近年来, 相控阵超声检测技术在各行各业的应用越来越广泛,相关检测标准也陆续发布,该检测技术能够以图像方式显示缺陷信息,能够通过电子扫描等技术提高检出率与检测效率。然而其也存在一定的局限性,例如由于声束扩散,不同声程位置对应的声束宽度不一致,从而对缺陷的测量精度产生一定的影响。
为了解决该问题,超声检测领域开发了全聚焦检测技术,近年相位相干成像(PCI)检测技术也开始应用于工业检测领域,其主要通过相位相干成像,信号幅值对PCI成像没有影响。因其在一些应用领域能够对传统相控阵技术和全聚焦技术进行有效补充,故应用范围越来越广泛。
文章详细介绍了全聚焦与PCI检测技术的原理,从原理上分析二者的差异性,并通过试验测试PCI检测技术对不同缺陷的检测特点及效果,了解PCI检测技术针对不同类型缺陷的检测优势与不足。
1、全聚焦成像检测技术与PCI技术基本原理
全聚焦成像检测技术是基于全矩阵数据采集的一种相控阵超声后处理成像方法。该技术能够在设定的区域范围内对每个位置都进行聚焦,使用时先设定聚焦区域,并将聚焦区域按一定的分辨率划分成网格,再在网格交点位置进行聚焦。
首先相控阵超声仪器需进行全矩阵采集(Full matrix capture, FMC),全矩阵采集时首先激发第一个晶片,然后其他所有晶片接收超声信号;随后激发第二个晶片,然后其他所有晶片接收超声信号;依次以同样的方式激发所有晶片,得到各晶片相应的超声信号,全矩阵采集完毕。FMC激发及采集模式示意如图1所示。
图1 FMC激发及采集模式示意
1、全聚焦成像检测技术基本原理
全矩阵采集完毕后,即可采用全聚焦数据处理算法,对聚焦区域内所有预先定义的位置点进行聚焦算法处理,如图2所示。
图2 全聚焦幅值计算示意
以图2为例,对聚焦区域的P点进行聚焦成像,假设第i个发射晶片为Fi,第j个接收晶片为Jj,首先需要计算晶片Fi到成像点P的超声传播时间ti,同时计算成像点P到接收晶片Jj的传播时间tj,得到超声波从晶片Fi传播至P点然后传播至Jj晶片的传播时间tij。假设在P点位置存在缺陷,超声波传播至缺陷时反射至接收晶片Jj,则Jj接收到的超声信号在tij时间位置处会有较强的反射信号,将tij时间点对应的幅值Aij用于聚焦成像,P点成像对应的幅值为所有接收晶片接收到的超声信号对应P点成像路径幅值的叠加,假设有N个晶片,则P点对应的全聚焦成像幅值可用下式表示:
(1)
全聚焦成像时,需要通过式(1)计算得到所有聚焦区域内成像点对应的幅值,然后将叠加得到的幅值通过相应的颜色进行显示。
2、PCI检测技术基本原理
PCI是基于全矩阵数据采集后的一种相控阵超声成像处理算法。全矩阵数据采集相关原理与全聚焦成像检测技术原理一样,只是数据采集后的数据处理成像算法不同。PCI成像主要利用超声信号的相位信息进行成像,而不利用超声信号的幅值信息进行成像,故超声信号幅值不参与到PCI成像计算中。
进行PCI成像,首先需要将全矩阵采集到的A扫描信号相位化,A扫描信号的相位化示意如图3所示,对应B点和D点位置的相位都是正相位,A点和C点对应的相位为负相位。通常正相位用1表示,负相位用-1表示,0点相位用0表示,因此经过相位化的A扫描信号每个时间点对应的相位值只会是1,0或-1三个值。采样点的幅值为80%与10%对应的相位值都是一样,均为1,因此A扫描信号幅值对PCI成像影响很小,只要A扫描信号能够准确得到相应点的相位信息即可。
图3 A扫描信号相位化示意
PCI成像算法计算过程与全聚焦的计算过程类似,需要将全矩阵采集到的A扫描数据通过符号函数相位化。如果采样点对应的A扫描信号幅值小于0即用-1表示;采样点对应的A扫描信号幅值如为0即用0表示;采样点对应的A扫描信号幅值大于0即用1表示。
PCI全聚焦幅值计算示意如图4所示,PCI成像需要得到P点的相位幅值信息,假设第i个发射晶片为Fi,第j个接收晶片为Jj,先要计算晶片Fi到成像点P的超声传播时间ti,同时计算成像点P到接收晶片Jj传播时间tj,得到超声波从晶片Fi传播至P点然后传播至Jj晶片的传播时间tij,然后在接收晶片Jj接收到的A扫描信号中提取tij时间点对应的相位值фij。
图4 PCI全聚焦幅值计算示意
P点对应位置的相位值为全矩阵采集数据中所有对应P点传播路径时间点相位值的叠加,如下式所示:
(2)
由PCI成像计算原理与过程可知,如果在成像点的对应位置,各晶片接收到的A扫描信号相位不相干,有可能负向叠加,例如一些晶片采集数据对应的相位值是1,一些晶片采集数据对应的相位值是-1,进行叠加后抵消而变为0。全聚焦成像算法进行叠加计算时,对应位置A扫描信号相位存在一些差异,其对应幅值也能正向叠加,不可能出现负向叠加的情况,这是PCI成像与全聚焦成像的最大区别。
2、PCI技术特点及检测应用
PCI技术只使用相位值进行成像,具有自身的特点,经过试验测试验证,某些特点有利于部分缺陷的检测和测量,某些特点不利于部分缺陷的检测和测量,下面重点介绍其对检测应用的影响。
1、PCI对反射信号弱的缺陷检测信噪比高
PCI技术对一些反射能量较弱的缺陷信号有较高的信噪比。
例如在相控阵检测技术中经常用到衍射信号,衍射反射信号传播的角度范围大,相控阵探头各个晶片都能接收到衍射波信号,但是衍射波信号能量很弱,接收到的回波信号幅值很低,衍射波叠加后幅值还是较低,很难与噪声信号区分开,信噪比不高。
由于PCI技术只使用相位进行成像,各晶片接收到的衍射信号相位相干,虽然衍射信号幅值低,但通过相位值叠加后成像的信号较强,其显示幅值与端角信号的幅值相当。
全聚焦技术与PCI技术检测刻槽时的衍射信号成像显示如图5所示,其显示的是深度为1,2,3 mm刻槽的图像,可以看到PCI技术显示的刻槽衍射信号信噪比远大于全聚焦检测技术。通过全聚焦技术无法区分显示深1 mm刻槽端点衍射信号与端角反射信号,而PCI技术能够区分显示深1 mm刻槽端点衍射信号与端角反射信号,提高了检测分辨力。
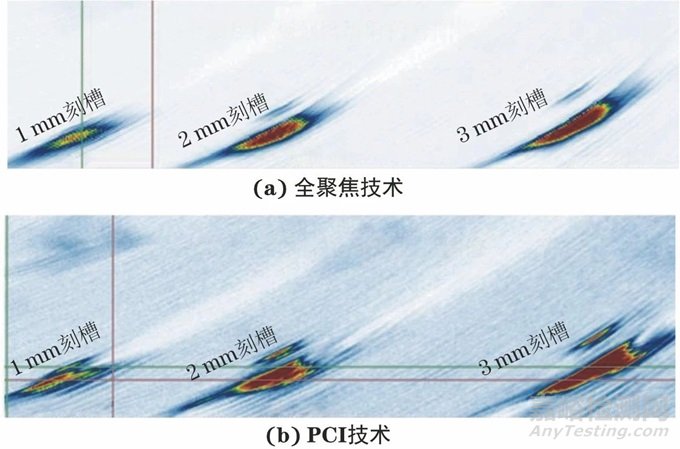
图5 全聚焦与PCI技术的衍射信号成像显示
由于幅值对PCI技术的影响小,对于一些反射能量较低的较小缺陷,PCI技术与传统相控阵超声及全聚焦技术相比有一定的优势。
对一些晶粒较粗的材料,缺陷信号幅值与噪声信号幅值相差较小,二者较难区分。相控阵超声探头各晶片接收到的噪声信号虽然幅值相差不大,但是其相位信息相差较大,一些噪声信号是正相位信号,而一些噪声信号是负相位信号,因此噪声信号叠加时为非相干叠加。而各晶片接收到的小缺陷信号通常为相干叠加,因此小缺陷信号的信噪比较高。
全聚焦技术与PCI技术分别检测ф0.2 mm平底孔的检测效果如图6所示,可以明显看出使用PCI技术得到的信噪比远大于使用全聚焦技术,并且PCI技术的上表面盲区也小于全聚焦技术的盲区。
图6 全聚焦与PCI技术检测ф0.2 mm平底孔的成像对比
2、PCI对面状反射体成像信号幅值弱
当相控阵探头一个晶片激发产生的超声波垂直入射至平面状反射体时,激发晶片相邻的晶片也能接收到较强的超声信号,但是各个晶片接收到平面反射超声信号的相位存在一定差异,有些晶片对应位置点是正相位,而有些晶片对应位置点是负相位,因此各晶片相位值进行叠加时,不是相干叠加,导致PCI技术得到的信号幅值弱。
全聚焦与PCI技术检测平面缺陷时的成像对比如图7所示,从图中可以看到全聚焦成像能够显示很强的底面回波信号、平面缺陷信号、界面波信号,而PCI成像图中没有显示底面回波信号、平面缺陷信号与界面波信号,因此检测与超声波入射方向垂直的面状缺陷时,应尽量避免使用PCI技术。
图7 全聚焦与PCI技术检测平面缺陷的成像对比
经上述分析,PCI技术对超声波垂直入射至平面的反射成像信号弱,从而能提高近表面缺陷的检测分辨力,全聚焦与PCI技术分别检测近表面附近3个横孔与下表面附近3个横孔的结果对比如图8所示。图8(a)为全聚焦检测下表面附近横孔的结果,图中能明显区分横孔信号与下表面回波信号。图8(b)为PCI检测下表面附近横孔的结果,图中可明显看到横孔信号,且没有底面回波信号干扰,但信噪比比全聚焦图像的差。图8(c)为全聚焦检测上表面附近横孔信号的结果,图中可以看出一个横孔信号与上表面信号重叠而无法识别,中间孔能看到,但无法与上表面信号分开。图8(d)为PCI检测上表面附近横孔的结果,可以看出PCI检测图像没有上表面信号干扰,能在一定程度上减小上表面盲区,图中能看到3个横孔信号,但信噪比均不高。
图8 全聚焦与PCI技术检测近表面缺陷的成像对比
3、PCI技术对体积状反射体成像能力与全聚焦相当
对于体积状反射体,各晶片接收到的相应位置反射信号在叠加时,通过幅值叠加与相位叠加,都接近相干叠加,因此全聚焦成像效果与PCI成像效果相当,缺陷显示均有较高信噪比,全聚焦与PCI技术检测体积状反射体的成像对比如图9所示。
图9 全聚焦与PCI技术检测体积状反射体的成像对比
3、结语
PCI技术能够提高点状较弱反射缺陷的检测能力,例如裂纹尖端衍射信号,同时能够提高小缺陷检测能力及粗晶材料工件的缺陷检测信噪比。
PCI技术对平面状缺陷检测能力较弱,特别是对超声波垂直入射至反射面的面状缺陷,容易产生漏检。
PCI技术能够提高近表面缺陷的分辨力,减小近表面盲区,对体积状缺陷检测能力与全聚焦技术的能力相当。
因此在使用PCI技术时,根据不同的检测场景与检测要求,充分发挥其优势,并可借助其他技术弥补其不足。
作者:张瑞,钟德煌,王晓宁
工作单位:艾因蒂克科技(上海)有限公司
第一作者简介:张瑞,高级工程师,主要从事工业及医疗超声技术相关研究工作。
来源:《无损检测》2024年1期
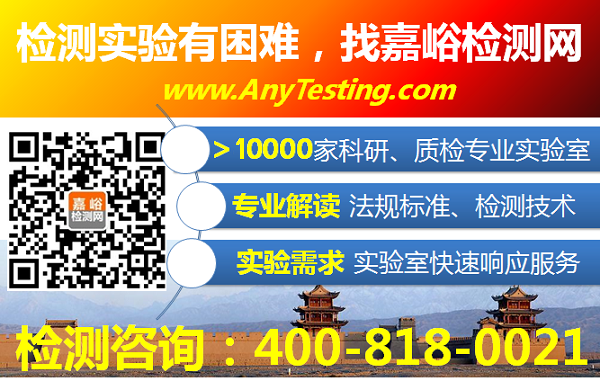