铝壳锂离子电池在应用过程中会经常发生壳体腐蚀漏液问题,该失效模式严重影响电池的安全性和寿命。因此,充分理解锂离子电池铝壳腐蚀的机理,并将该理念应用于结构设计、制造设计可有效预防该失效模式的发生。
铝壳电池腐蚀漏液的原因主要有两个方面。一、电池存放或使用过程中接触到腐蚀型物质(酸或碱物质),从外部腐蚀铝壳导致漏液;二、内部发生副反应导致壳体内部发生腐蚀漏液。
其中外部腐蚀可以通过控制电池存放和使用的环境进行控制;内部腐蚀则需要对电池结构、制造等进行设计与控制。
Al嵌锂电压及粉化原理
左图为Al箔作为石墨的集流体,对电极和参比电极都为金属锂片,构成三电极体系。电极的嵌锂容量高达720 mAh/g,高于石墨电极的理论容量,Li+脱嵌时,出现2个电压平台,这是由于Li+分别与石墨及Al发生嵌入反应。在0-0.4V主要是Li+从石墨中脱出,容量约为300mAh/g,而在0.4-0.6V主要是Li+从Al中的嵌脱反应,容量约为200 mAh/g。
Al作为工作电极时的首次放电曲线。Al箔的放电曲线分为两个部分,前期放电电压急剧下降,容量较小;后面的放电电压上升到0.2 V,成一个平台,放电容量随时间而增大,而电压不下降,反而稍有上升,直至末期电压才下降。金属Al的晶格八面体空隙大小与Li+大小相近,极易与Li+形成金属间隙化合物。假如金属Al晶格中所有的八面体都嵌入Li+,形成化学式为 LiAl的合金,则Al的放电容量约为990 mAh/g。由右图可知,Al箔的嵌锂容量超过了1200 mAh/g,这说明Al和Li+不单形成了化学式为LiAl的合金,还有可能形成了Li3Al2或Li4Al3。
综上,Al在电压0.2~0.4 V平台段会发生锂铝合金的副反应,Al晶格发生膨胀、破裂, Al变灰黑色,,失去金属光泽, Al 粉化严重,呈现多孔或裂纹。
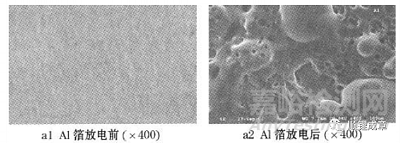
预防措施
对于全电池来说,腐蚀需满足3个条件,电子通道,离子通道,以及腐蚀反应电位。
离子通道无法避免,如何阻止电子通道和腐蚀反应电位的出现起到至关重要作用。
全电池的等效电路如下,从等效电路可知,V正负=V正壳+V负壳,V负壳为R2的分压,R2/R1比值越小,则V负壳越小,发生腐蚀的概率则越大。任何防止负极和壳体接触的措施均可起到一定的预防效果。
阻止负极与壳体接触,绝缘设计要做到全面化,常见设计有盖板正极弱导,顶盖绝缘介子,卷芯绝缘包裹充分,电芯包蓝膜;制造方面,要做到对绝缘包覆不良进行管控,如对绝缘包覆进行CCD检测,人工全检;其次,也要对金属异物管控。
下表显示使用不同的阻值导线连接正极与壳体,减低正极与壳体间的阻值,即正极弱导,从而提高V负壳,从图可知,R1越小,腐蚀的可能性越小。通过实验,可确定最佳的阻值范围。
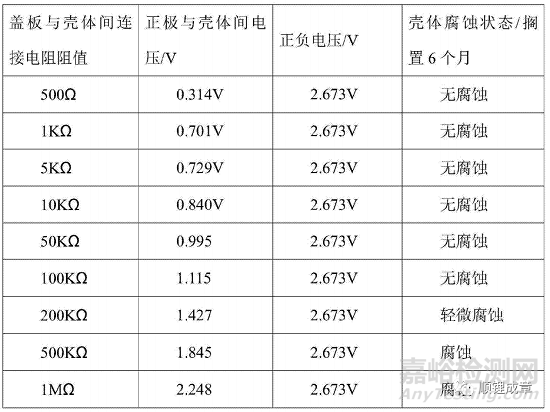
常见负短失效模式
负极直接与壳体接触导致腐蚀
上图为由于负极分切毛刺过长、卷绕或组装极耳粘贴胶带移位导致绝缘缺陷、极耳焊接错位和入壳时电极芯外绝缘破损等因素均使负极与壳体内壁接触。由表可以看出,负极与铝壳内壁短路类电池的壳电压全部为0 V。在此状态下,经几次短暂充放电循环后,电池铝壳就会发生腐蚀,负极与铝壳内壁短路类电池经过暂几次充放电后,铝壳最薄处的防爆阀区域出现腐蚀,腐穿后电解液流出。
电池负极端子通过残留电解液桥或金属多余物与壳体外短路类导致腐蚀
在化成后无电解液残留的锂离子电池壳电压在 1~2 V范围内;有电解液残留的壳电压全部偏低,在 0.15~0.4 V 范围内;说明残留电解液可以导致壳电压偏低。
电池在周转或测试过程中,铝外壳与负极端子无金属部件搭接电池, 其壳电压全部在 1~2 V 范围内,有金属搭接的电池其壳电压在 0~0.4 V 范围内, 说明铝外壳与负极被金属搭接会导致壳电压偏低。
从数据上看,初始壳电压在 1.5~1.9 V 内电池,当壳体与负极端子被金属导线搭接时,壳电压变低;移去导线后,壳电压有所恢复,但低于初始值;导线搭接时间越短,移去导线后壳电压恢复越快。
取壳电压为 1~2 V 的电池,用导线将其外壳与负极搭接,并用透明胶带固定好,,然后以 0.5 C 对其连续充放电10 周,查看铝壳腐蚀情况初始壳电压 1~2 V 的电池,铝壳防爆阀无腐蚀及漏液,但经导线搭接并做几次充放电后,铝壳防爆阀就出现腐蚀及漏液问题。说明铝外壳和负极间若被导电液体金属导通,在此状态下,电池若进行充放电,易出现铝壳的腐蚀及腐穿漏液。
相邻单体电池铝壳搭接的PACK电池组导致腐蚀
理论上单节壳电压范围应该在 0~3.4 V,对串联后电池若金属外壳出现搭接出现异常壳电压数值作简单原理分析。假设组件串联电池节数为 3, 组件负极引出端的单体电池序号为 1,其余两只电池顺序标为 2 和 3。1 号电池负极端子相对电位定义为 0 V,壳电压为 1.5 V,电池正极电位为3 V,2 号和 3 号单体不同部位电位和壳电压数值如上图,当 1号与3号电池铝外壳未碰接时,则组件处于开路状态,3只电池的壳电压无变化;当第1节与第3节电池铝外壳发生搭接时,红色虚线示意导通方式,此时组件外部接触,整个串联电池组形成回路, 3号电池的壳电压 (V5)7.5 V,1号电池壳电压(V1)1.5 V,两者出现6 V压差,两者因外回路 ,两者 6 V 壳压差会逐渐趋于平衡,V5不断变小,V1不断变大,最终达到近4.5 V 壳电压平衡(V5=V1=4.5 V)。此时第1节电池壳电压为 V1-V0=4.5 V, 第2节 电池壳电压为V3-V2=1.5 V, 第3节电池壳电压为V5-V4= -1.5 V,此时第1节壳电 压出现增大,而第3节壳电压出现负值减小的情况,壳电压偏小时,由于在低电位下,电池在充放电过程中铝外壳易发生锂铝合金电化学腐蚀反应,导致第 3 节电池铝壳防爆阀出现腐蚀现象,甚至腐穿,电解液漏出,使循环性能快速下降。
弱酸性水溶液中铝壳锂离子电池腐蚀
选取弱酸性的水溶液作为浸泡电池的溶剂,水溶液的PH值大约为5。
浸水 8 天后从水中取出擦干,晾置一天后各单体电压的正-壳电压有一定程度的恢复,但是均不能恢复至原来的正常水平,而且恢复程度杂乱无规律。浸水后每只单体电芯的壳负电压也都变得异常,变化趋势与正壳电压正好相反,001# 的壳负电压降至 -1.5V~-0.2V, 007# 的壳负电压则升至 19V 左右。在浸水过程中壳电压有一定的波动,但是波动不大。浸水 8 天后从水中取出擦干,晾置一天后各单体电压的壳 -负电压有一定程度的恢复,但是只有 002# 和 007# 的壳负电压恢复至正常范围内,其他电池的壳负电压依然异常。
浸水后的电池每天进行 1C 充放电,充放电之后以满电状态继续浸泡在水中。3 天后,电池壳体出现了比较明显的点状和圈状腐蚀现象。从现象来看,001# 与 006# 腐蚀现象相对比较明显,其壳电压异常,壳与负极电压低至 0V 相对应。该结果表明,电池浸水后继续充放电,会加速电池壳体的腐蚀。这可能是因为通电后,加速了铝壳的电化学腐蚀过程所导致的。
电池浸水后继续对电池进行充放电,会加速电池壳体的外部腐蚀。如果电池浸入雨水,雨水中还会有杂质离子,会进一步加速铝壳的腐蚀。而且,由于浸水后壳电压异常,此时对电池进行充放电,容易有金属锂沉积在壳体上,从而形成锂铝合金,使壳体腐蚀进而漏液。综上所述可知,正负极与壳体之间有电压的铝壳锂离子电池,浸水之后会发生腐蚀,因此在使用过程中应避免电池浸水。
负短电池与正常电池性能差异性分析
电池的充放电曲线以及循环测试
下图为正常电池和腐蚀电池的循环性能测试结果。由图可见,在前400次循环中两只电池的容量保持率率趋于一致,而在400次循环后,腐蚀电池的循环性能下降逐渐明显,正常 电池在循环在1500次后容量保持率为88%,而腐蚀电池循环1500次后容量保持率仅有60%,这说明随着循环的进行,有部分活性锂离子并没有嵌入石墨负极中,而是可能嵌入到金属铝壳中,从而导致铝壳与负极电位强制平衡,消耗了正极的活性物质,进而导致循环性能的下降。
电池存储以及放电倍率的比较
正常电池和腐蚀电池在满电存储一个月的情况下,残余容量与恢复容量无差别,随着存储时间的延长,腐蚀电池的残余容量和恢复容量逐渐降低。在5C以下的倍率放电时,正常电池和腐蚀电池的性能没有明显差别。而当电流逐渐增大到10C 以上时,腐蚀电池的放电倍率性能逐渐下降。由此可以看出,电池经过腐蚀后会严重影响电池的性能,降低了电池的使用寿命。
负极与壳体接触的电池,在电池的使用或者存储过程中,腐蚀反应先发生在铝壳的内壁,随着时间的增长,腐蚀反应进一步深入,导致铝壳内壁腐蚀反应逐步发展到铝壳外侧,因此铝壳外侧可以目测到腐蚀痕迹随着嵌锂的深入,逐步反应生成氧化锂、氢氧化锂,所以腐蚀样品溶解后呈碱性,随着腐蚀反应的进一步发生,锂单质、氧化锂、氢氧化锂以及嵌锂的铝化合物与空气中的二氧化碳反应生成Li2CO3和少量的和少量的[Al2Li(OH)6]2CO3,此时电池将逐渐失效。
参考文献
[1]秦红莲, 李艳杰, 高飞, et al. 弱酸性水溶液中铝壳锂离子电池的腐蚀研究[J]. 电源世界, 2016(11):29-31.
[2]倪江锋, 周恒辉, 陈继涛, et al. 锂离子电池集流体的研究[J]. 电池, 2005, 35(2).
[3]CN201910308500.4一种锂离子电池盖板正极弱导阻值的检测方法
[4]张娜, 李杨. 锂离子动力电池铝外壳的腐蚀[J]. 期刊论文, 2015, 36(004):351-354.
[5]张大峰, 刘炜, 刘丽. 制程对锂离子电池铝外壳与负极间电压的影响[J]. 电源技术, 2019, 43(03):83-87.
[6]秦红莲, 李艳杰, 高飞, et al. 弱酸性水溶液中铝壳锂离子电池的腐蚀研究[J]. 电源世界, 2016(11):29-31.
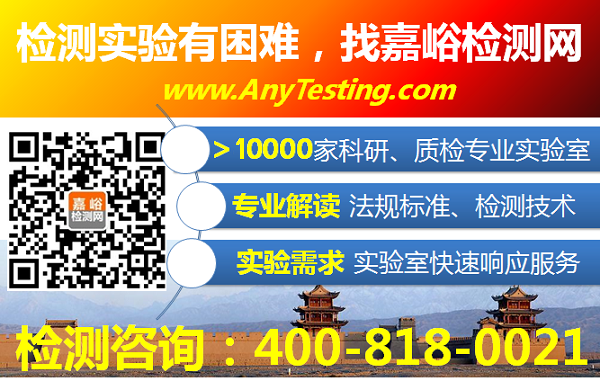