1、前言
目前我国汽车生产总量逐年增加,同时保持多年全球汽车销量第一。汽车的需求量增加直接导致汽车产量和报废车数量的增加,间接对汽车生产工艺、环境、能源、材料方面都带来了巨大挑战[1,2]。
汽车车身质量在整个汽车的总质量中占比约40%~50%。从汽车外形来看,汽车的车身在面积上基本覆盖了整个汽车[3]。因为汽车车身无论是在质量方面还是在汽车覆盖面积方面都分别占据了整个汽车质量和面积的绝大部分。所以在汽车研发过程对车身的研发会需要很多投入,而车身生产过程中也会耗费大量能源,因此在汽车车身生产技术的传承的基础上,车身技术发展需要加快新技术突破[4]。
2、车身覆盖件发展现状
目前看来,国内外对车身覆盖件的关注情况还是热度不减,主要集中在以下5个方面,如图1所示。其中,轻量化是多种发展方向共同追求的目的。文章围绕发动机罩盖、行李箱盖以及车门的外形、连接技术、材料进行现状概述,着重对冲压和压铸工艺进行概述和未来发展趋势研究。
2.1覆盖件外形
汽车车身覆盖件是汽车与空气接触面积最大的部分,车身覆盖件的设计让汽车外形更加贴合汽车空气动力学,让汽车外形更具有科技感,同时迎合大众审美。陈承杰等[5]设计了一种类似孔雀开屏的汽车尾翼,通过CFD模拟验证了该尾翼在汽车行驶过程中产生下压力的效果,做出了性能评价。张震等[6]通过对现有跑车外形进行三维建模和对模型进行空气动力学仿真,通过局部优化达到了降低空气阻力的目的。Alessandro Ferraris等[7]通过设定位于汽车轮罩的空气流量控制装置,通过风洞试验的方式对城市客车空气动力学进行改进优化。在空气动力学方面,主要通过优化汽车覆盖件外形、增加尾翼、局部增加装置调整空气阻力、隐藏式门把手、电子后视镜的方式优化汽车空气动力学。
汽车覆盖件中发动机罩盖和尾厢盖板外形发展来看,最初的发动机罩盖和行李箱盖属于方正外形,如来自1930年的雪铁龙Traction Avant宣传海报上的雪铁龙Traction汽车的发动机罩盖,如图2a所示。雪铁龙C6车型,如图2b所示。雪铁龙C6汽车发动机罩盖在外形上更符合汽车空气动力学,设计趋向低趴、扁平和过渡光顺。
在满足结构和功能性的前提下,提升对汽车外形审美的设计水平。以轿车为列,如国内某自主汽车厂商的2012款车型到2022款新车型,在发动机罩盖和行李箱盖方面都有呈现向过渡光顺、低趴式的趋势发展,车型上溜背汽车外形更加突出和采用了开口空间更大的掀背式尾门,通过边缘检测,如图3所示[9,10,11]。
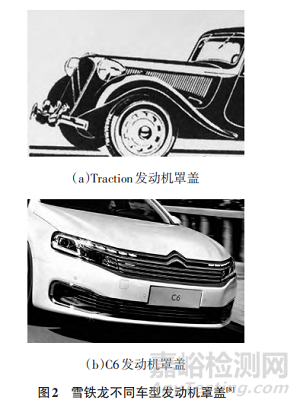
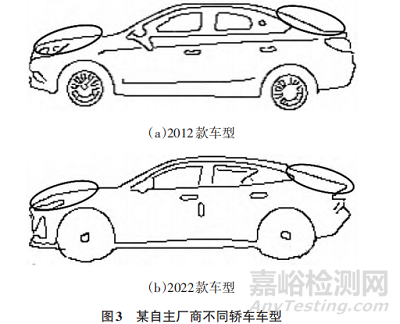
此外,科技感也很重要,部分车辆外形部件增加科技感,比如带显示功能的车灯、隐藏式后视镜等。
2.2轻量化
在2016年10月中国汽车工程学会年会上发布的《节能与新能源汽车技术路线图》中显示,到2030年要大幅度增加高强度钢应用,单车用铝合金超过350 kg,碳纤维超过总质量的5%,此次会议上展示了轻量化技术,预计从2015年到2030年,实现从18%到40%的减重目标。在2020年修订的《节能与新能源汽车技术路线图2.0》中,轻量化被列为九大技术方向之一,预计2035年燃油乘用车整车轻量化系数降低25%,纯电动乘用车整车轻量化系数降低35%[12]。
车身轻量化通过降低车身的质量达到降低能源消耗和降低产生污染物的目的,轻量化研究方向主要围绕轻质材料、结构优化、制造技术、铝合金和高强度钢以及塑料应用进行展开[13]。王童等[14]通过建立城市客车车身模型,对其进行多工况分析以及多方向结构优化达到轻量化的目的。韦学军等[15]基于碰撞角度,从碰撞结果对车身结构进行轻量化结构优化,这样既得到了安全性,又达到了轻量化目的。高丰岭等[16]通过将碳纤维复合材料应用到汽车车身,达到了降低车身质量的目的。Martin Ivanjko通过使用新型高强韧钢材(Twinning Induced Plasticity Steel,TWIP),同时应用新型连接钉进行连接,二者共同配合达到降低了车身质量的目的[17]。采用全铝车身相对于钢材可以达到减重40%以上。轻质材料的制造工艺研究和轻质材料典型部件的系列化、标准化和研究相关轻量化指数都可以作为研究的方向[18]。
2.3冲压及压铸技术
车身覆盖件多数由内外板组成,外板通常为A面,对表面质量要求高,目前由于冲压技术的相对成熟、冲压设备的完善和模具生产设备的完善,所以车身覆盖件成形工艺最多的仍然是冲压成形。为了优化冲压产品的减薄率情况以及表面起皱情况,主要集中在对冲压成形工艺参数、回弹方面进行研究。王康康等[19]将正交试验和神经网络引入汽车行李箱盖冲压成形过程中,神经网络对冲压参数进行学习和遗传算法优化,获得了提高冲压成形产品质量的多参数组合结果。曹琳琳等[20]针对U形较薄产品进行冲压成形回弹控制,确定了影响回弹的主要因素,同时对这些因素进行控制,最终降低了回弹。冲压仿真过程主要还是集中在对压边力、摩擦系数、冲压速度、冲压深度和拉延筋布局方面的调整,通过正交试验和神经网络优化算法以达到降低起皱和优化减薄率的目的。
压铸技术出现约在19世纪20年代,因为其本身可以直接避免冲压过程中遇到的起皱、R角、负角和模具出现互相干涉的问题,所以对压铸的研究也是在逐渐深入。因为压铸主要研究方向集中在优化压铸产品的成形内部质量和表面质量,所以主要研究压铸的工艺参数、压铸流道、模具和冷却。
如今特斯拉公司和沃尔沃汽车公司开始将其压铸技术引入国内,在国内建立大型压铸车间,用于生产汽车零部件,并且有意愿应用于一体式汽车车身生产[21]。Kurtulus等[22]通过建模和设定随形冷却的模具结构,获取到了更加均匀分布的模具表面温度,相对降低了冷却时间,获得了拥有更好质量的成形产品。牛志超等[23]将高压压铸应用于薄壁件进行了可铸造性、缺陷和力学性能方面的研究,得到了产品屈服强度和延伸率二者与浇道远近的位置关系,并且得到了大型薄壁件压铸产品容易在力学性能不均匀性方面出现问题的结论。总体而言,本文在车身覆盖件成形技术方面分析结构图如图4所示。
2.4连接技术
汽车车身目前还是采用多零件拼接而成,因此需要较好的连接工艺。提升连接工艺的技术手段也可以达到轻量化的目的、降低材料成本、人力成本和时间成本。
目前,汽车车身连接主要采用焊接、铆接、粘接方式进行连接,同时采用多种焊接结合的方式,在最新一代的奥迪A8全铝汽车上应用了14种焊接技术,其中包括激光焊等8种热连接技术和冲铆连接等6种冷连接技术。
车身焊接主要包含电阻焊、电弧焊、激光焊接等。电阻焊通过局部电流产生电阻热的方式将局部工件熔化,熔化的部位进行熔化焊接,具有焊接质量好和焊接速度快的优点。电弧焊通过电焊丝与部件之间的电弧作为热源进行焊接,并且同时需要一定的保护气体,比如二氧化碳。激光焊接是一种较新的焊接技术,利用激光束作为热源进行焊接。因为其焊接质量好、耗时短、节省材料、焊接件不易变形的优势被广泛使用于汽车车身焊接[24]。
焊接也会对产品造成一定的质量影响,因此对焊接也进行一定的技术优化。赵建姣等[25]将激光飞行焊接技术应用到白车身车门,飞行焊接指的是激光焊头通过CAN总线的方式与机器人通讯,实现激光飞行焊接的功能。通过试验证明了飞行激光焊接的可行性,也获取了相应的影响参数,为此技术的发展提供了优化方向。
铆接比焊接在车身上的应用较少,主要有自穿钉铆接、无铆钉自穿铆接和压力穿刺铆。目前中国重汽集团将螺母冲铆工艺应用到汽车白车身连接工艺中,验证了此工艺装配精度高、工件变形小、节能环保、易于实现自动化目的。
粘接车身技术是用结构胶粘实现车身粘接。结构胶指强度高、能承受较大荷载,且耐老化、耐疲劳、耐腐蚀,并在预期寿命内性能稳定、适用于承受大载荷结构件粘接的胶粘剂[26]。张士展等[27]对车身结构胶性能进行了仿真,通过多种试验对结构胶失效进行模拟验证。结构胶常常用于车上的塑料件粘接,在车身连接制造技术上的应用仍处于探索阶段。
2.5材料
汽车车身使用材料以钢材、有色金属铝材料、非金属为主要使用材料,汽车车身用主要材料分类如下表1。
车身材料从最初的铁质材料,已经发展到铝质材料和合金材料。研究汽车车身材料主要为了提高车身的力学性能以及降低车身质量[29]。汽车车身材料主要为钢、常规合金、工程塑料和复合材料。现阶段车身使用量最大的材料是钢板,并且针对车身不同部件采用不同的钢板。对车身面部件采用延伸性、耐腐蚀、抗凹陷性都较好的钢材,对结构件采用吸能性好、同时还具有一定刚性、耐腐蚀好的材料,将这些构件良好地组合在一起可以达到轻量化和提升力学性能的效果。
有色金属中的铝合金最大的优点就是密度低,能够大幅度降低车身质量,同时在结构布局合理的前提下,还能满足一定的力学性能,相对钢制产品还会具有更好的吸能性能。铝合金车身在目前应用于全铝车身车型,比如特斯拉Model S、路虎揽胜、ES8,凯迪拉克CT6则采用钢和铝合金混合车身,如宝马6系发动机罩盖等开闭合件为铝,其余结构为钢材。刘雅芳等[30]将代号为6082的铝合金材料应用于车门,通过碰撞分析软件对其模型进行碰撞受力分析,最终达到了降低产品质量的目的,符合国家标准,比原钢制产品具有更好的吸能效果。
当前汽车车身覆盖件已经采用了部分塑料件,比如保险杠、前挡板、门板框等。工程塑料因其具有质量轻、耐腐蚀、耐热和耐寒、可塑性强的优势,所以考虑将其使用在汽车车身,目的主要是为了汽车轻量化[31]。工程塑料在解决成本问题之后,在轻量化方面明显优于现有车身材料。现阶段国外通用汽车已经研发出适合车身板料的工程塑料。沃尔沃汽车一直坚持环保,曾宣称2025年再生塑料在汽车上应用将达到25%。2018年在哥德堡举行的沃尔沃环球帆船赛中,演示的汽车中包含170个组件,由总计60 kg的再生塑料制成[32]。
复合材料种类繁多,车身上使用的复合材料主要是指的是碳纤维复合材料,碳纤维具有轻量化、强度高的优点。碳纤维材料现在最大的难点就是成本问题,需要在碳纤维材料的生产技术方面加大研究力度。徐作文等[33]将碳纤维复合材料应用到汽车车门,对碳纤维材料进行了层次化结构设计与铺层,对模型进行力学性能仿真,验证了刚度、强度方面的提升效果,达到了轻量化目标。
3、成形技术
车身覆盖件成形工艺是降低生产节拍、减少人工成本、减少原材料浪费、减少模具使用套数、提高产品质量和实现轻量化目标的关键技术之一。
虽然冲压技术比较成熟,但是冲压技术存在工序繁琐、模具套数较多、材料利用率相对不够高的缺点[34]。冲压技术围绕研究压边力、摩擦因数、冲压速度相关工艺参数,采用正交试验或者传统神经网络结合的遗传算法以及其它多目标优化算法,获取工艺参数之间的最优组合来达到优化产品质量的目的。冲压过程不仅涉及提升产品质量,同时应该从模具方面入手,对模具成本进行控制,可采用拓扑优化手段对模具进行轻量化优化,研究低成本模具材料,可将部分强度较高的塑料引入制造受力较小的模具。
从压铸工艺来看,压铸可以避免工序复杂和模具套数较多和材料利用率低的问题。压铸技术在尺寸参数方面对压铸对象要求高,所以对于薄壁件而言,压铸应用还是相对较少的。压铸技术目前还是多应用于强度要求较高的汽车部件,压铸技术在大型薄壁部件内部质量控制和模具制造技术方面还需要加大研发力度。在压铸工艺参数优化方面与冲压技术类似,通过优化技术对压铸温度、压射速度、模具温度的参数进行组合优化。压铸技术可以与合金材料结合,包含铝合金、镁合金、钛合金和这些合金的半固态材料,研究提升压铸合金的流动性能、力学性能是提高压铸产品质量的关键。
连续变截面板(Tailor Rolled Blank,TRB)技术在生产车辆框架结构A柱、B柱和纵梁的成形有显著成效,能够让这些部位工件的力学性质在成形后能得到均匀分布。目前,部分车商已经开始将TRB应用于汽车车身生产,如图5所示。奥迪新Q5的车底纵梁、A柱、B柱都由TRB热成形钢材制成,在保证部件强度的同时减轻部件质量。
当前,车身覆盖件这样较大、较薄(厚度小于1 mm)部件以及对表面要求较高的部件采用冲压技术为主,比如车门外板、发动机罩盖和行李箱盖外板这样的A面产品等。厚度相对较厚(厚度大于1 mm)、对表面质量要求不高的B面和C面部件、结构相对复杂的部件可以采用压铸成形,比如车身内部的加强件。压铸技术本身在模具方面相对冲压模具数量减少,可以降低模具成本,比如对汽车发动机罩盖内外板,采用冲压技术需要通过拉延、修边、翻边整形、冲孔等多工序,涉及凹模、凸模、翻边镶块等多套模具,内板加强件结构复杂,需要的模具套数相对较多。若采用压铸对发动机罩盖进行生产,无需修边、翻边整形、冲孔等工序,因此压铸发动机罩盖外板只需要一套模具、内板只需要一套模具,在模具套数方面优势明显。因此,在现阶段融合多种成形技术,可以达到降低生产成本的目的。
当薄壁压铸技术逐渐成熟时候,对于车门、发动机罩盖、行李箱盖这些需要内外板的组合件,只需要采用单板,适当提升结构件平均厚度,对模型进行厚薄区域优化,设定合理的加强筋和流道,最终这些内外板结合件只需要一体式单板即可,因此未来随着薄壁压铸技术成熟,一体式车身或将进入大量应用。
4、总结与展望
(1)文章分析了车身覆盖件外形、轻量化、成形工艺、连接工艺、材料5个研究方向,分别对技术现状进行概述。
(2)对冲压、压铸技术进行了梳理,对TRB技术应用进行了概述。
(3)提出了根据车身覆盖件厚度和复杂度特性进行多技术结合的生产方式。
(4)汽车车身覆盖件技术正朝着一体化、低成本、轻量化方向发展。为此,需要进一步加强对车身成形工艺中压铸工艺以及TRB技术研究。
参考文献
[1] ZHAO D T, CHEN H, LI X D, et al. Air pollution and its influential factors in China’s hot spots[J].Journal of Cleaner Production,2018(185):619-627.
[2] AL-TAAI S H H, MOHAMMED A D W A. Air Pollution:A Study of Its Concept, Causes, Sources and Effects[J].Asian Jornal of Water, Environment and Pollution, 2022, 19(1):17-22.
[3] XU B, LUO L, LIN B. A dynamic analysis of air pollution emissions in China:Evidence from nonparametric additive regression models[J]. Ecological indicators, 2016(63):346-358.
[4] 董学锋.车身材料与车身轻量化[J].汽车工艺与材料,2017(7):1-18.
[5] 陈承杰,胡恩锴,许圳淇,等.新型仿生折扇两向可变汽车尾翼设计及分析[J].机电信息,2022(10):37-40.
[6] 张震,李旭,崔行振.基于CFD的某跑车外流场数值模拟[J].山东工业技术,2017(12):285-287.
[7] FERRARIS A, PINHEIRO H, AIRALE A, et al.City Car Drag Reduction by mea-ns of Flow Control Devices[C]//2020 SAE Brasil Congress&Exhibition,2021.
[8] 马爽,崔凯.东风雪铁龙C6[J].汽车与运动,2016(10):30-33.
[9] 王占强.安全的国民车长安逸动安全性深入解析[J].世界汽车,2012(11):100-105.
[10] 本刊编辑部.品质家轿进化者长安逸动PLUS[J].汽车观察,2020(5):84.
[11] 牛小欧,朱耘.长安汽车:仰望星空很远,脚踏实地有难[J].商学院,2020(10):84-87.
[12] 高驰.一文读懂《节能与新能源汽车技术路线图2.0》:2035年新能源市场占比超50%[J].汽车与配件, 2020(21):40-41.
[13] SUPHANUT K, PATTARAMON J, HIROSHI H A. Lightweight Bus Body Design and Optimization for Rollover Crash worthiness[J].International Journal of Automotive Technology, 2020, 21(4):981-991.
[14] 王童,杜轶群,陈轶嵩,等.基于结构轻量化的城市客车车身生命周期评价[J].汽车工程,2022, 44(5):778-788.
[15] 韦学军.基于碰撞安全性的汽车车身轻量化设计分析[J].中国设备工程,2021(21):82-83.
[16] 高丰岭,雪颖,战楠,等.碳纤维复合材料车用结构设计与仿真研究综述[J].汽车科技,2020(2):74-80.
[17] IVANJKO M, MESCHUT G. Innovative joining technology for multi-material applications with high manganese steels in lightweight car body structures[J]. Welding in the World, 2019, 63(1):97-106.
[18] 董学锋.商用车的质量特征及轻量化评价[J].汽车技术,2018(1):10-14.
[19] 王康康,陈泽中,江楠森,等.基于GA-BP的汽车行李箱盖内板冲压成形工艺优化[J].塑性工程学报,2021, 28(9):28-34.
[20] 曹琳琳,徐家川,张云,等.先进高强钢冲压成形回弹工艺参数优化[J].农业装备与车辆工程,2022, 60(5):137-140+145.
[21] 《铸造工程》编辑部.沃尔沃新工厂将导入一体压铸工艺[J].铸造工程,2022, 46(2):25-25.
[22] KARANI K, ALI B, AHMET C, et al. An experimental investigation of the cooling and heating performance of a gravity die casting mold with conformal cooling channels[J].Applied Thermal Engineering, 2021,194(7):117105.
[23] NIU Z C, LIU G Y, LI T, et al.Effect of high pressure die casting on the castability, defects and mechanical properties of aluminium alloys in extra-large thin-wall castings[J].Journal of Materials Processing Technology, 2022,303(5):117525.
[24] 冯永旺,孙广丰,张剡.汽车车身连接工艺现状及发展趋势分析[J].汽车工业研究,2020(1):28-30.
[25] 赵建姣,陈冲,汉俊梅,等.白车身车门激光飞行焊接技术及工艺调试[J].汽车工艺与材料,2022(6):33-37.
[26] 刘江超,徐士杰,谢涛.结构胶在汽车车身中的应用[J].山东工业技术,2015(13):271-271.
[27] 张士展,吴晓欢.车身结构胶失效仿真研究[J].中国胶粘剂,2022, 31(5):38-44.
[28] 董学锋.车身材料与车身轻量化[J].汽车工艺与材料,2017(7):1-18.
[29] CHEN X, ZHANG Y Q, JIA P, et al.Research on lightweight of thin walled beam for automobile body[C]//E3S Web of Conferences, 2021, 268:01057.
[30] 刘雅芳,董万鹏,饶轮.基于LS-DYNA的6082铝合金车门防撞杆轻量化设计与碰撞性能分析[J].上海工程技术大学学报,2015, 29(4):312-315.
[31] 杨岭,倪秀元.汽车塑料车身的最新发展现状与对策[J].汽车工艺与材料,2004(5):11-13+20.
[32] 许江菱,钟晓萍,朱永茂,等. 2015~2016年世界塑料工业进展[J].塑料工业,2017, 45(3):1-44+108.
[33] 徐作文,陈伟,赵春.碳纤维复合材料汽车前车门轻量化设计与分析[J].科技创新与应用,2018(36):79-81.
[34] FANG Q. Numerical Simulation of Hot Stamping Forming of AZ Series Magnesium Alloys and Optimization of Die Process[J]. Journal of Chemistry, 2022,2022(5):6484242.
[35] 吕兴锋. TRB构件在纯电动汽车车身结构中的应用[D].重庆:重庆交通大学,2020.
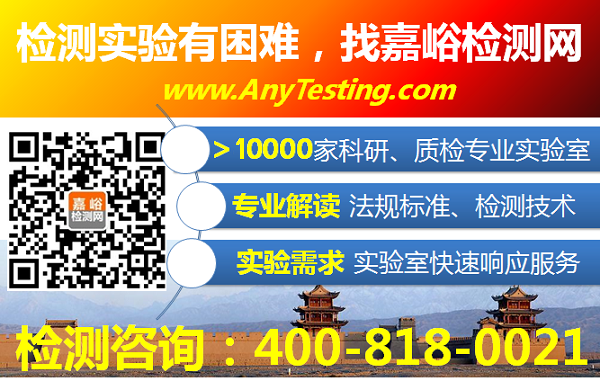