[摘要] 提出一种采用等效结构应力法计算汽车座椅骨架焊接结构疲劳寿命的方法。通过建立壳单元模拟焊缝结构的精细化有限元模型,开展座椅骨架的有限元分析,确定可能的疲劳失效部位;采用雨流计数法统计强化道路测得的汽车座椅随机载荷谱。以Conover 八级编谱原理为基础对雨流计数法结果进行再编谱,得到有工程代表性的等寿命典型载荷谱块。用结构应力法计算焊缝处的等效应力,以典型载荷谱、主S-N曲线为输入计算汽车座椅骨架的疲劳性能。对比实际试验统计数据,验证了提出的评估方法的有效性。
引言
汽车座椅是汽车必备的部件,座椅骨架通常用钢制管材焊接或者钢板冲压后焊接而成,行车过程中承受动态变化的载荷作用,常常发生焊接部分的疲劳损伤破坏,从而导致座椅骨架使用寿命降低,因此对汽车座椅骨架进行疲劳寿命研究具有重要意义。
目前,汽车行业常采用S-N 应力法估算疲劳寿命。相关研究中,周美施[1]等建立电动汽车车架有限元模型,基于工程中常用的恒幅载荷谱,用S-N 曲线法计算电动汽车车架疲劳寿命,并进行结构壁厚的优化设计;杨苍禄[2]等用CAE 技术建立汽车转向节有限元模型,施加多种工况恒幅载荷谱,用名义应力法进行疲劳分析并用耐久性试验对有限元结构进行可行性分析;高晶[3]等通过整车在不同等级道路上动力学分析,得到作用在弹簧座上的随机载荷谱,用名义应力法计算复杂工况下疲劳性能并做台架疲劳试验,最终得到模拟寿命和试验数据一致。名义应力法是参考结构和材料的疲劳危险部位的应力集中系数和名义应力来评估寿命,但标准试验焊接接头形式简单,试验数据有限,无法和实际汽车零部件复杂结构相匹配。近年来,随着测量技术和有限元技术的发展,基于真实工况下随机载荷谱开始应用于疲劳分析计算中。Singh[4]等以实验室和现场测得的随机载荷谱为基础,对载荷谱进行扩展和转化,并用Coffin-Manson,Morrow 模型计算疲劳寿命;王文伟[5]等通过对电动汽车电池箱结构建模,用频域分析和材料S-N 曲线法分析电池箱结构在随机振动条件下疲劳性能;孔振海[6]等分析在不平坦路面工况、制动工况、侧滑工况下轻型汽车前桥模型的受力状态,用名义应力法对前桥寿命进行预测;张林波[7]等模拟两种路面不同的载荷工况,用有限元法对车架进行弯曲疲劳寿命计算,并用试验验证计算寿命的合理性;宋桂秋[8]等考虑轮胎的试验气压对车轮的影响,通过加载动态载荷得到危险位置的载荷历程,用软件仿真车轮动态载荷疲劳寿命。
名义应力法,也称为应力-寿命法(Stress-life Method)是最早采用的疲劳寿命评估方法。该方法主要依据大量标准试验测试的材料曲线基础,参考结构和材料试件的疲劳危险部位应力集中系数和名义应力计算疲劳寿命。该方法计算简单,但在大量不同焊接接头的试验数据中选择合适的S-N 曲线比较困难,而且不同的焊接工艺可能无法找到匹配的焊接接头。Dong[9]基于平衡原理,提出等效结构应力法,以一条主S-N 材料曲线来估算复杂的焊接结构疲劳寿命,已在多个领域得到证实和应用。另一方面,恒幅载荷谱载荷形式单一,往往无法模拟真实的工况,导致计算精度不高。雨流计数法可以对实测载荷谱进行有效的统计和分析,准确得出随机载荷谱的幅值和均值分布情况,为再编谱提供良好的数据支持。
本文将等效结构应力法应用于汽车座椅骨架的焊接结构寿命估算中,使用壳单元模拟焊接结构,建立汽车座椅骨架有限元模型;采用雨流计数法对实测载荷谱进行统计分析,再以八级编谱为基础编制典型载荷谱。主S-N 曲线作为输入,以结构应力法计算焊接结构等效应力,最后得到焊接结构疲劳寿命,具体的过程如图1 所示。
图1 整体流程图
Fig.1 Overall flow chart
1、有限元模型建立和分析
座椅骨架一般采用氩弧焊进行焊接,焊接时的高温导致材料属性发生突变,形成疲劳性能薄弱的焊接区,焊接局部结构包括母材、焊趾、焊喉、和焊根区域,如图2 所示,焊喉是直接连接母材的部分,焊根是焊喉在母材上投影区,根据实际焊接的加工尺寸和经验得出焊趾的长度为两个被连接板件的厚度之和。采用壳单元模拟焊接结构,在保证计算精度的前提下壳单元可以降低网格调整时间和大量计算时间。座椅骨架在靠背骨架连接处、座盆骨架和座盆安装脚骨架处经常发生疲劳破坏,所以对这些区进行局部细化建模。
图2 壳单元模拟焊接结构图
Fig.2 Simulation welding structure diagram of shell element
根据座椅真实尺寸装配关系建立座椅整体结构有限元模型,如图3 所示。依据被焊接件的相对位置,以焊趾、焊根、焊喉的尺寸大小关系为基准,对座盆骨架边缘处(a)、靠背骨架连接处(b)、座盆安装脚骨架(c)建立局部精细化壳单元焊缝,如图3 中局部放大图所示。
图3 汽车座椅有限元模型
Fig.3 Finite element model of automobile seat
计算时,在滑轨的螺纹孔处施加固定约束,在座盆上施加大小为800 N 的均布载荷。材料设置为S500 结构钢,在标准温度下屈服强度为508.5 MPa,泊松比0.33。有限元静力分析结果如图4 所示。结果表示座椅整体结构应力分布比较均匀,在靠背骨架连接处(b)、座盆安装脚骨架(c)的应力相对较小,分别为89,115.8 MPa,而在座盆骨架边缘处(a)应力较大,最大值达到588 MPa,此处应为座椅骨架的危险部位。
图4 汽车座椅骨架应力云图
Fig.4 Stress nephogram of automobile seat frame
2.1 雨流计数法分析
雨流计数法是工程实际中常见的处理随机载荷谱的方法,综合考虑了动强度(幅值)和静强度(均值)2 个变量,符合疲劳载荷本身固有的特性[11]。首先以载荷谱最高峰或最低峰值为起点,然后将载荷谱旋转90°;接着雨流依次从最高的峰(或谷)向下流动,一直到最下一个峰(或谷)停止。同时当遇到来自上面留下的雨流就结束,记录下雨滴流过所有的完整循环和各自循环的幅值和均值。
根据有限元分析结果,座椅坐盆连接处应力最大。以文献[12]实测结果为例,提取座椅骨架座盆试验中的随机载荷谱片段,通过去除不合理数据和平滑处理,得到如图5 所示随机载荷谱,用雨流计数法统计载荷均值和幅值的频数变化,如图6 所示。
图5 实测随机载荷谱
Fig.5 Measured random load spectrum
图6 雨流计数法直方图
Fig.6 Rain flow counting histogram
2.2 等效载荷谱编制
根据雨流计数法的数据统计结果,运用“波动中心法则”将二元随机变量简化为只考虑载荷循环的幅值而忽视载荷循环均值,可用统计结果循环均值的算数均值表示载荷波动中心。一般将载荷谱分为4~16 级的载荷谱块。Conover 发现将载荷谱分成8 级可以准确地估算疲劳性能。根据Conover比值系数1.000,0.950,0.850,0.725,0.575,0.425,0.275,0.125 分级,计算结果如表1 所示。
表1 8 级载荷统计表
Tab.1 Statistical table of level 8 load
由于实测载荷谱的载荷时间长、损伤幅值大,在试验中不宜加载,且计算时间也过长,为了提高载荷谱的普适性和典型性,采用将疲劳极限低于60%和频次小的载荷去除,最终保留4,5,7,8 级作为试验载荷谱块。基于真实载荷谱的随机次数加载,选用“低—高—低”的加载次序,综合考虑载荷谱本身的工况特征,得到试验典型载荷谱块,结果如图7 所示。
图7 典型载荷谱块
Fig.7 Typical load spectrum block
3.1 应力计算
焊接结构因为结构和材料属性的突变使得在焊缝处应力分布呈现高度非线性,结构应力法只考虑危险截面整体力和力矩的平衡。座椅骨架发生疲劳破坏一般在焊趾部分,焊趾部分应力分布比较复杂,因此首先要关注焊趾部位的结构应力。局部坐标系焊趾结构如图8 所示。壳单元结构计算弯曲应力和膜应力的过程包括:设置局部坐标系,明确局部坐标系的法向方向,将焊缝沿着网格边线长度方向节点进行编号1、2……n;设ln为n 节点到n+1 节点之间的距离,根据力和力矩平衡原理可以计算出单位截面上在n 节点处力Fn和线力fn、节点力矩Mn 和线力矩mn 之间的关系式(1)、式(2)。
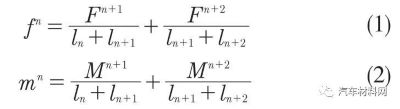
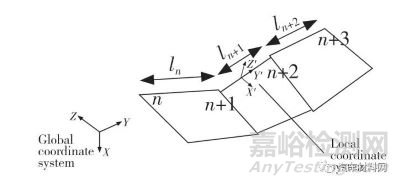
图8 局部坐标系焊趾结构
Fig.8 Weld toe structure in local coordinate system
将节点力和线力、节点力矩和线力的关系在全局坐标系中转化,可以得到膜应力σmembrane 和弯曲应力σbending,再通过结构应力式(3)计算得到结构应力值σs
等效结构应力是基于断裂力学中Paris 公式两阶段裂纹扩展规律,基于大量的疲劳试验数据统计和归纳[9],最后推导得出式(4)—式(6)。
载荷弯曲比r:
式中:Δσbending——弯曲应力变化幅度;Δσs——结构应力变化范围。
载荷效应的无量纲函数I(r):
式中:q——裂纹扩展参数,钢材为3.6。
结合载荷效应、板厚影响和应力变化计算得到等效结构应力ΔSS:

式中:t——板的厚度。
3.2 主S-N 曲线
Battelle 试验室通过大量的试验[10],用数据统计的方法得到用等效结构应力ΔSS 表达不同焊接接头形式的S-N 曲线落入非常狭窄的分布带的结果,从而最终推导出主S-N 曲线理论,表达式为
式中:h,Cd——依据不同的材料试验分析得到的常数值;N——寿命值[10]。
图9 是钢材焊接结构的主S-N 曲线图,和名义应力法类似,但是它更加全面考虑了焊接接头的应力分布、平衡原理、膜应力和结构应力等综合因素。
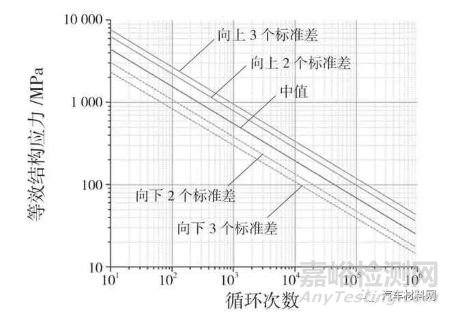
图9 主S-N 曲线图
Fig.9 Main S-N curve
3.3 疲劳寿命评估结果
根据汽车座椅有限元计算结果、等效结构法应力法和典型载荷谱块计算焊接结构的等效结构应力值,并结合线性累积原理,以主S-N 曲线为基础计算焊接结构疲劳寿命值如图10 所示。从云图中得出,寿命最小值在座盆骨架边缘焊接处,寿命值为12.1 万次。
图10 汽车座椅骨架焊接结构寿命云图
Fig.10 Cloud chart of automobile seat frame structure
汽车座椅骨架台架试验是将座椅系统安装在适当的模态安装台上,固定两边滑轨,施加相应工况下的载荷谱,经过载荷谱的循环作用,结构发生疲劳破坏的过程。如图11 所示,通过大量的同一座椅骨架平台的台架试验数据分析,得出座盆骨架断裂和座盆安装脚骨架开裂占比30%,靠背骨架断裂20%,靠背调角器裂纹破坏占比20%。座盆骨架焊接处为疲劳破坏高危区,与本文寿命评估得出破坏结果一致,验证了提出方法的有效性。
图11 汽车座椅骨架试验结果
Fig.11 Test results of automobile seat frame
采用雨流计数法对实测汽车座椅强化路面载荷谱进行数据统计分析,以8 级编谱理论为基础,编制有工程代表性的典型谱块,此载荷谱全面考虑了载荷加载顺序和小载荷作用,形式简单,易于实际加载。
依据座椅真实尺寸、装配关系和焊接结构的几何特性,建立精细化有限元模型并进行应力分析,发现座椅易损伤的区域,此模型计算结果更加贴近真实工况,为精细化有限元分析提供参考。
计算焊接结构等效结构应力,以主S-N 曲线为基础,将典型载荷谱作为输入结合线性累积原理得到焊接结构疲劳寿命。通过座椅台架试验的方式,验证此疲劳分析方法的合理性和准确性。
参考文献
[1] 周美施,尹怀仙,张铁柱,等.考虑疲劳寿命的负载隔离式电动汽车车架轻量化研究[J].公路与汽运,2016(4):1-4.
[2] 杨苍禄,朱传敏,刘素,等.汽车转向节疲劳寿命分析和试验研究[J].机电工程,2015(7):950-953.
[3] 高晶,宋健,朱涛.随机载荷作用下汽车驱动桥壳疲劳寿命预估[J].机械强度,2008(6):982-987.
[4] Singh S S K,Abdullah S,Ariffin A K.Fatigue reliability assessment in time domain using stochastic-induced random stress loads due to limited experimental data[J].Engineering Failure Analysis,2020,117(2).
[5] 王文伟,程雨婷,姜卫远,等.电动汽车电池箱结构随机振动疲劳分析[J].汽车工程学报,2016,6(1):10-14.
[6] 孔振海,王良模,荣如松,等.基于HyperWorks 的某轻型汽车前桥有限元分析及疲劳寿命预测[J].机械设计与制造,2013(2):97-100.
[7] 张林波,柳杨,黄鹏程,等.有限元疲劳分析法在汽车工程中的应用[J].计算机辅助工程,2006(S1):195-198.
[8] 宋桂秋,朱志鹏,李一鸣,等.全表面车轮径向疲劳试验的数值仿真及疲劳寿命分析[J].汽车工程,2017,39(5):556-560.
[9] Kyuba H,Dong P.Equilibrium-equivalent structural stress approach to fatigue analysis of a rectangular hollow section joint[J].International Journal of Fatigue,2005,27(1): 85-94.
[10] Dong P.A structural stress definition and numerical implementation for fatigue analysis of welded joints[J].International Journal of Fatigue,2001,23(10): 865-876.
[11] Rychlik I.A new definition of the rainflow cycle counting method[J].International Journal of Fatigue,1987,9(2): 119-121.
[12] 马浩松.座椅骨架疲劳强度试验的开发与研究[D].上海:上海交通大学,2007.
[13] 徐颢.疲劳强度[M].北京:高等教育出版社,1988.
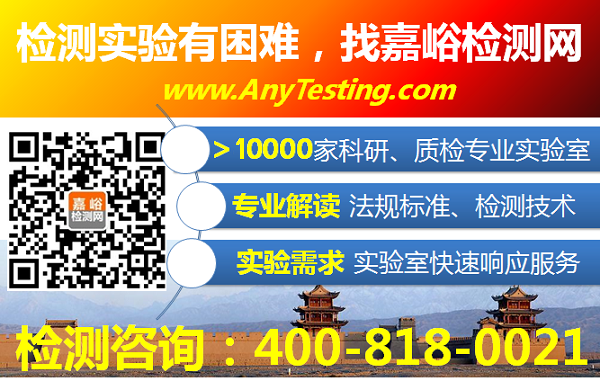