引 言
电泳过程中磷化层和电泳层成膜质量不仅决定了车身的防腐性能,同时还对涂装中面漆车身的外观有着至关重要的影响。可以说,电泳车身质量是汽车整车物化性质的重要组成部份。因此,严格控制电泳漆膜质量是前处理-电泳线工艺的重点工作。电泳漆膜颗粒、纤维、溢胶等质量问题是目前行业内面临的共性问题,而这些又主要由生产过程中的杂质影响。考虑到前处理电泳线各槽体区域相对封闭,外部污染源进入槽体机会较少,在电泳过程中杂质主要由白车身带入槽体,是污染前处理电泳线各槽体槽液的重要原因之一。提升前处理白车身洁净度进而减少污染物的带入量,能够显著降低员工打磨工作量,改善成品车外观质量。因此,本文主要针对白车身带入杂质进行分析,对各因素从源头进行严格防治、改善和解决,这对于控制电泳质量的良性循环具有良好的参考意义。
检测分析结果显示,由焊装进入涂装车间的车身洁净度影响因素包括焊球、油脂、涂胶溢胶、灰尘等,此类影响因素的产生受到人、机、料、法、环等各方面影响。陈磊、李平等人分别针对电泳漆膜缺陷类型进行分析,结果表明:由于焊接工艺影响直接或间接导致的缺陷分别占比40%和81%,纤维分别占比18%和4%,考虑焊装胶的影响,此影响因素占比高达到39%。为此,应该重点关注铁屑,焊装胶,纤维等影响因素,严格控制此类影响因素能够显著提升车身电泳漆膜质量。图1和图2汇总了某段时间两款车型白车身洁净度质量和车身前盖颗粒状态变化趋势,可见漆膜质量与洁净度正相关。结合前处理-电泳段清洁容量和电泳质量要求,公司严格制定白车身洁净度工艺标准,执行洁净度降低计划,白车身洁净度管控标准调整为低于5g/台。本研究针对不同白车身影响因素和缺陷类型进行总结分析。
图1 白车身洁净度管控变化趋势
图2 车身前盖颗粒状态变化趋势
1、白车身洁净度影响因素
1.1焊球、焊渣
焊球、焊渣一直都是白车身主要污染物,因焊球、焊屑导致的电泳漆膜缺陷数量也一直是占比最高,焊球、焊屑产生的最常见的质量缺陷为电泳漆膜颗粒,也是造成电泳漆膜表面粗糙度增加的主要原因之一。图3与图4就是典型的因焊球、焊屑导致的电泳漆膜颗粒缺陷。
图3 焊球导致的电泳漆膜颗粒
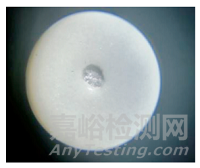
图4 焊屑导致的电泳漆膜颗粒
从实际的生产过程统计来看,焊渣、焊球的粒径存在一定的差异。根据生产线工艺的不同,一般都会使用不同精度的过滤袋进行过滤。像洪流、预脱脂、脱脂等槽体的过滤装置能过滤大部份的焊球、焊屑。但同时,一些细小粒径的焊球、焊屑会透过过滤袋,在槽体内沉积,并随着槽体内循环吸附于车身表面和缝隙,随车身进入后序工艺,造成硅烷、电泳等槽体污染,进而形成电泳颗粒等质量缺陷。此类缺陷一般采用400或600砂纸等低目数砂纸进行打磨处理,但会导致打磨区域电泳粗糙度的增加,进而影响后续中面涂工序的车身质量(比如车身短波),若需要重打磨,往往会打磨至漏铁,这对于车身防腐造成严重影响。
1.2油脂
白车身洁净度的另一个重要因素是油脂。一般而言,考虑到防腐等目的,白车身在冲压前及冲压的过程中都会使用了防锈油、拉延油等进行处理。在焊装车间,并不会对上述油脂进行专门的处理,因此,进入涂装车间进行生产的车身会存在较多的油污(见图5),这对涂装的除油提出了较高的要求。
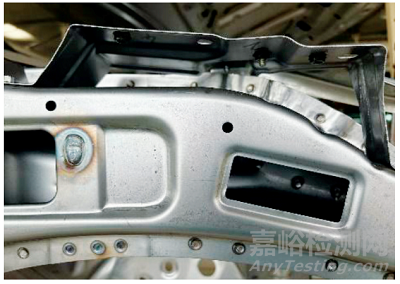
图5白车身内板油污
常见的汽车涂装生产线,一般会在前处理线配备预脱脂、脱脂工序,通过在槽液中添加脱脂剂、发泡剂等药剂,对白车身油脂进行皂化以达到除油的效果。若除油不彻底,油脂会随车身夹带至后续工序,进而污染槽体。同时,在油脂的作用下,电泳过程中油污附着的地方会影响漆膜生成,进而导致上漆不良或电泳缩孔等质量问题。电泳缩孔往往需要进行重打磨处理,对车身的防腐也会造成一定的影响。
1.3溢胶
白车身溢胶主要来自于焊装车间,焊装涂胶按功能主要分为结构胶、减震胶、密封胶,折边胶等,各类涂胶的应用确保了车身的密封性,同时提升了车身的整体结构强度,为汽车提供了密封性、减震性等功能。但目前的涂胶工艺还存在较多缺陷,无论是机器人还是人工,都无法对喷胶量和涂胶位置等做到精确控制,现场常以涂胶上限确保符合工艺要求。若涂胶偏少,则会造成空腔存液,后续电泳烘干过程中造成电泳二次流痕等问题,同时,滚边等工艺易造成胶体溢出。
图6白车身溢胶
溢胶会造成电泳车身局部电泳漆上膜不良或堵件安装孔位堵塞。因此,白车身溢胶也是影响其洁净度的重要原因。同时,由于白车身的涂胶一般未经过烘干,在进入涂装车间前处理电泳线后,由于各槽体的喷淋压力较大,会对溢胶部位进行冲刷,导致胶体掉落至槽体内,在后续的生产过程中,附着在车上而形成大块的电泳渣等,后续电泳打磨等工序需要花费较大的精力进行打磨、补喷防锈底漆等。
1.4纤维、灰尘
白车身在行进的过程中,环境中的灰尘、纤维等易沾染环境灰尘,纤维会掉落至车身,在油脂的粘附下难以脱落。此外,冲压、焊装工作人员衣服,手套,清理工具也会产生纤维、灰尘并掉落及吸附至白车身中。纤维、灰尘虽然在白车身的污染源中占比相对较少,但依然会造成电泳漆膜纤维、颗粒等质量缺陷,也涉及到砂纸的打磨。
以上从白车身的生产工艺过程,梳理了白车身的主要污染物。以白车身预处理工序为控制节点,首先通过分析各缺陷产生原因,对各影响因素产生根源制定相应的改善措施,达到白车身污染物的防治与改善目的。以白车身表面可擦拭的污染物质量总和<5 g为控制标准。通过改善涂装车间预处理的清洁能力,主要针对重点区域清理,规范清理过程和要素,实现槽体杂质清除量≥污染物带入量,提升车身表面电泳质量。
2、产生来源和预防措施
2.1焊球、焊渣、铁屑
产生来源:
(1)冲压件加工中,由于未达到工艺和质量要求,焊渣进行打磨后铁屑飞溅至工件上;
(2)焊装车间中,焊接过程中产生的飞溅焊渣会掉落在车身的内仓和空腔中;
(3)对于未达到焊装质量要求的焊点,或者焊接过程中产生的应力集中造成的局部变形需要进行打磨;
(4)车门铰链等结构相对位移区域会相互磨损,产生碎屑和漆渣;
(5)钢板缝、焊缝区域以及其他难以清理的杂质容易积存。
解决及优化措施:
(1)为了减少打磨量并及时清理,需要保持模具的洁净度,避免铁屑造成的冲压件二次缺陷;
(2)定期更换焊钳滑块,避免大量飞溅焊渣;
(3)提升冲压件的精度,避免匹配性差造成的焊接铁屑增加;
(4)提升冲压件的精度,避免匹配性差造成的焊接铁屑增加;
(5)在焊装指定区域安装吸尘器、压缩空气等清理工具,并将洁净度检查纳入作业指导方案;
(6)优化车身清洁计划,避免重复、无效清理;
(7)优化车身沥液孔位,便于焊装焊渣、铁屑清理及后续涂装工艺沥水;
(8)针对焊接过程中的飞溅焊渣问题,可以通过优化焊接工艺参数和使用适当的保护设备来减少飞溅的产生;
(9)涂装车间可在洪流水洗(或预备水洗)、预备脱脂、脱脂等工装安装磁性过滤器或者悬液分离器,提升对槽液的过滤效果,提升槽液清洁度;
(10)可在电泳前各槽体底部及两侧、副槽底部等防止磁棒,吸附槽液中焊球、焊屑,通过人工使用高压水枪的方式,定期对磁棒进行清洗、更换;
(11)提升电泳前各槽体过滤袋精度,提升过滤效果,但此方法会增加过滤袋的用量;
(12)加大洪流水洗、水洗1、水洗2等水洗槽体换水及清洗的频次,通过排放掉污染严重的槽液,减少对后工序槽液的污染。
2.2油脂
产生来源:
(1)冲压车间加工过程中,会使用到润滑油、拉延油等油品用于改善冲压成型状态;
(2)白车身板材在运送及保存的过程中,为了避免生锈,会在上面刷涂一层防锈油。
解决及优化措施:
(1)选用可清洗性较好的加工用油;
(2)优化运输、保存的环境,降低环境相对湿度,尽可能减少防锈油的用量;
(3)根据涂装车间的清洗能力和工艺特性,进行油品选择及制定用油标准;
(4)提升涂装预脱脂、主脱脂的游离碱度,提升槽液温度,缩短槽液更新周期;
(5)使用镀锌钢板替代冷轧钢板,降低运输、保存、冲压过程中的用油量。
2.3涂胶溢胶
产生来源:
(1)装配零件匹配若存在不良,板材缝隙较大或挤压会造成涂胶偏少或溢出;
(2)由于胶体粘附性问题,造成涂胶缺陷;
(3)手动涂胶过程中,未能准确控制胶量及涂胶位置。
解决及优化措施:
(1)优化自动涂胶的路径和准确度;
(2)提升设备稳定性,优化员工可操作性;
(3)保证板材的表面洁净度,避免胶体粘附问题;
(4)保证焊件尺寸和精度的情况下,优化装配作业。
2.4纤维、灰尘
产生来源:
(1)作业环境中的尘土、打磨灰、纤维等污染物;
(2)工作人员衣服、鞋底灰尘带入;
(3)擦布、拖把等清理工具掉落等。
解决及优化措施:
(1)定期更换车间循环空调过滤网;
(2)定时针对产线表面、生产工具等清理;
(3)完善保洁工作和检查制度,对于现场问题及时反馈处理;
(4)将清理工位进行隔离,避免污染物的二次污染;
(5)定期维护通风系统,定期更换过滤器。
3、车身预清理措施
3.1重点区域清洁
针对白车身洁净度,本研究分别制定了上述相关措施,但若能在涂装预清理工位对白车身的入涂质量进行管控,无疑是最经济、最有效的方式。预清理工位作为涂装车间的门户,也是涂装车间第一道质量控制点,在预清理工位对白车身洁净度进行管控及处理,一方面可以提升车身电泳后的总体质量,另一方面也能减轻涂装前处理电泳线对白车身污染物的处理压力。一般来说,目前各大车企都会在预清理工位增加人工对车身表面重点区域的清理作业。常见的方式包括气枪吹扫、黏性布擦拭、吸尘器吸附等。以进一步控制白车身洁净度,减少杂质带入量,从实际的白车身洁净度的统计来看,重点清洁的区域包括以下几个部位:前盖,两侧车门,两侧车门铰链区域,后盖,顶盖,顶盖流水槽。上述部位均为白车身外表面,一般仅需通过擦布单方向沿区域清理进行手工擦拭即可,通过定时定量更换擦布,提升清洁质量。此外,像前盖流水槽和发动机内舱区、前后地板等区域相对封闭,且焊缝较多,焊缝内的焊渣、铁屑很难通过黏性布进行擦拭的方式进行处理,可通过压缩空气吹扫配合吸尘器吸附的方式进行处理。
3.2注意事项
对于预清理工位对白车身的清洁工作,在实际的操作过程中,应当注意避免清洁过程中因为操作及作业方式不当导致的二次污染产生。比如,在清洁过程中,使用黏性布擦拭时经常会出现很多细小纤维,影响漆膜的质量。因此,在实际的操作作业过程中,员工需要注意避免车身边缘与黏性擦布直接剐蹭,从而减少绑带、擦布产生的细小纤维。同时,在对白车身大顶进行清洁的过程中,还需要特别注意车顶流水槽及螺柱等位置,避免擦拭布碎屑掉落。这些细节问题看似微小,但对于车身漆膜的质量和外观却具有重要影响,需要引起足够的重视和关注。最后,由于白车身未经过涂装,内外板存在较多尖锐、锋利等边缘,因此,在预清理工位对白车身进行清洁的过程中,一定要佩戴好安全帽、防割手套、口罩等劳保用品,避免作业过程中,员工被刺伤、割伤等。
4、结 语
电泳漆膜是汽车车身表面涂装过程中最为重要的一道工序,其质量直接影响到后续整个车身涂装质量和车身外观的美观度。然而,电泳漆膜缺陷的出现却常常给涂装的生产带来不小的困扰。白车身杂质是电泳漆膜缺陷的重要污染来源,而其影响因素众多,因此需要对杂质和缺陷影响因素进行全方位优化和改善。白车身洁净度不仅受到生产环节、工艺流程、操作技能等方面的影响,还与原材料的质量、仓储条件、物流运输等方面息息相关。因此,需要从多个角度对白车身的洁净度进行改善。总之,优化白车身洁净度是防治电泳漆膜缺陷的重要措施之一。只有全方位进行优化和改善,从根源上预防和解决问题,才能保证电泳漆膜质量的稳定和可靠。
本研究针对白车身积极度的提升提出的改善建议,是基于作者长期从事涂装前处理电泳工艺管理的作经验进行展开,但由于不同厂家的生产工艺存在差异,因此无法面面俱到,同时,上述措施由于工艺上的差异,在实际的执行过程中的效果可能会出现差异。
作者 | 赖云飞,李文博,李文鹏,等(合众新能源汽车股份有限公司,浙江桐乡 214500)
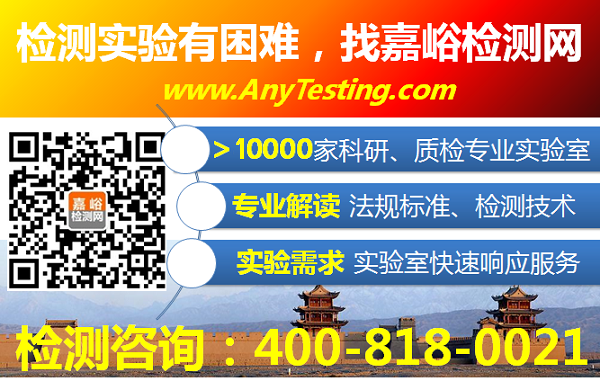