摘要:为了解决成熟生产线车身水性珠光色漆在量产初期出现气泡的问题,从设备、工艺条件、材料3个方面进行测试验证并分析产生气泡的原因。测试发现,通过降低机器人喷涂流量和旋杯转速、提高色漆闪干温度、降低烘烤温度、色漆中添加1% H-7消泡剂均可有效减少面漆漆膜中气泡的数量。根据以上测试结果,制定了可实施的方案,有效解决了气泡问题,为以后生产及其他主机厂再次出现此类质量问题提供了调查方法和解决方案。
关键词:面漆;气泡;喷涂参数;烘烤温度;消泡剂
汽车车身在涂装过程中,受到设备、工艺、人员、材料和环境等因素的制约,会出现各种涂膜缺陷。涂膜气泡是涂装中常见的一种涂膜缺陷,出现气泡的原因很多,例如:反应生成的气泡未烘干充分逸出,再加热时涂膜内气泡受热顶出;搅拌原漆产生的气泡在喷涂过程中未消除;环境湿度较大导致水分难以挥发形成气泡,车身涂装过程中被汗液、灰尘等污染。虽然可以通过打磨、抛光、修补等方法进行一定程度的解决,但是这不仅造成了生产工时和材料的浪费,降低了生产效率,同时影响了涂膜的外观质量,对涂膜的整体性及防护性能具有一定程度的影响,因此消除气泡不良影响具有重要的意义。本文就本公司某生产线汽车车身涂装过程中某珠光漆量产初期出现的气泡问题展开调查,从设备、工艺条件、材料3个方面进行测试验证并分析产生气泡的原因,结合生产线实际制定可行对策,为此类问题提供解决思路和方案。
一、现状调查
该生产线采用的传统3C2B工艺,具体工艺流程为: 前处理一电泳 (烘烤)-密封胶 (烘烤) 水性中涂(烘烤) 水性色漆 (闪干) 溶剂型清漆 (烘烤),色漆和清漆主要工艺参数见表1。此生产线已有近20年的生产历史,现行的工艺已经固化且相对稳定。在某珠光色投产初期 (所用色漆为湖南关西生产) ,车身大面积出现气泡。首先观察气泡的状态发现气泡均为颗粒状凸起,显微镜放大500倍观察到气泡为圆球状、内核无杂质,如图1所示。
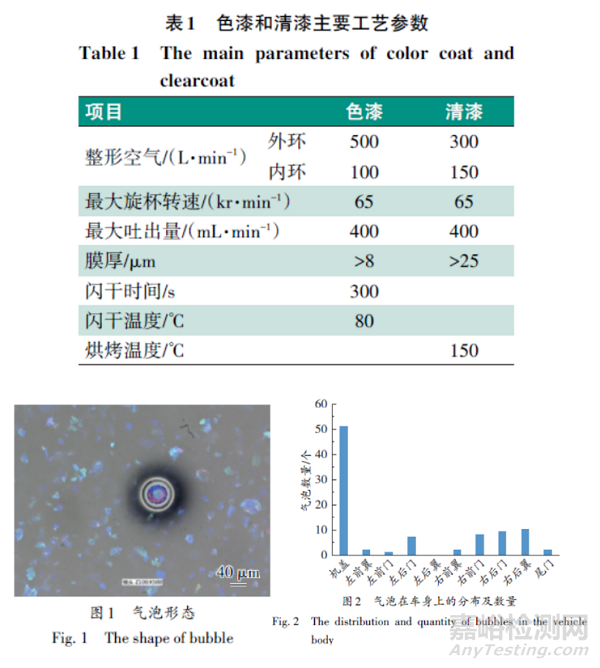
然后统计气泡发生的部位和数量 (如图2),发现气泡分布不固定,整车垂直面和水平面都可能出现,但水平面的气泡数量明显高于垂直面。为了快速确认气泡所在涂层,对气泡部位进行轻打磨并用显微镜逐层观察确认,发现对清漆层轻打磨之后气泡消失,打磨部位色漆层珠光排列与周围珠光排列无差异,且未漏出深色底涂颜色,可以由此推断气泡处于色漆层之上。确认珠光水性色漆的基础喷涂参数,喷房湿度为(75士5)%,温度为 (25士2)C,风速为0.3~04 m/s,色漆膜厚8~12 um,中涂膜厚30 um,清漆膜厚35 um,清漆烘烤时间20 min。为了尽快消除气泡对生产开动率的影响,在保证中涂和清漆膜厚不变的情况下,从色漆喷涂机器人参数设定、闪干炉和烘烤炉条件、涂料消泡性能这3个方向展开相关测试并分析原因,寻求消除气泡的最佳方案。
二、原因分析
2.1 设备参数
在静电喷涂中,喷涂流量、旋杯转速、成型空气、高电压等参数对涂膜的状态和涂膜质量都会产生一定的影响。由于成型空气会对喷幅、涂膜的叠加次数产生影响,高电压主要影响静电喷涂的静电效应、上漆率、涂膜的均匀性等,这些工艺参数在机器人导入初期就已经固化,考虑到生产线其他量产颜色的品质稳定性,这里暂不考虑调整成型空气和高电压参数的调整及影响,仅确认喷涂流量和旋杯转速对气泡的影响。另外,由于喷涂流量和旋杯转速会影响涂膜颜色,这里确认气泡消除的同时需要考虑参数调整对颜色的影响,此珠光漆的颜色标准值和色差管理基准如表2所示。
2.1.1 喷涂流量
喷涂流量决定涂膜厚度,同时影响涂膜干湿度,进而影响颜色。根据该珠光漆设计方案及性能要求,膜厚要大于8 um。采用单因素实验设计,控制旋杯转速为35 kr/min,设定不同喷涂流量研究其对清漆层气泡的影响,结果见表3。测试板采用A4大小与车身同材质及喷涂工艺的钢板制成,水平面和垂直面各4块钉在测试车身上,按下述喷涂流量进行喷涂,然后统计水平面和垂直面测试板上气泡数量。
从表3可以看出,增大喷涂流量,色漆厚度随之增大,颜色相对比较稳定,但是水平面产生的气泡数量明显增多,垂直面的气泡数量略增多。说明喷涂流量越大越易产生气泡,在颜色不受影响的情况下,需要尽量降低色漆膜厚。初步分析原因,随膜厚增加,涂膜中溶剂和水分、气泡逸出的时间变长,从而导致气泡的产生。
2.1.2 旋杯转速
旋杯转速主要影响涂料雾化效果、涂膜干湿度、涂料中珠光的排列方式,同时对涂膜颜色产生影响。控制色漆膜厚为10 um,通过设定不同旋杯转速,确认气泡改善情况和色差,结果见表4。
从表4可以看出,随着旋杯转速的降低,水平面气泡数量略有减少,垂直板的正视明度、色相会略微降低,颜色整体影响不大。初步分析原因:随着转速的降低,涂料雾化变差,但是同时涂装固体分 (NV) 降低,溶剂挥发减少,留在湿膜内的溶剂增加,水分、气泡随着溶剂逸出的机会增加,产生的气泡就相应减少。
2.2 烘烤条件
水性面漆需要合适的闪干条件和烘烤条件确保涂膜内水分和溶剂均匀挥发以达到外观、品质要求,闪干炉和清漆烤炉脱水都是通过热风循环实现的,主要包括时间、温度和风速3个要素,这里闪干炉和烤炉长度和链速是不可改变条件,风速调整会影响整个烤炉内风速平衡所以也暂不做调整。控制色漆80为10 um,闪干时间5min,烘烤时间20 min,设定不同闪干和烘烤温度确认温度对气泡影响,结果见表5。
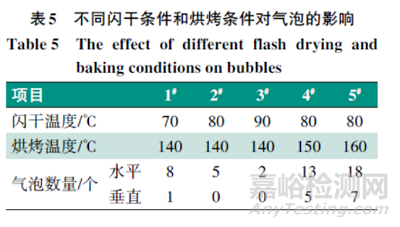
从表5可以看出,提高闪干温度对减少气泡有较好的效果,且随着闪干温度升高气泡数减少,90C时气泡改善效果最佳。在闪干温度不变的条件下,烘烤温度越高,产生的气泡数量越多。原因分析: 随闪干温度升高,涂膜表干后其中的水分也随之减少,最后通过烘烤产生的气体也随之减少,气泡数量降低;而当闪干温度不变,烘烤温度升高,表层清漆快速升温,成膜速率提高,微观缝隙急剧减少,涂膜内部的溶剂和其他气体向外层顶出但未顶破清漆层,便形成气泡。
2.3 涂料消泡性能
在色漆中添加1%不同种类消泡剂,控制色漆膜厚为8um,按照上述最优工艺条件喷涂A4测试板,即喷涂流量240 mL/min,旋杯转速20 kr/min,闪干温度90°C,烘烤温度140C,测试结果见表6。
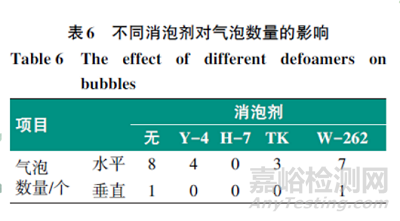
由表6可知,H-7的消泡效果最好,而Y-4、TK、W262对气泡消除有一定作用,但无法完全消除气泡。分析原因:消泡剂是一种表面活性剂,添加一定量的消泡剂可以改善涂料的表面张力、成膜过程中湿膜的表面张力梯度和湿膜表层的表面张力均匀化能力。同时,助剂的添加会对涂料溶剂挥发、溶解性能、流平性等其他性能产生影响,因此需要同时确认添加后涂料黏度 (福特4号黏度杯)、pH、干膜外观、颜色及抗针孔、流挂性等作业性和生产适应性能。添加H-7类型消泡剂后性能确认结果如表7所示,各项性能基本无劣化影响。
三、对策拟定及效果确认
通过以上测试结果可知,产生气泡是由设备参数、烘烤温度和材料本身施工范围窄等多重不利因素共同造成的,调整设备参数可在一定程度上消除气泡,闪干、调整烘烤温度、添加一定量消泡剂可有效消除气泡。由于涂料本身的施工范围调整及对性能的影响需要一定的验证周期,为保证量产顺利进行,制定了临时对策和恒久对策。临时对策: (1) 在满足遮盖力和颜色要求的前提下,适当降低整车车身膜厚;(2) 将产生气泡部位闪干炉出风口温度由80°C调整为90c; (3) 将烤炉升温段的温度由150°C调整为140°C。恒久对策: 涂料添加1% H-7消泡剂后确认其黏度、储存稳定性和管道循环稳定性是否变化,确认涂膜耐针孔、抗流挂性、耐水性、耐湿性、耐盐雾性等性能是否符合标准,没有问题再进行生产现场适用。效果确认:通过调整喷涂膜厚、闪干温度和烘烤温度,气泡的发生率大大降低 (<5个/台)。添加消泡剂并作相应调整后,气泡发生率降为0。
四、结 语
本文因涂装制造现场工艺条件的局限性,从机、法、料3个方向出发,研究设备参数、施工工艺参数和涂料消泡性能对气泡的影响。 (1) 在保证色差的情况下,尽量使用较小的喷涂流量,降低色漆膜厚,可以有效减少气泡产生的几率; (2) 涂装机器人旋杯转速对气泡数量有一定的影响,但由于其对颜色影响较大且不是产生气泡的根本原因,可作参考改善方法; (3) 适当提高闪干温度、降低烘烤温度有利于消除气泡; (4) 在涂料中添加一定比例的消泡剂,对消除气泡有一定的效果,但需同时考虑其对涂料黏度、涂膜颜色外观、流平性等的影响。由于产生气泡的原因较为复杂,应根据现场实际情况,从人员操作设备、材料、工艺参数、环境等多方面综合考虑,寻找利于改善气泡弊病的最佳方法和工艺条件。
刘双,朱虎义,陈双桂,等. 水性色漆气泡原因分析及解决方案探讨[J]. 涂料工业,2023,53(7):78-82.
LIU S,ZHU H Y,CHEN S G,et al. Cause analysis and solution of the bubble in waterborne top coat[J]. Paint & Coatings Industry,2023,53(7):78-82.
DOI:10. 12020/j. issn. 0253-4312. 2023-040