随着经济以及汽车工业的飞速发展,人们对汽车的安全性、舒适性和豪华性等要求都有大幅度提高。目前主机厂主要根据光泽、雾影、橘皮及鲜映性对涂层外观质量进行评价,其中光泽、雾影主要由汽车涂料决定。橘皮表征又分为长波和短波,长波波长为0.6~10mm,短波波长为0.1~0.6mm,如果长波和短波波长超标,则涂装质量不合格。鲜映性(DOI)可以表征涂装后外观的光泽度及成像的清晰度,并直接影响涂层的装饰性和人对整车的感观效果,DOI越高,漆膜成像越清晰和锐利,漆膜的外观质量越好。
汽车冲压外覆盖件直接暴露于汽车外部,表面上微小的缺陷在涂装后仍会导致光的漫反射,影响涂装外观性能参数,损害汽车美观。因此,汽车冲压外覆盖件表面的质量管控一直是主机厂冲压车间的重要问题。通常来说,冲压外覆盖件常见的质量问题有高点、开裂、鼓包、硌伤、凹坑等,其中高点问题占比达到80%以上。因此,改善高点是主机厂冲压车间的永久课题。
如果冲压模具或者板料上存在异物颗粒,在零件成形过程中,其表面形成的凸(凹)点缺陷称为高点缺陷。高点缺陷主要分为两种形态:一种是异物在板料下方,成型后形成高点;一种是异物在板料上方,成型后形成凹坑。目前,主机厂通过对落料、冲压清洗、成型等各生产环节所涉及的异物进行管控,来达到改善高点的目的。然而,异物、板料性能、冲压生产工艺等因素对高点影响的研究较少,冲压车间对异物的管控方法缺乏针对性以及指导性,无法有效降低高点不良率。研究人员对汽车冲压外覆盖件高点影响因素进行研究,确定异物种类及尺寸、板料厚度、冲压模具间隙等因素对高点的影响规律,以指导冲压车间进行高点管控,并通过冲压高点对涂装质量表征参数影响的研究,确定高点如何影响涂装质量以及高点高度控制极值,进而指导冲压车间建立高点高度管控标准,提高覆盖件表面质量及生产效率。
1、试验材料及方法
试验用板材为常见车身外板材料 DC53D+Z镀锌板,经落料、冲压清洗、成型等工艺过程完成门外板制备。首先对高点形成过程及机制进行解析,确认可能会影响高点的主要因素,然后开展以下3个方面的研究:①锌粉、铁屑、铝丝、尼龙以及不同直径锌粉对门外板高点高度的影响;②板材厚度对门外板高点高度的影响;③模具间隙对门外板高点高度的影响。采用德国霍梅尔T8000轮廓仪测试高点的二维轮廓,测量长度为20mm。高点二维轮廓如图1所示,通过轮廓最高点与最低点之间的高度来表征高点高度。
2、试验结果及分析
2.1 高点形成过程及机制
图2为冲压成型过程。图2a)为拉延成型开始,凹模向下运动,两侧拉延筋与下模压扁圈拉延槽优先接触,对板材两侧施加锁紧力,继续向下运动开始拉延成型;图2b)为沿凸模成型,两侧拉延筋夹紧板材向下运动,制件型面与凸模圆角型面相关,此时反凹造型不参与成型;图2c)为沿凹模成型,两侧拉延筋夹紧板料继续向下运动,模具凸起圆角及型面部分持续拉伸成型,反凹造型位置受凹模造型向下作用力,此时板料沿凹模型面凸起及型面拉伸成型;图2d)中,当上模压到下死点,管理面轮廓成型到位,拉伸成型完毕。
在沿凸模成型过程中,板材受到异物颗粒向上的作用力,当作用力大于板料屈服极限时,板材发生屈服形变,开始产生高点,凸模高点形成过程如图3所示。可见,减小异物颗粒作用力或者增加材料屈服极限都可以减弱高点程度,而异物颗粒的种类及尺寸等因素会影响作用力,而材料厚度会影响材料的屈服极限。
反凹部位成型后继续向下运动,当凸凹模间隙H小于颗粒尺寸h时,高点开始具备产生条件,从而形成高点(见图4)。可见,凸、凹模间隙会影响高点的产生。
2.2 异物种类对高点高度的影响
将同一直径(0.15mm)的锌粉、铁屑、铝丝、尼龙放入门外板模具中,完成板材DC53D + Z(0.7mm)冲压,在板材表面制备出不同的高点,测试了高点高度。不同异物在板材表面形成的高点高度如表1所示。可见,铁屑、锌粉、铝丝以及尼龙丝所形成的高点高度依次降低。
在成型过程中,板料受到异物颗粒向上的作用力,当作用力大于板料屈服极限时,板材发生塑性变形,即产生高点。在拉延过程中,异物颗粒发生弹性变形,板材则发生不可逆的塑性变形。在这个过程中,颗粒抵抗变形的能力会对高点产生一定影响。弹性模量是代表固体材料抵抗变形能力的物理量,因此研究了颗粒弹性模量与高点高度的关系,结果如图5所示。可见,异物颗粒弹性模量与高点高度呈现较为明显的正相关关系。
2.3 铁屑直径对高点高度的影响
分别将直径为0.05,0.10,0.15mm的铁屑颗粒投入到门外板模具中,完成材料DC53D+Z(0.7mm)冲压,在板料表面制备出高点并测试其高度,结果如图6所示。可见,高点高度与铁屑直径呈现较为显著的正相关关系。
2.4 板材厚度对高点高度的影响
将直径为0.15mm的锌粉颗粒投入到门外板模具中,分别冲制不同厚度的板材DC53D+Z,在板材表面制备出高点并测试其高度,结果如图7所示。由图7可知:高点高度与板材厚度呈较为明显的正相关关系。
2.5 模具间隙对高点高度的影响
将直径为0.15mm的锌粉颗粒投入到门外板模具中,调整模具间隙,完成材料DC53D+Z(0.7mm)冲压,在板材表面制备出不同高点,并测试了其高度,结果如图8所示。可见,随着模具间隙的增大,高点高度呈现减小的规律。
2.6 涂装试样高点测量结果
为保证试样的准确性,完全按照冲压拉伸过程获得高点试样,选取5.7μm~14.6μm之间8个高度等级,使用轮廓仪对8个高点试样的高点高度进行测量,得到高点高度分别为5.73,6.336,9.366,10.634,10.744,11.844,13.774,14.601μm。
2.7 高点高度对漆膜长波的影响
为保证试样准确性,使用试验车贴片方式,整车参数全车喷涂,喷涂色漆为玄晶黑,试样均按该法处理,喷涂过程与得到的试样外观如图9所示。使用橘皮仪测量每个试样长波3次,取平均值作为试样漆膜长波,测试结果如图10所示。由图10可知:漆膜长波与高点高度呈较为明显的正相关关系。
2.8 高点高度对漆膜短波的影响
使用橘皮仪对试样漆膜短波进行检测,每个试样检测3次,取平均值,即得到试样短波,测试结果如图11所示。由图11可知:可以看出高点高度与漆膜短波关系并不明显。
2.9 高点高度对漆膜鲜映性的影响
使用橘皮仪对漆膜试样的DOI进行检测,同样取3个数据的平均值作为最终结果,结果如图12所示。由图12可知:高点高度对漆膜 DOI影响较弱。
一般主机厂外覆盖件面漆长波、短波及鲜映性根据喷涂角度及面漆颜色有不同的控制标准,试验面漆喷涂方向为垂直喷涂,面漆颜色为玄晶黑,因此在该条件下标准要求长波数量≤10,短波数量≤25,鲜映性≥85。根据所得数据分析,高点高度与漆膜长波数量相关,而与短波数量和DOI弱相关,且全部试样的短波数量及DOI均在标准范围内,因此选用长波数量作为量化评价指标。根据试样高点高度及漆膜长波数量建立回归方程,其关系为长波数量=7.946+0.255×高点高度。结合该式可计算出高点极限高度标准为10.496μm。
2.10 结果与讨论
由结果可知,高点高度与漆膜长波数量呈较强的正相关关系,这是由于漆膜有一定流动性,在喷涂及烘干过程中会产生自流平,对材料表面有一定的遮盖性,喷漆对高点的遮盖作用如图13所示。汽车板实际表面形貌的几何形状偏差一般分为3种误差结构形式,即形状误差、表面波纹度和表面粗糙度,分布在不同的波长范围。根据 ASME(美国机械工程师协会)的定义,粗糙度的波长小于1mm,波纹度的波长为1~10mm,而波长大于10mm的为几何形状,这3种表面轮廓参数与长短波值的对应关系如图14所示,可以看出短波基本与粗糙度相对应,而长波值与波纹度及几何形状相对应。经测量可知,高点直径一般为5~15mm,经过涂装的遮盖后波长基本与波纹度波长类似,因此高点高度对漆膜的长波值影响较大。
3、结论及建议
对高点形成过程及机制进行了解析,确认异物颗粒、板材以及模具间隙等因素是影响高点的主要因素,并对高点高度的影响因素进行了研究;同时对冲压覆盖件高点高度对喷漆后漆膜的长短波及鲜映性的影响进行研究,并根据各参数的相关性关系及主机厂涂装控制标准得出冲压车间高点极限高度控制标准,对冲压过程清洁度控制提出了建议。
(1)冲压件高点高度与异物的尺寸及种类、材料厚度呈正相关关系,即异物尺寸越大、异物弹性模量越大、材料厚度越大,形成的高点高度越大;而高点高度与模具间隙呈负相关关系,即模具间隙越小,高点高度越大。
(2)面漆漆膜长波数量与冲压件高点高度呈强的正相关关系,随着高点高度的增加,高点处漆膜长波数量增大,而面漆漆膜的短波及鲜映性与高点高度关系较弱。
(3)建立高点高度与长波数量的回归方程,结合主机厂长波数量小于10的管控标准,可以推导出该冲压车间高点极限高度为10.5μm。
作者:姚士聪1,2,郝玉林1,2,龙袁1,2,郑学斌1,2,刘李斌1,2,李学涛1,2,孙鹏3
单位:1.首钢集团有限公司技术研究院;
2.绿色可循环钢铁流程北京市重点实验室;
3.北京首钢股份有限公司。
来源:《理化检验-物理分册》2023年第12期
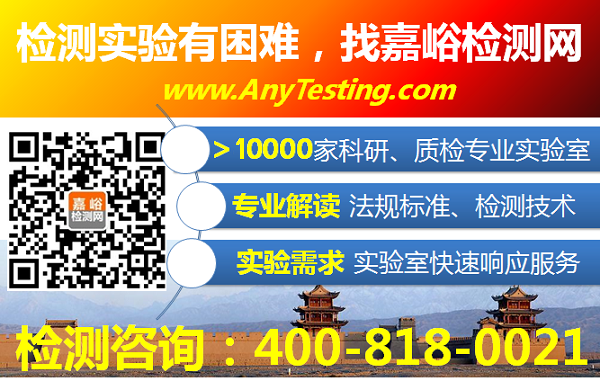