大型锻件的生产过程包括冶炼、注锭、凝固、锻造和热处理等工艺。由于冶金和凝固特性决定了钢锭中不可避免地存在孔隙、夹杂、偏析和组织等缺陷,并且钢锭越大缺陷越严重。通过炼钢采用超纯净钢水注锭,凝固过程中由于缺少结晶核致使晶粒过分粗大;采用电渣重熔锭,晶粒定向生长并且较粗大。两种方法均增加了后续锻造和热处理工艺的难度。而国内炼钢普遍以电炉为主,钢包精炼,合理控制注锭和凝固过程,钢锭中内生夹杂物数量虽然很多,但其单个尺寸远小于探伤标准中的容许值。锻造是唯一具有成形作用的工艺,通过锻造工艺控制缺陷形成是保证锻件探伤不超标的唯一途径。
1、夹杂物产生裂纹的原因
材料性质、夹杂特性、变形温度、 应力状态、应变速率和变形量等因素对产生夹杂性裂纹具有重要影响。材料性质由使用要求决定,材料性质和夹杂特性在钢锭凝固后已不能改变,因而只能依靠控制热力参数实现质量控制。温度对材料变形能力和夹杂物性能有重要影响,温度的变化决定了裂纹产生方式。应力状态决定了裂纹处于扩展或不变化等状态,而裂纹产生具有累积效果,变形量的大小与裂纹尺寸密切相关。应变速率高,金属组织由于不能充分再结晶,材料易出现加工硬化,因而易产生裂纹。
2、控制锻造工艺要求
根据大型锻件的检验标准制定锻造工艺应控制的内容,如目前性能要求最高的核反应堆锻件,既要求做严格的机械性能检验,又要做探伤检查,因此应控制孔隙类缺陷夹杂性裂纹、金属组织和偏析程度。实际生产中,应根据产品形状 尺寸和性能等要求,选择相应的控制锻造方法 ,采取相应的措施。
2.1 合理的变形组合
生产饼块类锻件通常使用细长钢,致使心部变形量过大,因而夹杂性裂纹最为明显生产饼、块类锻件既要足够的变形量保证孔隙焊合,又要防止伴生出夹杂性裂纹。可以充分利用孔隙性缺陷焊合后不会开裂,夹杂性裂纹处于动态变化这一规律,采用分步法,即预锻工艺使用 W HF FM和JTS法等大型锻件锻造工艺解决轴类锻件的空洞压实问题,终锻工艺充分利用夹杂性裂纹的变化特点控制夹杂性缺陷。
2.2 控制夹杂物形貌
通常钢锭中的夹杂近似球状,在变形初期其应力集中较小,夹杂周围不会产生微裂纹,锻件心部的塑性夹杂在变形过程中逐渐由球状、椭球状变为片状,变形量越大则夹杂成为片状的可能性越大,而成为片状的夹杂构成锻件心部潜在的裂纹源。由下图可知,夹杂越扁应力集中越大,越易使基体金属断开,形成夹杂性裂纹,致使探伤超标。在制定锻造工艺时,依靠选择钢锭锭形可以较容易控制夹杂形貌,如一个钢锭生产二个锻件,但超大型锻件受钢锭和锻造能力限制不适宜用此法。
2.3 依靠高温和变形修复夹杂性缺陷
研究表明,构成探伤超标的夹杂性裂纹原理上均可修复,但其修复机制各异,修复条件大不相同对于内部微小裂纹由于加热体积变化,裂纹表面接触,通过高温扩散和再结晶裂纹可以焊合;较大的夹杂性裂纹则需通过塑性变形使联接基体的裂纹焊合,通过大变形可以弥散引起缺陷的塑性夹杂,从而使锻件内部缺陷不超过探伤检查标准。
2.4 预留变形量用于控制缺陷
为消除大型锻件中可能产生的探伤超标的夹杂性裂纹,在锻造工艺中可以通过最后的整形工艺修复缺陷。具体执行时,首先使用镦粗和W HF FM或JTS法等工艺压实钢内孔隙性缺陷,并使锻件外形接近零件要求,返炉后重新加热至再结晶温度以上200°C,然后按可修复夹杂性裂纹的变形量进行终锻并整形。控制终锻火次的另一目的是保证锻件内部晶粒尺寸不粗大和避免混晶现象发生,满足晶粒度检验要求。
3、应用工艺实例
根据上述思想制造的300MW核电特大管板锻件在第一重型机械集团公司取得了重大成功,填补了国内空白,并使普通管板锻件生产合格率由舞锻热处理新技术新方法50%上升到95%以上。
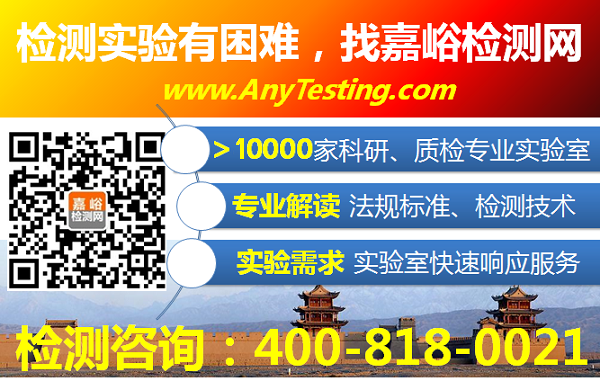