热控材料是实现航天器热控功能的重要介质,是航天器热控技术发展的基础。航天器热控系统中大量使用多层隔热材料、导热材料、热控涂层、界面材料等均是利用材料自身热物理特性实现航天器温度场的控制。本文从航天器热控材料工程应用角度,综述了航天器热控系统常用的隔热材料、高导热材料、涂层材料及界面材料等四类热控材料的研究与空间应用进展,分析了未来空间科学探测、低温推进剂在轨贮存等空间应用场景在深低温及高温环境下对热控技术的发展需求,提出了对深低温和高温环境下高效隔热材料、特种涂层材料等航天器热控材料的发展建议。
关键词:航天器 热控材料 隔热材料 导热材料 界面材料 热控涂层
引言
热控材料是实现航天器热控功能的重要介质,是航天器热控技术发展的基础。航天器热控系统中大量使用的多层隔热材料、导热材料、热控涂层和导热填料等均是利用材料自身热物理等特性实现对航天器温度场的控制。在我国已开展的月球探测、火星探测等深空探测任务中,热控新材料发挥了重要作用,例如,在祝融号火星车热控系统中使用的超低密度纳米气凝胶隔热材料为实现火星车在火面低温、火星尘暴环境下的保温功能发挥重要作用,高透明聚酰亚胺薄膜材料、高吸收低发射率热控涂层材料使火星车首次实现火面太阳能原位热利用。未来,随着我国高灵敏度空间科学探测、近太阳观测探测等复杂任务实施,探测器热控系统研制对深低温隔热材料、深低温高发射涂层材料、极端高温隔热材料、轻量化温度梯度防隔热材料、智能热控材料等特殊新型热控材料提出更多、更高的要求。
热控材料种类繁多,功能各异。本文仅选择航天器热控系统中常用的隔热材料、导热材料、涂层材料及界面材料等四种热控材料,综述其发展与应用现状,在此基础上,分析未来航天器热控技术发展趋势,提出了热控材料的重点发展建议。
1、 航天器用隔热材料发展与应用现状
所谓隔热,就是设法增大某特定方向的热阻,来使这个方向上的热流尽可能地减小。按航天器工作环境条件差异,隔热材料可分为真空环境下隔热材料和气体环境下隔热材料。
真空环境下隔热材料的隔热功能主要通过增大辐射和导热热阻来实现,通常使用多层辐射反射型隔热材料,采用多次反射热辐射的方式实现良好的隔热效果,其研究重点为降低多层隔热材料的面密度和增大多层隔热材料的热阻。
中科院理化所采用低热导率、轻质、高强度中空玻璃微球胶结在双面镀铝聚酯薄膜上,取缔传统多层隔热材料中的涤纶网间隔层,使得每单元的面密度降低 45%,以达到减重的目的,但异质结构的引入带来了多余物脱落的风险。利用薄膜表面结构改性方法,采用压出凸纹的双面镀铝聚酯膜作为反射屏,通过反射屏与间隔层一体化设计,取缔涤纶网间隔层来实现减重,可避免中空玻璃微球异质材料结构改性带来的脱落风险。
在提高多层隔热材料隔热性能方面,主要措施是减小反射屏之间的接触导热漏热。在深低温环境下,辐射漏热份额降低,层间接触导热漏热份额增加,因此减小层间接触导热漏热对多层隔热材料在深低温环境下的应用具有重要意义。针对深低温管路保温应用场景,以离散分布式小型三正交圆盘形聚合物隔离垫片代替传统多层隔热材料中的涤纶网,减小多层材料内部反射屏之间的接触导热漏热,如图1所示。实验结果表明,改进后的5单元多层材料的有效发射率为 0. 005(温度295K) ,而传统 5 单元多层材料的有效发射率为 0.062。针对宇宙和天体物理空间红外望远镜项目(Space infrared telescope for cosmology and astrophysics,SPICA) 深低温环境(<6K) 隔热需求,以一种离散分布式小型层间非接触聚醚醚酮(PEEK) 材质的垫片代替涤纶网,消除多层材料内部反射屏间的接触漏热,如图2所示。实验结果表明,改进后的6单元多层材料的有效发射率为 0. 0046(温度300K) 。
图 1 三正交圆盘隔离器及其在多层材料中的应用
图 2 反射屏非接触隔离器及其在多层材料中的应用示意图
气体环境下的隔热通常使用泡沫、隔热毡和气凝胶材料等,利用材料内部小空间约束气体分子运动,降低气体对流换热,从而实现气体环境下隔热,其研究重点主要集中在降低隔热材料的热导率和密度、提高材料强度和使用温度等方面。
低温气凝胶材料一般是SiO2气凝胶及其复合材料,该材料的制备技术相对成熟,已逐步实现工程应用。针对我国首次火星探测任务需求,研制了密度不大于30kg /m3的低密度泡沫增强SiO2气凝胶隔热材料,研究了材料在不同气氛、不同压力环境下的隔热性能,并开展了热循环、热真空、电离总剂量等空间环境试验验证,该材料在服役温度-145~85 ℃、1000Pa、SiO2气氛下的热导率为 6.6mW/( m·K) ,服役温度范围内热稳定性良好,已被成功应用到我国祝融号火星车热控系统中。美国在索杰纳、机遇号、勇气号等火星车热控中使用了低密度纳米气凝胶,其在1400 Pa、CO2 气氛下0℃时的热导率约为7mW/( m·K) ,密度约为20kg/m3,但在服役过程中,材料的体积收缩率大。
高温气凝胶材料因其低密度、低热导率和耐高温的特点在高温辐射热防护方面具有应用前景。材料高温环境下的热性能稳定性和尺寸稳定性的提高,主要通过使用耐温性更好的材料、改善气凝胶内部纳米颗粒尺寸等措施来实现,由此发展出氧化物气凝胶、碳气凝胶及碳化物气凝胶等; 材料热导率的降低,主要通过提高材料孔隙率和添加红外遮光剂等措施来实现。氧化物气凝胶是当前隔热领域研究最早、也是制备技术相对成熟的一种耐高温气凝胶,主要研究方向有SiO2、Al2O3、ZrO2气凝胶及其复合材料。SiO2气凝胶及其复合材料的制备技术成熟,室温热导率可达到 0. 02W/( m·K) ,但受其内部网络结构限制,耐受温度一般在800 ℃左右,进一步增大其初级颗粒尺寸,可将其耐受温度提升至 1 100 ℃左右;Al2O3、ZrO2 等气凝胶在高温环境易出现晶型转变,限制了其在 1 000 ℃以上环境下的应用,需要对其制备技术开展进一步研究。碳气凝胶具有良好的耐高温性能,在惰性气体及真空环境下耐受温度高达2000 ℃,但在有氧环境下,350 ℃时便会发生氧化。碳泡沫增强碳气凝胶的制备技术是当前碳气凝胶方向研究热点,但其制备技术仍处于实验室探索阶段。在高温气凝胶材料应用方面,针对我国首次火星探测任务需求,航天特种材料及工艺研究所研制了莫来石纤维增强SiO2气凝胶,其短期耐受温度为1200 ℃,面向线膨胀系数小于 4. 06×10-6 /K,900 ℃的热导率为0. 051 W/(m·K) ,已被成功应用于天问一号火星探测器进入舱的7500N变推力发动机热防护系统中。
2、 航天器用导热材料发展与应用现状
导热材料的功能是实现热量的快速传递,主要应用形式是热负载的扩热和点对点的热流传递。在航天热控制应用中,对导热材料的需求主要来源于半导体芯片封装及热负载扩热。
导热聚合物基复合材料和金属基复合材料是两类具有发展前景的电子封装材料。导热聚合物基复合材料具有密度小、电气绝缘性能好等优点,但由于聚合物材料内部传热主要靠声子,其热导率仅为0. 3W/(m·K) ,因此提高该材料的热导率是研究重点,一般有两种方法: 一是改变聚合物材料的分子/分子链接结构,合成具有高度结晶体或高度取向的本体聚合物材料,但采用这种方法制备高导热材料的工艺复杂,成本高; 二是向聚合物基体中添加高导热填料,通过提高填料和聚合物之间界面结合质量,使其形成连续的导热网络,从而提高材料的导热特性常用的高导热填料有碳材料( 碳纳米管、石墨烯等) 、陶瓷材料(氮化铝、六方氮化硼等) 及金属材料(银、铜等) 。
金属基复合材料具有高热导、低膨胀、易加工及良好的韧性等优点。金属基复合材料的导热性能主要与增强体、金属基体、增强体/基体的复合界面质量及复合构型等因素有关,其研究的重点是构建合理高效的复合结构及提高金属基体与增强体之间的界面结合质量。碳纳米纤维、碳纳米管及石墨烯等碳材料具有优异的力学性能、极低的热膨胀系数及很高的导热性能,研究纳米碳增强体在金属基体中的均匀分散及其与金属基体界面结合的控制技术有望成为金属基复合材料的一个重要方向。例如,采用碳纳米管作为增强体,控制碳纳米管质量分数不超过1.0%时,碳纳米管在基体中可较均匀地分散,镁基复合材料的导热率可达187. 7W /(m·K) 。
高导热C/C复合材料是以碳为基体、碳纤维为增强体的复合材料,具有优异的导热、力学性能和结构设计性,可作为大范围扩热用轻质高导热材料。国外比较成熟的高导热C/C复合材料的室温热导率为一维( 维度是指碳纤维铺设状态,下同) 600~800W/(m·K) 、二维300~500W/(m·K) 、三维200~400W/(m·K) 。樊桢等采用中间相沥青作为基体碳前驱体、中间相沥青碳纤维作为增强体制备了一维、二维和三维高导热C/C复合材料,其材料热导率分别达到 700W/(m·K) 、400 W/(m·K) 和 350 W/(m·K) 。姚彧敏等进一步研究了不同处理温度对沥青基C/C复合材料微观结构的影响,通过提升热处理温度,可获得更高导热特性的C/C复合材料。
3、 航天器用热控涂层材料发展与应用现状
热控涂层是通过改变物体表面的太阳吸收率和红外发射率参数实现对表面温度的控制,是航天器热控系统中使用最普遍的热控材料之一。
随着航天技术的发展,我国已经建立起体系相对完整、种类齐全、可满足多种需求的热控涂层型谱。在我国开展月球及火星探测工程中,为满足新任务热控制的需求,也相继开发了新的热控涂层,例如: 火星探测器任务中开发的低吸收 /低发射涂层,太阳吸收比为0.19± 0.02,半球发射率为0.2~0.4,实物照片如图3a所示; Al-AlN复合膜系结构吸热涂层,其太阳吸收比为0.92,半球发射率为0.08,实物照片如图3b所示。近年来新开发的热控涂层详见表1。
图 3 ( a) 低吸收比低发射率涂层
表 1 近年来新开发热控涂层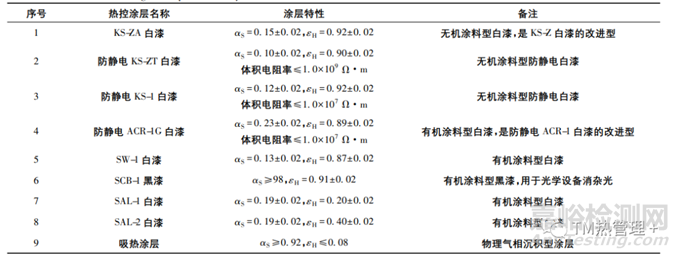
( b) 吸热涂层(蓝色区域) (电子版为彩图)
为满足深空探测需求,适应空间极端低温/高温环境下的热控涂层成为当前研究热点。在低温涂层方面,美国鲍尔宇航技术公司为詹姆斯韦伯望远镜( JWST) 项目研制的一种低温热控涂层( 鲍尔红外黑漆,英文简写 BIRBTM ) ,其表面具有交织的矩阵结构,在35K低温环境下红外发射率大于0. 9,且具有良好的耐污染性能,已被成功应用在 JWST 项目中。在高温涂层方面,美国为近太阳观测探测器热防护罩研制了耐高温 Al2O3 陶瓷涂层,该涂层耐温范围为0~1400 ℃,吸收/发射比值为 0. 2~ 0. 3,能够适应太阳附近大剂量电子、质子及紫外辐射环境。
智能涂层是近年来为满足航天器低能耗、自主化需求而发展的一类能够根据环境温度的变化改变涂层发射率的智能材料,该材料预计将给航天器热控技术发展带来新突破。据仿真结果,采用变发射率智能涂层( 红外发射率变化范围为 0. 2~0. 8,太阳吸收比为 0. 2) 能够节省热控系统电加热功率约 90%,减轻热控质量约75%,特别适合对功率和质量要求苛刻的深空探测器或小卫星的热控制。智能涂层一般包括热致变色涂层和电致变色涂层。目前国内外关于热致变色涂层的研究主要围绕锰酸镧和二氧化钒两种材料。对于锰酸镧材料涂层,太阳吸收比高和转变温度范围宽阻碍了该材料在工程中的应用。
对于二氧化钒材料涂层,加拿大 MPB公司采用 VO2 /SiO2 /VO2 多层膜结构制备了热致变色涂层,其发射率变化范围为0. 38~0. 74,太阳吸收比为0. 32,转变温度范围为30~90 ℃,并开展了热循环、热冲击及原子氧侵蚀试验,结果表明涂层经过热循环和热冲击试验后性能稳定,但原子氧侵蚀会使涂层 发 射率增加、转变温度范围变宽。研究了纯VO2及掺杂VO2多层膜结构热致变色涂层,制备了纯VO2多层膜结构涂层(见图 4) ,其发射率变化范围为0. 38~0. 76,太阳吸收比为0. 44,转变温度范围为50 ~ 70 ℃(见图 5) ,他们也开展了热循环(- 50 ~ 100 ℃) 、高温存储(600h@ 90 ℃) 及真空紫外辐照试验(1112 ESH) ,结果表明真空紫外辐照试验对涂层发射率无影响,但使转变温度升高 10 ℃。国内哈尔滨工业大学和上海硅酸盐研究所在基于VO2 的多层膜结构涂层研究方面取得进展,制备的涂层发射率变化量为0. 35,太阳吸收比为 0. 6,转变温度为0~ 40 ℃。基于VO2的多层膜结构涂层是最有可能实现工程应用的智能涂层,如果能解决涂层太阳吸收比高的问题,将会大大推动热致变色智能热控涂层的工程应用。
图 4 基于二氧化钒材料的多层膜结构热致变色图结构( 左) 及产品照 片( 右)
图 5 基于未掺杂二氧化钒的热致变色涂层发射率随温度变化曲线 ( 电子版为彩图)
电致变色涂层是指在外部电压的作用下,材料的光学性能发生可逆且持久稳定变化的一类材料。按照材料化学属性可分为无机电致变色涂层和有机电致变色涂层。无机电致变色涂层主要以 WO3 等过渡金属氧化物为主。美国Eclipse Energy Systems 公司基于 WO3 制备的多层膜层结构电致变色涂层的发射率变化范围为0. 06~0. 77,并于2007年在 MidStar 卫星上进行了飞行试验。制备了结构为ITO/WO3 /Ta2O5 /NiO/Ag /Glass 的全固态电致变色涂层,其发射率变化值为 0. 49,吸收率为 0. 38; 制备了结构为 Glass/ITO/WO3 /LiNbO3 /NiOx /ITO 的多孔结构电致变色涂层,该涂层呈现出更优的变色性能。有机电致变色涂层主要以导电聚合物材料为主。2001 年美国采用导电聚合物制备了电致变色涂层,其发射率变化范围为0. 32~0. 79,涂层在经历 γ 源照射、质子及电子辐照后,热光学性能未发生明显变化,但随着温度降低,电致变色时间加长,在- 90 ℃ 时转变时间增加到 15 min,在温度高于90 ℃ 时,涂层封装材料出现分层现象。2003 年采用导电聚合物材料制备电致变色涂层,其涂层发射率变化范围为 0. 21 ~ 0. 69,并通过了-70 ~ 75 ℃ 真空热循环试验以及质子、电子和紫外辐射试验,试验前后性能未见明显变化。2021年制备了电致变色涂层,其发射率变化范围为 0. 22 ~ 0. 75,太阳吸收比为0. 44,但经过热循环( -50 ~ 100 ℃ ) 试验后出现电解液泄漏现象; 2022 年制备了电致变色涂层,其发射率变化范围为 0. 61 ~ 0. 81,太阳吸收比为 0. 45,并经过- 20 ~50 ℃ 的热循环试验,未见电解液泄漏,但如何避免聚合物中电解液泄漏仍是该涂层制备的难点。采用两种无机材料复合或无机与有机材料复合制备电致变色涂层,利用每种材料的优点,可提高涂层的变色效率,扩大发射率调制范围,改善涂层的热稳定性。电致变色涂层较弱的耐空间环境能力限制了其在航天器上的应用。
4、 航天器用热控界面材料发展与应用现状
在航天领域,界面材料主要用于填充设备安装面与安装板、电子器件与安装面之间的间隙,使两界面之间的接触形式由点接触变成面接触,以提升界面接触换热率。基于安全性考虑,航天用界面材料不仅需要导热率高,还需要电绝缘性好、化学稳定性好、出气率低、无毒、无味、无腐蚀性等。常用的热控界面材料有硅脂类和硅橡胶类。
导热硅脂/导热硅橡胶是以硅油/硅橡胶为基体、导热粉体为填料,并添加功能助剂,经混合研磨而成的膏状混合物。提高界面材料导热性能通常有两种方法: 一是选用高导热填料; 二是采用不同粒径填料颗粒级配,利用不同粒径颗粒的协同效应,在导热硅脂/导热硅橡胶内部构筑贯通的导热通路。添加适量单一粒径高导热填料可以有效增强界面材料的导热性能。通过对填料粒径级配优化填料比例可以进一步提高界面材料的导热性能。近年来,随着高导热碳材料制备技术的发展,研究人员将石墨烯、碳纳米管等高导热碳材料作为界面材料的填料以增强界面材料的热导率。但需要使用纳米杂化处理等手段屏蔽碳材料的导电性以满足导热和电绝缘特性要求。另一方面,对导热填料进行表面处理提高填料与基体之间的相容性,不仅可以减小填料与基体之间的界面热阻,而且可以提升材料界面化学稳定性,例如: 使用适量的硅烷偶联剂处理氮化铝、氮化硅等陶瓷填料粉体,在填料粉体表面形成单层包覆,可有效提高材料的导热性能。
导热硅脂在工程应用中存在的主要问题是在高低温交变循环情况下,硅脂会从界面缝隙中逐渐溢出,甚至出现硅油析出和迁移,对敏感设备造成污染风险。相比导热硅脂,导热硅橡胶垫片的界面热阻要大一个数量级,且需要相对较大的界面压力才能获取较小的接触热阻,但材料长期空间热稳定好,污染风险小。图 6a、图6b分别给出了采用Flextein Grease5030 型导热硅脂( 标称导热系数为 3 W/( m·K) )和Flextein S50 型导热橡胶垫片测试接触热阻与压力的关系,从中可以看出,在界面压力大于 30 Psi 时,导热硅橡胶垫片才能获取比较稳定的接触热阻,但比使用导热硅脂测得的接触热阻整体要大一个数量级。
图 6 ( a) 导热硅脂的测试接触热阻与压力的关系;
( b) 不同厚度导 热垫片的接触热阻与压力的关系
5、 航天器热控材料发展建议
航天任务对热控技术发展需求是牵引热控材料发展的源动力。根据国内外航天器发展趋势分析,未来热控材料发展需求主要体现在三个方面: (1)20~100K低温环境下的高效隔热材料、高导热材料、高发射率热控涂层等热控材料。(2) 750~2000 K 高温环境下的隔热材料、耐高温涂层材料( 一般要求涂层的吸收/发射比小于 1. 0) 等热控材料。(3) 针对集成度越来越高的航天器的导热强化、高效热排散等共性要求而提出的对高导热材料、高导热界面材料、智能热控涂层材料以及热存储材料等的发展需求。
在隔热材料方面,建议优先发展深低温环境( ≤100K)下高效隔热材料和高温环境( 1200 ~ 2000 K) 下高效隔热材料。深低温环境下高效隔热材料仍以辐射反射式隔热材料为主,重点研究如何在减小反射屏间接触导热漏热的同时不对可操作性产生较大影响。极端高温环境下高效隔热材料重点研究耐高温气凝胶材料、泡沫碳材料等,研究材料在高温环境的热稳定性及化学稳定性。
在导热材料方面,针对电子封装用导热材料,建议重点研究复合构型设计及基体/增强体复合界面质量( 接触面积、浸润状态、粘结强度等) ,以较少的增强体添加量获得更好的增强效果; 针对 C/C 高导热材料,建议开展工程化应用研究,同时开展极端高温环境(>1 550 ℃) 下 C/C 材料热学、力学性能研究,推动 C/C 高导热材料在航天器上的应用。C/C 材料的耐高温性能使其在极端高温环境下隔热方面也有良好的应用前景。
在热控涂层材料方面,建议开展深低温环境下的超黑热控涂层及极端高温环境下的耐高温涂层技术研究,重点研究涂层的耐空间环境( 质子/电子辐射、真空紫外辐射等)适应性及温度环境适应性,以及涂层的热光学/化学稳定性;建议开展基于 VO2 材料的智能涂层优化技术研究,提高涂层发射率调节范围,降低涂层太阳吸收比( < 0. 2) 和转变温度(10~30 ℃) ,开展智能涂层耐空间环境( 热真空、热循环、质子与电子辐射、紫外辐射等) 适应性验证。
在界面材料方面,建议开展可重复拆装的高弹性体导热垫片技术研究,使其能够在低压力负载下获取较小的接触热阻以适应航天器自动化生产线装配要求; 研究导热硅脂基体与填料界面相容性增强技术,减少或消除硅油分离现象。
来源/作者:材料导报、新材料科技资讯
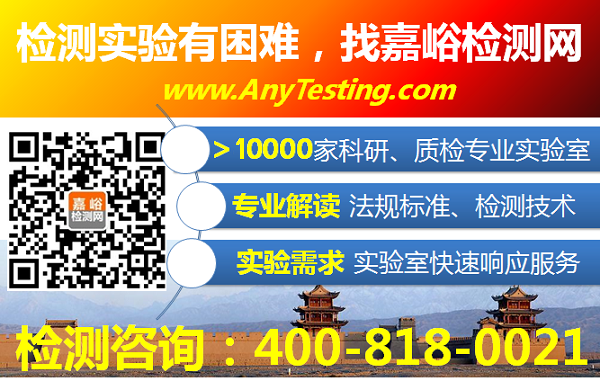