某车型发动机在进行200h交变载荷台架试验时,其安装支架发生断裂。该发动机为4点式支撑结构,断裂支架为右后侧支架。支架材料为HT250灰铸铁,生产工艺为熔炼→浇注→机械加工→电泳黑漆,断裂支架尺寸如图1所示。支架的技术要求为:附铸试棒抗拉强度不小于250MPa,铸件本体硬度不小于200HBW,石墨形态为A型,基体组织为珠光体,且珠光体质量分数不小于98%。研究人员采用宏观观察、扫描电镜(SEM)分析、化学成分分析、金相检验等方法分析了支架的断裂原因,并提出改进措施,以防止该类问题再次发生。
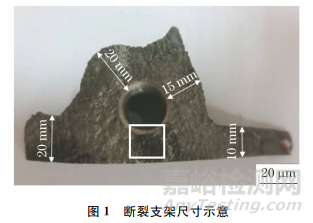
1、 理化检验
1.1 宏观观察
目视观察整个断面,发现其无塑性变形及明显剪切痕迹,断面呈暗灰色,无金属光泽。进一步观察后,发现一条贯穿裂纹,裂纹宏观形貌如图2所示。
由图2可知:该裂纹靠近底部边缘处较宽,裂纹向孔的方向延伸并逐渐变窄,裂纹较宽的位置已产生红褐色的腐蚀产物,主要为铁的氧化物,由此可知裂纹起源于底部边缘处。
1.2 扫描电镜分析
超声波清洗断口后,在断口上截取试样,将试样置于扫描电镜下观察,断口SEM形貌如图3所示。
由图3可知:底部边缘处发现少量微裂纹,其中图3b)为图3a)方框处的形貌;裂纹起源于表面微小缺口处,并向基体内部延伸扩展;基体上无规则分布着少量清晰可见的微小孔洞[见图3c)]。
1.3 化学成分分析
采用火花直读光谱仪对支架材料进行化学成分分析,结果如表1所示。由表1可知:C元素和 Si元素质量分数接近技术要求的下限值,其余各元素质量分数未见异常,计算可知硅碳比为0.568。
1.4 金相检验
在断裂支架上截取金相试样,对试样进行磨制和抛光后,将试样置于光学显微镜下观察,结果如图4所示。由图4可知:石墨形态均为E型,呈一定方向分布于枝晶间,同时存在少量的石墨团聚;用体积分数为4%的硝酸乙醇溶液腐蚀试样后,可观察到其显微组织为珠光体。
2、 综合分析
由上述理化检验结果可知,发动机支架断裂的直接原因是石墨形态不合格,基体中存在大量E型石墨。相关文献研究表明,灰铸铁中石墨的分布形
态、尺寸以及基体组织是决定灰铸铁力学性能、疲劳性能等的主要因素。石墨几乎没有强度,其在基体中相当于显微缺口,理论分析及大量实践证明,A型石墨最好,C型、E型石墨对基体有割裂作用,不允许出现。发动机支架的最小厚度仅为10mm,由于壁厚较薄,浇注时冷却速率较快,过冷度较大,虽然铸铁液孕育良好且未出现过冷石墨,但先析出的石墨晶核来不及生长,无法形成片状 A型石墨。同时浇注成型的铸件表面存在大量的微缺口,在应力作用下这些缺口极易导致应力集中,从而萌生裂纹源,大部分微裂纹最早在石墨-基体相界上形成,尤其在片状石墨尖角处形成。在交变载荷的影响下,微裂纹逐步向基体内扩展。由于E型石墨对基体有严重割裂作用,故裂纹在扩展的同时还会沿枝晶方向形成二次微裂纹,使基体承受载荷的有效面积减小,石墨的缺口效应导致支架在承受低于设计安全裕度载荷的情况下也会发生断裂。
支架断裂的另一个原因是化学成分设计不合理,虽然各元素质量分数满足技术要求,但C、Si元素质量分数接近下限值。Si元素是促进石墨化的元素,Si元素含量较低时,石墨本身形核条件较差。吴孝庭等认为铁液在凝固时先析出树枝状奥氏体初晶,余下的铁液发生共晶转变,在过冷度下形成比D型石墨更小的E型石墨。同时初生奥氏体枝晶的形核和生长也会消耗大量可作为石墨结晶核心的SiO2颗粒,导致石墨的生长进一步受限。由于硅碳比较小,石墨核心少,共晶转变时稳定系统与介质系统之间的温差小,碳原子来不及充分聚集析出,导致共晶时只有一部分碳原子在初生的奥氏体周围以石墨形态析出,并沿着奥氏体散热方向长大,形成E型石墨。
3、 改进措施及验证
由以上分析可知,尽管铸件的化学成分满足技术要求,但未考虑铸件壁厚薄导致的冷却速率快、过冷度大的问题。因此,在不改变壁厚的前提下,优化铸件的化学成分,提高硅、碳元素含量的同时提高硅碳比,促使其形成A型石墨,可有效提高铸件的力学性能。提高碳、硅元素含量可增加形核量和强化孕育效果。硅元素能减小碳在液态和固态铁中的溶解度,促进石墨析出,使石墨片增粗,数量增多,有利于A型石墨生长,改善基体组织并获得优质的灰铸铁件。经理论计算后,将技术要求中的碳元素质量分数下限值由3.0%提高至3.1%,硅元素质量分数下限值由1.7%提高至2.1%,其他元素含量不变。采用随流孕育的方式加入质量分数为0.2%的碳化硅进行试验浇注,增加C元素含量,因为在冷却过程中,可以将碳视为一种非平衡石墨,这种非平衡的新生碳具有较高的活性,且不均匀分布在铁液中,可以在局部形成高浓度的“碳峰”,促进形成A型石墨,细化片状石墨,提高石墨化程度。
试验浇注温度为(1400±20)℃,浇注时间为13s,随后检测附铸试棒和本体的性能。检测结果为:附铸试样 抗拉强度为288MPa,本体硬度为209HBW,本体化学成分分析结果如表2所示。由表2可知:Si、C元素含量满足预计的要求,硅碳比由0.568提高到了0.699。
优化后材料的石墨形态和显微组织形貌如图5所示。由图5可知:优化后基体石墨形态为A型,长度为4级,基体显微组织为珠光体,各项性能指标均满足技术要求。
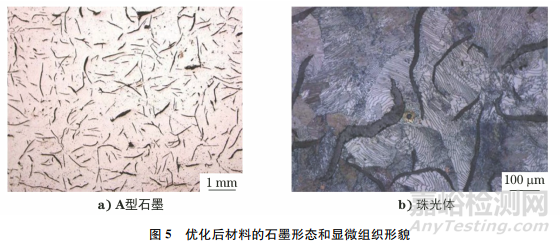
4、 结论
(1)发动机支架断裂的直接原因是基体存在大量E型石墨,加大了对基体的割裂作用,支架承受交变载荷时,其边缘微缺口处产生微裂纹,裂纹逐渐向基体内扩展。
(2)化学成分设计不合理是导致石墨形态不合格的根本原因,虽然各元素含量满足技术要求,但C、Si元素含量接近下限值,硅碳比较小,同时铸件壁厚薄导致冷却速率快、过冷度大,无法形成优良的A型石墨。
(3)通过随流孕育加入质量分数为0.2%的碳化硅,可以提高C、Si元素含量,同时提高硅碳比,试验浇注后附铸试棒抗拉强度满足产品技术要求。
作者:冀鹏,陈世荣
单位:浙江零跑科技股份有限公司
来源:《理化检验-物理分册》2024年第2期
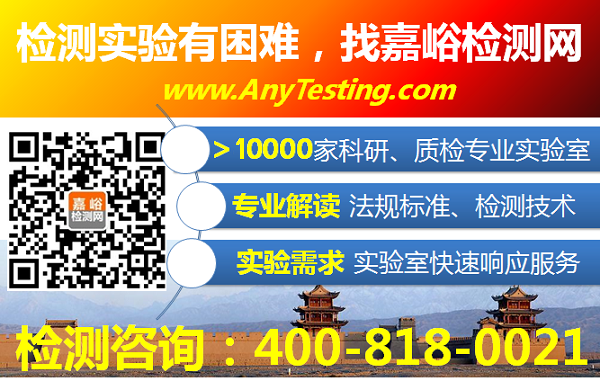