药品冻干是利用溶液经冷冻冻结在低温低压的条件下,从冻结状态不经过液态直接升华,去除掉水分完成干燥的一个过程,可以使冻干后的药品保持原有的理化性质和药物活性,且其有效成分损失很少。冻干后的产品由于自身的疏松结构,可以遇水复溶,具有含水量极低的特性,可以长期保存。
根据 2010 新版 GMP 要求,产品的生产工艺及关键设施、设备应当按照验证方案进行验证,而冻干机的性能则会影响产品的质量,如产品的性状、水分等。对冻干机的相关功能进行确认,可以确保冻干机能够按照既定的冻干工艺进行运行,保证药品冻干过程的稳定性,使制成的冻干粉针剂能有效地防止水溶液不稳定造成药物的降解,冷冻干燥后其真空状态能有效消除氧气对药品的氧化作用,从而大大改善药品的贮藏稳定性。
1、 冻干机箱体结构和内部系统组成
1.1 冻干机箱底结构组成
冻干机的箱体结构一般由以下结构组成:箱体、箱门、隔板、冷阱和主阀。
1.2 冻干机内部系统组成
冻干机的内部系统由液压系统、气动系统、热媒循环系统、制冷系统、真空系统、通气系统、CIP 系统、SIP 系统、排水及水环泵干燥系统和控制系统组成。
(1)液压系统:用于箱门、隔板和主阀等液压控制和运动。
(2)气动系统:包括一系列启动阀门。
(3)热媒循环系统:采用多个循环泵、多个板框换热器,换热回路上带有膨胀箱,以补偿在不同周期中由于温度变化而引起的容积变化。
(4)制冷系统:载冷剂流过蒸发器,蒸发器内的制冷剂蒸发吸热,随后制冷剂蒸汽(蒸发器上部蒸汽)被压缩机抽走,加压升温排入冷凝器,经过水或风进行冷却冷凝,有节流装置控制蒸发器制冷剂流量。
(5)真空系统:由一台罗茨泵和两台干泵组成,配置压力计用于真空控制,配置真空探头监视压力,普通压力变送器测量粗真空和压力。
(6)通气系统:向箱体掺气火冻干后破解真空,还起到化霜后向冷阱通风的作用。
(7)CIP 系统:由 CIP 储罐和增压泵组成,可蒸汽灭菌,通过泵供应 CIP 水压力,对冻干机进行清洗。
(8)SIP 系统:通过 121 ℃纯蒸汽对腔体和冷阱进行灭菌。
(9)排水和水环泵干燥系统:配置水环泵,用于除霜之后的冷阱抽空干燥。
(10)控制系统:通过 PLC 和 HMI 对系统进行监控。
2、冻干程序描述
冻干粉针剂的冻干程序可以分为以下阶段[1]。
(1)首先是对冻干制品进行半加塞,然后将制品放入冻干机。
(2)依次进行制品的预冻,将冷凝器降温,抽真空。
(3)待真空度达到一定的数值后,可对冻干箱内制品进行加热,第一步加温不使制品的温度超过共晶点的温度,进行升华干燥。
(4)待制品内水分基本干燥完再进行第二步加温,使制品上升到规定的最高温度,进行二次干燥。
(5)进行真空压塞或充氮压塞。
3、功能确认部分
3.1 检测仪器与材料
研工 TVS 温度验证系统、嗜热脂肪地芽孢杆菌生物指示剂(D121℃值为 1.5~3.0 min、孢子浓度约为 1.0×106~5.0×106 mL/个)。
3.2 功能确认测试方法
3.2.1 冷凝器降温时间和最低温度测试
真空冷凝器的工作温度直接影响冻干箱内部的压力和最终产品的干燥质量,因而需要通过测试来确定。
测试步骤:
(1)对冷凝器进行降温,当冷凝器开始制冷时,记下20 ℃左右的温度和时间,当冷凝器温度降至-40 ℃时,记录温度和时间。
(2)当温度到达-45 ℃以下时,启动真空泵组并在真空条件下继续给冷凝器制冷,直至温度降到-75 ℃以下,并记录数值。
判定标准:
(1)从 20 ℃降至-40 ℃的时间≤30 min。
(2)最低温度≤-75 ℃。
冷凝器降温时间和最低温度测试结果如表 1 所示。
由表 1 可以看出,冷凝器从 20℃降至-40℃的时间为24 min,小于 30 min,且最低温度可达到-75℃以下,说明冷凝器制冷效果达到要求。
3.2.2 板层(冷媒)降温时间和最低温度测试
板层由于和产品直接接触,板层的降温速率和温度,直接影响产品的冻干效果,对板层进行降温时间和最低温度测试,可间接反映产品的冻干温度[2]。
测试步骤:
(1)使板层温度为 20℃左右并记录板层温度和时间。
(2)设定板层温度为-40℃,并对板层进行降温。
(3)当板层温度降至-50℃时,记录时间。
判定标准:
(1)板层从 20℃降至-40℃的时间≤70 min。
(2)最低温度≤-50 ℃。
板层(冷媒)降温时间和最低温度测试结果如表 2 所示。
由表 2 可以看出,板层从 20 ℃降至-40 ℃的时间为 27 min,小于 30 min,且最低温度可达到-50 ℃以下,说明板层降温效果达到要求。
3.2.3 板层(冷媒)升温速率和最高温度测试
板层的升温速率和升温效果,会影响产品的升华和干燥效果,可通过对板层进行升温速率和最高温度进行测试。
测试步骤:
(1)使板层温度降至-40 ℃以下,记录温度和时间,并设定板层温度为 70 ℃。
(2)对板层进行加热,当温度升至 20 ℃时,记录温度和时间,并计算板层升温速率。
(3)继续对板层进行升温至 70 ℃以上,并记录温度值。
判定标准:
(1)板层升温速率>1 ℃/min。
(2)板层的最高温度≥70 ℃。
板层(冷媒)升温速率和最高温度测试结果如表 3 所示。
由表 3 可以看出,板层升温速率为 1.8 ℃/min,且最高温度超过 70 ℃,说明板层升温效果达到要求。
3.2.4 抽气所需时间和极限真空测试
测试步骤:
(1)对冷凝器进行降温,当冷凝器制冷至-45℃时,开启
真空泵,并记录开启时间。
(2)记录抽真空至真空度为 10 Pa 的时间。
(3)继续进行抽真空,并记录极限真空度。
判定标准:
(1)当冷凝器到达-45℃时,真空度从大气压抽到 10 Pa,所需要的时间≤30 min。
(2)极限真空度值≤1 Pa。抽气所需时间与极限真空测试结果如表 4 所示。
由表 4 可以看出,冻干机抽气用时 26 min,符合抽气时间小于 30 min 的要求,极限真空小于 1 Pa,该确认方法可真实反映冻干机抽真空性能良好。
3.2.5 系统真空泄漏率测试
当冻干机进行抽真空时,若系统有泄漏,将会影响产品冻干效果,对系统进行真空泄漏率测试,可以考察冻干机整体的泄漏状况,测试步骤如下:
(1)对冷凝器进行降温,使其降温至-40 ℃以下。
(2)当冻干箱加热至 40 ℃以上时,开启真空泵进行抽真空,使真空度到达极限真空,并停止抽真空,关闭中隔阀进行保压,记录开始时间和真空度。
(3)待 30 min 后,记录冻干箱真空度,并按照公式计算真空泄漏率。
系统真空泄漏率计算公式:
Q=△P× V/t Pa·m3/s;
Q:泄漏率;△P:压差(
P2-P1);V:箱体容积;t:所需时间;P2:30 min 后箱内真空度。
判定标准:真空泄漏率应≤0.005 Pa·m3/s。
系统真空泄漏率测试结果如表 5 所示。
由表 5 可以看出,系统真空泄漏率喂 0.0006 Pa·m3/s,远小于规定的 0.005 Pa·m3/s,说明系统运行抽真空后,箱体泄露量少,箱体密封性能好,可保证冻干工艺流程既定流程顺利完成。
3.2.6 板层温度分布均匀度确认
通过在冻干机板层上均匀放置温度监测探头,可以考察冻干机板层温度,从而反映实际生产中产品实际到达温度,测试方法如下[3]。
(1)选用 50 颗温度探头,平均分布于 10 层冻干机板层上(每层 5 颗,每层探头分布如图 1、图 2 所示),设定温度验证记录仪记录时间间隔为 1 min。
(2)启动冻干机,在空载的情况下进行板层热分布测试,温度测试点分别设置为-45℃、0℃和 45℃。
(3)在每个测试温度点温度稳定后,稳定记录 30 min。
判定标准:
(1)温度验证仪各探头温度的温差应<2℃。
(2)探头平均温度与系统显示温度温差应<2℃。
板层温度分布均匀度测试结果如表 6 所示。
由表 6 可以看出,在设置点-45 ℃、0 ℃和 45 ℃,温度验证仪各探头温度的温差均小于 2 ℃,探头平均温度与系统显示温度温差均小于 2 ℃,该性能测试方法可有效证明该冻干机各温度段板层温度均匀。
3.2.7 在线蒸汽灭菌功能与生物挑战性测试
测试方法:
(1)与板层温度分布探头布置相同,选用 50 颗温度验证探头放置冻干机内。
(2)设定灭菌温度为 121 ℃,灭菌时间为 20 min。
(3)运行冻干机在线灭菌程序,并启动温度验证系统记录冻干机内温度变化。
(4)在进行在线蒸汽灭菌测试的同时进行生物挑战性测试,用 10 支湿热灭菌生物指示剂放置于板层中间,灭菌完成后,取出,按说明书条件放置培养箱进行培养,另取 1 支不经过灭菌的指示剂作为阳性对照。见图 1、图 2。
判定标准:
(1)灭菌过程所有温度探头温度应大于 121℃。
(2)所有探头当中,最小 F0 值应大于 12。
(3)灭菌所需时间与灭菌曲线时间应一致。
(4)阳性对照应呈阳性,经过灭菌的生物指示剂经培养后应为阴性。
在线灭菌测试功能与生物挑战性测试结果如表 7 所示。
由表 7 可以看出,灭菌过程符合温度均大于 121℃的要求,各探头 F0 值均大于 12,且生物指示剂全部为阴性,可达到可靠的灭菌效果,冻干机灭菌性能符合要求。
4、 结论
通过对真空冷冻干燥机性能确认技术进行测试和研究,证明一系列确认方法有效,若在测试过程中出现个别项目不合格,需仔细查明原因,找出影响冻干机性能的具体原因,并再次进行测试确认,必要时还可以进行多次测试。
真空冷冻干燥机的性能确认方法和测试标准不止以上所述,可通过查找设备自身参数等因素进行适当调整,更换重要设备零件后需对真空冷冻干燥机进行再次确认,以确保各重大变更不会对设备造成严重影响,确保生产出质量合格的产品。
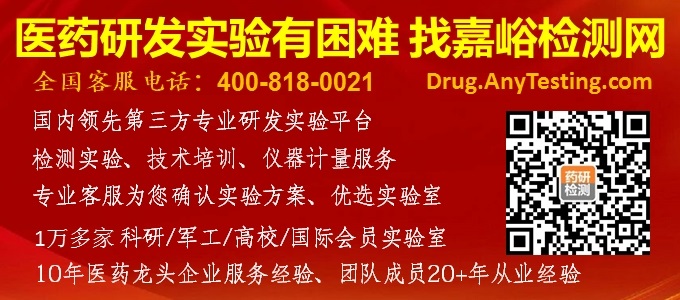