3#,4#,5#试样的应力集中系数分别为2.70,7.90,4.26。
2.2不同表面状态对试样弯曲力学性能的影响
1#~5#试样的室温弯曲试验结果如表1所示。
图4为1#~5#试样的弯曲应力-应变曲线,由图4可知:原始表面及带缺口试样的抗弯强度均略低于光滑试样,没有明显的缺口强化效应。计算不同表面状态试样抗弯强度与光滑试样抗弯强度的比值,以进行试样表面敏感度判定,其中2#,3#,4#,5# 试样对1#试样的表面敏感度分别为0.94,0.94,0.97,0.97,说明对 Ti80材料来说,缺口对材料的脆化效应大于缺口处的三向应力状态产生的缺口强化效应,缺口尺寸对试样的抗弯强度影响较小,而断裂应变随着缺口尺寸的增加迅速下降,试样塑性变形能力较差。
表面打磨及缺口会导致试样的断裂应变显著降低,1#表面抛光试样的断裂应变最大,塑性最好,2#原始表面试样虽无缺口,但断裂应变相较于1# 试样下降52%,说明断裂应变对表面状态十分敏感。
2.3弯曲过程中的局部变形行为
DIC测量下压量为1mm时1#~5# 试样的应变云图如图5所示,由图5可知,应变均集中在试样下表面与压辊同轴的位置,其余大部分区域的应变都很小,1#,2#和3#试样的应变分布区域较大,而4#,5#缺口试样的应变主要集中在缺口附近。1#~5#试样下表面中心沿厚度方向的应变分布如图6所示,由图6可知:1#,2#和3#试样的应变分布比较接近,表明表面状态对试样应力、应变分布的影响较小;在弹性阶段,1#,2#和3#试样并无明显差别,4#,5#试样的应变明显大于1#,2#和3#试样,并且下降的趋势更明显,表明缺口处承受了更大的载荷,离缺口越近,应力集中现象越明显。
图7为断裂前1#~5#试样的应变云图,1#试样破坏时的应变最大,弯曲挠度也最大,塑性最好,随着表面缺口处应力集中的增加,弯曲挠度逐渐减小,试样破坏时的应变更加集中,试样下表面中心沿厚度方向的应变分布如图8所示,随着表面质量的下降及缺口尺寸的增加,试样的塑性变形区也减小。随着缺口深度的增加,试样的破坏应变进一步减小,但4#和5#试样较为接近,这说明当缺口未达到断裂阈值时,仍可通过塑性变形把应力集中在一定区域内并释放。3#试样的应变区域相较于4#,5#试样更大,说明该种类型的缺口虽造成了应力集中,但束缚相对较小,加载过程中能够用更大的塑性变形区域缓解局部应力集中,从而延迟断裂。通过断裂前的应变分布可以发现,随着应力集中系数的增大,应变集中区域的面积显著减小,这是因为钛合金应变强化能力较弱,缺口产生应力集中时,应变强化影响的范围小,塑性变形集中,导致钛合金对缺口更为敏感。
2.4断口分析
图9为1#~5#试样起裂位置附近断口的SEM形貌,试样断口特征主要为韧窝,在3#,4#,5#试样中观察到二次裂纹。不同表面状态试样的断裂形式均为微孔聚集断裂,表明虽然引入了缺口,存在应力集中,但缺口处仍然发生塑性变形,表现为延性断裂。
图10为1#~5#试样断口侧面的显微组织形貌,晶粒经历过变形,产生一些碎化,1#,2#和3#试样碎化较轻微,4#和5#试样晶粒碎化更严重,并且在1#试样中观察到一些孪晶。根据统计,1#~5#试样中均存在大量的2°~5°的小角度晶界,晶界数量随表面质量的下降及缺口尺寸的增加呈下降趋势,小角度晶界的数量越多,试样变形越严重。
3、 结论
(1)表面抛光试样的抗弯强度最大,表面打磨及缺口试样的抗弯强度略有降低,表明钛合金应变强化能力较弱,没有明显的缺口强化效应,缺口尺寸对试样的抗弯强度影响较小,即抗弯强度对缺口不敏感。断裂应变随着表面质量的下降及缺口尺寸的增加迅速减小,缺口产生应力集中时,应变强化影响的范围小,塑性变形集中,导致钛合金塑性对其表面状态十分敏感。
(2)利用DIC分析了不同表面状态试样的变形情况,应力集中程度越大的试样,变形区域越小,断裂前的应变也越小,表明材料容易断裂。
(3)断口分析结果表明:Ti80合金主要断裂形式为韧窝断裂,并存在大量的小角度晶界,晶界数量随表面质量的下降及缺口尺寸的增加呈下降趋势。
作者:高琛,徐魁龙,王磊,蔡海琛
单位:中国船舶集团有限公司第七二五研究所
来源:《理化检验-物理分册》2023年第8期
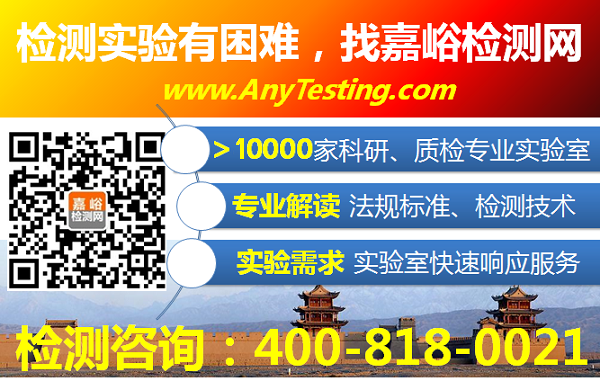