钎焊作为一种高效、廉价且焊接接头光滑美观、可靠性高的连接技术,适用于焊接精密、复杂和不同材料组成的构件,在工业上得到了广泛应用。钎焊的无损检测技术可以有效地提高焊接接头的质量,节约成本。
作为一种新型的无损检测技术,超声显微镜(SAM)技术可以有效地检测出分层、空洞等内部缺陷,其通过扫查检测可获得工件内部的C扫描图像,直观地识别出缺陷以及缺陷的位置。但是由于缺陷的形状不规则,对于缺陷面积的计算具有一定困难。传统的人工判别计算存在误差大、效率低等问题。
为此,大连交通大学和大连外国语大学的研究人员针对检测得到的C扫描图像,采用基于阈值的图像分割方法,将缺陷目标与背景分割,对缺陷进行标记,计算缺陷的面积,通过设定缺陷面积阈值,判断面积较大的严重缺陷;其后设定工件的检测标准,判断工件是否合格。验证试验结果表明该方法计算时间短,结果更加准确,重复性更高,检测效率更高。
超声C扫描成像原理为:将采样点的超声缺陷回波特征值(即缺陷波的波高)转化为相应的颜色,用不同的颜色填充扫描点周围区域,从而描述该采样点的信号特征。将超声C扫描图像中最小四边形组成单元定义为一个像素点,该像素点包含了二维坐标信息和超声缺陷信号信息,一个像素点相当于超声探头在某个检测点所采集到的信息的可视化。
超声C扫描图像生成示意如图1所示,矩阵中的各元素是超声检测系统扫查过程中得到的采样点,超声C扫描图像上的像素点与矩阵中的各个元素一一对应,图中m和n分别表示C扫描图像像素点的行数和列数,i和j分别表示超声检测过程中扫描点的行号和列号,点(i,j)上的像素值用函数f(i,j)表示,f表示灰度值。
图1 超声C扫描图像生成示意
检测得到的C扫描图像是一种伪彩色图像。某钎焊工件(称为工件一)C扫描图像如图2所示。在超声C扫描图像中,将超声波信号的波高定义为幅值,超声信号幅值较高的区域为橙红色,幅值较低的为蓝白色,中间过渡的为黄绿色。从工件的C扫描图像中很容易看出缺陷与非缺陷区域。图2中,主要背景色为蓝白色,是钎焊质量较好的位置,黄色与橙色部分则是缺陷区域。
图2 钎焊工件一C扫描图像
2、缺陷识别与面积计算流程
基于超声C扫描图像的缺陷识别与面积计算方法的流程如图3所示,首先,采用基于阈值的图像分割方法对C扫描图像进行二值化处理,区分缺陷与非缺陷区域;然后采用所提出的缺陷识别算法进行缺陷标记,得到多个互不相连的缺陷;最后通过设定缺陷面积阈值的大小,分别计算出一个工件中所有缺陷的面积占比和大于缺陷面积阈值的缺陷的面积占比,根据工件缺陷面积检测标准,判断该工件是否合格,给出工件检测报告。
图3 缺陷识别与面积计算流程
3、C扫描图像的二值化处理
为了对缺陷进行定量分析,需要先将缺陷与非缺陷区分开,然后在此基础上进行计算。为此,设定缺陷阈值T0,对于图像中像素值为t的图元,其二值化后的像素值T为:
缺陷阈值T0的大小是确定缺陷的依据,其与被检测工件的材料、探头的选取、探伤仪器的参数设定以及工件验收要求等因素紧密相关。
在实际应用中,一般按照检测规程在统一的检测参数条件下,通过用对比试块进行试验的方式来确定合适的缺陷阈值。
某钎焊工件(工件二)的超声C扫描图像如图4所示,其由122×104个像素点组成,经过二值化处理后的图像如图5所示。
图4 钎焊工件二的C扫描图像
图5 二值化处理后的C扫描图像(对应图4工件)
4、缺陷标记
对C扫描图像进行二值化处理后,只是将缺陷点与非缺陷点区分开,实际还需要将一个缺陷与其他的缺陷区分开,并且设置缺陷面积阈值S0,将缺陷面积大于S0的缺陷提取出来。提出的缺陷识别算法过程如下:
(1)对二值化后的图像按照由左至右,由上至下的顺序进行扫描,将同一行中的相邻缺陷点定义为一个分组,记为G(x,n),x表示该分组所在的行数,n表示该分组的序号。缺陷标记示意如图6所示,G(0,1)表示第一个分组,在第0行。该分组包含3个缺陷点,第二个分组只包含一个缺陷点。
图6 缺陷标记示意
(2)获得所有分组后,按照由下至上,由左至右的顺序进行扫描,判断分组G(x,m)与其上一行的分组G(x-1,n)是否相邻。如果G(x,m)中最右侧像素点的横坐标加1不小于G(x-1,n)中最左侧像素点的横坐标,并且,G(x,m)中最左侧像素点的横坐标减1不大于G(x-1,n)中最右侧像素点的横坐标,则认为此两个分组是相邻的,将两个分组序号记录下来,记为K(a,b)。如图6所示,第5个分组与第6个分组相邻,将其序号记录下来,记为K(5,6)。
(3)对所有分组按照序号进行遍历,如果当前分组序号与K(a,b)中的任意一个值相同,假如与a0相同,则用b0对其余的K(a,b)进行遍历,如此进行循环,则可以将所有相邻的分组提取出来,聚类为一个缺陷,记为Dq(q表示该缺陷的序号)。如图6所示,D5为工件中的第5个缺陷。
(4)遍历一个缺陷中的所有缺陷点,确定该缺陷所在的矩形区域。根据设定的缺陷面积阈值S0创建一个M×M图元的缺陷模板,如图7所示。模板中每个像素点的像素值都设为1,将工件中缺陷点的像素值设为1,非缺陷点的像素值设为0。使用模板按照由左至右、由上至下的顺序对缺陷覆盖的矩形区域进行扫描,对模板与工件对应位置的像素值进行异或运算,判断该缺陷是否能覆盖模板,将大于缺陷面积阈值的缺陷与其他缺陷区分开。
图7 缺陷分布与模板示意
(5)计算缺陷面积,一个工件中所有缺陷的面积占比就是缺陷点的个数与所有像素点的个数的比值,大于缺陷面积阈值S0的缺陷面积占比就是这些缺陷中包含的缺陷点与所有像素点的个数比。
5、试验与结果
为验证提出的缺陷识别算法的可行性,共进行了10组钎焊工件超声检测与缺陷识别试验。根据对对比试块进行试验,确定缺陷灰度阈值为100。试验时,扫查精度为0.1 mm,并且设定缺陷面积阈值T0为0.5 mm,即缺陷模板为边长为5(0.5/0.1)个像素点的正方形。工件缺陷判别标准计算公式如下:
式中:A0为理论焊接面积;A1为尺寸大于T0的缺陷面积之和;A2为所有缺陷面积之和;F1为小于缺陷面积阈值的其他区域面积占比;F2为非缺陷区域的面积占比。
F1≥90%且F2≥65%的工件,检测结果为合格。
第一组(工件1)和第五组(工件5)试验的C扫描图像与缺陷识别处理后的图像如图8所示,图中黑色部分为焊接质量较好的位置,彩色部分为缺陷。对缺陷进行着色,将各个缺陷区分开,白色矩形为缺陷模板,说明该缺陷面积大于缺陷面积阈值。经过缺陷识别处理后的图像与工件C扫描图像具有很高的一致性,对于大于缺陷面积阈值的缺陷筛选较准确,大大提高了工件检测结果的准确率。
图8 两组试验(工件1与工件5)的C扫描图像与识别处理后图像
10组钎焊工件的缺陷识别试验结果如表1所示。
表1 钎焊工件缺陷识别试验结果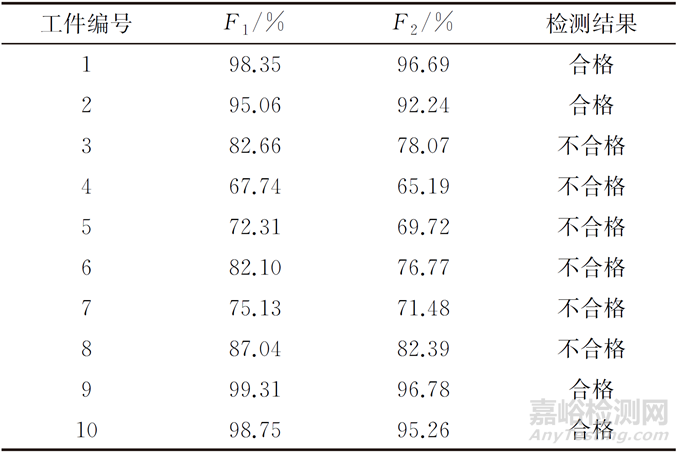
以工件1和工件5为例,工件1的F1≥90%且F2≥65%,所以检测结果为合格,工件5的F1<90%,所以检测结果为不合格。由图8也可以看出,工件1中的缺陷面积明显小于工件5中的缺陷面积,工件1中的大于缺陷面积阈值的缺陷与工件5中的大于缺陷面积阈值的缺陷相比也较少。
结论
(1) 提出的缺陷识别方法能够有效地识别超声C扫描图像中的形状不规则缺陷,并将其与其他缺陷进行区分,通过设置缺陷面积阈值,准确地提取目标缺陷。
(2) 在工件完成超声检测后,所提方法能自动对检测结果进行缺陷识别,通过设置的缺陷阈值与缺陷面积阈值,在毫秒级的时间内显示工件经过缺陷识别处理后的图像并给出工件的缺陷识别检测结果,大大提高了缺陷识别计算的效率与准确率。
作者:赵新玉1,姜德顺1,李正光2,张佳莹1
工作单位:1.大连交通大学 材料科学与工程学院
2.大连外国语大学 软件学院
第一作者简介:赵新玉,博士,副教授,主要研究方向为焊接和检测技术与装备。
通信作者简介:张佳莹,博士,副教授,主要研究方向为材料的无损检测与评价。
来源:《无损检测》2023年11期
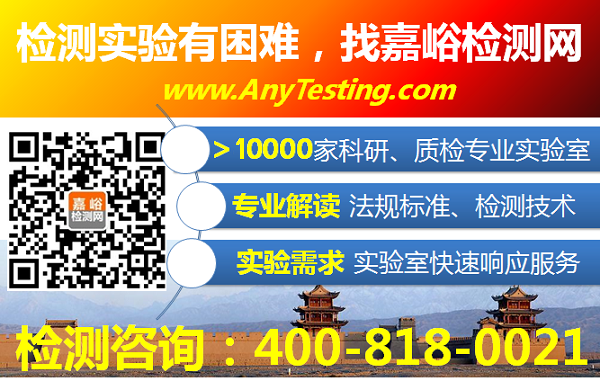