石油套管是油气开采过程中必不可少的结构部件,对钢材的强度、韧性、抗氢致开裂(HIC)、抗硫化物应力腐蚀开裂(SSC)等性能有很高要求[1,2]。随着浅层石油资源的逐渐枯竭,中国油气开采重点已转向中西部地质条件恶劣的酸性含硫化氢油气田,因而对石油套管钢的耐腐蚀性能提出更高的要求。微合金高强石油套管钢的抗腐蚀能力与生产过程的冶金缺陷密切相关,尤其是生产过程不可避免产生的非金属夹杂物[3,4]。国内外研究表明[5,6,7,8,9,10,11],非金属夹杂物与钢基体间的空隙部位常常成为氢陷阱,大量氢原子在此富集,当其数量达到某一临界值时,这些夹杂物的周围就会产生微裂纹,甚至造成钢在远低于其屈服强度时断裂。因此,必须控制非金属夹杂物的数量、尺寸、形态、偏聚、形变硬化程度等。HIC和SSC的产生与钢中硫化物和B类、D类夹杂物有密切关系。石油套管钢通常采用铝脱氧钙处理的生产工艺,脱氧产物Al2O3经钙处理后会被改性为熔点较低的钙铝酸盐(xCaO·yAl2O3),在良好的动力学搅拌条件下夹杂物大多数上浮去除,从而提高了钢水洁净度并减轻了由Al2O3造成的水口堵塞风险[12]。另外,钙还会与钢中的硫结合形成高熔点的CaS,从而降低链条状的MnS对套管钢抗蚀性能的影响[13,14,15]。尽管钙处理有诸多好处,然而控制不当同样会形成B类和D类硬质夹杂影响钢的耐蚀性能。
本研究涉及的110级石油套管钢是一种典型的高强度抗硫钢,主要用于制造含H2S的深井和超深井油气开采套管,目前中国只有极少数几个钢厂具备生产能力。某厂近两年该钢种φ87 mm(6.5 mm厚)薄壁管生产统计数据表明,其抗硫化物应力腐蚀A法检测合格率不足70%。分析认为主要与钢中夹杂物有关。为此本文借鉴前人关于稀土在钢中的应用经验[16]提出改善抗硫性能的理念。通过在VD后加入Ce-La合金取样分析中间包、铸坯和轧材样中夹杂物的变化规律,揭示稀土对高强抗硫石油套管钢夹杂物的改性规律。抗硫检测结果表明,试验炉次加稀土后抗硫化物应力腐蚀A法检测合格率提升到100%,取得了令人满意的效果。
针对稀土对钢的作用,李根等[17]概述了钢液中铈及其化合物的热力学行为,并预测了铈加入钢液后的稳定化合物类型及其变化规律。其针对TWIP钢的研究表明,随着铈含量升高,钢中夹杂物由Ce2O3向Ce2O3+少量Ce2O2S转变[18]。马钰等[19]研究了铈对55SiCr弹簧钢夹杂物的改性规律,表明铈加入后,首先生成大量小尺寸复合稀土夹杂物;随着反应进行,夹杂物逐渐长大、去除,其数量呈现减少趋势,但铈的添加量对钢中最终残留的夹杂物特性有显著影响。LUO Sen等[20]研究了铈对20CrNiMo齿轮钢夹杂物演化的影响,表明铈质量分数小于0.1%时,随着其含量增加,夹杂物演变规律为Al2O3 →CeAlO3 →Ce2O2S → Ce2O2S +CeS。WANG Li-jun等[21]利用稀土铈将弹簧钢中MgO·Al2O3尖晶石夹杂物改性为稀土夹杂物,黄宇等[22]基于FactSage 6.3的理论计算与试验观察,认为稀土铈对钎具钢中MgO·Al2O3夹杂物的改质顺序为MgO·Al2O3→ CeAlO3+MgO→ Ce2O3+MgO→ Ce2O3。WANG Hao等[23]在IF钢中加入稀土铈,使大尺寸、有尖角的团聚Al2O3夹杂物转变成尺寸为2~5 μm的球形或纺锤形复合稀土夹杂物。GENG Ru-ming等[24]研究了RH精炼过程中铈对铝脱氧钙处理钢中夹杂物的改性情况,发现钢液中液态Ca-Al-O系夹杂向(Ca-Ce-O-S)+(Ca-Al-Ce-O)系复合夹杂物转变。XIN Wen-bin等[25]研究了铈对含砷钢中夹杂物的影响,结果表明随着铈含量的增加,主要夹杂物依次由Al-Ca-O→Ce-S-O→Ce-S-O+Ce-S-As→Ce-S-As+Ce-As转变,且分别在铈质量分数为0.055%和0.095%的钢液中发现了Ce-S-As和Ce-As夹杂物。综上所述,尽管稀土在很多钢种中得以研究,然而针对不同钢种和作用目的,其作用机制和合理加入量并不相同。本研究涉及的110级石油套管钢工作在含H2S的深井或超深井环境中,抗硫性能是影响其服役寿命的关键因素,而抗硫性能与钢生产过程中产生的夹杂物密切相关。稀土具有调控钢中夹杂物特性的能力,而关于其对110级石油套管钢中夹杂物的调控研究未见文献报道,为此本文借鉴前人的研究经验提出了在其中添加复合稀土改性钢中夹杂物进而改善钢抗硫性能的研究思路并取得了显著效果。
1、生产工艺与检测方法
以30MnCr钢为代表性钢种,研究Ce-La合金加入对其中夹杂物的影响规律。共进行了两炉工业对比试验,在连铸生产的最后两炉(共连浇6炉)进行,其中一炉不加稀土,命名为方案A,生产流程为150 t电炉冶炼→LF钢包精炼→VD真空精炼→六流弧形圆坯连铸机→加热与轧管。电炉出钢时加铝进行沉淀脱氧,然后在LF造白渣脱硫脱氧,VD脱气后向钢水中喂300 m纯钙线,软吹15 min后进行浇注。另一炉喂同样的钙线后软吹8 min,之后调整氩气流量使其吹开渣面,加入用铁盒包装的110 kg Ce-La合金(其中w(La)≥19%,w(Ce)≥38%),再软吹10 min,对比分析钢中夹杂物的变化规律。该方案命名为B。
取样方案见表1。分别在两炉次浇注过程中大包余钢110 t(A1和B1)、80 t(A2和B2)时用锆质取样器在中间包内取样,并在铸坯(A3和B3)和轧材(A4和B4)上分别取样。
表1 取样方案
Table 1 Sampling scheme
在所取样品上钻屑,采用ICP (inductive coupled plasma emission spectrometer)电感耦合等离子光谱仪检测其中的Ce、La、P和As元素含量,用氧氮氢分析仪(TCH 600, LECO)测定O和N含量,其他元素含量采用光谱直读仪检测。另外,在所取不同工序的试样上分别切取10 mm×10 mm×8 mm的金相样品,磨抛后用Phenom Pro扫描电镜和JEOL JSM-6701F型场发射电镜并结合相应的EDS能谱仪观察钢中典型夹杂物的形貌和成分,并用EVO18夹杂物自动扫描分析仪分析不同工序钢样中夹杂物的数量、成分和尺寸。
2、试验结果与分析讨论
2.1 钢的化学成分
两种方案下铸坯的化学成分见表2,加Ce-La稀土合金后(理论加入量w(La)=0.0139%,w(Ce)=0.0278%)不同阶段钢中的稀土元素含量和收得率见表3。由表2可知,两炉钢成分接近,说明生产工艺控制稳定,这为加稀土后的对比提供了原料条件的基本保障。由表3可知,铈在各个阶段的收得率分别为57.5%、79.1%、54.0%和50.3%,相应地镧的收得率则分别为50.3%、71.9%、51.1%和41.0%。铈在各个阶段的收得率均高于镧的收得率,这可能和稀土元素自身的性质有关,也可能和加入的稀土量有关。有研究[26]表明,随着稀土加入量增加,其收得率提高。本研究的Ce-La合金中铈的质量分数为38%,远高于镧的19%,因而铈的收得率高于镧。
表2 铸坯的化学成分(质量分数)
Table 2 Chemical composition of the billet castings %
表3 方案B试样中Ce、La含量和收得率
Table 3 Content and yield of Ce and La in steel of case B %
方案B在方案A之后生产,B1取自开浇前期的中间包钢水样,此时中间包内有两个方案的混浇钢水,其w(Ce)和w(La)分别为0.016%、0.0070%;而B2取自浇注中期,中间包内已无混浇钢水,因而其稀土含量较B1有所增加,w(Ce)和w(La)分别达到0.022%和0.010%。由于中间包和结晶器均有去除夹杂物的功能,因此B3铸坯中的稀土含量较B2又有所下降。B4轧材中w(Ce)和w(La)分别为0.014%和0.0057%,较B3有所降低,可能是由于稀土分布不均匀、铸坯和轧材样的检测部位很难完全对应所致。
2.2 钢中典型夹杂物
2.2.1 方案A钢中典型夹杂物
方案A采用铝脱氧钙处理的生产工艺,在中间包、铸坯和轧材所取样品中观察到的夹杂物类型主要有Ca-Al(-Mg)-O、Ca-Al(-Mg)-O+CaS、CaS和TiN 4类,典型夹杂物形貌见表4,面扫描结果如图1所示。
由表4中Ca-Al(-Mg)-O夹杂物的形貌、成分并结合图1(a)和(b)面扫结果,该类夹杂物大多呈球形,各元素成分分布均匀,表明这类夹杂物多是在钢水中生成的液态夹杂物,其中的镁元素主要来源于耐材。
由表4中Ca-Al(-Mg)-O+CaS夹杂物的形貌、成分并结合图1(c)和(d)面扫结果,该类夹杂物大多呈球形或椭球形,各元素分布不均匀。图1(c)一侧为CaS,另一侧为Ca-Al(-Mg)-O,它是钢水钙处理时形成的CaS与Ca-Al(-Mg)-O夹杂物碰撞黏附形成;图1(d)是以Ca-Al(-Mg)-O为核心,外部包裹CaS,应为钙处理过程中或钢水冷却过程中CaS以Ca-Al(-Mg)-O氧化物为形核核心析出。纯CaS夹杂物在铸坯中大多呈球形(表4中A3),在轧制过程中被拉长(表中A4)。A1~A4样品中均检测到TiN夹杂,大多呈不规则形,其在凝固过程中析出并遗传到轧材中。
表4 方案A不同工位样品中的典型夹杂物形貌
Table 4 Morphology of typical inclusions at different stages in case A
图 1 方案A中典型夹杂物的面扫描
Fig. 1 Element scan mapping of typical inclusions in case A
(a)、(b) Ca-Al(-Mg)-O;(c)、(d) Ca-Al(-Mg)-O+CaS;(e) CaS;(f)、(g) TiN。
2.2.2 方案B钢中典型夹杂物
方案B加Ce-La合金后,在中间包、铸坯和轧材所取样品中观察到的夹杂物类型主要有:Ce-La-O(-S)、Ce-La-O(-S)+CaS、Ce-La-P-As和TiN 4类。典型夹杂物形貌见表5,面扫描结果如图2所示。
由表5中Ce-La-O(-S)夹杂物的形貌、成分并结合图2(a)和(b)面扫结果,该类夹杂物大多呈球形或方形。其一方面来源于钢中加入的Ce-La合金对Ca-Al(-Mg)-O夹杂物的改性,另一方面来源于Ce、La与钢水中O、S的直接反应。
由表5中Ce-La-O(-S)+CaS夹杂物的形貌、成分并结合图2(c)、(d)和(e)面扫结果,该类夹杂物大多呈球形或椭球形。根据元素分布不同分为两种类型,一类各元素分布不均匀,即以CaS为核心,外围包裹Ce-La-O(-S),如图2(c)和(d)所示;另一类各元素分布均匀,如图2(e)所示。其形成原因将在后文结合热力学计算结果进行分析。
由表5中Ce-La-P-As夹杂物的形貌、成分并结合图2(f)和(g)面扫结果,该类夹杂物大多呈方形,各元素分布均匀。HUANG Yu等[27]的研究表明,当铈质量分数大于0.025%时,钢中会有Ce-P和Ce-As夹杂物产生。由于本文中的铈理论加入量(质量分数)为0.0278%,大于文献中的临界值,且稀土加入钢液后是由局部扩散到整个容器中,局部区域内的铈含量会更高;另外镧的化学性质与铈相近,其加入量(质量分数)也达到了0.0139%,因而会形成Ce-La-P-As夹杂物。
B1~B4样品中均检测到TiN夹杂,大多呈不规则形。其中部分TiN附着在稀土夹杂物的外围或周边如图2(h)、(i)所示,部分独立存在如图2(j)所示。
表5 方案B不同工位样品中的典型夹杂物形貌
Table 5 Morphology of typical inclusions at different stages in case B
图 2 方案B中典型夹杂物面扫描
Fig. 2 Element scan mapping of typical inclusions in case B
(a)、(b) Ce-La-O(-S) ;(c)、(d)、(e) Ce-La-O(-S)+CaS;(f)、(g) Ce-La-P-As;(h)、(i)、(j) TiN。
2.3 钢中夹杂物的统计特征
用夹杂物自动扫描分析仪分别扫描磨抛后的A1~A4和B1~B4金相样品,扫描面积均为20 mm2左右。设定扫描的夹杂物最小尺寸为1 μm。统计夹杂物的数密度、类型和各类夹杂物的所占比例和平均尺寸,结果如图3所示。其中阴影和数字表示各类夹杂物所占比例,圆点和方点表示各类夹杂物的平均尺寸,表示各样品中所有夹杂物的平均尺寸。
图 3 钢中各类夹杂物所占比例与平均尺寸
Fig. 3 Percentage of different types of inclusions in steel and their average diameters
(a)方案A;(b)方案B。
对比两个方案夹杂物的统计特征,A1和B1的夹杂物平均尺寸相近,分别为2.4 μm和2.5 μm,但B1的夹杂物数密度低于A1,分别为13.16个/mm2和7.46个/mm2;A2和B2的特征与A1和B1类似。表明VD中加入目前的稀土量可使中间包内钢水的夹杂物数量减少,而夹杂物平均尺寸变化不大。数量减少意味着大多数稀土夹杂物在软吹过程和中间包中上浮去除。A3和B3相比,A3的夹杂物平均尺寸较B3小,分别为1.9 μm和3.1 μm,但A3的夹杂物数密度高于B3,分别为19.01 个/mm2和14.72 个/mm2;A4和B4相比,二者夹杂物平均尺寸相近,分别为2.3 μm和2.4 μm,但A4的夹杂物数密度小于B4,分别为16.94 个/mm2和19.80 个/mm2。
A2是中间包所取钢样,A3和A4分别是铸坯和轧材样。中间包的钢液到铸坯成型的过程中夹杂物还有机会被中间包覆盖剂和连铸保护渣继续吸附去除,使得A3中夹杂物的平均尺寸小于A2。经过轧制后,A4的平均尺寸上升,一方面是在轧制过程中部分夹杂物被拉长造成,另外轧制前的加热和后期的冷却过程也会导致部分夹杂物尺寸变大[28],尤其是TiN,其在加热和冷却过程中会出现回溶和重新析出长大的现象[28],因此A4和B4轧材中TiN夹杂物的尺寸均较相应铸坯中有所增加。对比两方案不同类型夹杂物所占的比例,方案A中主要是Ca-Al(-Mg)-O和Ca-Al(-Mg)-O+CaS夹杂物,其中Ca-Al(-Mg)-O夹杂物的平均尺寸与所有夹杂物的平均尺寸相近,且二者在不同工位的尺寸规律也相似,可见在方案A中该类夹杂物的影响是最大的,应重点关注该类夹杂物的控制。轧材A4中TiN的比例较其他样品高,可能和轧制过程中的保温制度有关。方案B的B1样品中Ce-La-O(-S)+CaS夹杂物所占比例最高,其次是Ce-La-P-As和Ce-La-O(-S);而B2~B4中Ce-La-O(-S) 夹杂物所占比例最高。B3中Ce-La-P-As夹杂物所占比例较其他样品高,B3来自于铸坯样,表明钢水冷却过程中会形成更多的Ce-La-P-As,因为冷却过程中P、As的偏聚更加明显。在B3样品中,Ce-La-P-As夹杂物的平均尺寸为3.7μm,在轧材B4中降为2.6 μm。B3到B4中Ce-La-O(-S)和Ce-La-O(-S)+CaS类型的夹杂物比例增加,可能的原因为:(1)部分夹杂物在轧制的过程中被轧碎,使得尺寸变小、数量增多;(2)所取轧材样和铸坯样检测位置不能完全对应;(3)轧制过程中Ce-La-P-As夹杂物回溶,其所占比例减小使得其他类型夹杂物所占比例相应变大。
综上所述,在110级石油套管钢生产过程中,于VD钙处理后加入当前试验量下的稀土La-Ce合金,可使中间包内钢水中的夹杂物数密度减小,夹杂物平均尺寸较未加稀土的工艺变化不大,均小于3 μm。尽管在铸坯凝固过程中会形成平均尺寸大于3.5 μm的Ce-La-P-As夹杂物,但轧制保温后这类夹杂物部分回溶,其平均尺寸也较铸坯中有所降低。另外,加稀土后形成的夹杂物大多为方形、球形、椭球形。
3、夹杂物形成机理的分析与讨论
3.1 方案A钢中夹杂物的形成机理
针对方案A,选用Factsage 8.2的Phase Diagram模块和FT oxid、FT msic数据库,设置计算温度为1600 ℃,钢水成分按表2中试样A3的基础成分,作Al-Ca平衡关系图,如图4所示。可以看出在给定铝含量下,随着钢中钙含量增加(图4中红线),夹杂物的转变路径为Al2O3→ CaO·6Al2O3→ CaO·2Al2O3→ 液态夹杂物(Incliq)→ Incliq+CaS→ Incliq+CaS+CaO。软件中液态夹杂物默认为CaO·Al2O3、12CaO·7Al2O3和3CaO·Al2O3。A3试样铝和钙质量分数分别为0.0255%和0.002%,即图中红点所在位置,因而形成的夹杂物主要为液态夹杂物Ca-Al-O,试验中检测到比例最大的夹杂物是Ca-Al-(Mg)-O(如图3(a)),与计算相符。其中个别夹杂物中所含的少量镁是由耐材侵蚀造成,计算时没有考虑侵蚀。另外,试验中也检测到大量的Ca-Al(-Mg)-O +CaS夹杂物,这是由于石油套管钢实际生产过程中,钙线喂入的区域钙局部浓度较高,超过了图4中红线与黑线相交处的钙浓度,因而会与硫结合形成CaS夹杂析出,然后与Ca-Al(-Mg)-O碰撞或黏附在一起从而形成如图1(c)和(d)所示的不同形貌的复合夹杂物。
图 4 方案A在1600 ℃下钢中Al-Ca平衡相图
Fig. 4 Equilibrium phase diagram of Al-Ca at 1600 ℃ in case A
3.2 方案B钢中夹杂物的形成机理
考虑到试验过程中使用的Ce-La复合稀土合金中铈占大多数,且铈在钢水中热力学计算的准确性已得到众多学者的证实[22,24,26],因此本计算中将镧含量折合为铈含量以简化计算过程。
选用热力学软件Factsage 8.2的Phase Diagram模块和Fact PS、FT oxid、FT msic以及SGPS数据库,计算温度设置为1600 ℃,钢水成分按表2中试样B3的基础成分,作Ce-Al、Ce-Ca平衡相图,并将表3中实测钢水对应的成分点置于图中,结果如图5所示。
图 5 方案B在1600 ℃下钢中平衡相图
Fig. 5 Equilibrium phase diagrams of steel at 1600℃ in case B
(a)Ce-Ca平衡相图;(b)Ce-Al平衡相图。
由图5可知,1600 ℃时,在不同的Ca、Al、Ce含量下钢中生成的夹杂物并不相同。当钙质量分数小于0.0015%时,钢水中不会生成CaO夹杂。随着钙含量的增加CeAlO3消失,夹杂物逐渐向CaO+CaS过渡(图5(a))。在B1~B4样品的Ca、Al和RE含量下,钢中存在的夹杂物都应该是CaS+Re2O3。图5中的CaS+Ce2O3实为CaS和Re2O3两相共存区,因计算时将La-Ce中的镧折合为铈。实测的B1-B4样品中的夹杂物大多是Ce-La-O和Ce-La-O+CaS,个别稀土氧化物中含少量硫,这和计算结果基本吻合。该类夹杂物形成的一种原因可能为:该钢种采用铝脱氧钙处理的生产工艺,钙处理后形成了Ca-Al(-Mg)-O液态夹杂物和CaS夹杂;当在随后的VD工位加入Ce-La合金后,由于铈和镧的活性更高,因而对前期生成的Ca-Al(-Mg)-O夹杂物进行了改质,Ce、La取代了其中的Al、Ca、Mg元素,与O、S结合形成Ce-La-O(-S)夹杂物。由于CaS的熔点高且较稀土硫化物稳定,原钢水中的CaS并未完全被Ce-La所置换,因而形成Ce-La-O(-S)+CaS复合夹杂物,如图2(c)和(d)。该类夹杂物形成的另一种原因可能是RE、O、S、Ca直接反应形成,如图2(e)所示。
为验证以上第一种猜测,选用热力学软件Factsage 8.2的Equilib模块和Fact PS、FT oxid、FT msic以及SGPS数据库,计算了钢中夹杂物含量随铈含量的变化规律。设置计算温度为1600 ℃,钢水成分依然按表2中的B3,计算结果如图6所示。
图 6 1600 ℃下钢中夹杂物含量随铈含量的变化
Fig. 6 Amount of formed inclusions against Ce content in steel at 1600 ℃
(a)夹杂物含量随铈含量的变化;(b)图(a)中红框区域放大图。
由图6可知,当铈质量分数小于0.004%时,钢水中主要是Ca-Al-O液态夹杂物。随着铈含量增加,钢水中的液态夹杂物减少,逐步转变为其他类型夹杂物。当铈质量分数达到0.0040%和0.0078%时,依次析出了CaS和CaO。当其质量分数继续增加到0.0091%时,钢中的液态夹杂物完全消失并开始有CeAlO3生成;但当Ce质量分数达到0.0096%时,CeAlO3完全消失,同时开始生成Ce2O3;当Ce质量分数达到0.0121%时,钢水中的CaO夹杂物也完全消失,只剩CaS和Ce2O3。以上热力学计算结果表明铝脱氧钙处理后再加入稀土,钢中夹杂物的演变顺序依次为Incliq(Ca-Al-O)→CaS+Incliq→CaS+CaO+Incliq→CaS+CaO+ReAlO3+Incliq→CaS+CaO+ReAlO3→CaS+CaO+ReAlO3+Re2O3→CaS+CaO+Re2O3→CaS+Re2O3。以上研究同样表明,当钢水中加入稀土后,其会改质由钙处理形成的Incliq液态夹杂物从而形成RE-O和CaS夹杂物,它们在钢中或单独存在或以复合形态存在(图2(c)~(e))。
为证实钢水中Ce-La-O(-S)和Ce-La-O(-S)+CaS夹杂物的第二种形成机理,即由RE、O、Ca、S直接反应形成,采用经典热力学计算了1600 ℃下Ce反应产物的Gibbs生成自由能,其中[Ce]、[Al]、[O]、[S]等元素的活度由Wagner模型计算得出,见式(1)。元素间一阶相互作用系数见表6[23,24,29,30,31]。
式中:ai为组元i的活度;w(i)为组元i的质量分数;eij为一阶相互作用系数;i,j为组元i和j。
表6 组元间一阶相互作用系数表
Table 6 First-order interaction coefficients of the elements
表2中给出的T[O]为钢中总氧含量,根据铈加入前钢中铝含量和Al-O反应平衡,根据式(2)计算钢中溶解氧含量:
式中:ΔGθ为标准Gibbs自由能,J;T为温度,K 。
其中Al2O3夹杂物的活度以CaO•Al2O3中Al2O3活度0.64[33]进行估算,计算得出钢中溶解氧质量分数为0.00025%。加稀土合金后,1600 ℃下钢水中可能发生的反应(式(4)~式(10))见表7[17,31,32,34,35]。根据式(11)代入Ca、S、O、Al活度求得各反应的Gibbs自由能与铈含量的关系如图7所示。可以看出,在当前钢水条件下,Ce2O3的Gibbs自由能低于CaO和Ce2O2S的自由能,因此在钢水中更易形成Ce2O3夹杂物。生产中钢水采用了钙处理,氧与铈结合后会使钢水中的氧降低、钙增加,而CaS的Gibbs生成自由能又低于Ce2S3、Ce3S4和CeS,因此钙会与硫优先结合形成CaS。
表7 1mol 铈在铁液中反应的标准Gibbs自由能
Table 7 Standard Gibbs free energies of 1mol Ce reacted in molten iron
式中:∆G为Gibbs自由能,J;R为气体常数,8.314 J/(mol·K);Q为化学反应的产物与反应物的活度熵。
图 7 1600 ℃钢液中不同化学反应的Gibbs自由能
Fig. 7 Gibbs free energy of various chemical reactions in liquid steel at 1600 ℃
综上所述,针对B1~B4样品中占绝大多数的Ce-La-O(-S)和Ce-La-O(-S)+CaS夹杂物,以上两种形成机制均可能存在。夹杂物演变过程可总结如图8所示,铝脱氧后的钢液经钙处理首先形成Ca-Al-(Mg)-O和Ca-Al-(Mg)-O+CaS类型夹杂物,加入稀土后由于稀土的活性高于Ca、Al等元素,因而稀土可置换这些元素形成RE-O-(S)类和RE-O(-S)与CaS的复合夹杂物,即通常所说的夹杂物改质。复合夹杂物有的各元素分布均匀,有的是CaS析出在RE-O(-S)上面。另外,稀土也可和钢水中溶解的[O]、[S]、[Ca]直接反应形成以上稀土夹杂物。针对钢中检测到的少量Ce-La-P-As和TiN夹杂物,前者主要是由磷和砷在凝固过程中偏析从而与稀土结合形成,由于其偏析量不好估算,在此不做热力学计算。该类夹杂物在许多钢种中都存在[25,27,36,37]。形成该类夹杂物可以减轻磷和砷在晶界偏聚的危害,但要控制其尺寸不能过大[38],否则会对钢的疲劳和冲击性能造成不利影响。TiN夹杂通常是在凝固过程中析出。钛和氮在高温钢水中溶解度较高,一般不会形成TiN,但随着凝固过程进行,其溶解度迅速下降,当其活度积超过TiN的饱和活度积时就会以TiN形式析出[39,40]。减少其析出的方法主要是控制原料中的钛和氮以及冶炼过程中的二次氧化[41,42]。
图 8 加稀土后夹杂物的演变过程
Fig. 8 Evolution process of inclusions in steel with the addition of rare earth
3.3 加Ce-La合金后对钢抗硫性能的影响
以上试验中检测到的夹杂物均比较细小,其中轧材A4和B4中夹杂物平均尺寸分别仅为2.3μm和2.4 μm,它们对钢疲劳性能的影响都较小。针对高强石油套管钢,抗硫性能是其最重要的指标之一,为此进行了抗SSC性能的NACE TM 0177-2005标准试验方法中的A法检测。
A法即在室温下,材料在H2S腐蚀环境和拉伸应力共同作用下的抗开裂试验,通过断裂时间来确定材料抗环境开裂的敏感性。试样在饱和H2S溶液内加载规定载荷(最小屈服强度为85%)720 h后未发生断裂失效被视作检测合格。采用A法对比测试了加和不加Ce-La合金所生产的110级φ87 mm (6.5 mm 厚)的薄壁管的抗SSC性能,各试验8个样品,结果表明加稀土的调质管试样100%检测合格,而未加稀土的有3个样品断裂,合格率仅为63%,可见加稀土后套管的抗硫性能显著提高。需要说明的是,这只是针对本次试验的检测结果,进一步的抗硫试验验证还在进行中。
众多研究[4,43,44,45,46,47]表明,钢中Al2O3、钙铝酸盐及沿轧制方向延长的MnS均容易成为氢陷阱造成氢致裂纹和硫化物应力腐蚀开裂。不加稀土的套管钢中夹杂物主要是Ca-Al(-Mg)-O和Ca-Al(-Mg)-O+CaS类型的钙铝酸盐,它们均易成为氢陷阱,导致氢原子富集。当氢原子数量达到某一临界值时,就会在夹杂物周围产生裂纹,使钢的抗硫化氢应力腐蚀性能下降;而加Ce-La合金后,尽管钢中夹杂物的平均尺寸和数密度较不加Ce-La变化不大,但夹杂物类型由原来的钙铝酸盐转变为RE-O(-S)。RE-O(-S)夹杂物的物理性质与钢基体较钙铝酸盐和氧化铝夹杂更接近[45,47],因而受到外力作用时不容易因应力集中形成氢陷阱,从而改善了钢的抗硫化氢应力腐蚀性能。另外,这类夹杂物还结合了一定的硫,从而减少了链条状MnS的析出。
4、结论
(1) 在La、Ce质量分数分别为0.0139%、0.0278%条件下,添加Ce-La合金具有显著改性110级高强度石油套管钢中夹杂物的作用。改性前夹杂物主要为Ca-Al(-Mg)-O、Ca-Al(-Mg)-O+CaS、CaS和TiN,改性后前三类变为Ce-La-O(-S)、Ce-La-O(-S)+CaS和Ce-La-P-As。
(2) 当前的Ce、La试验加入量可使中间包内钢水中的夹杂物数密度减小,夹杂物平均尺寸较未加入变化不大,但在铸坯冷却过程中会形成平均尺寸大于3.5 μm的Ce-La-P-As夹杂物。
(3) 热力学计算表明,加La-Ce合金后钢中夹杂物的演变顺序为


(4) 抗SSC性能的A法检测结果表明在110级套管钢冶炼过程中加Ce-La合金可显著提升套管钢的抗硫化物应力腐蚀性能,这为深井、含H2S油气田开发用钢产品(管线、套管、储油罐等)提供了潜在的应用前景。
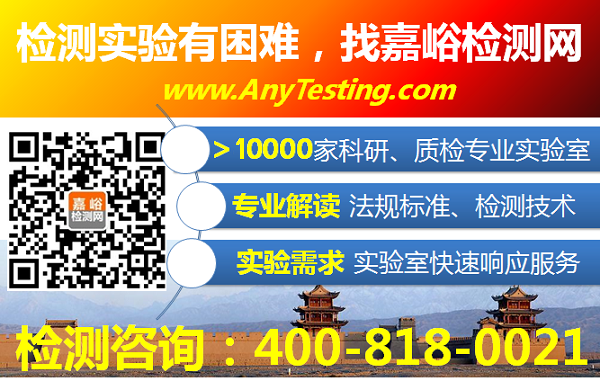