本文针对某伺服机构控制器电路板采用故障物理方法进行失效分析,然后在不同温度应力下开展该电子产品温升试验和热仿真,之后基于Coffin-Manson模型进行产品焊点疲劳寿命仿真并求解各元器件寿命分布,最后构建竞争失效模型进行电路板寿命预计。通过温度应力试验得到了关键元器件温升值在23℃~31℃范围内,基于CRAFE热仿真得到了产品各元器件温度,应用Coffin-Manson模型得到了元器件寿命分布,运用竞争失效方法计算了产品失效概率函数,评估了产品工作10年的可靠度为0.94,在可靠度指标为0.9时其工作寿命为12.11年。本文基于温度应力试验和热仿真,通过进行故障物理分析和元器件竞争失效分析有效评估了电子产品工作寿命,对其他类似电子产品可靠性分析提供了一定参考。
引言
随着军事科学技术的发展和新时期装备的迭代更新,现代装备对可靠性的要求越来越高,研究发现在环境引起的装备故障中电子产品的失效比例在所有统计试验中占比最大。电子产品作为装备关键组成部分对保证装备战备完好性、任务成功性以及维修保障性等十分重要,同时装备中电子产品也呈现出研制周期短、新技术大量应用、可靠性指标越来越高的发展趋势,因此如何有效分析和提升装备电子产品的可靠性成为亟待解决的问题。
可靠性分析包括基于概率统计和基于故障物理模型两个方向,然而,在无故障样本情况下,基于概率统计方法面临应用上的局限性。美国马里兰大学最先提出并展开了基于故障物理(Physics of Failure,PoF)模型的可靠性分析技术研究,之后广泛应用于美国的航空航天和陆军的装备研究。基于故障物理的试验通常需要耗费大量资源,而仿真具有成本低、可重复等优势,现今多数研究采用试验仿真相结合的方式探索电子产品故障机理模型。
国内外学者在电子产品故障物理分析、疲劳模型研究、可靠性仿真、寿命预计等方面已取得许多成果。Jiao J等给出了电子产品故障原因统计结果,其中温度占比43.3%,这温度和振动应力已成为电子产品可靠性研究的重点。Wilman A等针对电子产品进行了基于故障物理分析的寿命预测研究,但其对可靠性求解过程分析不充分。胡博等针对机载电子产品进行了可靠性仿真试验的应用探索。栾家辉等针对电子产品薄弱环节进行了单应力和多应力累积损伤仿真分析并给出产品寿命预测结果。陈颖等分析了电子产品部分元器件失效模式、机理与故障物理模型,研究了一种基于故障物理的产品可靠性仿真方法,但对有热源产品的温升参数研究存在不足。黄姣英对故障物理分析中常用焊点疲劳模型进行了综述。李宝兰针对舵机控制电路板进行了热分析及基于Coffin-Manson模型的焊点疲劳寿命预测研究,该研究只针对电路板部分焊点进行了分析。现今,对于电子产品可靠性分析虽已有大量研究,但针对装备典型电子产品基于故障物理的可靠性分析应用研究仍不充分,现有研究多针对电子产品薄弱环节进行分析,仍需将产品多个关键元器件纳入整体寿命评估研究中。
本文针对某伺服机构控制器电路板,运用故障模式、机理及影响分析(FMMEA)方法进行产品故障物理分析并确定基于温度应力的故障物理模型;之后分析确定产品组成和材料参数,通过温度应力试验和热仿真相结合的方式分析电路板温度分布;进一步,通过焊点疲劳模型计算疲劳寿命,求解元器件疲劳寿命分布;最后结合竞争失效分析实现电子产品可靠工作寿命有效评估。
失效物理模型分析
1、电路板结构
本文研究实例对象为某装备伺服机构控制器电路板,该产品属于典型电子产品。电路板整体较小,长126mm、宽54mm、厚2mm,其中部分元器件质量和体积相对较大。该电路板硬件主要由DSP及外围电路模块、功率驱动模块、模数转换模块和接口模块等组成,PCB焊接各类电阻、电容、集成电路、电连接器等元器件。
图1 电路板实物图
2、失效物理分析
使用FMMEA方法对电路板进行潜在的故障模式和机理分析。电路板工作环境条件良好,可排除振动、断裂、静电和辐射等故障因素,同时电路板元器件满足军用标准,自身故障发生可能性远小于焊点发生故障可能性。实际使用时,温度变化会导致电连接部位焊点热疲劳失效,因此本文主要进行基于焊点热疲劳的电路板失效分析研究,该产品部分元器件故障物理信息如表1所示。
表1 部分元器件的FMMEA
3、Coffin-manson模型
焊点疲劳寿命预测模型主要基于塑性变形、蠕变变形、断裂参数、能量等进行构建,研究表明材料的塑性应变逐渐累积将会引起疲劳失效,对于电路板故障物理失效分析常用焊点热疲劳模型为基于应变的Coffin-Manson模型,该模型体现了应力与循环周期的关系,模型公式如下:
式中:
—器件失效所经历的循环周期;
—疲劳系数,该系数与材料相关,对于63Sn37Pb,该值取 0.325;
c—疲劳指数,该指数与材料相关;
—剪切应变范围。
式中:
—焊点温度循环中平均温度;
—最高温恒定时间;
f —温度循环频率。
式中:
F —应力范围因子,
L—元器件长度,
h—焊点高度,
—元器件壳体热膨胀系数,
—基板热膨胀系数,
—器件外壳工作温度,
—基板工作温度,
—初始温度。
常见焊点横截面如图2所示。
图2 焊点横截面示意图
已知温度循环载荷作用下元器件与PCB基板均受温度影响发生胀缩,PCB板焊接多种材料的元器件,不同元器件相对基板产生应变,进而导致焊点疲劳损伤。
温度试验与仿真
通过分析电路板组成,研究文献确定各部分的材料类型、热膨胀系数、弹性模量、导热系数等材料参数,对于本文研究的电路板,采用温度试验和热仿真相结合的方式确定各元器件温升参数,用于计算焊点疲劳寿命。
一.温度应力试验
1.温升试验环境搭建
通过梳理元器件清单并根据实际使用情况,得到该电路板4个发热功率较高且容易产生焊点热疲劳的关键元器件。对于1号、2号和3号器件分别使用编号为S01、S02、S03的热电偶分别采集电源模块温升数据,由于4号集成电路尺寸较大,使用S04和S05号2个热电偶在不同位置采集温度数据,之后按照控制器实际安装方式进行组装,进一步通过连接供电电源、数采设备、计算机,并将该控制器放入温箱组成试验系统,热电偶贴片和测试系统如图3所示。
图3 温度应力试验环境搭建
2.温升试验流程
将温箱分别调整到25℃、35℃和45℃进行试验并采集数据,设定每种温度应力下数据采集时长为35分钟、采样频率10Hz。试验环境搭建完成后,首先将温箱温度设置为25℃,待温箱温度稳定至25℃后观察计算机显示的热电偶感知温度,数值稳定至25℃时打开电路板电源使其正常工作,通过计算机记录设备采集的温升数据,完成该温度应力下试验后关闭电路板电源。
3.温升试验结果分析
试验得到25℃、35℃和45℃温度应力下电路板关键产热元器件温升数据,通过中值滤波和均值滤波方法对信号数据进行处理,各测点在3种温度环境下的温升曲线如图4所示。
图4 热电偶测量温升曲线
电路板在不同温度环境应力下运行时同一位置温升速度随温度升高逐渐变慢最后趋于稳定;电路板不同位置工作运行温升量和热平衡值存在差异,例如1号位置(S01)在不同温度应力下热平衡温升值均比2号位置(S02)低5.5℃左右,比3号位置(S03)低4.3℃左右。根据热电偶采集数据,计算得到在25℃,35℃和45℃环境温度下各热电偶测量点热平衡时的温升数据,热平衡温升随温度变化的温升曲线如图5所示。
图5 各监测点温升规律图
从图5中可知热平衡时各测点温升在23℃到31℃内,随着环境温度的升高稳态温升量略有下降趋势,同一位置不同温度应力下温升差均小于1℃。将试验温升结果作为可靠性仿真模型的参数输入,用于进行电路板温度分布仿真分析。
二. CRAFE热仿真
1.仿真模型构建
本文基于CRAFE软件进行电路板的温度应力仿真分析,该软件可提取各元器件仿真过程温度参数值。使用AD(Altium Designer)软件将设计的电路板模型转换为ODB++模型导入CRAFE软件并生成相应的几何模型。该模型主要包括元器件层、丝印层、钻孔层、阻焊层、铜层、机械层等,模型如图6所示。
图6 电路板模型图
2.边界条件设定
热仿真过程设置电路板为自由状态,根据温度应力试验设置对应仿真试验剖面和器件温升参数,对于不同温度应力采用相同的环境温度变化趋势,构建3种温度应力下的环境剖面如图7所示。
图7 仿真试验剖面
选取4个关键发热元器件作为温升参数设置点,将温度试验结果输入仿真模型。在温度试验过程中对于4号位置通过热电偶获取了两组温升数据,因此模型4号位置对应元器件温升参数设置为S04和S05热电偶得到温升的均值。
图8 温升参数设置点
3.电路板热仿真
使用仿真软件在25℃温度应力仿真试验剖面下进行电路板热仿真,得到三维温度云图结果如图9所示,基于温度云图提取产品各元器件温度。
图9 电路板热仿真结果(25℃)
在25℃、35℃和45℃三种温度应力下通过仿真可以得到产品温度应力云图和所有位置的温度数据,根据以下公式计算温升设置点仿真与试验结果的相对误差,仿真与试验对比结果如表2所示。
式中:
s —仿真温度结果;
e —试验温度结果;
p —相对误差。
表2 仿真与试验结果对比
仿真结果和试验结果相对误差均小于5%。因此通过仿真得到的产品各位置温度具有较强可信度,同时表明在CRAFE软件中设置的各参数较为准确,可用于电路板各元器件温度仿真提取。
产品寿命预计
1、 Coffin-Manson寿命预计
将改进后的 Coffin-Manson 热疲劳模型作为寿命预计的故障物理模型,设置电路板全寿命周期经历的温度循环任务剖面如图10所示。
图10 任务剖面
根据各元器件封装、引脚、焊点和温度等方面参数输入,将任务剖面作为仿真条件输入,通过每周一次的温度循环仿真对产品各个元器件进行基于焊点热疲劳故障的寿命预计。得到各元器件预计失效时间(Time to Failure,TTF),部分结果如表3所示。
表3 部分元器件寿命预计结果
2、Weibull寿命分布分析
在温度循环载荷条件下,元器件的焊点疲劳寿命的随机性通常可采用 Weibull 分布或对数正态分布进行描述。本文使用双参数威布尔分布表征元器件寿命分布特性,基于寿命预测结果仿真得到元器件失效概率分布,元器件累积失效概率和概率密度函数表达式如下:
式中:
m—形状参数;
η—尺度参数。
已知双参数威布尔分布 MTTF 可表示为:
设置经验参数m=3并根据各元器件焊点疲劳失效时间计算得到元器件寿命分布参数
,部分元器件寿命分布参数计算结果如表4所示。
表4 元器件寿命分布参数结果
3、竞争失效分析
将电路板元器件视为串联可靠性分析系统进行评估,根据各元器件失效概率分布,应用竞争失效理论计算电路板总体寿命分布。在电路板使用过程中,最早失效的元器件将导致电路板失效,假设每个元器件的失效时间为Ti,则电路板的失效时间为:
其中:K为电路板元器件个数。设Fi(t)是元器件 i 的累积失效概率分布,电路板的累积失效概率分布函数和可靠度函数分别为:
通过竞争失效公式求解得到电路板服从的威布尔失效分布的参数结果为m=3、η=25.66。电路板累积失效概率分布结果如图11所示。
图11 电路板寿命分布预计结果
由计算结果可知,运用竞争失效分析得到电路板的可靠度小于各元器件可靠度。电路板在规定任务剖面下使用10年的预计累积失效概率为5.75%,可靠度约为0.94。在产品实际可靠性设计中,若以0.90为可靠度指标计算剩余使用寿命,则可设定产品累计失效概率F(t)=0.1,通过威布尔分布逆函数计算得到产品预计出现故障的时间为12.11年。
结语
文中针对装备典型电子产品提出了一种基于温度应力试验的可靠性分析方法,用于评估了某伺服机构控制器电路板寿命。通过开展温度应力试验和热仿真,获得关键元件器温升特性和温升参数,通过应用Coffin-Manson模型得到了元器件寿命分布,结合元器件竞争失效分析进行了电路板工作寿命预计。论文主要针对故障物理中温度环境变化导致焊点热疲劳对电子产品可靠性的影响进行了研究,在后续工作中还需综合考虑其他复杂环境因素和失效模式,进而使得可靠性分析更加全面和准确。
引用本文:曹敬帅,秦强,张生鹏,杨培,乔洪凯.基于温度应力试验的电子产品可靠性仿真分析[J].环境技术,2023,41(03):31-37+43.
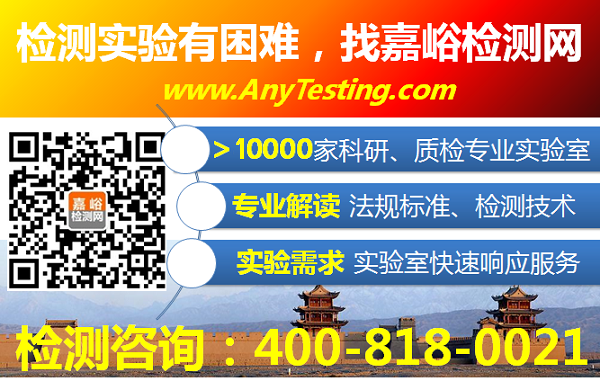