钼是一种具有许多优良的物理、化学和力学性能的金属,熔点高达2620 ℃,为典型的难熔金属。由于钼原子间结合力极强,所以在常温和高温下强度及弹性模量都很高,并且膨胀系数小,导电、导热性能优良,抗腐蚀性能良好,被广泛应用于冶金、电气、化工、环保等行业,成为国民经济中重要的、不可替代的战略金属。
虽然钼的高温性能优异,但由于其塑-脆转变温度较高,高温条件下使用的钼回到室温附近时会出现严重的脆性,限制了其应用。目前,国内外学者针对在钼中掺杂微量元素以获得更好的性能方面开展了大量的研究。在钼中掺杂一定稀土氧化物,可以极大程度改善钼的韧性,降低韧脆转变温度,提高再结晶温度,改善高温力学性能,进一步扩大其加工及应用范围。
一、合金的掺杂工艺
通常,在Mo金属中掺杂La2O3的方式主要有以下三种:
(1) 固-固掺杂法:将钼粉与La2O3粉末通过球磨方式混合,经压型、再烧结形成钼合金;
(2) 固-液掺杂法:将硝酸镧雾化喷入氧化钼,干燥后进行还原,经压型、再烧结形成钼合金;
(3) 液-液掺杂法:向钼酸盐溶液加入可溶性镧盐溶液,通过喷雾干燥、还原、压型、烧结形成钼合金。
1、固-固掺杂法
目前固-固掺杂法工艺已十分成熟,能够较大程度提高钼的性能,但如果掺杂的稀土含量较少(<1%)时,存在稀土元素在基体中分布不均匀的问题。
刘涛等采用固-固混合法,将10%氧化镧以固态颗粒形式掺杂至二氧化钼中,经还原形成复合钼镧粉,经冷等静压和1900 ℃×3 h的高温烧结得到钼镧合金,粉末形貌和烧结钼镧合金组织如图1和图2所示,研究发现:氧化镧以团聚体或与二氧化钼碎屑形成团聚体形式存在。其稀土相主要是La(OH)3,少量以La6Mo2O15存在于细小颗粒团聚体中。
图1 掺杂镧MoO2粉末扫描电镜
图2 烧结钼镧合金扫描电镜
付小俊采用混粉制料、压型、烧结的方法制备钼镧合金,通过对断口形貌的分析发现,固-固掺杂生产合金钼粉烧结后晶粒相对细小,断裂以沿晶断裂为主,而通过固-固悬浊液和固-固+喷水雾的方法制备的钼镧合金,其粉末晶粒较大,与固-液掺杂后制备的晶粒相似,合金密度有所提高。
吴壮志等发明了一种高性能超细晶钼镧合金的制备方法,首先通过水浴法获得球形纳米La2O3粉末,与钼粉混合后,采用SPS烧结工艺,压力30~50 MPa,烧结温度在1500~1600 ℃,保温4~6 min,获得3.7 μm左右晶粒尺寸的合金,抗拉强度较传统的固-固掺杂工艺提高16%以上。
2、固-液掺杂法
固-液掺杂法具有成本较低、工艺可控性良好、操作简便等特点,是目前生产企业中应用最广泛的一种方法。
刘宁平等将硝酸镧用酒精溶解后,在球磨机中与钼粉均匀混合,烘干后采用粉末冶金方法制备钼镧合金,该方法简单易行,制备出的钼镧合金组织均匀,性能优良。
刘仁智等通过固-液掺杂法制备Mo-0.7%La合金坯料,再经90%变形量的轧制加工制成合金板,研究钼镧合金热处理后的微观组织稳定性,通过观察和金相模拟发现组织从变形加工态纤维组织经热处理后演变成等轴晶状,然后形成宽条状,在1373 K、4320 h以内的热处理工艺条件下,组织均呈现较好的稳定性。
王锦等通过制备前驱粉和固-液掺杂法两种工艺制备了弥散强化钼镧丝材,对比研究证实了基体中La2O3相的存在,分析了第二相粒子对钼合金加工性能影响规律,提出通过适当调整拉拔温度、增加退火次数或者减小冷拉量来改善丝材的性能,以提高材料成品率。
固-液掺杂法是通过硝酸物的形式掺杂,故在配置硝酸镧溶液和还原硝酸镧过程中会产生大量的NO、NO2等危害气体,对环境造成一定危害。尤其近年我国环保政策力度加大,工业生产受到限制,迫切需要开发新的工艺方法。
3、液-液掺杂法
相比于前两种工艺,液-液掺杂法先将掺杂基体和掺杂剂以溶液的方式混合,保证了各成分混合的均匀性,可用于制备高性能钼合金。
王攀等将仲钼酸铵加入La(NO3)3溶液中制成白色粉末,并于粉末中加入适量柠檬酸溶液,真空烘干成凝胶。之后将凝胶焙解生成掺杂MoO3,经过二段还原反应后通过压型、烧结制备钼镧合金。掺杂Mo粉的稀土相形貌如图3所示,Mo粉颗粒分散性很好,大多呈规则多面体,颗粒十分细小。烧结钼合金坯断口形貌如图4所示,La2O3颗粒以点状物形式弥散分布在钼基体上,与钼基体结合良好。
图3 掺杂Mo粉的稀土相形貌
图4 烧结钼坯断口形貌
杨涤心等通过液-液法制备了不同稀土种类及含量的钼合金坯,研究发现液-液法制备Mo-La-Y复合粉体时,掺杂稀土的种类和掺杂含量的变化对钼粉的形貌及尺寸的影响不明显,而总体上钼坯基体颗粒随掺杂含量的增加而变细,并逐步规则化,适当提高掺杂含量或者采用双元复合掺杂有利于提高钼坯的硬度。
周美玲采用硝酸盐水溶液湿法掺杂3%~6% Re2O3(La2O3、Y2O3、Sc2O3)和350~500 ℃加热分解的方法成功制备了新型稀土钼阴极材料,该方法保证了Re2O3在钼基体中的均匀弥散分布,满足了电子阴极规格要求的Mo-Re2O3细丝的批量生产,其最小直径达0.19 mm,性能优异。
4、不同工艺的对比研究
三种掺杂工艺各有其优缺点,研究人员针对不同工艺进行了对比研究,固-液法制备的合金材料在化学成分、粉末粒度、晶粒尺寸、抗拉强度等方面要优于固-固法,与液-液掺杂法相比,又稍有逊色。表1列出了三种工艺在性能方面的优劣势情况。
表1 三种掺杂工艺对比表
二、合金的力学性能
1、抗弯强度
郭让民等采用不同轧制和退火工艺制备Mo-1.0%La2O3钼镧合金板材,测试了1700 ℃和1800 ℃的抗载荷弯曲性能,钼镧合金板晶粒细小均匀,较常规钼板性能优异。当加大变形量和调整热处理工艺时,最大弯曲值小于常规热轧板材弯曲值的20%。这是由于经高温再结晶后,晶粒相互搭接,具有较低内能,高温下蠕变减小,有利于抗弯曲性能的提高。
表2列出了纯钼和钼镧的烧结态和锻造态坯条的抗弯强度及弯曲角数据。由表2可知:与纯钼坯相比,钼镧坯的抗弯强度最高为796 MPa,提高了27%,锻造加工后抗弯强度最高提高至1259 MPa。同时,La2O3的加入对钼的韧性(以弯曲角表示)也有明显的改善作用,烧结态纯钼的弯曲角仅为5°,而钼镧坯弯曲角可达15.3°,坯料的抗弯性能得到了大幅度提高。
表2 纯钼和钼镧的弯曲强度对比
2、抗拉强度
李敏通过固-液法制备3.5 mm的钼镧合金板材,测量不同温度下抗拉强度。研究发现:随着温度的升高,抗拉强度呈现下降的趋势;同时,断后延伸率随着温度的升高而增加。300、500、700 ℃时,抗拉强度及延伸率分别可达627.3 MPa、7.3%,561.7 MPa、8.5%和453.4 MPa、9.3%。
吴朝圣等研究发现:在900 ℃以下时,具有细晶组织的钼镧轧制板抗拉强度优于粗晶组织。
淡兴国等以不同粒度的氧化镧粉为原料,采用固-固法制备了钼镧合金板材。研究表明:掺杂粒度增加使烧结过程中粉末长大受到阻碍,相应的金相粒径减小,性能上轧制横向强度要大于轧制纵向强度,但横向延伸率低于纵向延伸率,而横向强度随着掺杂粒径减小而依次增大,延伸率提高,如表3所示。
表3 相同成分不同晶粒尺寸的钼镧板力学数据
张久兴等采用La2O3的质点强化量,其公式计算为:
Δσb = σb(Mo-La2O3) - σb(PMo)
式中:σb(Mo-La2O3),σb(PMo)分别是Mo-La2O3合金板材和纯钼板的高温抗拉强度值。
La2O3对加工态钼镧板高温性能的影响如图5所示。由图5可知:添加La2O3大幅度提高了钼的高温强度,强化幅度随La2O3掺杂量的增加而增加,在800~1500 ℃之间,2%~3%La钼镧板的高温抗拉强度较纯钼板提高100 MPa以上,而超过1400 ℃后钼镧板的高温抗拉强度甚至超过了TZM板。
图5 质点强化量随温度的变化
3、断裂韧性
由于稀土元素镧的掺杂,会导致O、C、N等脆性元素优先集中在晶界和稀土氧化物粒子表面,而稀土氧化物粒子同时分布在晶界和晶内,即增大了界面表面积,降低了晶界的杂质浓度,最终提高了钼的韧性。
杨帆在La-TZM的研究中也发现,氧化镧粒子能够细化晶粒,在晶界处阻碍位错的运动和穿晶断裂,显著提高了合金的强度和韧性,并且将其塑-脆转变温度降低40 ℃。
张久兴等提出了La2O3粒子钝化微裂纹机制,细小弥散分布的La2O3第二相粒子的存在,不仅可以使变形更均匀,缩短滑移面的有效长度,使位错塞积减弱;同时,大量的位错被La2O3粒子钉扎在晶内或强滑移带内,使晶界或强滑移带附近的位错密度降低,这种位错组态延缓了沿晶微裂纹的产生。测试数据显示,烧结态钼镧板材的断裂韧性KIC可达24.76 MPa·m1/2,是纯钼板(8 MPa·m1/2)的近3倍。
4、热发射性能
周美玲等将不同稀土元素的稀土钼阴极制成标准二极管,测试它们的热电子发射性能与参数,如图6所示。图6为有相近拐点电流的La2O3-Mo,Y2O3-Mo,ThO2-W三种阴极的I-U曲线,研究发现La2O3-Mo的发射效率最好,掺入微量的La2O3可以提高钼丝的再结晶温度,提高高温抗蠕变性能。而掺入量为4.0%时,在较低的温度下,就会有足够的La(La2O3)供应阴极表面从而形成良好的发射体,材料体现出优良的热电子发射性能。
图6 不同掺杂稀土的钼阴极I-U曲线
5、抗下垂性能
祁美贵等通过固-液粉末冶金方法制备了钼镧板坯。通过测量板坯的抗下垂性能,发现高温定型处理可以显著改善板材的组织形态。经高温定型,钼镧合金板具备较好的高温抗蠕变性能,并且在1750 ℃和500 g的载荷试验下,下垂值从原始态的4.2 mm减小至1.8 mm,体现了较好的高温抗下垂性能和抗变形能力。
三、影响合金性能的关键因素
影响钼镧合金最终性能的因素较多,包括掺杂物粒径、掺杂量、掺杂工艺、烧结工艺、变形工艺和热处理工艺等。其中,适当的掺杂量(1%)可以较大程度增加钼合金的强度和塑性等综合性能,但含量过高时,强度和延伸率反而降低,如图7所示。刘宏亮等的研究数据显示,当镧含量介于0.36%~0.93%之间时,随着合金中镧含量的增加,钼镧合金在700 ℃下时表现出的塑性越好。
图7 不同La含量的钼镧合金强度和延伸率曲线
烧结是粉末冶金过程中至关重要的环节,不同镧含量的粉末会有不同的烧结反应,烧结形成的烧坯致密度也会不同。因此,控制好烧结过程对提高材料性能非常关键。
研究表明,La2O3含量越高,出现异常大晶粒的烧结温度点就越低。在同一烧结温度下,随着La2O3含量的增加,越容易出现晶粒粗大,导致致密性降低,建议钼镧合金的烧结保温温度应控制在异常大晶粒出现之前,致密化效果更好。
卢瑶等通过SPS烧结制备Mo-1%La2O3合金,当烧结温度为1600 ℃,保温时间7 min时,合金平均晶粒仅为3.74 μm,烧结坯抗拉强度和抗压强度分别达765 MPa和2307 MPa,较管式炉氢气烧结的钼镧合金,在晶粒大小、均匀性、抗拉强度和抗压强度方面性能更优异。
另外,学者在对钼镧合金板材的轧制和热处理工艺研究中发现,将钼镧合金热轧的终轧加工率控制在50%以上,能明显改善轧后产品的组织和性能,可以保证在后续温轧加工中不开裂,强度、塑性和硬度综合性能良好,弯曲性能和后续温加工性能得到明显提高。对Mo-0.8%La钼镧合金板材,最合适的退火温度为1300 ℃,在此温度下晶粒发生再结晶,如温度继续升高,晶粒发生晶界迁移,晶粒长大。
四、应用领域
钼镧合金凭借其优异的性能,目前广泛应用于电子、航天、核能、机械加工等领域。
在电子领域中,由于钼镧合金具备强韧性、高发射性和无污染等特点,可以替代钍钨材料作为阴极材料,解决传统钍钨阴极在制备、加工和废弃后产生的严重放射性污染问题;在航天领域中,钼镧合金作为发动机用喷管材料,具有良好的抗烧蚀性能,充分满足短时固体火箭发动机的使用要求,并已得到批量使用;在机械加工领域,钼镧丝代替纯钼丝作为电火花线切割电极丝,使用寿命比纯钼丝提高约50%,可有效节约成本。
钼镧合金还可用作高温炉发热体、X射线极靶、模具等,非常具有推广应用价值。
五、结论
(1) 不同掺杂工艺均有特点,其中液-液掺杂法制备的钼镧合金较固-固掺杂法、固-液掺杂法制备的钼镧合金,粉末粒度、晶粒尺寸更小,抗拉强度等性能更好。
(2) 钼镧合金中弥散的La2O3颗粒大幅改善了合金性能。相较于纯钼,钼镧合金具有更高的热电子发射性能、抗拉与抗弯性能,同时有着更好的延展性与断裂韧性,并具有良好的抗蠕变性能。
(3) 鉴于钼镧合金的优异性能和较大的应用价值,后续研究可以与实际生产相结合,针对市面上常用的钼镧合金材质,从理论研究、制备方法、工艺研究等方面提供理论与数据支持,促进钼镧合金制品的应用与发展。
作者:唐亮亮,林冰涛,弓艳飞,王承阳,张保红,熊宁
工作单位:安泰科技股份有限公司,安泰天龙(北京)钨钼科技有限公司
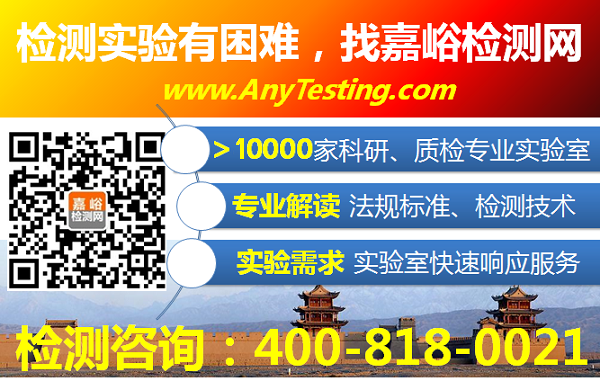