机械、运载和能源等领域已服役多年的典型重大装备的构件中已产生了裂纹等缺陷,但过早判废退役就意味着巨大的经济损失,继续运行则需要合理的寿命预测以保证安全。因此,合理预测含裂纹构件寿命是有效提高装备使用潜力和控制失效事故发生的重要途径。
金属材料特别是高强度铝合金作为结构主承力件材料被广泛应用于大型运输机、高铁、舰船等大型机械设备,如军用飞机导弹挂架的过渡梁对接处(铝合金结构厚度达40 mm左右)、机翼梁框(铝合金结构厚度在30 mm左右)等部位,大型机械装备关键承力隔框、耳片接头等部位(铝合金结构厚度可达20 mm以上)。常规的裂纹扩展数据都是基于标准试件(厚度一般在2~10 mm)通过试验获取,是否适用于大厚度(特指20 mm以上)铝合金板尚需研究。
为了给相关领域研究人员提供参考,空军工程大学航空工程学院的科研人员对大厚度铝合金板裂纹尖部应力应变场与裂纹扩展形貌、疲劳裂纹扩展厚度效应、腐蚀疲劳交替作用下裂纹扩展机理等方面国内外研究现状和发展趋势进行了总结分析,探讨了大厚度铝合金板疲劳裂纹扩展特性研究的新问题与关键问题,旨在为发展大厚度铝合金板三维损伤容限评估方法及模型提供帮助。
大厚度铝合金板疲劳裂纹扩展的新问题
目前,研究普遍表明疲劳裂纹在扩展过程中表现出“隧道效应(crack tunneling)”特征,即当包含初始直线裂纹前沿的穿透裂纹试样受到循环加载时,中心层裂纹前沿首先向前扩展,其余裂纹前沿随后扩展,形成指甲盖形状裂纹前沿形貌。
然而,作者在开展厚度分别为20和60 mm的7050-T7451铝合金单侧裂纹板(垂直轧制方向)拉伸疲劳裂纹扩展试验时发现,试样厚度由20 mm增至60 mm后,裂纹形貌发生改变,出现了“双隧道效应”,又称“马鞍效应”,即裂纹形貌呈马鞍形,如图1所示。
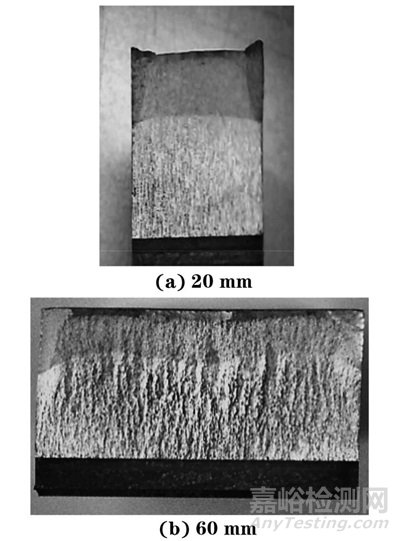
图1 不同厚度铝合金单侧裂纹板断口形貌
试验的载荷及环境工况见表1,疲劳载荷为常幅载荷,载荷频率为5 Hz,正弦波形,应力比为0.06。
表1 不同厚度铝合金单侧裂纹板拉伸疲劳裂纹扩展试验载荷及环境工况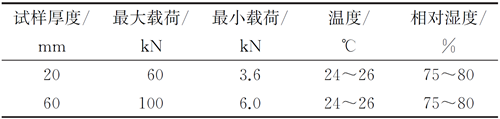
对于大型机械设备中的大厚度铝合金结构,其三维穿透裂纹前沿形貌难以准确判读,多数情况下只能依据表面裂纹长度或基于“隧道效应”的等效裂纹长度来评估结构安全状态,预测结构剩余强度与疲劳寿命,误差较大。
作者采用板两侧表面裂纹的测量长度(aS1,aS2)的均值aS作为裂纹长度,基于传统断裂韧度准则(K≤KC,KC=KIC=35 MPa·m1/2)对60 mm厚试样进行剩余强度Ps评估,并与试验结果Pt进行比较,结果见表2。对比发现,采用表面裂纹长度估算的剩余强度值与试验值的相对误差约为30%,预测结果偏危险。
表2 采用表面裂纹长度计算的剩余强度与试验结果的对比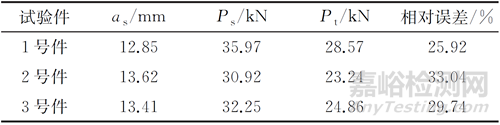
另一方面,已有研究表明,试样厚度对疲劳裂纹扩展具有显著影响,随着试样厚度增加,裂纹扩展寿命降低,薄板试样的计算模型无法用来估算厚板结构裂纹扩展寿命。试样厚度增加引发的裂纹扩展“马鞍效应”是厚度与三维裂纹尖部应力应变场内在联系的表象反映,在未得出这种内在联系机理与规律的情况下,基于传统模型对厚板及变厚度板进行损伤容限评定必然存在很大的风险。
当前,结构完整性、安全性、经济性和维修性等已成为飞行器、高铁等重大机械装备设计的重要目标,材料的疲劳断裂性能和结构的损伤容限能力需要发挥到极致,才能满足日益严苛的设计要求。
在含裂纹结构中,裂纹尖部复杂的三维应力场对含裂纹结构的强度起着至关重要的作用。试验表明,采用基于二维理论发展起来的断裂以及疲劳寿命预测模型对实际三维结构进行评估将会导致不精确且偏危险的预测结果。因此,深入研究大厚度铝合金板三维裂纹扩展/断裂机理,发展连续变厚铝合金板三维损伤容限评估方法及模型,成为保证大型机械设备安全服役亟待解决的问题。
大厚度铝合金板裂纹扩展研究现状
大厚度金属板三维裂纹扩展特性研究涉及尖部应力应变场与裂纹扩展形貌、疲劳裂纹扩展的厚度效应等内容,作者对国内外相关研究成果和发展趋势进行了总结。
1、裂纹尖部应力应变场与裂纹扩展形貌
自IRWIN提出应力强度因子K以后,裂纹尖部场的描述体系便经历了从线弹性体系到弹塑性、蠕变理论体系,从单参数体系到三参数体系以及从二维体系到三维体系的发展。
郭万林等研究发现,三维裂纹与二维裂纹最本质的区别可以通过三轴应力约束参数TZ描述。根据TZ有限的特性,从三维弹塑性体的基本方程出发,在形变理论框架下获得了J-TZ双参数描述下裂纹尖部场的解析解,进而将面内约束与离面约束理论结合,发展了裂纹尖部场的线弹性K-T-TZ和弹塑性J-QT-TZ三参数描述。随后,研究人员又进一步对三维裂纹尖部场理论解进行了完善,并基于此提出了等效厚度概念并进行应用。
随着计算机性能提高,通过仿真方法研究三维裂纹的尖部场得到了重视,并通过三维有限元法发现三维裂纹尖部沿厚度方向各点的应力强度因子值并不相同。然而,由于靠近板自由表面时的角点奇异性(vertex singularity),解析应力强度因子沿厚度方向的变化规律仍然比较困难。
三维裂纹尖部应力应变场决定裂纹扩展形貌。KIKUCHI等基于有限元方法,采用移动节点来模拟弹塑性状态下三维裂纹扩展问题,结果表明,裂纹沿裂纹前沿扩展,J积分分布趋于均匀,所得的裂缝前沿形态与许多试验结果一致。
BRANCO等将裂纹尖部应力强度因子分布与裂纹形貌联系,基于有限元计算对中心孔裂纹拉伸试样的裂纹扩展形貌进行了分析,提出了分别由指数函数和多项式函数组成的瞬态和稳定阶段的数学模型,并指出裂纹形状的变化与应力强度因子沿裂纹前沿的分布有关。
FIORDALISI等基于试样真实裂纹扩展形貌,运用Abaqus有限元分析软件计算了裂纹前沿有效应力强度因子幅值,对比研究了含二维穿透直裂纹与三维曲线裂纹的304L奥氏体不锈钢紧凑拉伸(CT)试样的裂纹长度与裂纹前沿形貌对裂纹尖端闭合效应的共同影响,计算得到的裂纹形貌与试验结果较为吻合。
RÉTHORÉ等采用有限元法对试验中的三维裂纹新形貌沿厚度方向的应力强度因子进行了计算,通过试验给出了大范围应力强度因子ΔK值范围内的裂纹扩展速率-应力强度因子(da/dN-ΔK)曲线。
SALVADORI等基于权函数法与变分法对三维弹性体裂纹前沿形貌演变进行分析,提出了能够更加准确描述裂纹前沿扩展行为的计算方法。
NAVARRO等采用权函数法研究发现,平面应力、平面应变、三维状态下三点弯曲试样裂纹尖部应力强度因子的分布不同。
综上所述,三维裂纹尖部应力应变场与裂纹扩展形貌之间有着密切的联系,并且最终影响着含裂纹结构的疲劳寿命。但是,目前的研究大多是对试验确定的裂纹形貌进行数值计算或仿真分析,对于三维裂纹尖端张开位移沿裂纹前沿的变化规律尚无明确的理论及数值计算方法来确定,缺少大厚度裂纹板的三维裂纹扩展形貌的定量计算方法模型。
2、疲劳裂纹扩展的厚度效应
疲劳裂纹扩展的厚度效应早在20世纪60年代就已引起关注。20世纪90年代,欧洲航空技术组以及波音飞机公司都系统地进行了不同厚度(2~20 mm)试件在飞行模拟载荷下的裂纹扩展试验,以了解厚度效应,确定经验参数并提供考核和发展裂纹扩展分析模型的试验依据,试验结果表明,试件越厚,裂纹扩展越快,寿命越短。
张诗捷等开展了不同厚度金属板(3.0~12.7 mm)的疲劳裂纹扩展试验,结果表明,广义改进的Willenborg模型不能反映厚度对裂纹扩展寿命的影响,J.B.Chang模型中的过载截止比与试样厚度有关。
何宇廷等开展了7075铝合金中心裂纹拉伸(CCT)试样在随机谱下的裂纹扩展试验,并对不同厚度(2~12 mm)试样的疲劳断口形貌进行了分析,结果表明,随着试样厚度的增加,稳态扩展区的疲劳条带变稀疏,裂纹扩展速率增加。
殷之平等从损伤容限设计概念出发,分析了变厚度壁板的裂纹尖端应力强度因子、剩余强度和裂纹扩展寿命,采用有限元软件对变厚度壁板损伤容限特性进行了研究,发现凸台厚度的变化(2.4~12 mm)对变厚度壁板的损伤容限特性具有明显影响。
PARK等研究发现,随着304不锈钢CT试样厚度的增加,疲劳裂纹扩展速率增大。
HOLPER等以2024-T3和7075铝合金试样为研究对象,通过低频疲劳试验和超声疲劳试验研究了疲劳裂纹在近门槛区扩展时的厚度效应,结果表明,当扩展速率为10-10和10-9 m/周次时,薄试样的裂纹扩展门槛值较大。
顾绍景提出一种谱载三维疲劳裂纹扩展寿命模型,并采用该模型模拟了1.6和3.1 mm厚2024-T3铝合金中心裂纹拉伸试样在TWIST载荷谱下的疲劳裂纹扩展寿命,模拟结果与试验结果吻合较好,说明该模型在一定程度上能够反映疲劳裂纹扩展的厚度效应。
综上所述,在裂纹扩展分析中考虑试样厚度的影响非常重要。目前较成熟的疲劳裂纹扩展寿命预测模型大多基于平面模型,认为随着板厚的增加,含裂纹板逐渐从平面应力状态过渡为平面应变状态,致使裂纹扩展速率增大,疲劳寿命降低。然而,对大厚度(20 mm以上)板的裂纹扩展计算与试验分析却鲜有报道,缺乏相应的损伤容限分析方法,其裂纹扩展、断裂机理也未能得到合理解释。因此,研究大厚度板三维疲劳裂纹扩展的厚度效应,发展并完善相应的损伤容限分析模型,是大型机械设备结构长寿命安全服役使用的迫切之需。
3、腐蚀疲劳作用下裂纹扩展机理与模型
海洋、石油化工设备、飞机、高铁等均在不同程度的腐蚀环境下服役,在交变应力和腐蚀环境的影响下,材料的裂纹扩展规律和机理与纯机械载荷下完全不同。目前,针对铝合金结构,相关研究主要集中在预腐蚀疲劳、腐蚀疲劳交替作用和腐蚀疲劳共同作用3种条件下。
预腐蚀疲劳是研究腐蚀导致机械结构寿命退化规律最常用的基础研究条件,研究内容包括加速腐蚀环境谱编制、腐蚀特征量随腐蚀时间及腐蚀介质的变化、腐蚀对材料寿命的影响规律等。
腐蚀疲劳交替作用条件更符合飞机结构服役的实际情况,飞机于地面停放时主要受到腐蚀损伤作用,在高空飞行时由于环境温度低、腐蚀性小,主要受到疲劳损伤的作用。
MENAN等研究发现,腐蚀疲劳交替作用下2024铝合金材料的疲劳特性与预腐蚀作用下的疲劳特性存在不同。
杨晓华等提出了考虑腐蚀环境作用的腐蚀疲劳交替寿命预测模型——损伤累积“迟滞”模型。腐蚀疲劳共同作用更符合海洋装备结构的服役情况,在该条件下,材料的疲劳寿命和裂纹扩展寿命会大幅下降。
腐蚀环境促进疲劳裂纹扩展的本质在于裂纹尖端金属材料的化学反应所造成的局部材料损伤,主要体现在阳极溶解以及氢进入导致裂纹尖部局部材料力学行为的变化上。
TROCKELS等研究发现,腐蚀环境中铝合金裂纹扩展速率的提高与裂纹尖端化学反应所释放的氢原子有关。
SHIPILOV等引入了断裂过程区的概念,用于描述氢致腐蚀疲劳裂纹扩展速率。
目前的腐蚀疲劳裂纹扩展模型主要有WEI等提出的叠加模型、AUSTEN等提出的竞争模型、基于环境修正的Paris模型和CHENG等基于腐蚀疲劳中的阳极溶解和氢脆提出的腐蚀疲劳裂纹扩展模型。
然而,上述文献多集中于一般厚度金属结构的裂纹扩展研究。大型机械结构需要在腐蚀性环境中服役数十年,为保证其大厚度主承力结构满足长期安全使用要求,必须要针对大厚度结构在腐蚀和疲劳作用下的裂纹扩展规律、损伤机理和预测模型开展研究,从而更准确地进行寿命预测和管理。
大厚度铝合金板裂纹扩展研究关键问题
虽然国内外在三维裂纹尖部应力应变场、裂纹扩展形貌及疲劳裂纹扩展的厚度效应等方面开展了大量研究,但仍无法满足我国大飞机等国家重大装备的迅速发展需求,目前存在的关键问题如下:
(1)“马鞍效应”机理
从断裂力学的角度讲,含裂纹结构的净截面积是影响其剩余强度的关键因素,而裂纹扩展形貌则直接决定了结构的净截面积;另一方面,只有确定了裂纹形貌,才有可能结合断口分析及三维裂纹尖端应力应变场分布,探明厚度效应导致的裂纹在沿厚度方向产生不同扩展速率的物理机理,从而进一步揭示板厚对三维裂纹扩展速率的影响机制。
因此,必须从机理上揭示大厚度板裂纹扩展“马鞍效应”出现的原因及规律。解决这个关键问题,涉及到的技术难点主要包括含尖部裂纹体三维弹塑性有限元模型的建立及分析、裂纹形貌函数的确定等。涉及到的理论难点主要包括三维裂纹尖端的闭合效应分析、基于有效能量释放率理论确定裂纹扩展形貌的可行性分析与验证等。
(2)三维损伤容限分析的厚度效应
损伤容限分析的两大核心任务是含裂纹结构的剩余强度评估和裂纹扩展寿命预测。传统损伤容限评估模型主要从平面应力及平面应变两个角度来分析,缺乏对厚度连续性的考虑。
实际上,三维结构裂纹尖端始终存在着平面应力与平面应变两种状态,并且这两种状态主导地位也随着结构厚度的变化发生着转换;厚度变化会引起断裂韧度KC增大2~3倍,疲劳裂纹扩展寿命提升1~2个数量级。
因此,定量分析三维结构裂纹扩展及断裂的厚度效应,是对该结构进行三维损伤容限评估的关键。其中,如何建立连续大厚度下三维裂纹尖部平面应力与平面应变控制函数,如何利用实验室标准试验件得到的材料性能数据预测含实际裂纹大厚度三维结构的剩余强度和疲劳裂纹扩展寿命,如何在传统损伤容限评估模型的基础上引入厚度系数从而建立连续大厚度金属板三维损伤容限的评估模型等问题,都需要进行研究解决。
(3)腐蚀介质对裂纹尖部应力应变场的影响
在探明厚度效应对大厚度铝合金板疲劳裂纹扩展影响机理的基础上,应进一步考虑实际服役环境中腐蚀介质对三维穿透裂纹扩展的影响,研究腐蚀介质导致的三维裂纹尖部应力应变场变化的物理机制及其对裂纹扩展速率的影响机理;这是探讨腐蚀疲劳作用对大厚度复杂应力状态下铝合金板裂纹扩展影响机理的前提。
涉及到的关键理论问题主要包括三维穿透裂纹尖部区域金属材料基体的腐蚀如何影响裂纹尖部复杂应力应变场分布,这种影响在理论层面上是否会引发裂纹尖端奇异性的变化,腐蚀介质如何作用于裂纹尖部并对裂纹扩展产生什么影响,其作用机理是什么等。
涉及到的关键技术问题主要包括如何对含腐蚀损伤的大厚度铝合金板不同厚度层上裂纹尖部进行金相分析及对三维塑性区进行描述,如何从弹塑性力学和电化学腐蚀的角度建立腐蚀介质对裂纹尖部应力应变场影响的数值计算模型等问题。
(4)腐蚀疲劳交替作用对裂纹扩展影响机理
腐蚀疲劳交替作用对大厚度铝合金板裂纹扩展的影响机理是一个多元耦合的复杂问题。一方面,裂纹扩展影响因素多,载荷幅值、腐蚀介质、厚度效应等都会对裂纹扩展产生影响;另一方面,这些影响因素之间的耦合关系复杂,如腐蚀介质对裂纹尖部显微组织的影响会导致裂纹扩展速率下降。
解决这一关键问题,必须在科学合理的试验设计基础上,探明腐蚀、疲劳环境中各因素对大厚度铝合金板裂纹扩展的影响规律,研究腐蚀疲劳交替作用下各因素耦合作用对大厚度铝合金板裂纹尖部应力应变场的影响机理,进一步通过解析方法和数值仿真的方法研究腐蚀疲劳交替作用对裂纹扩展形貌和裂纹扩展速率的影响。
结束语
目前,大厚度铝合金板疲劳裂纹扩展关键问题包括“马鞍效应”机理,三维损伤容限分析的厚度效应,腐蚀介质对裂纹尖部应力应变场的影响,腐蚀疲劳交替作用对裂纹扩展的影响机理等。
针对这些关键问题,可以提出几点解决方案,比如深入研究大厚度金属板三维裂纹扩展及断裂机理,发展大厚度金属板三维损伤容限评估方法及建立相关模型解析腐蚀、疲劳环境中各因素对裂纹尖部应力应变场影响的耦合作用等。
不仅将在理论上丰富三维疲劳/断裂理论体系,在技术上完善金属结构三维损伤容限分析评估方法,也是满足大飞机、高铁、远洋船舶等大型机械设备结构长寿命安全服役使用的迫切之需,意义重大。
作者:伍黎明,何宇廷,张腾
工作单位:空军工程大学航空工程学院
第一作者简介:伍黎明,讲师,博士。
来源:《机械工程材料》2024年2期
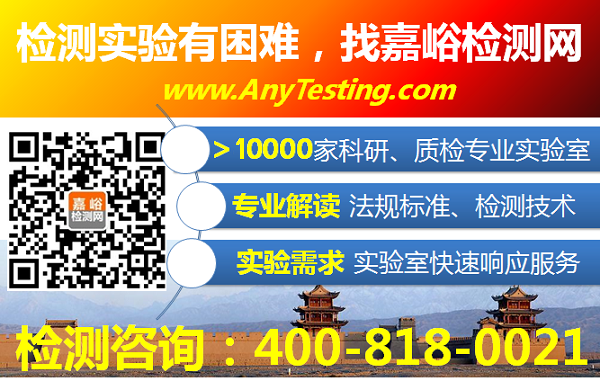