给水加热器(FWH)是热电厂和核电厂的汽-水循环中的关键部件,是管侧给水和壳侧蒸汽冷凝的界面。由于位置关键,给水加热器的性能对电厂的效率和利用率有明显的影响。
冶金工艺、焊接工艺,特别是无损检测技术的进步,使焊接产品得到不断的发展。给水加热器所用的产品主要有无缝管、焊接和冷拨管或焊接管三种。下面通过介绍瓦卢瑞克焊接换热管有限公司(VHET,原Valtimet)的生产工艺,论述与其它工艺相比该工艺的特别之处,以及工艺中无损检测的重要性。
图1 核电厂(左)和热电厂(右)中的低压和高压给水加热器
自上世纪70年代以来,人们就采用不锈钢材料来制造低压和高压给水加热器,主要采用两种不锈钢:铁素体不锈钢和奥氏体不锈钢,下面主要探讨奥氏体不锈钢。根据给水加热器的运行条件,可选用的各种奥氏体不锈钢如下:
最常用的钢种是TP304。
当对耐腐蚀性能有特别要求,而ASME标准要求的机械性能低于TP304时,采用碳含量低的TP304L。
当ASME标准要求的机械性能较高时,高压给水加热器通常使用添加氮的TP304N制造。
当对耐腐蚀性能有特殊要求时,有时也可使用TP316和其衍生钢种。
典型的高压不锈钢给水加热器管道的外径为15~18 mm,管壁厚度为1.1~3 mm。虽然人们传统上使用无缝不锈钢管道,但是为了降低成本,已采用焊接和冷拨管或焊接管代替了无缝钢管。
在上世纪80年代,瓦卢瑞克公司开发了一种按最高标准要求生产高压给水加热器管的工艺,生产的热管壁厚度最大为2.1 mm。然后公司对其印度厂的工艺进行了改进,来生产壁厚3 mm的不锈钢管。
高压给水加热器管的生产工艺
将冷轧带钢进行开卷,送入多机架成型机,把带钢形成管状。在惰性气氛下利用非自耗电极进行自熔焊接(TIG)。瓦卢瑞克公司已开发了一种在焊接过程中对焊接熔池进行支持的工艺,利用该工艺可使内外焊缝形状完美平滑,并可防止管道内表面产生氧化。
ASTM A249和ASTM A688标准要求在退火前对焊缝和基体金属或仅对焊缝金属进行冷作加工。为确保通过均质和再结晶使焊缝和基体金属具有相似的机械和耐腐蚀性能,在进行热处理前进行冷作加工是必不可少的步骤。现有几种工艺可满足这一要求,如焊缝整平、焊缝锤击、辊式减径、拉拨等。
瓦卢瑞克公司利用轧制减径退火(RSA)工艺进行生产,该工艺使钢管进入一组水平和垂直辊系,对钢管进行缩径,使其达到最终的管径。由于焊缝比基体金属要软,所以主要是对焊缝进行冷作,如图2所示。
图2 利用轧制缩径对焊缝区域进行压下
轧制减径退火(RSA)工艺的最后一步是在线退火处理,来促进焊缝材料的再结晶(图3)和铁素体的溶解。由于在(利用环形线圈进行感应加热的)热处理过程中和在(利用水套系统的)冷却过程中采用惰性气氛对钢管进行保护,瓦卢瑞克公司对钢管进行光亮退火处理可确保管道的内外表面不产生氧化。
图3 在线退火有助于焊缝材料的再结晶
接着对钢管进行外观检查和无损探伤(气压试验、涡流检测和超声波检测)。然后按照用户要求进行弯管,对弯曲部分去除应力,再次进行水压试验和外观检查,最后清洗和包装,如图4所示。
图4 对钢管进行外观检查
无损检测方法
1、涡流检测
按照ASTM标准,如A688,需要进行涡流检测(ECT)。涡流检测可检测出短的和体积型条形缺陷或短小焊缝缺陷,如图5所示的凹痕和线状缺陷)。
图5 利用涡流检测判废的焊缝凹痕
一般来说,人们利用频率设定在10 kHz和30 kHz,以不同工作方式的环形线圈进行涡流检测。ASTM A688规定了带有直径0.8 mm钻孔的标准缺陷。判废标准是ASTM A1016,该标准规定当管道产生的测试信号等于或大于标样产生的最弱信号时应判废(也就是说,K值为1)。在有些情况下,可选用更加严格的判废标准,如ASTM A688的补充要求S1。
2、超声波检测
超声波检测一般以纵向方式进行,来检测长的和纵向焊缝缺陷,如未焊透或焊缝不匹配,如图6所示。常用的标准缺陷为深度为额定管道壁厚10%或12.5%、宽度为0.2 mm、长度为12.7 mm的U形纵向凹口。为了更好地进行焊缝缺陷检测,这些人工缺陷须在焊缝中。
图6 利用超声波判废的未焊透、焊缝不匹配、焊缝过厚
奥氏体钢管所用的灵敏度K=0.8/0.9(-2/-1 dB)。虽然在标准ASTM A688中,超声波检测不是强制性检测项目,但由于高压给水加热器的工作环境相当恶劣(高温、高压),强烈建议对高压给水加热器进行超声波检测。
实际上按照标准A688的补充要求S1或S3中的严格参数进行了几次试验,来检查是否可用涡流检测来代替超声波检测,但试验结果并不理想。即使采用高灵敏度进行检测,也无法检测出未焊透或错边缺陷。这些缺陷是典型的长缺陷,仅超声波才能检测出来。
即使是人们所认为质量较高的焊接拉拨管也可能产生图7所示的重大缺陷,所以也须进行超声波检测。
图7 拉拨管的错边
该工艺为什么特殊?
无碳污染
上述生产工艺的优点之一是在成型或定径过程中钢管内部均不使用润滑剂。这样工艺可保证钢管在退火过程中不会被碳污染。与此相反,拉拨工艺的冷作加工使用润滑剂,在退火前要进行脱脂,由于钢管很长(长度在15米以上),内径非常小(大约10 mm),脱脂非常困难。
图8 A262操作A腐蚀试验:晶间碳化物沉淀
残余应力小
采用拉拨工艺,钢管的平直度在连续退火炉内进行离线退火后无法满足用户要求。因此须采用双曲线旋转辊矫直要对钢管进行娇直。娇直操作会使钢管外表面产生很深的印痕和很大的残余应力,这会对耐应力腐蚀裂纹性能(SCC)造成不利影响。
在高温高压条件下,304对这种腐蚀机理非常敏感。因此必须要对残余应力进行限制。上述工艺可确保钢管在退火过程中平直度保持不变,这样钢管就不需要进行矫直,残余应力就很低。
没有铬贫化或过酸洗的风险
在进行空气退火时,为了去除氧化皮和贫铬层,必须要进行酸洗。由于钢管内径非常小,钢管很长,在钢管表面很难进行该操作。酸洗条件不好时,不是不能完全去除贫铬层就是造成过酸洗,如图9所示。过酸洗会使表面变粗糙,增大压降。上述生产工艺采用光亮退火避免了这些风险,由于不进行酸洗,同时对环境友好(不产生含氮化物的废液),使用安全(无HF酸)。
图9 钢管内表面的过酸洗
严格的无损检测
在钢管生产规范中,涡流检测是标准规定的检测方法,但是为了检测出利用其它方法无法检出的关键性缺陷,还须强制实施超声波检测。这些关键缺陷会导致管道故障,特别是在高温高压条件下,会使设备产生重大问题,因此强烈建议在钢管生产中使用涡流检测和超声波检测。
降低运送带来的风险
在线加工处理可明显降低将钢管从一台设备运送到另一台设备所产生的风险。为了防止产生凹痕、应力或管道变形等缺陷,在运送时要格外小心谨慎。
来源:不锈、中国钢铁工业协会不锈钢分会
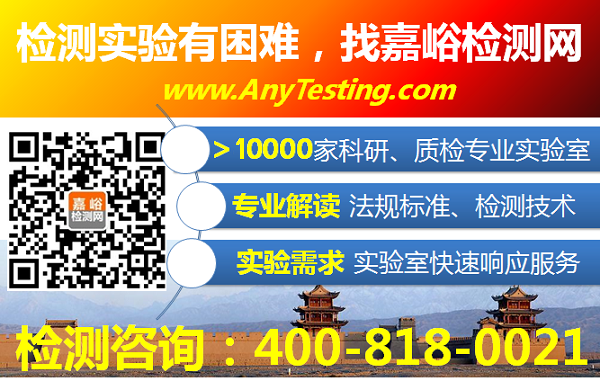