原料药中间体的精致提纯是原料药生产中至关重要的一环——本文结合对原料药中间体精制提纯工艺及装置的见解和实际应用中的创新改进,着重对原料药中间体如何去除有机杂质的改进型萃取装置、改进型脱色过滤及重结晶装置进行了论述。
原料药中间体的纯度是确保原料药API 质量的关键,因此,在原料药生产中,大部分中间体都需要进行精制提纯,以去除机械杂质和有机杂质。常用的精制提纯方法包括:重结晶、利用酸碱提纯、利用物化性质提纯、吸附层析提纯、手性拆分、萃取等。对于易引入或产生杂质的工艺甚至每一步都需要精制提纯。接下来,本文将以常用萃取、重结晶等装置方面的创新为例来论述原料药中间体精制提纯装置的技术改进。
1、工业萃取装置的改进
大部分有机杂质是在合成反应中产生的,或因工艺欠缺,或因物料及反应条件差异引起。为改善这一情况,在优化工艺的同时通常采用萃取的方法来去除这些有机杂质。理想的萃取效果必然有优良的萃取装置来支撑,萃取装置也是决定除杂效果的重要因素。常用的萃取装置包括萃取分液罐、离心萃取机等。对萃取装置不断进行改进创新,以达到更好的除杂效果,也是化学制药人一直努力追寻的方向之一。图1展示了笔者团队结合一线经验设计的一种在原料药生产过程中去除有机杂质的改进型萃取装置。
1.1 改进说明
本次设计的改进型萃取装置的组合方式可描述如下:溶解调节釜01 上方连接设置高位槽011,溶解调节釜01 底部通过底阀012和管道与分液萃取罐02 顶部相连,分液萃取罐02 底部连接有视镜023,视镜023 正下方设置有水相控制阀025,视镜023 侧下方设有有机相控制阀027 和过渡层控制阀028,有机相控制阀027 和水相控制阀025 之间用斜管026 相连,分液萃取罐02 顶部连接有真空管029,真空控制阀022 设置于分液萃取罐02 下面一侧位置,分液萃取罐02 顶部还连接着放空管030,放空控制阀024 设置于分液萃取罐面02 一侧位置。如此设计,在溶解调节釜中,作为萃取剂的溶剂和物料便能充分混合均匀并适度调节pH 值和浓度;在分液萃取罐中,便能以真空为动力反复混合萃取,或以超声波为动能反复混合萃取,确保水相和有机相界面清晰分层,尽可能地分开水相和有机相。
本设计中,有机相控制阀和水相控制阀之间连通的斜管与水平线呈30°~ 75°角,斜管长30 ~ 50 cm ;这样设计的目的是确保管道中的水相残余不能流入到有机相中。上文所述的放空控制阀、真空控制阀、有机相控制阀、水相控制阀处于相同或相近的水平高度位置;这样设计的目的是保证安全操作和减轻劳动强度。上文所述的放空管自分液萃取罐顶部插入到分液萃取罐底部;这样设计的目的是为了再混合时采用真空作为动力,使空气自分液萃取罐底部进入,以鼓泡形式带动物料充分混合。
1.2 实际操作
本设计装置详细的操作过程如下:首先把要萃取提纯的物料和相应的溶剂投入溶解调节釜01,启动搅拌使其混合均匀,并借助高位槽011 中和酸或碱调节pH值;一定时间后,打开真空控制阀022,借助真空将混合物料经底阀012 和混合液021 进口转入分液萃取罐02 中;当发现分层效果不理想时,打开放空控制阀024,借助真空让空气经放空管030 从分液萃取罐02 底部进入,并以鼓泡形式使物料再混合;当发现溶剂量不足时,以同样方式,打开放空控制阀024,借助真空让溶剂经放空管030 从分液萃取罐02 底部进入,以进一步萃取;当界面分层清晰时,打开水相控制阀025,把水相放出转移到另一工序;当从视镜023 处发现有机相时,关闭水相控制阀025,打开过渡层控制阀028,放出油水相过渡层,流转到下工序作进一步处理;然后,关闭过渡层控制阀028,打开有机相控制阀027,把有机相转移到另一工序作进一步处理;如此反复操作2 ~ 3 次就能把有机杂质清除干净。
1.3 改进效果
本设计带来的明显的有益效果包括3 方面:(1)有机相控制阀和水相控制阀之间连通的斜管能够确保水相无法进入到有机相中,保证了萃取效果;(2)各控制阀保持在相同或相近的高度,有利于安全操作和减轻员工劳动强度;(3)放空管插入分液萃取罐底部能保证空气以鼓泡形式促进物料混合,进而提高萃取效果。
2、脱色、过滤、重结晶装置改进
应实际应用的需要,笔者团队设计了一种改进型原料药中间体精制提纯装置,集脱色吸附、过滤、结晶功能于一体,它的主要创新点是引入了并联连接的炭过滤器组合、高精度的微孔膜过滤器和具有不同搅拌方式的连体型分步结晶装置。该装置的平面结构如图2 所示。
2.1 改进说明
本次设计的改进型原料药中间体精制提纯装置的组合方式可描述如下:吸附脱色釜01 上部设置有氮气进口11 和回流冷凝器12,吸附脱色釜01 底部出口通过管道、流体分布器21 与炭过滤器组合02 相连,炭过滤器组合02出口依次与微孔膜过滤器A03 和微孔膜过滤器B31 相连,微孔膜过滤器B31 出口通过管道、料液进口41 与降温析晶釜04 上部连通,降温析晶釜04 底部出口通过上闸阀46 与深冷结晶釜05 上部相连,深冷结晶釜05 的正下方设置有离心机06。这样的设计能使原料药中间体经过四级提纯精制,确保原料药达到《中华人民共和国药典》规定的标准。
本设计方案中,设置吸附脱色釜是为了先用相应的有机溶剂或水把一定量的原料药中间体溶清,然后再用活性炭进行脱色吸附;炭过滤器组合是由1 ~ 4 台炭过滤器以并联的方式连接在一起组成,每台炭过滤器进口连接着流体分布器;这样设计的目的是使流体分布器能够相对均匀地将物料分配到每个炭过滤器,而炭过滤器之间以并联方式连接能够加快过滤速度,进而提高生产效率和避免因降温造成的管道析晶问题;微孔膜过滤器由2 ~ 4 台以串联方式连接在一起,微孔膜过滤器内部设置有8 ~ 12 根微孔膜柱子,有效膜面积为100 ~ 350 m2 ;微孔膜过滤器流量为4 ~ 8 t/h,精度为0.02 ~ 0.10 μm ;这样设计的原因是采用高精度、大表面积的微孔膜过滤器有助于快速过滤和去除更微小杂质。降温析晶釜和深冷结晶釜为连体型分步结晶装置,降温析晶釜的卸料口与深冷结晶釜通过闸阀直接连通成一个整体, 它们的下半部分呈圆锥体结构, 物料出口直径为200 ~ 300 mm ;采用该设计的连体型分步结晶装置能够有效避免物料与外界的接触以及连续交替操作;另外,圆锥体结构和较大的卸料口直径有利于物料顺利放出,对减轻劳动强度和提高生产效率也比较有利。安装于降温析晶釜内的搅拌器为星形搅拌桨,星形搅拌桨上下与水平方向平行,有1 ~ 3 层,每层搅拌桨均匀分布着3 ~ 5 片桨叶,搅拌速度设置为20 ~ 40 r/min ;设计采用这样的搅拌器形状能够保持料液在搅拌降温过程中不起旋涡、晶体不挂壁。安装于深冷结晶釜的搅拌器为横向耙式搅拌桨,耙式搅拌桨设置有2 ~ 6 片平行的桨叶,转动速度为10 ~ 20 r/min ;设计采用横向耙式搅拌桨更有利于把晶体推出深冷结晶釜,对减轻劳动强度和提高生产效率也比较有利。
2.2 实际操作
本设计装置简单的操作过程如下:首先把待精制的原料药中间体和相应的溶剂或水投入到吸附脱色釜01,在一定温度条件下加入活性炭脱色除杂,然后,打开和关闭相应的控制阀,从氮气进口11 处逐步压入高纯氮气,让料液通过管道、流体分布器21 经并联连接的炭过滤器组合02 进行第一次过滤除杂;料液继续沿着管道再依次经串联连接的微孔膜过滤器A03 和微孔膜过滤器B31 进行第二次和第三次除杂;接下来,料液进入到降温析晶釜04 中,打开冷却水进口43 和冷却水出口44,启动星形搅拌桨45,让料液缓缓降温析晶;当观察到少量晶体析出时,打开上闸阀46,让料液流入到深冷结晶釜05 中,开启冰盐水进口51 和冰盐水出口52,启动耙式搅拌桨53,让小晶体逐步长成大晶体,此谓第四次除杂;然后,打开下闸阀54,让料液放入离心机06 进行固液分离,收集固体,离心母液经离心母液出口转移到下工序作无害化处理。
2.3 改进效果
本设计带来的明显的有益效果表现为以下4 个方面:(1)能够有效去除原料药中的机械杂质和副产物杂质;(2) 能够有效降低杂质进入原料药的机会;(3)能够有效改善原料药晶体颗粒大小及晶型,对提高原料药纯度非常有利;(4)具有操作便捷、劳动强度低、生产效率高、结构紧凑的优点。
3、结晶釜的技术改进
原料药中间体的晶型及晶体颗粒大小也是结晶工艺控制的关键。由于生产装置具有局限性,在结晶过程中往往会产生降温滞后迟缓、晶体挂壁、晶体结粘块、晶体沉积底部堵塞卸料口造成延迟卸料等不利于质量控制的现象。
以中间体对羟基苯甘氨酸的结晶过程为例,降温迟缓会造成结晶时间长,降温太快又会出现包晶现象;结晶过程中的强力搅拌会使结晶体和有机副产物形成粘块;晶体颗粒的逐步沉积会造成卸料口的堵塞,延迟卸料亦会造成晶体质量下降,同时也会给操作带来不便和安全风险。
鉴于此情况,笔者团队设计了一种改进型原料药中间体结晶釜,它的创新点是引入了自制的改进型桨叶作为搅拌器和自釜底引入气流通入结晶釜。本设计解决了结晶釜内降温的问题,解决了结晶过程中高浓度固液混合物翻转不均匀的问题,解决了晶体沉积釜底进而堵塞卸料口的问题。该装置的平面结构如图3 所示。
3.1 改进说明
本次设计的改进型原料药中间体结晶釜的组合方式可描述如下:结晶釜01 正上方设置有高位计量槽03,结晶釜搅拌器采用自制的改进型桨叶02,结晶釜底部连接有气流管道06,气流管道上设置有上气流控制阀07 和下气流控制阀08。这样设计是为了使改进型桨叶02 在缓慢搅拌下也能保持物料翻转均匀,进而确保晶体颗粒散热均衡不粘连;结晶釜底部连接气流管道06,可以使结晶过程中不间断通入净化的空气或氮气,这样设计一方面利于结晶釜内降温,另一方面气流会阻止晶体沉积,进而可以避免卸料的堵塞。
本设计中,所述的改进型桨叶为自制扭梭形结构,以搅拌轴为中心呈一边高一边低的手性不对称状态;如此设计接触面积相对较大,但搅拌时阻力相对较小,扭梭形结构的改进型桨叶会使物料自下而上翻涌,进而使物料混合均匀无盲区。
3.2 实际操作
本次设计的改进型结晶釜的操作过程如下:首先启动搅拌,让物料在改进型桨叶02 带动下缓慢地自下而上均匀翻涌;当有晶体析出时,打开上气流控制阀07 和下气流控制阀08,使气流自结晶釜底部源源不断地通入到结晶釜内部,这样既能实施内降温同时又能有效阻止晶体颗粒沉积;尾气经尾气出口09 进入下工序集中进行无害化处理;晶体析出完成后,打开出料控制阀05,让物料转入下步工序进行固液分离等进一步操作。
3.3 改进效果
本设计带来的明显的有益效果包括4 个方面:(1)物料混合均匀,晶体颗粒群蓬松而不结粘块、不挂壁;(2)实施气流内降温能缩短结晶时长,避免副产物过多产生,有利于提高生产效率和中间体纯度;(3)连续不断的气流能有效阻止晶体颗粒沉积,进而避免因卸料口的堵塞造成卸料时间延长带来的质量下降风险;(4)对安全生产和生产效率提高非常有利。
4、结语
本文进行的论述只是对常规的原料药中间体精制提纯装置的技术改进,相信随着“超临界流体萃取工艺”、“高速逆流色谱法”、“制备色谱法”等提纯新技术的深入应用,以及原料药质量标准的提升,国内原料药质量一定会取得更大、更快的跨越!
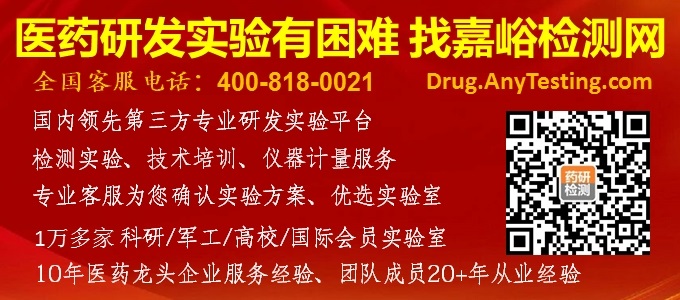