偏航轴承是偏航系统中的重要部件,位于机舱的底部,承载着风力发电机主传动系统的全部质量,并传递气动推力到塔架,可以准确、适时地调整风力发电机的迎风角度。偏航轴承是风力发电机及时追踪风力变化的保证。风力发电机组偏航变桨轴承一般采用单排或双排四点接触球转盘轴承,承受着较大的轴向力、径向力以及倾覆力矩的共同作用。
某型双排四点接触球风电偏航轴承在服役期间出现多起轴承外圈断裂情况,仵永刚对其进行一系列理化检验与分析,查明了该轴承的断裂原因,以避免该类问题再次发生。
一、理化检验
1.1 宏观观察
断裂轴承外圈的宏观形貌如图1所示,发现轴承外圈出现贯穿断裂或局部断裂,并且轴承套圈断裂位置非常一致,均位于外圈装球缺口部位。
断裂轴承外圈断口处的宏观形貌如图2所示,可见断口整体由4个独立断口组成,各独立断口断裂源均分布在装球缺口与锥销孔交接的尖角附近,各断口可见弧线状疲劳辉纹,呈疲劳断裂扩展形貌。
1.2 化学成分分析
采用直读光谱仪对断裂轴承进行化学成分分析,根据结果可见断裂轴承的化学成分符合GB/T 29717—2013 《滚动轴承 风力发电机组偏航、变桨轴承》对42CrMo钢的要求。
1.3 金相检验
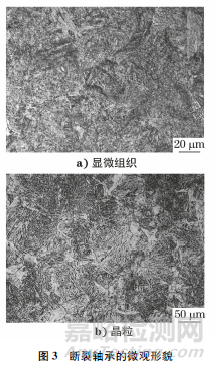
在轴承外圈装球缺口与锥销孔断裂位置取样,并进行金相检验,结果如图3所示,可见断裂轴承的显微组织为回火索氏体调质组织,晶粒度等级为7.0级。
1.4 力学性能测试
在断裂轴承外圈基体处取样,并进行力学性能测试,结果如表1所示,可见断裂轴承的力学性能均符合JB/T 6396—2006 《大型合金结构钢锻件 技术条件》的要求。
表1 断裂轴承的力学性能测试结果
1.5 扫描电镜(SEM)与能谱分析
在轴承外圈断口处截取试样,并进行SEM分析,结果如图4所示,其中断口Ⅱ和断口Ⅲ的断裂源因受到挤压摩擦而被严重破坏。由图4可知:断口Ⅰ断裂源位于孔壁摩擦塑性变形沟槽底部,断口Ⅳ断裂源位于孔壁腐蚀坑底部,断口Ⅰ和断口Ⅳ的断裂源均位于锥销孔的孔壁处,与装球缺口的距离为0.5~1.5mm,断裂源位置有明显的金属塑性变形和挤压摩擦痕迹,呈沟槽状[图4a),4c)圆圈所示标记位置为断裂源位置];锥销孔的孔壁有大量沿圆周方向分布的摩擦塑性变形痕迹,局部锈蚀明显。
对断口Ⅰ和断口Ⅳ的断裂源进行能谱分析,发现断口Ⅰ断裂源处的化学成分为42CrMo钢基体成分,未发现夹杂物分布痕迹;断口Ⅳ断裂源处主要含有Fe、O元素,推测其主要成分为铁锈(见图5)。
二、综合分析
由上述理化检验结果可知,断裂轴承的化学成分、显微组织、晶粒度、力学性能均未见异常。双排四点接触球偏航轴承的结构复杂,轴承内圈与机舱连接,外圈和塔架顶部法兰通过螺栓连接,锥销孔和安装孔均匀分布,风机在工作过程中受轴向力、径向力和倾覆力矩的联合作用。风力发电机开始偏转时,偏航加速度会产生冲击力矩。偏航转速越高,产生的加速度就越大,使转动惯量增大,导致本来就很大的冲击力矩成倍增加。
在轴承支撑刚度不能保证轴承受力后的结构稳定时,冲击或交变载荷使轴承套圈产生一定的弹性变形,并引起内部应力重新分布。在轴承表面的边界棱角处,棱角效应增加,产生严重的应力集中。应力集中削弱了轴承的强度,降低了轴承的承载能力,是引起轴承破坏的主要因素。
应力集中部位的表面损伤加剧了应力突变带来的影响,在相同的应力水平作用下,轴承的疲劳寿命随着表面粗糙度的增加而降低。塑性变形凸起、划痕、腐蚀坑等都是常见表面损伤形态,会降低轴承表面完整性,并在环境和交变载荷的影响作用下诱发显微裂纹,形成疲劳裂纹源。裂纹在交变冲击载荷的作用下逐步扩展,形成疲劳扩展特征,最终导致轴承外圈断裂。
三、结论与建议
风电偏航轴承外圈装球缺口与锥销孔结合部位存在应力集中,在锥销孔内壁塑性变形损伤及腐蚀部位产生疲劳裂纹源,裂纹逐步扩展,导致轴承发生疲劳断裂。
建议在安装使用轴承时,加强轴承支撑刚度,确保轴承套圈弹性变形可控;加强日常维护保养和监测,避免在安装孔、锥销孔等应力集中位置产生表面损伤。
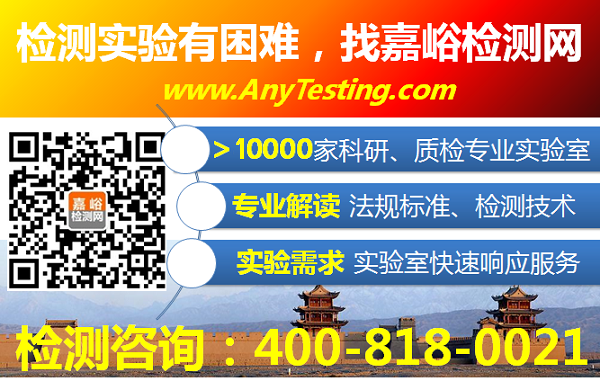