随着工业不断发展,市场对轴承的质量要求越来越高。滚子作为轴承中的滚动零件,关系到轴承工作时的动态性能,因此滚子的加工工艺必须达到国家标准要求。滚子也是轴承中最薄弱的地方,如果滚子表面存在裂纹,当其工作于高速重载条件下时,不仅工作精度和使用寿命等会受到影响,裂纹还会进一步扩大,而最终导致轴承失效,造成重大安全事故。因此,需要对滚子表面质量进行检测。
国内外研究学者对于轴承滚子的检测研究从接触式逐渐发展到非破坏性、非接触式的无损检测。无损检测是在保证不损伤检测工件的前提下,对检测对象进行质量评估以及缺陷检出定位等的技术。目前轴承滚子的主要检测方法有磁粉检测、涡流检测、光电检测、超声检测、机器视觉检测等。
磁粉检测法适用于零件表面以及近表面裂纹检测,检测效率低,且存在污染;涡流法难以检测内部缺陷,同时受背景磁场影响较大;光电检测法精度要求较高,易受检测过程中的振动、抖动影响;超声法检测效率低,存在表面检测盲区,且检测时需使用耦合剂,影响后续工艺进程;机器视觉法只能检测滚子的表面缺陷,同时滚子表面光滑、粗糙度低,易发生镜面反射导致成像质量差。
与以上检测方法相比,漏磁检测具有检测效率高、自动化程度高及无污染等特点,同时检测灵敏度高,能够有效检出裂纹、表面划伤、凹坑等缺陷。基于漏磁检测原理,提出了一种轴承滚子微细裂纹漏磁检测方法,可适用于不同规格及复杂检测工况下的轴承滚子检测。
1、漏磁检测方法
漏磁检测利用磁源对铁磁性工件进行磁化,磁场主要分布在工件内部;如果工件存在裂纹,部分磁通会泄漏到工件表面的空间中,并在工件裂纹处激发形成漏磁场,检测时采用磁传感器来拾取漏磁场信号从而获得裂纹信息。轴承滚子漏磁检测原理如图1所示。
图1 轴承滚子漏磁检测原理示意
根据该检测原理,提出了轴承滚子微细裂纹漏磁检测方法,设计了漏磁检测系统,如图2所示。该系统主要由磁化器、轴承滚子、检测探头、信号处理系统等4部分组成。检测时,磁化器将滚子磁化到近饱和状态,裂纹处磁场泄漏到空气中,探头拾取到漏磁场,将漏磁信号转化为电信号,传输到信号处理系统中进行放大、滤波等处理,最终得到裂纹信号,实现对轴承滚子表面裂纹的检测。
图2 轴承滚子漏磁检测系统结构示意
2、仿真分析
为了对该检测方法进行验证,建立如图3所示的仿真模型(Q为内部测点,P为外部测点),研究滚子表面的背景磁场及漏磁场特性。
图3 轴承滚子磁化仿真模型
滚子直径(D)为30 mm,裂纹深度(h)为100 μm,宽度(b)为100 μm。材料设置为GCr15,磁化线圈匝数为600匝,通5~10 A的电流。内部测点Q(距离滚子表面0.4 mm)磁感应强度随电流强度的变化曲线如图4所示;在外部测点P(距离滚子表面0.4 mm)处测得背景磁场与裂纹的漏磁场强度(将裂纹处材料设置为GCr15),计算得到无裂纹处背景磁场与电流大小的关系,如图5所示;进而得到不同电流强度下裂纹的漏磁场信号,如图6所示。
图4 滚子内部磁场强度随电流强度的变化曲线
图5 无裂纹处背景磁场强度随电流强度的变化曲线
图6 不同电流强度下裂纹的漏磁场信号
对于同一尺寸的裂纹,磁化强度越大,滚子内部近表面的磁感应强度越大,裂纹产生的漏磁场强度越大,传感器越有可能拾取到裂纹信号。根据图6可以看出,随着电流强度的增大,滚子近表层的磁感应强度不断增大,当磁化电流为9 A时,外壁检测区域的磁感应强度为1.6 T,接近饱和磁化。因此,线圈通电电流选取为9 A,此时滚子表面的背景磁场大小为37 mT。
在滚子表面设置宽度为100 μm,深度分别为15,30,50,100,150,200 μm的裂纹,磁化电流设置为9 A,在滚子表面提离0.4 mm处,沿扫描路径提取不同深度下的切向漏磁感应强度分量Bt,Bt随裂纹深度的变化曲线如图7所示。
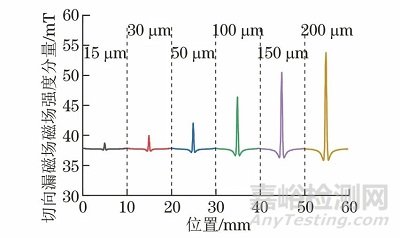
图7 切向漏磁场磁场强度分量随裂纹深度的变化曲线
由图7可知,磁场在光滑表面分布均匀,缺陷处波形出现一个单峰;在缺陷正上方,磁场磁感应强度达到最大,裂纹越深,磁感应强度越大,且信号幅值与裂纹深度呈线性关系。
3、基于测点区域近零磁场调控的TMR测磁方法
在漏磁检测过程中,对于不同规格的滚子,随着滚子直径的增加,所需磁化强度越来越大,而表面微细裂纹产生的漏磁场强度较小,检测要求更加严格。因此,利用漏磁检测方法对滚子进行微细裂纹检测时,存在漏磁场小,背景磁场大的检测问题。漏磁场的拾取主要依靠磁传感器,较大的背景磁场会导致传感器超量程饱和,出现灵敏度降低、信号失真甚至无法检测出信号等问题。常用的霍尔元件线性范围大,但灵敏度较低,TMR(隧道磁电阻)传感器相较于霍尔传感器、AMR(各向异性磁阻)以及GMR(巨磁阻),具有良好的温度稳定性,同时检测灵敏度更高。基于以上问题,选择TMR传感器拾取信号,结合仿真得到的背景磁场磁感应强度,提出了基于测点区域近零磁场调控的TMR测磁方法。
对不同规格或不同工况的轴承滚子进行检测时,需要施加不同强度的磁化场,改变检测探头所处的背景磁场强度。因此,设计了线圈电磁磁化的偏置检测探头,建立基于线圈磁化回路的自适应测点近零磁场环境。基于线圈偏置的TMR传感器检测原理如图8所示,探头主要由TMR传感器、霍尔元件、磁轭、线圈组成,TMR传感器选用多维2001型号;选用0811型霍尔元件测量TMR传感器所处位置背景磁场的大小;磁轭选用高磁导率、低损耗的硅钢片制作而成,用以聚磁、传导磁场;线圈采用直径为1 mm的漆包线制作,包裹在磁轭外,用以产生与背景磁场相反的偏置磁场,对TMR的背景磁场进行调控,使得其工作在高灵敏度区,并且具有较强的抗外界电磁干扰能力。在实际漏磁检测中,测点处测量得到的磁感应强度为线圈磁化后产生的漏磁场磁感应强度与施加的反向偏置磁场共同作用后的磁感应强度。
图8 基于线圈偏置的TMR传感器检测原理
建立直径为30 mm的轴承滚子模型,滚子表面设置宽度为100 μm,深度为100 μm的刻槽,磁化线圈匝数为600匝,磁化电流为10 A。传感器偏置磁场的磁感应强度设置为35 mT,仿真得到加偏置磁场前后的裂纹漏磁场信号如图9所示,检测区域背景磁场下降至约0 mT,根据仿真结果显示加偏置磁场前后裂纹处的漏磁场云图如图10所示,可见反向的偏置磁场对滚子的磁化状态有一定影响,但影响较小,漏磁场强度峰峰值下降15%左右,不影响信号检出。
图9 加偏置磁场前后裂纹的漏磁信号
图10 加偏置磁场前后裂纹处的漏磁场云图
为了保证偏置电流能够随背景磁场变化而相应改变,采用了电流反馈控制系统,主要包括PLC控制模块、模拟量模块、可控硅电源调节模块。控制调节变压器初级线圈中可控硅的导通角,即可改变变压器初级线圈的电压幅值,从而改变变压器次级线圈的输出电压,达到控制偏置电流大小的目的。
根据设定值对PLC模拟量输出端给定一个初值,初始输出电流为0 A,在输出初始电流后,再检测霍尔传感器的输出电压值,并将其作为输入端信号;比较霍尔元件在静态时输出的电压值与磁化后的输出电压值,然后根据比较结果进行增量电流调节,微调量(ΔI)取0.1 A,形成一个闭环调节的反馈回路,使得输出电流满足要求。
4、检测试验
为了对该测磁方法进行验证,搭建如图11所示的试验平台,选取如图12所示,直径为30 mm的轴承滚子进行检测,工件表面刻有周向分布的标准伤,长度为10 mm,宽度为100 μm,深度为100 μm,检测探头如图13所示。
图11 轴承滚子漏磁检测试验平台
图12 检测工件外观
图13 检测探头外观
未磁化时,霍尔元件输出电压为0 mV;磁化线圈加载10 A激励电流,此时轴承滚子处于近磁饱和状态,滚子表面的背景磁场强度为15 mT,霍尔元件输出电压为50 mV;偏置线圈调节电流输入为2.2 A时,霍尔元件输出电压归于0 mV。探头采集到10 A电流偏置前后的输出电压信号如图14所示。
图14 10 A电流偏置前后的输出电压信号
采用上述试验平台,检测工件上刻伤裂纹深度分别为15,30,50,150,200 μm(其中15,30 μm深裂纹采用标准磁粉试片代替),得到偏置前与偏置后输出电压信号峰峰值与裂纹深度的关系曲线如图15所示。由图15可见,在一定条件下,随着裂纹深度的增加,输出信号峰峰值呈线性增加,偏置后的输出信号幅值相较于偏置前的信号幅值明显增大。
图15 10 A电流偏置前后输出电压信号峰峰值与裂纹深度的关系曲线
经过数据统计与计算,得到10 A电流激励下不同深度裂纹的信噪比如表1所示,可见偏置后裂纹漏磁信号的信噪比明显提升,对于15 μm深的裂纹,偏置前无信号,偏置后可检出信号。
表1 10 A电流激励下不同深度裂纹的信噪比/dB
激励电流为15 A时,轴承滚子处于磁过饱和状态,滚子表面的磁感应强度为24 mT,霍尔元件输出电压为85 mV。偏置线圈调节电流输入为3.5 A时,霍尔元件输出电压归于0 mV。深为100 μm的裂纹15 A电流偏置前后的输出电压信号如图16所示,15 A电流偏置前后输出电压与裂纹深度的关系如图17所示,可见过磁饱和状态下,TMR传感器拾取到的信号很小,调节偏置电流后,探头才能有效拾取到裂纹信号。15 A电流激励下不同深度裂纹的信噪比如表2所示。
图16 深为100 μm的裂纹15 A电流偏置前后的输出电压信号
图17 15 A电流偏置前后输出电压与裂纹深度的关系
表2 15 A电流激励下不同深度裂纹的信噪比/dB
由表2可见,对于15,30 μm深的裂纹,偏置前无信号,偏置后可检出信号,偏置后不同深度裂纹的检出率均有提升,且与近饱和磁化状态下相比较,信号的信噪比略有提升,即对于不同背景磁场强度下的漏磁检测,该偏置探头均可调节偏置电流的大小,建立良好的测点区域近零磁场环境。
结 语
(1) 基于漏磁检测原理,提出了轴承滚子微细裂纹漏磁检测方法,并通过仿真分析了裂纹产生的漏磁场特性。
(2) 提出了测点区域近零磁场调控的TMR测磁方法,并设计了线圈电磁磁化的偏置检测探头,建立基于线圈磁化回路的自适应测点近零磁场环境,使得探头能够适用于不同工况下的漏磁检测。
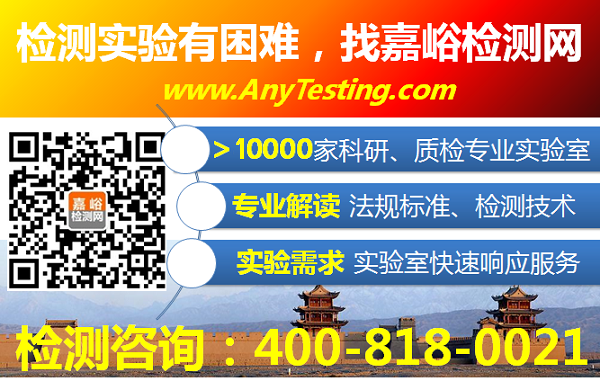