对于海洋或沿海地区工作的航空发动机来说,其高温结构表面易沉积硫酸盐(主要为NaCl、Na2SO4或V2O5等的混合物)。在高温作用下,硫酸盐容易引起一种被称为“热腐蚀”的加速损伤模式,从而使得高温合金表面容易萌生裂纹,最终导致高温结构强度下降和寿命降低。最近几年,连续出现多起因高温结构热腐蚀导致的叶片断裂故障。
在结构设计阶段,可通过考虑热腐蚀因素的安全寿命设计或损伤容限设计来保障高温结构的安全性;在运行维护阶段,为了减少发动机的维护成本并提高其可用性,需要提供经济和安全的外场维护方案。本文主要关注后者。目前,外场维护正处在由定时维护逐渐向视情维护转变的阶段。因此,亟待采用主动积极的方式对含热腐蚀缺陷的高温结构进行运行维护。
视情维护是通过在线监测或离线检测手段获取航空发动机结构的损伤程度,以此为发动机提供最经济的维护方案。在线监测的精度较低,难以监测到热腐蚀缺陷。因此,不得不通过离线检测方法获得热腐蚀损伤信息,即在不损伤被检对象的情况下,借助声、电、磁、电磁波、中子、激光等手段检出缺陷的形态、大小和数量,最终建立热腐蚀损伤程度或其与失效因子(或剩余寿命)的映射关系。这种方法可以弥补状态监测的不足,从而为航空发动机视情维护的进行提供更好的支撑。
No.1 腐蚀的一般性特征
国家标准GB/T 10123-2001中对腐蚀的定义是金属与环境间的物理-化学相互作用,其结果使金属的性能发生变化,并常可导致金属、环境或由它们作为组成部分的技术体系的功能受到损伤。
可从不同角度对腐蚀进行分类,若按腐蚀机理分类,可分为化学腐蚀、电化学腐蚀、物理腐蚀和生物腐蚀;按是否受力分类,可分为无应力作用下的腐蚀和应力作用下的腐蚀;按腐蚀形态分类,可分为均匀腐蚀和局部腐蚀。
如图1所示,均匀腐蚀是指整个金属表面均发生腐蚀;而局部腐蚀即金属表面局部位置发生腐蚀,主要包含点蚀、晶间腐蚀、剥蚀、电偶腐蚀、缝隙腐蚀等。
图1 腐蚀形貌示意图
No.2 航空发动机高温结构中的腐蚀问题
航空发动机中的热腐蚀通常可分为Ⅰ型热腐蚀(高温热腐蚀)和Ⅱ型热腐蚀(低温热腐蚀)。一般认为Ⅰ型热腐蚀发生在800~950 ℃的温度范围内,此时沉积盐为熔融态,因此,Ⅰ型热腐蚀的损伤特征是在合金表面产生均匀的腐蚀层,属于均匀腐蚀;而Ⅱ型热腐蚀通常发生在650~800 ℃的温度范围内,此时沉积盐为固态和熔融态共存,其显著特征是形成点蚀坑,属于局部腐蚀中的点蚀。
航空发动机高温结构的热腐蚀与常温下有所不同,无论是腐蚀产物、还是腐蚀机理均存在差异。如常温下金属腐蚀产物可以是金属氧化物、氢氧化物、硫化物、卤化物等,而热腐蚀最终产物主要为金属氧化物和硫化物。
相比于一般腐蚀,热腐蚀反应复杂,目前典型的Ⅰ型热腐蚀机理模型主要有硫化模型、酸碱熔融模型。其中,硫化模型认为Ⅰ型热腐蚀发生时,金属中还原性组分与熔融盐反应还原成硫化物(MS),然后硫化物进一步与金属反应生成低熔点的金属-金属硫化物共晶(即M·MS),随后金属-金属硫化物共晶又进一步的氧化,生成氧化物(MO)和硫化物,硫化物再次与金属基体组分形成共晶,形成自催化过程。酸碱熔融模型则认为金属发生热腐蚀时,表面形成的具有保护作用的氧化膜在沉积的熔融盐中发生酸性(O2-浓度低,熔融盐呈酸性)或碱性(O2-浓度高,熔融盐呈碱性)溶解,导致金属的加速腐蚀。
相比于Ⅰ型热腐蚀,Ⅱ型热腐蚀发生的温度范围“较低”,沉积盐为固态或固液共存态,其腐蚀机理与Ⅰ型热腐蚀存在差异。Luthra描述了几种钴基合金在不同温度和SO3分压(PSO3)下发生Ⅱ型热腐蚀时腐蚀形貌和腐蚀产物的传输过程与分布,提出了钴基合金热腐蚀机理,这一机理还被推广到预测镍基合金的Ⅱ型热腐蚀行为。Ⅱ型热腐蚀条件下涂敷在合金表面的Na2SO4为固态,大气中如果有足够的PSO3便可以使得NiO或者CoO硫化以生成NiSO4或CoSO4。两种化合物将进一步与表面上过量的Na2SO4反应,形成液态共晶盐Na2SO4-MSO4(M代表Ni和Co)。低熔点共晶盐的存在使得合金表面出现熔融盐,熔融的混合硫酸盐通过溶解保护性的氧化层,并通过点蚀坑中的液体来传输反应产物,加快了腐蚀速率。这一混合熔融硫酸盐液相侵蚀的Ⅱ型热腐蚀机理目前被广泛接受。
另外,有研究者用电化学机理对热腐蚀反应过程(包括硫化物生成、疏松金属氧化物在熔融盐中的沉积等)进行了解释。他们认为引起热腐蚀的沉积熔融盐是离子导体,亦即是电解质,热腐蚀在几何上与薄水溶液电解质膜下的金属和合金的腐蚀形式极为类似,实际上是金属和合金在薄熔盐电解质膜下发生的腐蚀破坏。
发动机常见无损检测技术
无损检测技术种类繁多,常见的无损检测技术主要包括超声检测、涡流检测、磁粉检测、渗透检测、射线检测、光学检测、声发射检测等。从文献调研看,这些技术的大部分都已应用于航空发动机结构的检测维护之中。
超声检测技术主要利用超声波在界面(声阻抗不同的两种介质的结合面)处的反射和折射以及超声波在介质中传播时的衰减等性质来检测缺陷,是应用最广泛的无损检测技术。超声检测技术可对发动机金属或非金属结构进行检测,对于内部缺陷的定位定量检测较其他检测方法有综合优势,同时对裂纹、未焊透等缺陷也有较高的检测能力。超声检测技术在发动机压气机叶片、涡轮叶片、整体叶盘等结构的检测中均有应用。
涡流检测技术基于电磁感应现象对被检对象的性质或缺陷进行评价。涡流检测只适用于导电材料的检测,并且由于趋肤效应的存在,更适用于表面及近表面缺陷的检测,不太适用于较厚工件的内部缺陷检测。它对结构表面的缺陷比较敏感,且检测时不需要清理涂层。涡流检测技术对发动机涡轮叶片、榫槽、篦齿盘等结构表面裂纹的检测均有文献报道。
磁粉检测技术只适用于铁磁性材料缺陷的检测,它是利用被磁化工件表面或近表面缺陷形成的漏磁场吸附磁粉来显示缺陷。磁粉检测技术在发动机压气机叶片等结构表面裂纹的检测上有应用。
渗透检测技术是基于毛细作用和显影剂在一定条件下的发光现象对表面开口缺陷进行检测的一种技术。它不受被检对象材料的影响,但由于其检测原理,无法对多孔结构进行检测。有文献报道了渗透检测技术在发动机复杂机匣表面缺陷检测的应用。
射线检测技术是利用X射线、γ射线和中子射线易于穿透物体,但在穿透物体过程中受到吸收和散射而衰减的性质来检测缺陷的技术。射线检测技术对较薄结构内部体积型缺陷的检测更有优势,对于发动机涡轮叶片、机匣、火焰筒等结构缺陷的检测均有应用。
光学检测即利用光在传播时的反射、折射、干涉和衍射等特性进行直接观察被检对象形貌或间接测量其在加载时的表面变形来评价对象缺陷或性质的检测技术。在发动机结构的检测维护中,孔探仪是最常用的光学检测手段之一。通过发动机机匣上的探视孔,不用拆解发动机便可有效发现发动机压气机、涡轮、燃烧室的腐蚀、裂纹等损伤缺陷情况。
声发射检测技术是通过接收声发射现象产生的信号并进行一定的处理分析来对材料或结构的性质和存在的缺陷进行评价的技术。声发射检测的缺陷是动态的,且发射源为缺陷本身,对于缺陷发展过程中伴随着声发射现象的检测对象,它都是潜在的检测方法。目前声发射检测技术在飞机结构状态监测上已有应用,同时研究人员也在研究和探索其在发动机结构监测上的应用。
腐蚀的无损检测研究现状
No.1 点蚀无损检测研究现状
1、点蚀的声发射检测
金属点蚀发生时,常会伴随声发射现象。早在1984年,Arora便对铝合金点蚀过程产生的声发射特征进行了研究,结果表明数字化记录的声发射频率和波形分析有助于识别主动腐蚀过程。
Idrissi等以声发射作为评估方法,研究了2024T351铝合金点蚀不同阶段的声发射活动特征,并与氯离子浓度进行了相关性分析,得到了如下重要结论:在点蚀萌生的初始阶段无法被声发射检测到;但是,金属表面微气泡或大气泡气体释放时释放的能量是声发射探测的发射源,即当H3O+还原形成第一个氢微泡时,通过声发射可以立即检测到铝合金的点蚀现象。
Fregonese等对316L不锈钢点蚀过程的研究同样表明声发射源来自点蚀生长过程,而在点蚀萌生过程无明显声发射现象。这些研究揭示了点蚀过程中声发射现象的特点,体现了声发射技术用于金属材料点蚀检测的潜力。
声发射信号可分为突发型和连续型两种基本类型,一般以信号持续时间的长短进行区分。点蚀的声发射检测过程中受到各种随机因素的影响,既有连续型信号,也有突发型信号,属于非平稳的随机信号。典型的点蚀声发射信号如图2所示。对于不同类型的声发射信号,常采用不同的信号特征参数进行描述。突发型信号特征参数主要有撞击计数、振铃计数、上升时间、持续时间等,连续型信号特征参数有振铃计数、平均信号电平和有效电压。
图2 典型声发射信号
在点蚀发生过程中,两种声发射信号占比受到材料类型、溶液浓度等因素的影响。且在点蚀的三个阶段(点蚀萌生、生长、稳定)中,点蚀萌生阶段几乎没有信号(撞击计数、振铃计数)发出,声发射信号是在点蚀萌生后一段时间才出现。相对于点蚀萌生阶段,生长阶段声发射信号较多且增长较快,而稳定阶段增长变缓。点蚀声发射信号的这些特征是对金属点蚀进行检测的基础。
由于点蚀过程会伴随声发射现象,声发射技术在点蚀的监测上有较多研究与应用。王光卿等研究了储罐底板钢点蚀过程中声发射信号特征,对评估金属储罐罐底腐蚀程度,鉴别腐蚀类型具有一定的指导意义。Tang等在碳钢的声发射监测过程中采用开路电位测量并通过光学显微镜原位观察腐蚀形貌,开发了声发射信号处理和腐蚀类型识别方法。该方法能有效区分点蚀与均匀腐蚀,表明声发射技术可用于不同行业碳钢或不锈钢容器腐蚀的现场监测中。Wu等分析了单个点蚀坑在萌生和生长过程的声发射信号,认为腐蚀产物的开裂或流出可能是除氢气泡以外的另一声发射源。
声发射技术的点蚀检测效果显著,为人们进一步了解金属点蚀机理提供了手段。目前的研究主要集中在声发射机理探索和溶液环境中点蚀的检测,对于非溶液以及高温环境中点蚀的检测,声发射技术难以实现。
2、点蚀的涡流检测
通有交变电流的涡流检测线圈产生的磁场使试样表面产生涡流,试样表面的点蚀缺陷会导致涡流分布发生变化。涡流分布变化会影响线圈磁场分布从而使检测线圈阻抗发生变化,最终反映在输出信号发生变化。将带点蚀试样信号与对比试样输出信号进行对比,从而对点蚀损伤进行评估。
樊明亮等用不同半径不同深度的人工圆孔缺陷模拟奥氏体不锈钢点蚀损伤,通过建立的脉冲涡流实验系统提取缺陷出现的峰值来分析其响应特性用于点蚀缺陷的评估。李鹏改变带圆孔型腐蚀缺陷管道的包覆层厚度,发现涡流检测差分电压信号峰值随厚度的增大而增大,当包覆层厚度小于20 mm,信号峰值呈线性增加趋势,当超过这个厚度信号幅值增加变缓并在30 mm时趋于稳定。Yin等通过对传感器参数的优化设计,提出了一种基于解析优化的电涡流传感器的点蚀坑检测方法,结合数字电感测量系统和数据处理方法,检测系统具有较高的灵敏度,能够检测百微米级别的点蚀坑。
目前,研究者们在提升涡流检测技术对点蚀缺陷检测能力的研究上取得了不错的进展,主要体现在对隐藏点蚀缺陷和微小尺寸点蚀缺陷的检测上。
3、点蚀的超声检测
超声导波和非线性超声表面波由于特殊的传播性质常应用于检测点蚀。超声导波检测点蚀和通用的超声检测原理类似,主要是利用超声导波在试样中传播时遇到点蚀缺陷时的反射、散射等线性特征,并通过声速、衰减系数等进行表征,以判断点蚀的位置和大小。其本质是利用缺陷和材料声阻抗的差别来实现检测。非线性超声表面波对点蚀的检测则是利用点蚀缺陷与大幅度超声表面波相互作用产生的非线性效应(表现为产生高次谐波)来对点蚀缺陷进行评价。
超声导波检测信号按照检测方式的不同可分为A型显示和超声成像显示。A型显示是沿声传播方向的一维波形显示,表示的是超声信号的幅值和传播时间的关系,一般横坐标代表传播时间,纵坐标代表信号幅值。图3为无缺陷(图a)和有缺陷(图b)超声导波的A型显示信号。超声成像显示信号是综合了沿着试样截面某一方向(B显示)或沿着整个截面扫描(C型显示)得到的A型信号,能够显示缺陷的深度或形状等信息。图4为典型的超声成像C型显示,坐标对应的为扫查位置,坐标系中信号幅值以灰度显示。
图3 超声导波A型显示信号:(a)无缺陷;(b)有缺陷
图4 超声导波C型显示信号:(a)滤波前;(b)滤波后
非线性超声表面波表征点蚀损伤的参数为超声非线性系数,其定义公式如下:
其中,k为波数;x为超声波传播距离;A1与A2分别为频域信号基波与二次谐波幅值。图5为带有不同点蚀坑尺寸试样的超声非线性系数曲线图,当凹坑尺寸增加时,非线性系数也增加。
图5 超声非线性系数
点蚀在萌生和发展时具有较大随机性,其数量、位置分布、形貌等难以预测。数值模拟能够建立任意数量,任意分布、任意形貌点蚀坑模型,是研究点蚀缺陷对超声波影响的有效方法,可为点蚀的超声检测技术研究提供参考。
对超声波传播过程的数值模拟,合理设置模型网格尺寸、边界条件和积分时间步长等参数是关键。为了保证模拟精度,网格尺寸需根据超声波波长来确定,最大网格尺寸必须满足:
其中,λmin为最小超声波长,Δx、Δy、Δz为节点间距。超声波在遇到边界会发生反射,为了消除反射信号的干扰,常采用吸收边界或适当扩大模型尺寸的方法。积分时间步长是数值模拟的另外一个重要参数,决定模拟结果的准确性及精确度。超声检测模拟积分时间步长的选择需遵循Nyquist定律和Moser定律。
Shivaraj等采用高阶圆柱超声导波对管道隐蔽位置点蚀进行检测,并建立带针孔型缺陷的圆环二维有限元模型,观察了波在圆环中的传播方式,得到了含缺陷圆管的反射波纹图和反射能量值,并与实验结果进行了比较,两者吻合较好。王晓娟等针对管道常见的点蚀缺陷超声导波检测问题,通过有限元仿真对其反射回波信号进行分析,提出了确定仿真参数最优设置的优化策略,保证建模仿真的准确和高效。王腾腾构建了非线性表面波检测模型,模拟研究了蚀坑形貌参数对表面波传播行为的影响。
数值模拟是研究超声波在介质中传播行为的有效手段,为点蚀的超声检测研究提供了新思路。但是,由于超声波模拟需满足最大网格尺寸小于八分之一波长的要求,常导致过大网格数量的和过高的计算成本,这尤其限制了其在三维有限元分析中的应用。
2、 均匀腐蚀无损检测研究现状
均匀腐蚀是工业生产中常见的腐蚀形貌之一,往往导致构件大面积减薄。各种工程结构(如管道、储罐等)内部发生均匀腐蚀时常常难以及时察觉,为能减少这种隐蔽性损伤引起的结构破坏,研究者们对均匀腐蚀的无损检测进行了研究。
Jirarungsatian等将均匀腐蚀过程声发射源分为三类:腐蚀开始时金属表面损伤源;腐蚀在金属表面的形核和发展;腐蚀过程中气泡破裂,并选取信号持续时间和共振频率作为声发射参数对均匀腐蚀与点蚀进行分类。
李伟等分析了低碳钢均匀腐蚀过程的声发射信号特性,并对比实验条件下低碳钢腐蚀声发射信号与实际条件下储罐罐底腐蚀声发射信号的参数特征,为低碳钢均匀腐蚀过程声发射特征研究和储罐在线声发射检测提供参考。张春辉建立了一套提取均匀腐蚀声发射信号的实验系统,对均匀腐蚀各个过程进行声发射监测,分析了Q235均匀腐蚀气泡产生和金属溶解过程的声发射特征,运用小波分析相关理论对声发射信号进行处理,实现了对两种腐蚀模式的识别。
Yang等通过数值模拟、实验和现场实测,研究了均匀腐蚀对导波传播规律的影响。结果表明均匀腐蚀会产生相干噪声,使导波能量衰减,腐蚀层越厚,相干噪声越大,导波衰减速率越大。而使用较高的导波频率能降低相干噪声,但也会降低导波传播的能量。实测结果与数值模拟结果吻合较好,研究获得的结果有助于检查人员区分管道均匀腐蚀区域内的局部腐蚀,管道均匀腐蚀的有限元模型如图6所示。Shim等发现690合金蒸汽发生管均匀腐蚀行为与涡流检测旋转探头测量的管道噪声密切相关,因此,可将管道噪声用于预测其均匀腐蚀行为。
与点蚀相比,均匀腐蚀的无损检测研究较少。这些研究通过实验或仿真探索了均匀腐蚀对各种检测技术信号的影响,找到合适的信号特征是将这些技术应用于均匀腐蚀检测的关键。
图 6 管道均匀腐蚀有限元模型
3、 对腐蚀缺陷的识别与定位
在检测到缺陷后,有必要进一步的对缺陷类型进行识别并大致对缺陷进行定位。对于腐蚀缺陷的识别,根据声发射信号特征,可分辨处于不同阶段的点蚀,或对腐蚀严重程度进行判断。
另外,通过结合各种算法及信号处理方法建立的基于特征识别的腐蚀类型分类方法已能够实现对多种腐蚀类型的分类,如Tang等通过声发射信号的二维模式识别方法有效区分了低碳钢的均匀腐蚀与点蚀,Van等则利用小波分析及机器学习实现了无腐蚀、均匀腐蚀、点蚀、应力腐蚀开裂四种腐蚀模式的分类,分类准确度可达75.7%。
虽然腐蚀缺陷的危害性不同于一般的表面缺陷,但是目前基于声发射检测的缺陷类型识别的研究还较少,如在对于分辨腐蚀缺陷与其他类型缺陷(如外物打伤等)的研究几乎没有。
常规的超声检测对缺陷的识别主要通过人工判别试块和被检工件超声信号波形的差异来进行的,随着各种模式识别与分类方法的发展,超声检测对缺陷识别的研究与应用已趋于自动化,有效提高了缺陷识别的效率及准确性。
在腐蚀缺陷识别的研究上,Ghodsi等通过离散小波变换和离散傅里叶变换从超声Lamb波信号中提取基频频带作为信号特征对裂纹、局部减薄(厚度减薄程度与腐蚀试样近似,由电火花加工而成)、均匀腐蚀三种缺陷进行了识别与分类,分类准确度达到95%。图7所示为傅里叶变换后的三种缺陷信号。
图7 三种缺陷信号的FFT输出
Deng等利用分段主成分分析(S-PCA)法对实验和有限元法获得的铁轨超声导波信号特征进行提取后,利用支持向量机算法实现了裂纹缺陷和腐蚀缺陷的高准确率分类。
研究者们在研究超声检测的缺陷识别时,常使用机械加工的缺陷来代替真实的腐蚀缺陷,如禹化民用多种人工缺陷来模拟点蚀和腐蚀穿孔等缺陷。这种方法虽然简便,但只是真实缺陷的几何近似,图7中真实均匀腐蚀缺陷试样和人工减薄试样信号的差异在一定程度上说明了这种近似处理方法的局限性。
目前,已经有一些对于腐蚀缺陷厚度测量和重构的研究,Liu等发现合金基体与腐蚀层界面会产生一个微弱的回波信号,将时域信号转换成时频域信号后提高了信号对比度,通过测量信号飞行时间实现了对100 μm以下腐蚀层厚度的测定。这些研究表面了超声检测应用于更精确的腐蚀缺陷识别的潜力。
实际应用中,涡流检测对缺陷的识别同样需要通过比较被检工件与对比试样的信号差异。对涡流检测缺陷识别技术的研究中,大部分都是通过提取涡流信号的时域或频域特征,然后选择适当的数据处理方法及识别分类算法来识别缺陷。
目前,对腐蚀识别的涡流检测研究中同样使用了人工缺陷模拟腐蚀层或点蚀缺陷,如有文献用不同深度盲孔近似点蚀,也有文献用激光加工的不同厚度人工缺陷模拟多层结构中腐蚀导致的金属损失。这些研究很好地识别了缺陷的几何特征,但忽视了除几何特征外的腐蚀特征(如腐蚀层)的识别。
无损检测技术对包括腐蚀缺陷在内的各种缺陷识别的研究上大都是基于信号特征的识别,更优的信号处理技术、特征相关性算法和分类方法实现了对缺陷高准确度的识别。但是,对于多类型缺陷的识别上研究较少,且研究过程中预制的人工缺陷不能很好的反映真实缺陷的特征。
缺陷定位是无损检测技术的另外一个重要能力。声发射检测技术缺陷的定位即声发射源定位,主要是通过分析检测过程中传感器阵列接收到的信号来确定缺陷的位置。对于突发型信号可采用时差定位或区域定位等方法,对于连续型信号则可采用互相关式定位或衰减测量式定位法。
涡流检测对缺陷的定位主要依靠探头在工件表面移动时阻抗变化来确定。另外,由于涡流的趋肤效应,不同深度不同大小的缺陷信号幅值可能相同,此时需要利用相位分析来确定缺陷深度。
超声检测技术对缺陷的定位是通过超声波飞行时间来实现的。当超声波发射后,通过接收到缺陷回波的时间来计算缺陷位置,这种可以根据信号飞行时间来计算缺陷位置的方法被称为脉冲反射法。另外相控阵超声检测技术可以实现对缺陷的成像,从而直接显示出缺陷的位置。
目前,各种无损检测技术对缺陷识别的研究具有一定的局限性。大量研究未能考虑到腐蚀缺陷的特殊性,仅考虑了其几何特征。超声检测技术在进一步的腐蚀特征识别上表现了不错的效果,具有打破缺陷识别技术困境的潜力。各种无损检测技术对于缺陷的定位方法有一点差异。
总的来说,声学手段的检测技术主要通过计算信号飞行时间对缺陷定位,光学手段的检测技术主要通过成像显示缺陷位置,电磁手段的检测技术则依靠了传感器相对缺陷位置变化时检测信号的变化来实现对缺陷的定位。
4、 腐蚀缺陷的检测技术比较
各种无损检测技术中,光学检测、超声检测和涡流检测常应用于金属结构的腐蚀损伤无损评估,而对于管道、压力容器等运输和储存液体的结构,声发射检测技术也有广泛应用和研究。
对于腐蚀的检测,每种无损检测技术都有一定的优势和局限性,表1对其优势与局限性做了总结。不同技术不同的方法在不同类型的缺陷检测上将有不同的表现,应当根据检测需求结合技术或方法的特点选择合适的检测手段。
表 1 几种技术腐蚀检测的优势与局限性
基于无损手段的强度评估方法
无损检测技术在获得结构的损伤信息后,为了进一步评价结构劣化程度,一些研究者通过无损检测获得的损伤信息对结构的剩余寿命进行了评估。这些寿命评估方法大致可分成三类。
第一类方法通过无损信号特征直接与寿命联系来评估寿命。早在1956年,Truell等已经发现疲劳实验时铝试样中超声波信号的衰减与循环数存在联系。Joshi等基于这一现象测量了疲劳实验过程中铝和钢试样的超声波信号衰减,结果表明超声信号衰减对疲劳损伤非常敏感,可用于预测实际应用中的早期疲劳损伤和疲劳寿命。Birt等使用超声C扫描和涡流检测技术对试样的点蚀与缝隙腐蚀进行检测,发现无损检测信号与试样疲劳寿命有很好的相关性。阎红娟研究了超声非线性系数随金属构件弯曲疲劳寿命的变化趋势,提出了基于超声非线性综合参数与疲劳寿命的曲线,形成基于超声非线性和概率分析预测金属构件疲劳寿命的P-α-F方法。
第一类方法是最容易实现的方法,其寿命评价的精度取决于选择的信号特征是否合适。
第二类方法通过智能算法建立信号特征与寿命之间的联系。Shell等使用超声波测试、白光干涉显微镜和显微放射照相对试样进行检查来量化试样腐蚀损伤水平,为寿命预测模型提供输入,使用多元线性回归(MLR)和人工神经网络(ANNs)探究了无损信号和剩余疲劳寿命之间的相关性。Carson在自适应学习网络(ALN)中使用从超声信号特征(幅值、时间、频谱)中选择的特征来检测早期疲劳损伤并对剩余寿命进行预测。Ibekwe使用24组低周疲劳实验的声发射幅值数据来训练和测试用于预测寿命的反向传播神经网络(BPNN),最终得到一个能够预测失效寿命的网络。Spivey通过Kohonen自组织映射网络和反向传播神经网络,对收集的7075-T6铝合金试件的声发射数据进行了失效机理分类和疲劳循环次数预测。Okur拓展了Ibekwe和Spivey等的工作,利用声发射数据对铝合金缺口试样的裂纹扩展进行识别并预测其失效。
第二类方法通过相关算法找到信号特征中与寿命相关性最好的特征,是基于第一类方法的改进。尽管这两种方法所用的具体的分析模型不同,但都是引入能够反映热腐蚀缺陷尺寸的检测信号。因此,对于应力和载荷历程相对简单的机械结构来说是有效的。然而,对于涡轮叶片等来说,其几何结构复杂、应力分布不均匀,且应力分布和载荷历程的影响则显得尤为重要,采用第一、二类方法无法有效地进行评估。
第三类方法结合了无损检测技术和损伤力学的剩余寿命评估方法。朱旭程等提出一种基于力残差向量的损伤检测和结构寿命评估方法,即采用力残差向量进行桨叶的损伤定位和损伤大小估计,利用腐蚀疲劳裂纹扩展规律建立桨叶剩余寿命预测模型。程兴根据埋地燃气管道腐蚀深度发展规律建立了腐蚀发展趋势预测模型。
这种方法突破了前两种方法无法考虑腐蚀缺陷损伤过程的物理机制或规律的局限性。但是,无损检测得到的通常是局部损伤,因此,通过检测信息的反演与结构损伤演化过程的正演相结合才有可能进行准确评估。
发动机高温结构腐蚀损伤无损检测的难点
1、 腐蚀损伤检测能力对比
当无损检测技术应用于缺陷检测时,需了解该技术在检测中的灵敏度或检测能力。可检测到的最小缺陷尺寸越小,则检测灵敏度越高,检测能力越强。图8显示了在合适的应用场景下光学检测、超声检测、声发射检测和涡流检测在检测点蚀缺陷的能力。其中,当点蚀坑尺寸生长到某一尺寸时将发展为裂纹。
图 8 几种技术检测能力对比
光学检测能在点蚀萌生时便检测到点蚀坑;对于声发射检测,声发射信号通常出现在点蚀萌生后一段时间,对相关文献中点蚀坑萌生后的尺寸进行测量,尺寸约为60 μm。对于涡流检测,有文献使用涡流检测技术对单个点蚀坑进行了检测,所能检测到的点蚀坑直径最小约为592 μm,最小坑深约为148 μm。还有文献利用非线性超声表面波对单个点蚀坑进行检测,点蚀坑直径最小约为280 μm,最小坑深约为60 μm。
2 、发动机高温结构腐蚀损伤检测的应用难点
发动机高温结构服役环境恶劣,容易产生热腐蚀损伤。虽然各种无损技术已大量应用于金属结构腐蚀的检测,但对于发动机高温结构腐蚀的检测仍存在一些难点,主要体现在以下几个方面。
首先,结构几何形状复杂导致技术难以应用。虽然实际结构大都几何形状简单或可由简单结构组成,在各种无损检测技术的研究上,对简单结构进行研究已能够满足大部分工程应用的需求,但发动机高温结构(典型的如涡轮叶片)大都具有复杂几何形状和结构。对于这类复杂构件,一些无损检测技术难以较理想的应用。如用反射法对不规则的变厚度工件进行超声检测时,各扫描点的界面波和底波位置随工件形状变化而变化,难以确定缺陷位置;超声波在进入复杂几何构件后,存在波束变形、方向偏移、灵敏度损失等问题,导致检测性能下降;另外,复杂几何形状导致的换能器接触不良、换能器移动时的定向障碍都会使检测灵敏度下降,导致无法正确表征缺陷。
其次,对于高温结构使用的各向异性材料(如定向凝固高温合金、单晶高温合金),材料的各向异性还会导致超声检测信号产生散射、模式耦合、能量聚焦和衰减,对缺陷检测带来不利影响。不少研究者为改善这种状况已经做了一些努力。Putkis等选择具有更优分辨率与灵敏度的检测信号频率和传感器位置来减弱碳纤维复合材料各向异性对导波检测的影响。Wang等则使用带双矩阵阵列探头的自动相控阵系统实现了各向异性焊缝中缺陷更高准确度的识别。
最后,检测能力不足将导致小缺陷无法被有效检测。图9所示为CF6发动机断裂涡轮叶片上的点蚀坑截面形貌,该点蚀坑尺寸约83 μm。对于非承力或承力较小结构,腐蚀在较严重时才会影响其功能,此时无损检测技术检测能力绰绰有余,在腐蚀威胁结构安全前缺陷已被检出。而对于承受巨大疲劳载荷的发动机高温结构(如发动机涡轮叶片),类似图9所示的小尺寸腐蚀缺陷难以在维修维护时被有效检出,此时该缺陷已经足够威胁到结构的安全运行。有文献报道了CF6发动机涡轮叶片断裂的事故便是维修时未检测到低温热腐蚀产生的小尺寸腐蚀坑导致的。
图9 涡轮叶片点蚀坑形貌
结论与展望
对于均匀热腐蚀和点蚀两种典型腐蚀的检测,光学检测、声发射检测、涡流检测和超声检测最为常用。对比了这几种检测技术对腐蚀的检测能力、技术的优点及局限,其中光学检测具有最高的检测能力,但是难以检测隐藏的腐蚀;声发射技术具有较高灵敏度,能实时监测腐蚀,但是只适合在溶液环境中应用;涡流检测和超声检测技术都可实现百微米级别点蚀坑的检测,对于隐蔽腐蚀有不错的检测能力。
在实现对缺陷检测的同时,研究者们更进一步的探索了无损检测信号特征与结构疲劳寿命的联系,或结合无损检测技术与损伤力学方法建立了剩余寿命模型,对结构剩余寿命进行了评价。无损检测技术的应用为结构疲劳寿命预测提供了新思路。
然而,由于发动机高温结构的复杂性、材料的各向异性等,当前的无损检测技术虽然能够检测管道、压力容器等结构的腐蚀,但是对发动机高温结构腐蚀的检测仍存在难点。
在腐蚀的无损检测技术研究与应用上仍然有巨大的进步空间,基于本文的综述,以后的研究重点应该在以下几个方面:即对复杂结构的检测;实现更强的检测能力;同时采用多种检测技术的结合对复杂结构进行全面精确的检测。
此外,一方面应重点关注无损检测与其他技术(如信号处理、人工智能等)的结合;另一方面,无损检测获得了结构的损伤信息后,如何利用固体力学知识对结构的剩余寿命进行评价,这是无损检测技术走向无损评估研究的一个重要方向。
来源:航空动力学报、两机动力先行
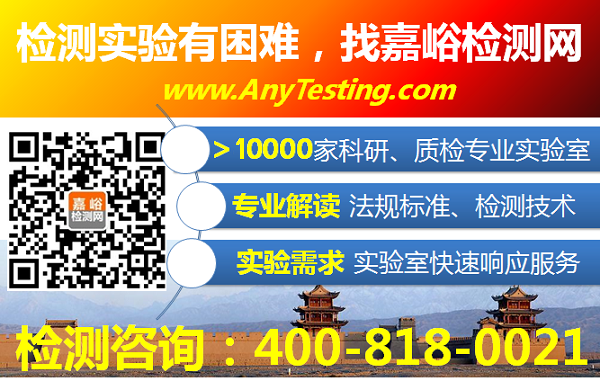