新能源汽车行业由“油改电平台”向“纯电动平台”的转变后,动力电池作为纯电动新能源整车中质量最大、成本最高的核心部件,对整车续航里程、碰撞安全性、行驶性影响更加凸显。以动力电池为主的全新电动平台带来了轻量化、智能化、网联化等诸多方面的改善,集成技术在其中的重要性愈加凸显,本文从动力电池与整车在结构、热管理、高压电气系统、低压控制系统集成方面,论述了新一代动力电池与整车创新集成的主要发展方向及挑战。
在新能源行业蓬勃发展的初期,各家OEM 发布了大量“旧瓶装新酒”的油改电新能源车型,因其产品延续着传统油车的空间布局和造型设计,电池系统在整车的布局处处受限,产品力低下,用户体验不佳。随着以特斯拉为代表的新势力“全新的智能化电动车平台”发布,匹配着一代电池技术,在全球范围内快速掀起了一场全新的绿色工业革命。在这种原生纯电动车基础上,电池组得以更高效、规整的安装在最理想的空间位置,三电系统可以更合理的布局,整车的电子电气架构及热管理设计实现了更高效的集成,使得车辆的能效、续航、智能化等维度产品力极大加强。据中国汽车工业协会统计,2021 年我国新能源汽车全年产销两旺,销售完成 352.1 万辆,同比增长 1.6 倍,连续 7 年位居全球第一,整个新能源汽车产业正处于技术变革驱动、生态重塑转型的关键阶段 。我国历来重视新能源产业的布局与发展,在这次变革中涌现出了一批优秀的自主研发设计的优秀企业,诸多创新技术引领着行业发展方向,其中动力电池作为电动汽车的核心部件,其性能优劣直接决定了整车的成本、续航、安全可靠性、使用寿命等各类指标。
目前主流液态锂离子电池材料技术经历过去几年的快速发展,能量密度的提升与成本下降已经进步相对稳定的发展阶段,动力电池与整车集成效率进一步提升可以为整车带来显著的轻量化、节能化、智能化及低成本边际效益。多个研究机构和企业近几年重点研究并发布了 pack 级或系统级的新技术,特别是在如电池轻量化、热管理集成化、高低压系统集成化等集成化方面取得诸多创新的技术进步。另外电池本身作为机械、化学、热力学、电气耦合的复杂集合零部件,集成技术发展方向将涉及更精密的尺寸控制,多功能合一、空间共享、化繁为简等多维度更精细化的设计平衡与跨界融合。
结构集成
动力电池结构集成指通过车辆的结构件或功能部件与动力电池进行结构共用、功能融合,以达到减少零部件总数,减少空间,降低成本并能提升整车强度与实现更高效的热管理性能的集成技术。目前动力电池行业主流技术为 CTP(Cell to Pack,电芯到电池包)技术,有向 CTC(Cell to Chassis,电芯到底盘)技术演进的趋势,如图 1 所示。下面具体介绍 CTP 技术和 CTC 技术。
图1 电芯到底盘的成组路径
CTP 技术
CTP 技术由宁德时代在 2016 年已有第一代商用车启动应用,2019年下半年乘用车推出,指电芯跳过模组,直接集成在电池包中,在技术层面实现了两个维度的升级。一是结构件集成效率提升,取消了模组结构件,采用电池包结构梁承载;二是功能融合提升,水冷板与底版共用,电池包上盖自带隔热保温功能。使得系统体积利用率提升、系统能量密度提高、零部件数量减少,进而降低了成本。
CTP 技术经历了几代发展,目前可将箱体结构件、加热装置、冷却装置、高压保护装置等高度集成,Pack 能量密度可达 230Wh/kg,比传统 Pack140Wh/kg 提升 60% 以上。
如图 2 所示,宁德时代第一代 CTP 通过采用虚拟大模组,端板结构等技术,提升了Pack 集成化程度,能量密度可达到 180Wh/kg 以上;第二代 CTP 通过 Pack 下箱体分区设计,去除端板结构,同时可兼容 NP 技术(不热扩散技术)和 AB 电池等,能量密度可达到 200Wh/kg 以上;第三代 CTP 技术通过水冷版侧置,即起到隔热功能,又加强了系统的冷却能力,使得高倍率快速充电成为可能,能量密度可达到 250Wh/kg 以上,计划于 2023 年量产。
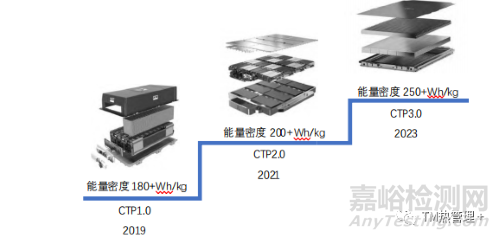
图2 宁德时代CTP技术演进
宁德时代第三代 CTP 技术,称为麒麟电池。其取消横纵梁、水冷版、隔热垫原本各自独立的设计,集成为多功能弹性夹层,内置微米桥连接装置,同时具备支撑、水冷、隔热、缓冲四大功能;此外麒麟电池电芯排列采用倒置方式,开创性的让多个模块共用底部空间,将结构防护、高压连接、热失控排气等功能进行智能分布。宁德时代公布的最新参数表明,体积利用率达 72%,能量密度 255Wh/kg,同时快充性能达到 10 分钟充电 10% ~ 80%SoC 的能力。
图3 宁德时代麒麟电池内部结构
图4 特斯拉CTC结构图
CTP 技术的优势显而易见,但随着集成效率的逐渐提高,在高压安全、热管理、采样及算法控制方面给设计、制造带来了巨大挑战。具体有:(1)结构件采用高强铝型材,挤压、焊接工艺;(2)水冷板设计、水道流向、水流支路流量及制冷量分配;(3)电池包内部温度与外部环境温度隔离设计;(4)电气间隙、爬电距离、绝缘设计匹配;(5)电芯采样及控制精度,绝缘设计及检测等。
为了应对以上挑战,需要电池厂家具有很强的开发验证及生产制造能力,随着车厂逐渐重视电池系统和整车匹配技术,行业上将目光投向 CTC 技术,希望通过 CTC 能进一步提升车辆的整体性能。
CTC 技术
电池包技术从 CTP 发展到 CTC,零件的外形、材质、组合形式等都伴随电池集成技术的进步发生改变,整体的方向是一体化、集成化。在乘用车和商用车上,都有新一代的产品发布。
乘用车CTC技术
2020 年 9 月,特斯拉发布了与 4680 圆柱电芯匹配的 CTC 技术,引发了行业关注。电池上盖与车身地板集成为一个部件,车内座椅直接安装在地板上。为车内增加了 10mm高度空间。从结构原理上看,其电芯底托板、电芯布置均为 CTP 技术,只是在电池包上盖上做了集成,特斯拉称可为车辆降低 10% 车重,减少 370 个零件,单位成本下降 7%。2022 年 4 月和 5 月,零跑汽车和比亚迪汽车发布的 CTC 和 CTB 技术原理与特斯拉如出一辙,称可通过电池包结构件与车身结构件融合,提升车辆扭转刚度。
商用车CTC技术(或称MTC、MTV技术)
商用车如客车、卡车等,一般为大电量(电量 200kWh~450kWh)设计,采用多个电池包通过串并联得到所需电压和电量,系统设计复杂,通过支架安装,导致空间利用率低。
以客车为例,现有电池安装在车辆下部,如图 5a,导致人员站立位置有台阶,人员上下车辆不便。新一代电池安装在车辆顶部,如图 5b,电池采用模组到车辆的集成方式,与车辆一体化设计,体积利用率提升 40%,重量能量密度提升 10%,并可帮助整车减重150kg。
综上所述,CTP 技术已被广泛应用,通过 3 代技术的迭代创新,在乘用车上续航已可突破 1000km。CTC 技术目前处于快速发展阶段,乘用车厂家发布的 CTC 不约而同的采用了电池上盖与车身地板集成的方式,与真正意义上的 CTC 还有较大差距;商用车的CTC(MTV)技术,应用优势明显,发展前景广阔。
热管理集成
随着新能源汽车不断向高能量密度、高能量效率转换和高集成度发展,三电系统(电池、电机、电控)的热管理需求与日俱增,已经关系到新能源汽车的整体安全和效率问题,同时新能源车辆的冬季的里程焦虑与安全事故频发一直是阻碍行业发展的痛点问题。在传统燃油车中,由于冬季可以采用发动机余热进行供暖,车载空调仅需考虑夏季制冷应用即可,但对于纯电动汽车而言,发动机余热的缺失导致车辆冬季供暖的需求尤为紧迫,另外环境温度对电池的性能指标有显著影响,温度过高或过低不但是驱动力电池的性能指标大幅度降低,对使用寿命和安全系数也是有较大危害,因而如何更高效的热管理系统至关重要,促进了一体化集成式热管理系统的提出、升级和演化。
集成式热管理技术研究现状
现阶段新能源汽车热管理系统正经历从常规单冷空调技术到热泵空调技术的系统架构转变升级的过渡阶段。热泵空调可以简单类比我们平时抽水的水泵,两者概念意思相同,热泵空调工作过程并不只会搬运热量,夏天的冷气同样可以,不过相比单冷空调,其成本更高。
新能源汽车传统的热泵空调技术主要由乘员舱热泵空调机组,电池专用热管理机组及电机电控热管理机组三套分布式系统共同构成;乘客舱的温控主要依赖热泵机组来源于空气的热量进行供暖 / 制冷,考虑到环境温度对热泵机组系统的效率影响,在较低温度需要给乘客室升温时,需配合 PTC 供暖;电池、电机电控则依赖于各自独立的专用热管理机组供暖 / 制冷。为了进一步提高热管理效能与整车空间利用率,把空气、电机电控和电池的余热废热更高效的耦合利用,集成式的三源热泵技术是目前行业内整车热管理术重点研究的解决方案方向之一。
三源热泵整车热管理集成方案
利用热泵、回收、Free-Cooling &Heating、超级阀及模糊控制技术实现三电系统与空气之间废热转移 / 转化和低品质热的提升对驾驶室和电池进行加热或者冷却,大幅减少车辆系统 PTC 加热的电量消耗,解决或者缓解电动车冬天里程衰减的问题,并且已经在众多商用新能源卡车上配套使用。三源热泵系统根据运行模式和温区的不同,热泵的热源可以在:电机电控,电池及空气间自由切换。针对新能源车辆在使用的不同工况,均可以匹配对应的控制策略,使效率达到最优。图 6 列举了冬季低温驾驶模式下三源热泵的工作原理:外界环境温低、驾驶室座舱需要加热、电池需要加热、电机电控需要冷却。
图6 三源热泵系统冬季驾驶工况工作原理示意图
新能源汽车热管理集成技术的发展趋势是将乘客舱的舒适性与三电系统的精准温控要求进行深度耦合。随着电池系统热管理界面的设计将与整车耦合交集越来越深入,新一代绿色制冷剂应用、电池整车热管理功能一体化、BMS 与整车热管理控制智能化将成为未来热管理集成系统的关键研究课题。
高压电气系统集成
新能源汽车由众多高压部件组成。随着新能源汽车的发展,高压电气集成是节省整车空间、提高产品可制造性、实现降本的必要手段。同时在电气集成度逐步提高的进程中,也需要重点关注电气系统的效率、安全性、可靠性和便捷性。目前高压电气集成化推进的主要方向是子系统集成及零部件集成。
子系统集成
新能源汽车关键零部件主要有整车控制器(VCU)、电池及电池管理系统、高压配电箱(PDU)、驱动电机、电机控制(MCU)、减速器、高低压电源转换器(DCDC)、车载充电器(OBC)、加上客车用的气泵控制器、油泵控制器等,如下图 7 所示。
图7 新能源汽车关键零部件多合一组合图
随着新能源技术的不断推广与运用,新能源部件由简单集成向高度集成化发展,多合一集成化电驱动系统在电能转化效率、机械空间紧凑化、线束精简化、成本等方面具备优势。目前新能源部件集成化主要可以分成两条路线:
一条路线是电驱动系统和高压电附件独立集成。电驱动系统根据驱动电机、减速器、电机控制器的不同集成组成出常见二合一或三合一。高压电附件根据低压电源转换器、车载充电器、高压配电箱、气泵控制器和油泵控制器的不同集成组成出常见二合一、三合一或五合一。
另一条路线是电驱动系统与高压电附件高度组合集成,常见的有二种方式:第一种是电机控制器、高压配电箱、高低压电源转换器、车载充电器集成四合一;第二种是电机控制器、高压配电箱、高低压电源转换器、气泵控制器和油泵控制器五者集成五合一。
随着新能源技术的不断创新、融合,市场推出更高集成度的七合一电驱动系统(如下图 8),该系统直接集成了电机控制器、驱动电机、减速器、高低压电源转换器、车载充电机、高压配电箱和电池管理系统等七大部件,实现了机械部件和功率部件的深度融合。
图8 电驱动系统七合一
为了更进一步提升集成度设计电驱动系统八合一(如下图 9 所示)近期也发布于市,其融合了驱动电机、驱动电机控制器、减速器、高低压直流转换器(DCDC)、双向车载充电器(OBC)、高压配电箱(PDU)、电池管理器(BMS)、整车控制器(VCU)等八大部件为一体。系统整体功率密度提升近 20%,重量和体积降低达 15%,综合效率可实现89%。
图9 电驱动系统八合一
不论电驱动系统与高压电附件采用独立集成还是高度集成方案,均在一定程度上实现了降本增效,并进一步提升了产品安全性和可靠性。但高压电气集成化也存在结构、电气和控制策略方面的难点。
对于结构方面,高压集成方案通过一体化压铸、焊接和机械连接等工艺形成,需要解决轻量化、强度、散热等问题。对于轻量化和结构强度方面,可以通过三个方面实现:一是在材料方面采用高强度钢、铝合金、镁合金、碳纤维增强复合材料等新材料的运用;二是在结构上采用薄壁化、中空化,复合化来实现轻量化,增强结构强度;三是在加工工艺上采用摩擦焊接、超声冲击处理等方式。对于结构散热,可以采用同侧化或同层次、低扬程设计,提升流道结构流畅性和换热能力结构设计,尽可能减少系统流阻,并在结构和空间上实现与其它部件隔离,减少热传递和热辐射对其它部件的影响。
对于电气方面,电气部件(特别是功率部件)工作时各自会产生电磁场,集成设计因时空上的交集容易引发干扰,集成化程度越高,电磁兼容性(EMC)问题就越突出。EMC 问题可以从 EMC 产生的三要素(源头、路径、设备)进行阻断和削弱。对干扰源头通过隔离、滤波处理抑止,对传播路径通过屏蔽、滤波和接地处理进行切断,对于设备通过接地、硬件扩频等方式降敏、阻隔处理。
对于控制策略方面,在提高集成系统总体能效,提高部件工作于高效区间占比方面是控制的难点,故可以从三个阶段着手:首先从高压部件设计或选型着手,尽可能使高压部件额定电压基本一致;其次,根据电池、电控和电机性能特性进行典型工况、环境条件下的仿真和测试优化,使系统获得最佳匹配;最后,引入自学习算法,根据用户使用工况、使用习惯、运行环境条件、系统自学习制定最佳的控制策略和控制方法,实现因人而异,精准施策,最大程度上降低能耗,提升车辆使用经济性。
全新的纯电动平台引入了很多新的电气零部件,零部件的零部件的集成化趋势越来越清晰,典型的高压零部件集成包括:高压连接巴片与电芯电压采样线集成、手动维护开关(MSD)与熔断器集成、熔断器 + 继电器集成、高压连接器集成等,这类集成能够有效的带动零部件成本的降低、安全可靠性提升,并为智能化制造奠定了良好的基础。
高压连接巴片+电芯电压采样线集成
高压连接巴片 + 电芯电压采样线集成较传统的模组设计方案,减少了模组生产过程中巴片和高压采样线焊接的工序,从而避免了工序中的 particle 产生。另外由于巴片与采样线集成性,也提高了电芯采样的稳定性。在电池包的全生命周期中,电芯会随着容量衰减、产气使其内部膨胀力增大,导致电芯出现相对位移,拉扯高压连接巴片和电芯电压采样线。故在前期的设计环节,需要对电芯全生命周期的膨胀力及相对位移量进行计算,预留足够的安全间隙,保障高压连接巴片和电压采样线全生命周期的可靠性。
图10 高压连接巴片集成电芯电压采样线示意图
手动维护开关(MSD)+熔断器集成
手动维护开关(MSD)+ 熔断器集成较非集成设计,可以节约大量的布置空间,有助于产品进一步提升体积利用率。熔断器的温升对其寿命的影响很大,在过流条件下会产生大量的热,集成之后存在热量无法散发的问题。产品设计的时候,需要考虑熔断器散热。主要的散热方式有:(1)熔断器接线柱导电面积做大,加快散热;(2)MSD 外壳选用铝外壳,内部填充导热材料加快熔断器散。
图11 手动维护开关(MSD)集成熔断器示意图
熔断器+继电器集成
熔断器 + 继电器集成方案可以同时实现继电器的功能(断高压,且可恢复)和熔断器的功能(异常状态下快速、安全的切断高压)。在实现体积利用率提高的同时还具备智能化的通断控制,根据整车提供的指令(如碰撞、热失控信号),实现毫秒级的快速断高压。由于带电的切断,会影响整车其他部件的正常使用,可能存在一定的行车安全隐患,故对于断高压的判定逻辑,需要结合整车的控制策略共同制定。
图12 继电器集成熔断器示意图
高压连接器集成
传统高压连接器为单 PIN 设计,以新能源电池系统中的高压盒为例,通过将所有高压接口,由一个集流排 + 多个格兰头的形式进行集成,可以大大节省连接器的布置空间,同时起到一定的降本。集成高压连接器需要考虑将多个不同电气特性的高压连接器集成在一个面板中,需要考虑预留足够的爬电距离和电气间隙,同时要保障结构空间的最大利用率。
图13 高压连接器集成示意图
应用在电动汽车的系统不断追求高体积利用率和能量转换率。随着各高压零部件和子系统可靠性提升,高压子系统集成和高压零部件集成已大批量的应用到各类车型,而子系统已越来越多从四合一、五合一往七合一、多合一集成化。高度的集成化同步提高了大系统的可靠性,降低整体成本。
低压控制系统集成
在汽车“新四化”(电动化、网络化、智能化、共享化)发展趋势下,传统的分布式汽车电子电气架构由于其通讯架构的复杂 性、 电子控制单元(Electronic ControlUnit,ECU)的多样性逐渐暴露出诸多问题,例如:无法实现多路实时高速通讯、高实时控制,ECU 数量过多甚至达到瓶颈,总线长度、接口数量和成本无法有效优化减少,同时线束连接故障率占比高。因此设计一个高性能、高集成、高可靠且功能齐全的硬件处理器(域控制器)成为了一个新的发展趋势,走在前沿的各大汽车厂商开始尝试将一些功能相似、分离的 ECU 集成到一个域控制器平台上。而动力电池系统的核心部件电池管理系统(Battery Management System ,BMS),也根据整车不同的域控制器架构需求集成在不同的域控制器中。
电动汽车域控制器及电子电器架构发展现状
2017 年德国博世公布其在整车电子电气架构方面的战略图,将整车电子电气架构的发展划分为三大类:分布式汽车电子电气架构、集中式域融合架构、中央集中 + 云计算架构方案,并提出经典的五域集中式电子电气架,将汽车功能划分为 5 个域:动力域、底盘域、车身域、座舱域、自动驾驶域。在电动汽车领域,随着汽车智能化需求的不断提升,各大汽车厂商进一步提出域融合产品解决方案。
电池管理系统的域集成解决方案
目前电池管理系统相关的整车域控集中技术正处于集中式域融合架构向中央集中 +云计算架构发展阶段,电池管理系统(Battery Management System,BMS)可根据整车不同域控架构需求集成在底盘域控、动力域或网关、智能驾驶域控或网关中。现有如下 3种不同解决方案。
方案一:BMS 保持独立,BMU(BatteryManagement Unit,BMU)集成了整车其他功能部件,如 VCU、MCU、网关等,同时域控制器置于 Pack 内部。该方案因降低了Pack 能量密度、域控制器不便维修等问题,市场推广应用少。
方案二:动力电池仅采样模块留在 Pack内部,其余功能移出 Pack,BMU 可根据需要和 VCU、MCU 等整车其他部件集成域控制器,目前市面上,部分商用车或 CTC 项目上已开始尝试该种解决方案。该集成方案具备如下技术优势:① 可将电池、电机、电控等多个低压控制模块在物理上实现集成,实现至少 15% 以上的物料减少;
②不同控制器的功能模块得以优化调整:整体代码量减少 >10%,部分响应处理缩短>20ms;
③支持基于单一内核的功能更新 OTA;
④有利于 Pack 能量密度提升,并提升了域控制器的可维修性。
方案三:在方案二的基础上,动力电池内部保留电芯采样模块、动力电池继电器驱动模块、数据存储模块等基本功能部件,其余功能移出 Pack 与整车其他部件集成域控制器,实现 BMU1(电池端)+BMU2(整车域控端)的双层架构。目前市面上,该方案逐渐成为乘用车的主流解决方案。
随着中央网关及高性能处理器等软硬件设备的发展进步,为智能网联电动汽车的 EE架构革新带来新的动力。而适用于智能驾驶的车载电脑 + 云计算 EE 架构将是今后各大车企研究的重要方向。以此同时,动力电池企业,也根据整车不同域控制器架构的需求,将 BMS 集成到整车不同域控制器模块中。
结语
本文主要介绍了目前行业内整车结构、热管理、高压电气系统及低压控制控制集成方面最新的整车一体化集成的技术与发展趋势,诸多先进技术也已逐步商用落地,技术变革会为消费者带来全新的乘驾体验。如何在电池包有限空间内做好各模块功能的协同集成,如何将电池包与整车更高层级的进一步的系统融合仍将是未来行业的重点创新发展研究方向,集成技术持续融合创新能够给新一代智能网联纯电座舱带来源源不断的成本下降与性能提升源动力,进一步推进全面电动化的时代的到来,助力汽车行业“碳达峰”“碳中和”目标的早日实现。
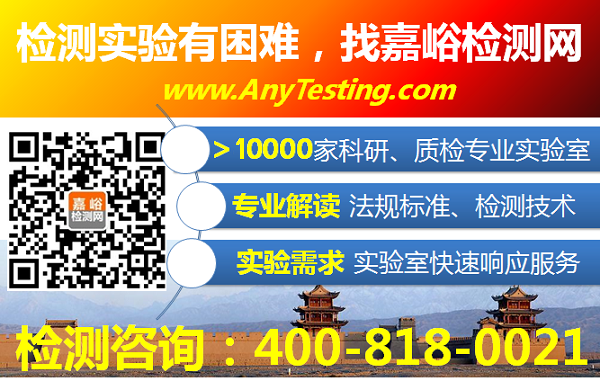