【摘要】 对380CL钢汽车车轮进行了弯曲疲劳试验,随后对轮辐进行了疲劳断口分析和金相检验,包括夹杂物的形态、分布和成分,以揭示轮辐疲劳失效的原因。结果表明:疲劳裂纹萌生于轮辐表面,这与微动磨损有关;在振动和法向力的共同作用下,轮辐表面以下形成了深度约100 μm的变形层;轮辐内存在较多尺寸为4 ~6 mm 的球状夹杂物,加速了高周疲劳阶段裂纹的扩展,导致轮辐的疲劳寿命降低。
【关键词】 轮辐,弯曲疲劳试验,裂纹,夹杂物
随着重载运输行业的发展,重载汽车的需求量越来越大,这对车轮的安全性和可靠性提出了更高的要求。车轮是汽车底盘系统中最重要的结构件[1-4],除承载车身质量外,还要承受弯曲和交变扭转载荷,起承载、驱动、转向和制动等作用,其性能将影响整车的安全性[5-7]。疲劳开裂是汽车运行中车轮的主要失效形式[3-4,8-9],在周期性载荷的作用下,车轮的疲劳损伤积累到一定程度就会断裂,具有不可预见性和隐蔽性,危害性极大。因成本优势和安全性,商用车普遍使用钢质车轮,通常由轮辋和轮辐焊接而成。轮辋在闪光对焊后采用滚压成形,是车轮周边安装和支撑轮胎的重要零件。轮辐通常采用旋压成形,是车轮上介于车轴和轮辋之间的重要支承件,因此要求车轮用钢具有优良的强韧性、可成形性、焊接性及耐疲劳性能等。车轮在使用前必须进行多项测试,其中弯曲疲劳试验是一项重要的测试项目。本文研究了380CL 钢轮辐在弯曲疲劳试验中疲劳失效的原因。
1、 试验材料与方法
1.1 试验材料
研究用380CL 汽车车轮钢的生产工艺为铁水预处理→转炉→LF精炼→连铸→热轧,精炼采用Ca处理,从强度、成形性能和焊接性能要求等方面考虑,采用低碳锰成分体系,并添加微量的Nb和Ti,一方面可以细化晶粒、提高强度,另一方面也可提高材料的可焊性。380CL钢的化学成分如表1 所示。
表1 汽车车轮用380CL钢的化学成分
Table 1 Chemical composition of 380CL steel for automotive wheel
380CL钢的抗拉强度为409 MPa,屈服强度为282 MPa,断后伸长率为35%。热轧采用3 +3 的粗轧工艺,中间坯厚度为50 mm;精轧经过7 架次轧制,层流冷却采用前段集中冷却,热轧卷厚度为13. 5 mm。热轧卷的抗拉强度为409 MPa,屈服强度为282 MPa,断后伸长率为35%。380CL钢的显微组织为铁素体和少量珠光体,铁素体晶粒度为10 级,无带状组织,如图1 所示。
图1 380CL钢的显微组织
Fig.1 Microstructures of the 380CL steel
1.2 弯曲疲劳试验
车轮的弯曲疲劳试验设备包括一个被驱动的旋转装置,车轮固定不动承受旋转弯矩;或使车轮在一个固定弯矩作用下旋转,如图2 所示。为对车轮施加弯矩,在加载臂上施加一个平行于车轮安装面的载荷。加载系统保持设定的载荷,试验设备安装台的表面光洁平整,且与车轮在车辆上采用的连接件具有相同的装配特性。试验对连接件表面硬度、螺孔或螺栓位置均有一定要求,试验弯矩、轮胎与路面间的摩擦因数等相关参数按GB/T 5909—2021《商用车车轮弯曲和径向疲劳性能要求及试验方法》设定,车轮尺寸为19. 05 ~57.15 cm,试验力为3 550 kg。弯曲疲劳试验结果如表2 所示。
图2 车轮弯曲疲劳试验示意图
Fig.2 Schematic diagram of bending fatigue testing for the wheel
表2 380CL钢车轮的弯曲疲劳试验结果
Table 2 Bending fatigue testing results of the 380CL steel wheel
2、试验结果和讨论
2.1 疲劳失效的轮辐
从表3 疲劳试验结果可以看出,虽然轮辐达到了标准要求的25 万次疲劳寿命,但在循环次数达到42.4 万次左右时检测到了疲劳裂纹,裂纹出现在轮辐的螺栓孔处,如图3(a)所示。裂纹出现在轮辐与试验台(车轮连接件)的接触面,延伸至螺栓孔内壁,轮辐螺栓孔周围还有明显的褐色磨损痕迹,是典型的微动磨损形貌,磨损深度不同,如图3(b,c)所示。
图3 失效轮辐的疲劳裂纹
Fig.3 Fatigue crack on the failed wheel disc
采用线切割从疲劳失效的螺栓孔处取样,检测裂纹部位的微观组织、夹杂物及断口形貌,如图4(a)所示。同时,在靠近螺栓孔内壁裂纹处切取断口试样,在开裂区域取样进行金相检验。在螺栓孔内壁发现严重磨损,连接螺栓在螺孔内壁靠近裂纹一侧出现明显的螺纹压痕,如图4(b)所示。说明在疲劳试验过程中,由于轮辐与连接件之间发生了滑移从而导致螺栓倾斜与内壁接触,产生压痕,这也从另一方面验证了疲劳试验过程中轮辐发生了微动磨损。在失效轮辐其他螺栓孔中相同方向的内壁也发现有这种现象。
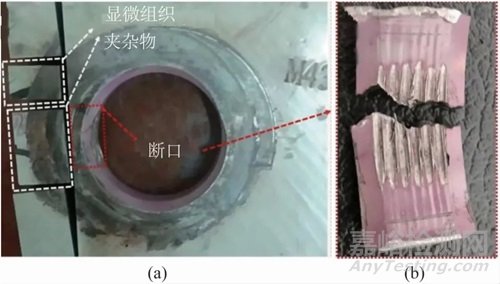
图4 失效轮辐(a)及从裂纹部位切取的试样(b)
Fig.4 Failed wheel disc(a)and the specimen cut from crack place(b)
从裂纹处的宏观组织可知,裂纹萌生于轮辐的上下表面并向内部扩展,两处裂纹均未贯穿辐壁,如图5(a)所示。由于轮辐两个面的裂纹均未贯穿,取样时用外力沿疲劳断裂面将轮辐断开,得到图5(b ~c)所示的白亮色断口。
图5 失效轮辐疲劳断口的宏观形貌
Fig.5 Macroscopic appearance of fatigue fracture of the failed wheel disc
褐色区域为疲劳断口,在循环载荷作用下,经过反复摩擦,断口表面较光滑。另外,由于断口已出现严重氧化(图6),疲劳辉纹不明显,如图5(d)所示。尽管断口污染较严重,但仍可看出裂纹起始于轮辐表面,扩展方向与厚度方向呈约30°的角,向螺栓孔内壁方向扩展至螺栓孔内壁。
图6 疲劳裂纹的能谱分析
Fig.6 Energy spectrum analysis of the fatigue crack
2.2 轮辐的显微组织
如图7 所示,失效轮辐的显微组织与图1 所示的380CL 钢卷的一致,为铁素体和珠光体,且在轮辐厚度方向晶粒细小均匀,轮辐中心有轻微偏析。因为疲劳裂纹的萌生及扩展未达到中心区域,因此中心偏析不会导致疲劳失效。
图7 疲劳失效轮辐表面以下1/2(a)和1/4(b)厚度处的显微组织
Fig.7 Microstructures at 1/2(a)and 1/4(b)thickness below surface of the fatigue-failed wheel disc
从断口形貌可知,在弯曲疲劳试验中,连接件或螺栓垫片在与轮辐的接触面发生了微动磨损,致使轮辐的上下表面发生塑性变形,如图8 所示。从图8(b,d)可明显看出,裂纹起始于晶粒变形区,其扩展方向基本与晶粒变形方向一致,即摩擦副相对运动的方向。变形层深度可达100 mm,并且裂纹附近变形层更深。从图8(b,d)可知,轮辐上下表面开裂处的晶粒变形深度分别为110 和128 mm。
图8 轮辐上(a,b)、下(c,d)表面的显微组织
Fig.8 Microstructures of upper(a,b)and lower(c,d)surface of the wheel disc
检测疲劳裂纹周围的夹杂物发现,轮辐D 类夹杂物较多,如图9(a)所示。夹杂物尺寸约4 ~6 mm,如图9(e,f)所示。夹杂物尺寸小、数量多,选一个较差视场评定为D2.0 细系。裂纹附近均有这类夹杂物,对裂纹的扩展有一定影响,如图9(b ~d)所示。
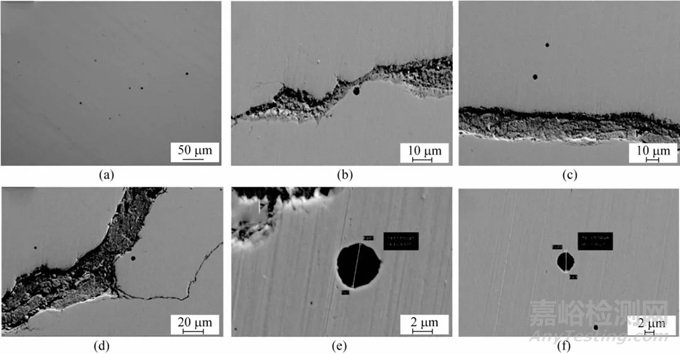
图9 轮辐疲劳裂纹附近的夹杂物
Fig.9 Inclusions near the fatigue crack in the wheel disc
对疲劳裂纹边部一球形夹杂物进行了能谱分析,结果显示,该夹杂物具有镁铝尖晶石结构,如图10(a ~b)所示。对另一球形夹杂物进行面扫描,结果表明,这类球形夹杂物内部为Al2O3 和MgO,外层为Mn、Ca、Ti的硫化物,如图10(c)所示。
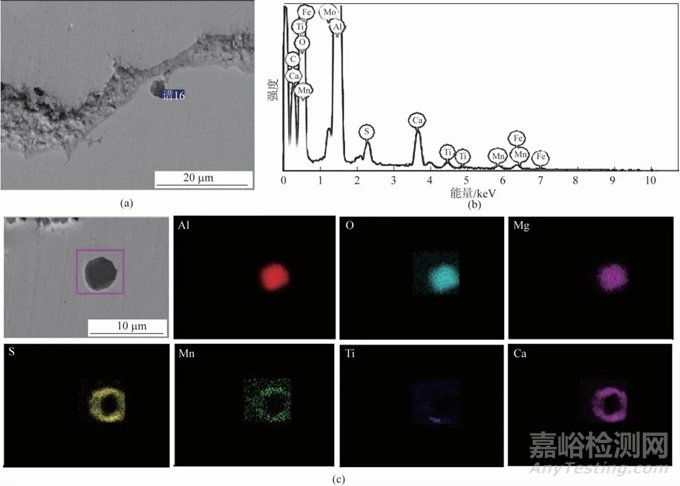
图10 失效轮辐内夹杂物的能谱分析(a,b)和面扫描分析(c)
Fig.10 Energy spectrum analysis(a,b)and linear scanning analysis(c)of inclusions in the failed wheel disc
2.3 轮辐疲劳开裂分析
如上所述,裂纹在螺栓孔边缘的上下表面产生,沿表面和壁厚方向扩展。疲劳试验过程中,车轮轮辐与试验台用螺栓固定,由于两者之间存在微米级的间隙,试验过程中发生微小的相对运动,接触面发生微动损伤。
在弯曲疲劳试验过程中,轮辐的失效与微动磨损有关。微动疲劳[10-12]是指在循环载荷的作用下,相互接触的表面在法向力作用下互相挤压并产生往复相对滑动,滑动幅度为5 ~400 μm,产生小振幅相对滑动,导致部件疲劳强度降低或早期断裂。在摩擦表面法向力和振动的作用下,产生粘合点和表面伤疤,疲劳往往产生于试样表面或有缺陷处或最大应力处,最终成为疲劳裂纹的起始点。
如图11 所示,失效轮辐的组织为图1 所示的铁素体和少量珠光体,其变形性能良好。在弯曲疲劳试验过程中,轮辐上下表面在车轮连接件和螺栓垫片夹紧力、摩擦力的作用下发生如图8 所示的塑性变形,塑性变形区会产生大量位错,导致塑性变形受阻,因此变形层深度仅约100 ~130 mm。轮辐表面发生微动磨损,在循环载荷的作用下轮辐表面应力集中区即晶粒变形层产生裂纹。

图11 轮辐弯曲疲劳试验过程中初始(a)和高周(b)阶段微动疲劳的示意图
Fig.11 Schematic diagrams of fretting fatigue at initial(a)and high cycle(b)stages during bending fatigue testing for the wheel disc
在循环载荷的持续作用下,裂纹进一步扩展。而轮辐内有大量如图10 所示的球状夹杂物,其变形性能差,导致基体与夹杂物的变形不一致,随着循环次数的增加,这种效应加剧,并在夹杂物周围产生应力集中,导致裂纹快速向这些应力集中点扩展。如图9、图10 所示,夹杂物尺寸小于10 mm,且形态为钙处理后的包覆类球形夹杂物,对成形和焊接等加工的影响不明显[13-14],但会恶化疲劳性能,所以在低周疲劳阶段夹杂物的影响较小,在高周疲劳阶段影响较大,导致380CL 钢轮辐的弯曲疲劳寿命仅为42.4 万次。为进一步提高轮辐的弯曲疲劳性能,尤其是螺栓孔部位的微动疲劳,在车轮用钢的冶炼流程尤其是精炼工序,应优化钙处理工艺,确保有足够的钢包底吹(静吹)时间提高钢水质量。
3、 结论
(1)疲劳裂纹从轮辐的上下表面萌生并向内部扩展,疲劳寿命为42.4 万次时,裂纹未贯穿幅壁。
(2)在弯曲疲劳试验中,轮辐表面与试验垫片和连接件之间在循环载荷的作用下产生微动磨损,并产生疲劳裂纹。
(3)在弯曲疲劳试验中,在法向压力和振动力的作用下,轮辐表面形成了深约100 mm 的塑性变形层,疲劳试验初期裂纹的扩展方向与变形方向一致。
(4)轮辐内有较多的尺寸为4 ~6 mm的球形夹杂物,加速了高周疲劳阶段裂纹的扩展,降低了轮辐的疲劳寿命。
参考文献
[1]HU J,DU L X,WANG J J,et al. Cooling process and mechanical properties design of hot- rolled low carbon high strength microalloyed steel for automotive wheel usage[J].Materials and Design,2014,53:332-337.
[2]许珞萍,邵光杰,李麟,等. 汽车轻量化用金属材料及其发展动态[J].上海金属,2002,24(3):1-7.
[3]JHA G,DAS S,LODH A,et al. Development of hot rolled steel sheet with 600 MPa UTS for automotive wheel application[J].Materials Science and Engineering A,2012,552:457-463.
[4]DEY A,JUGADE H,JAIN V,et al. Cracking phenomena in automotive wheels:an insight[J]. Engineering Failure Analysis,2019,105:1273-1286.
[5]张明博,刘效云,高建国,等. C380CL钢车轮焊缝开裂原因分析[J].上海金属,2019,41(3):34-38.
[6]马鸣图,SHI M F.先进的高强度钢及其在汽车工业中的应用[J].钢铁,2004,39(7):68-72.
[7]祖荣祥.热轧高强度钢的研究及在汽车车轮上的应用[J].汽车工艺与材料,1994(12):23-27.
[8]康永林,朱国明.中国汽车发展趋势及汽车用钢面临的机遇与挑战[J].钢铁,2014,49(12):1-7.
[9]张大伟,杜林秀,肖宝亮,等.乘用车轮辐用600 MPa 级热轧双相钢失效原因分析[J]. 金属热处理,2018,43(7):224-228.
[10]OUNPANICHA D,MUTOH Y,YOSHII K. Plain fatigue and fretting fatigue behavior of hot- rolled steel sheet after cold spinning[J]. Materials Science and Engineering A,2009,509(1/2):14-22.
[11]蒋小松,何国求,何冰,等.材料的微动疲劳机理及防护措施的研究进展[J].材料导报,2008,22(12):10-14.
[12]ZHENG J F,LUO J,MO J L,et al. Fretting wear behaviors of a railway axle steel[J]. Tribology International,2010,43(5/6):906-911.
[13]杨振国,张继明,李守新,等. 高周疲劳条件下高强钢临界夹杂物尺寸估算[J]. 金属学报,2005,41(11):1136-1142.
[14]温瀚. SCX400 车轮钢非金属夹杂物控制工艺研究与实践[J].炼钢,2020,36(6):54-60.
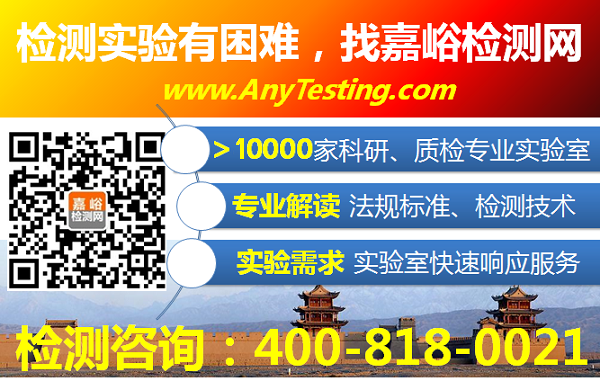