摘 要: 焊接工艺是汽车白车身生产过程中经常用到的工艺,其在汽车四大生产工艺中占据重要位置,也是衡量一个车企整体生产工艺水平的重要标志,其焊接质量的好坏不但决定着汽车的安全性能,也与汽车外观的美观性息息相关。其中在整车个白车身焊接过程中,点焊工艺又是应用最多的一种焊接工艺,本文通过在汽车车身点焊工作过程中所学习到的一些焊接方法和部分专业知识,从点焊的工艺特点、质量控制手段、质量检测手段等方面来探讨和分析白车身点焊过程中其外观焊点的质量控制手段及方法。
1 引言
随着人们对汽车产品的安全性和美观性要求越来越高,这就要求车企不但在整车性能和外观上提升竞争力,更要在细节生产工艺上提升制造水平,其中汽车焊点的焊接质量控制上要更要精益求精。因此作为影响汽车安全和美观性能之一的点焊工艺,其焊点质量和美观性控制的好坏一定程度上影响着用户对整车品牌的选择性。下面将从点焊的质量控制要求,点焊焊点常见的缺陷,点焊焊点质量评价方法等方面来简要阐述车身焊点的质量控制手段。
2 车身外观焊点质量要求
2.1 点焊的原理
将待焊的金属零件交叠搭接起来,置放于上下铜电极之间,然后施加一定的电极压力,将两个或三个零件压紧。然后施加一定的电流,电流流经焊机机臂、电极以及被焊零件时,由被焊零件本身电阻产生电阻热,从而使被焊零件迅速加热至熔融状态,当被焊零件的结合部位中心及其附近被加热到融化温度,并逐渐向四周扩大形成熔核,并在上下电极压力下冷却至结晶状态,形成焊点。原理图如下图1所示:
图1
2.2 点焊焊点的质量技术要求
车身点焊焊点质量好坏决定着焊接的强度,并且对白车身的耐疲劳性能和车身的整体强度性能起着非常重要的作用。对于点焊焊点质量的技术要求和评判标准,不同汽车厂商采用的方式与方法也略有不同,但归根结底车身焊点的质量要求主要体现在五个方面:①焊点的的数量:产品图纸上规定的焊点数量的±12%(焊点数量大于40的情况下);②焊点的外观:呈圆形或椭圆形,避免出现裂纹、穿孔、毛刺、过烧、凹陷及焊点挤出现象;③焊点的位置、间距:焊点的位置控制在产品图纸中规定的位置±10mm,焊点之间间距应布置均匀;④焊点的焊透率:薄板零件一侧的焊透率(%)=t1/T1*100%,厚板零件一侧的焊透率(%)=t2/T2*100%(具体如下图2所示),通常被焊零件的焊透率质量要求值为(20~80)%;⑤焊核的直径:熔核直径的最短径与熔核直径的最长径之和的1/2,不同钣金厚度的焊点直径经验值如下表1所示;
表1
图2
3 车身外观焊点常见缺陷及质量检测方法
3.1 白车身在点焊焊接过程中由于受外界或人为因素(如焊接工艺参数设置不合理、相互搭接的被焊零件搭接面设计不合理等)的影响,焊点处经常会出现各种缺陷,车身外观焊点常见的缺陷主要有以下八种:
(1)虚焊:熔核直径尺寸小于图纸技术要求或根本无焊核;如边缘焊点现象、熔核尺寸过小缺陷等;
(2)烧穿:点焊焊点中出现穿透被焊工件的通孔的缺陷现象;
(3)裂纹:出现在围绕焊点周圈不规则的不可接受的裂纹现象;
(4)边缘焊点:没有包括焊件所有边缘部分的焊点缺陷现象;
(5)压痕过深:对应焊点位置处点焊后总料厚减小超过50%的缺陷现象;
(6)焊接扭曲:被焊零件焊接后在焊点处出现变形超过25度的缺陷现象;
(7)位置偏差:被焊工件焊接后出现焊点位置偏离理论位置超过10mm的缺陷现象;
(8)漏焊:实际焊点数量少于理论设计焊点数量的缺陷现象;
3.2 车身外观焊点的质量的评价分为外观评价和强度评价两方面,对于焊点外观合格性与否的质量检测手段主要是肉眼目视,而且有时还需要用到千分尺、厚度仪、游标卡尺等检测工具对焊点的表面及焊核进行测量来综合判定,此种检测手段可以归类为非破坏类检测手段;而对于焊点强度合格性与否的质量检测手段主要是通过手工剥离试验测量焊点熔核的直径尺寸,此种检测手段是当前评价车身焊点强度的最常用的有效方法,此种检测手段可以归类为破坏类检测手段,主要分为凿裂试验(如图3)和手动扭转(如图4)试验两种方法。通过凿裂试验或手动扭转试验,都将会在一个被测样品上留下与之对应的另一个被测样品的熔核部分,测量留下部分的平均直径即为该焊点熔核的直径,当所测的熔核直径未明显小于图纸技术要求的直径尺寸时,则可判断所测焊点的该熔核直径尺寸合格,从而近一步判定焊点的强度是否符合设计要求。当前随着科技的发展和进步,对于焊点强度评价的还可以通过金属金相检测和焊点超声波检测手段来进行全面评估,此两种手段可从本质上更加全面的检测焊点的强度是否满足整车性能要求,从而为整车可靠性和安全性能提供更加有力的保障。
图3
图4
4 车身外观焊点质量控制手段
车身外观焊点质量控制方法主要有①被焊零件本身的质量精度控制;②点焊焊接工艺参数的设定;③焊钳正负电极帽的调试和修正;④其它不常用的控制方法这四种方法,各控制方法主要包含内容如下:
(1)被焊零件本身的质量精度控制:主要从零件设计精度上进行保证,如被焊零件之间的间隙应尽量最小化,焊接部位上下表面应设计平整光滑且角度尽量平行一致,避免出现4层或四层以上的钣金件的点焊,点焊工件的综合厚度应控制在6mm以内;
(2)点焊焊接工艺参数的设定:不同板厚的工件之间的焊接应选以较薄工件的允许焊接工艺参数为准;同一台焊机在同时焊接两层板和三层板时,应以两层板的允许焊接工艺参数为基准,逐步调试和修正相关焊接参数,以此来同时满足两层板和三层板相互焊接的工况;另外当被焊零件为镀锌板时,焊接电流应根据需要适当增大;
(3)焊钳正负电极帽的调试和修正:焊接钳的正负极与被焊工件直接接触的接触面直径也属于焊接工艺参数的一个重要项,由于焊钳正负电极头端面在长期使用过程中会出现不能程度的磨损和磕碰,磨耗后的正负电极头端头状态会直接影响焊点焊核成形的外观和质量,所以经常对焊钳正负电极头断面状态进行修磨控制和调试。
(4)其它不常用的控制方法:其它不常用的焊接质量控制方法主要包含中频逆变点焊焊接和自适应点焊焊接系统,中频逆变点焊焊接主要是通过对焊接电流的有效控制来提升焊点质量。而自适应点焊焊接系统是为零满足不同材质、不同厚度的工件之间焊接能够平稳切换而采取的多个焊接参数的柔性自适应控制系统来保证焊接质量的方法。
5 小结
随着车身焊接工艺的提升,车身焊点质量检测手段和控制方法正呈现出多样化,另外伴随着新技术、新工艺、新材料的不断运用,客户对于汽车车身焊点的焊接外观质量和整车安全性能要求越来越高,面对这些机遇和挑战,我们要更加深入地学习和研究汽车焊接工艺,运用更加有效和先进的创新性手段来控制车身焊点质量。
参考文献:
[1]李强.汽车车身制造工艺基础.机械工业出版社,2020.
[2]张西振.汽车车身焊接技术(第2版).北京理工大学出版社,2005.
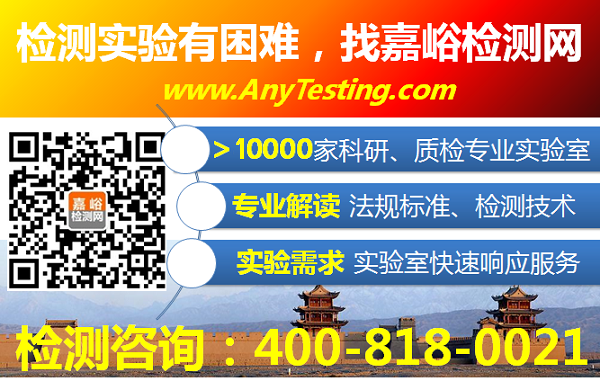