作为常用的金属材料,铜因强度较低而应用范围受限,石墨烯具有优异的综合性能,作为极具潜力的增强体而受到广泛关注。石墨烯增强铜基复合材料兼具了铜和石墨烯的优良性能而成为了重要的研究对象。介绍了石墨烯增强铜基复合材料的制备工艺与综合性能,重点讨论了各种制备工艺的特点、强化机制、构型设计,总结了针对复合界面结合弱与石墨烯分散困难这2类主要技术难点的解决途径,最后对石墨烯增强铜基复合材料的制备工艺进行了展望。
1、 制备工艺
1.1 粉末冶金法
粉末冶金法是将石墨烯粉与铜粉通过球磨等方式混合,然后经过压制与烧结进行致密化而获得石墨烯增强铜基复合材料(Gr/Cu复合材料)的一种方法,其原理如图1所示。
SALVO 等通过球磨将石墨烯纳米片(GNSs)与铜粉混合,再通过真空热压烧结制备了GNSs/Cu复合材料;在球磨过程中石墨烯的润滑作用使得铜粉冷焊倾向减小,粉末颗粒形状趋于扁平细小,烧结后石墨烯分布于铜基体晶界处,在一定烧结压力下适当降低烧结温度有利于提高复合材料的力学性能和导电性。充分混料并烧结后制备的块体复合材料可通过塑性变形加工,进一步降低复合材料孔隙率,实现完全致密化,改善增强体分布状况并细化晶粒。WANG等采用片状粉末冶金工艺与轧制变形相结合的方法制备出GNSs/Cu复合材料带材,发现片状粉末冶金工艺中的球磨可以有效将石墨片剥离为石墨烯,并与二维片状铜粉结合良好,轧制后石墨烯在基体中分散良好,复合材料截面呈有序片层堆叠状结构,其抗拉强度达330MPa,并拥有极高的弹性模量(170GPa)与优良的抗弯曲能力。
粉末冶金法作为石墨烯增强铜基复合材料最为成熟的制备工艺,对基体粉末与增强体的含量、尺寸、形状等基本没有限制,具有较高的可设计性,但混料过程易破坏石墨烯结构的完整性,降低石墨烯的强化效果。
1.2 分子级水平混合法
分子级水平混合法通过将氧化石墨烯(GO)与铜氨等含有Cu2+的溶液混合,使Cu2+吸附到GO表面,并在还原气氛下高温还原或使用水合肼(分子式N2H4·H2O)等强还原剂还原,得到还原氧化石墨烯(rGO)与铜的复合粉体,其原理如图2所示;再经烧结后制得石墨烯增强铜基复合材料。
ZHANG等以石墨烯纳米微片(GNPs)和GO为碳源,通过分子级水平混合法制备了GNPs/Cu、rGO/Cu和镀镍的GNPs-Ni/Cu 3种复合材料,发现:GNPs与铜基体界面处存在机械与冶金结合;GNPs-Ni与铜基体间存在铜镍过渡层,使复合材料具有更高的负载能力,抗拉强度达281MPa,高于镀镍前的256MPa;rGO与铜基体界面处为富氧区域,二者形成了化学键合,改善了界面结合情况,复合材料的抗拉强度为278MPa,并拥有与纯铜相当的塑性。分子级水平混合法的优点在于铜以离子形态吸附在GO表面,能有效防止团聚发生。WANG等通过在溶液中引入高剪切混合过程,进一步降低了石墨烯的团聚倾向,石墨烯在基体中分布更为均匀,并且得到的复合粉体粒径更小,因此复合材料的力学性能显著提升。YANG等研究发现,溶液酸碱度与温度能够很大程度影响复合粉体的微观结构,铜在酸性环境下以片状Cu2(OH)3Ac的形式存在,在碱性环境时生成Cu(OH)2以及CuO纳米纤维,在低温高剪切的作用下不稳定的片状复合微板开始堆叠组装形成微层结构,所制备的复合材料抗拉强度高达748MPa。综上,分子级水平混合法可使石墨烯在溶液中具有良好的分散性,所制备出的复合材料界面结合强度较高。
1.3 化学气相沉积法
化学气相沉积法是以聚甲基丙烯酸甲酯(PMMA)或甲烷等含碳有机物为碳源,在一定反应条件下直接在基体金属表面生成石墨烯从而得到复合粉体或石墨烯薄膜,再经烧结制得复合材料的工艺,其原理如图3所示。
WANG等采用化学气相沉积法以甲烷为碳源在铜粉表面生长石墨烯,该工艺下石墨烯可将铜粉完全覆盖,有效防止铜颗粒氧化,烧结制备的复合材料硬度较纯铜有显著提高,并且具有与纯铜相近的电阻率,同时石墨烯的表面润滑作用使得复合材料具有良好的耐磨性能。通过化学气相沉积法生成的石墨烯与铜粉体之间具有典型的包覆结构,另引入球磨破坏包覆结构后制备复合材料的抗拉强度较破坏前提高了52.3%,其断裂伸长率达35.2%,同时具有较高的电导率;与包覆结构相比,非包覆结构更有利于粉体在烧结时的扩散,在粉体间形成较强的结合,从而使复合材料获得较优的力学性能。
通过调控化学气相沉积法的沉积参数可制备出层数可控的高质量石墨烯增强体,该石墨烯二维平面尺寸大并且与基体金属结合良好,有利于使复合材料获得较高的导电、导热性能;但该工艺流程繁琐,使用设备较为昂贵。
1.4 电化学沉积法
电化学沉积法是通过施加电流使沉积液中的石墨烯与铜在阴极金属表面沉积得到复合粉体颗粒,如图4所示,再经过洗涤、干燥、还原与烧结制备复合材料的工艺。
ZHAO等在采用电化学沉积法制备石墨烯增强铜基复合材料的过程中发现:随着硫酸镍与硫酸铜混合沉积液中石墨烯含量的增加,复合粉体中的铜颗粒尺寸、石墨烯厚度以及沉积液电导率均呈先减小后增大的趋势;Cu2+吸附在石墨烯表面可以阻碍石墨烯的增厚与团聚,石墨烯添加过量则会使沉积液电导率降低,从而导致复合粉体颗粒沉积效率的下降;在沉积过程中镍粒子被有效嵌入石墨烯中,促进了石墨烯与铜的结合,并存在(111)Cu//(1010)石墨烯与(222)Ni//(1010)石墨烯的取向关系;石墨烯与铜界面处存在Cu-O-C的键合,可显著提高复合材料的硬度,当石墨烯质量分数为11.8%时,其硬度可达111.2HV,导电率为89.2%IACS。电化学沉积法更适合制备力、电学性能俱佳的复合材料箔材。SONG等采用电化学沉积法通过改变沉积电位在预先制备好的GO薄膜上下两侧沉积铜层,在沉积过程中GO还原成石墨烯从而形成复合箔材;石墨烯与铜箔结合紧密,撕裂断口呈锯齿状,抗拉强度(535MPa)可达铜箔的2倍,导电性能与铜箔相当。
电化学沉积法制备过程简单可控,设备成本低,制备过程中复合材料界面处铜晶格中的间隙氧原子通过共价键或离子键与铜相结合,提高了复合材料的力学性能,但石墨烯悬浮液稳定性较差的问题尚待解决。
1.5 静电自组装法
静电自组装法使用十六烷基三甲基溴化铵(CTAB)在片状铜粉表面引入正电荷,再通过超声处理与GO溶液混合,二者在电荷作用下相互吸附形成复合浆料,再经干燥、还原、烧结制备得到复合材料,其原理如图5所示。
ZHANG等研究发现,CTAB改性促进了Cu2O的形成,并在复合界面处搭建起了Cu-Cu2O-rGO的结构,延缓了复合材料在外力作用下发生断裂的过程,载荷可以有效从基体铜向石墨烯传递,从而提高复合材料的强度。SHAO等结合化学镀与静电自组装法制备了GNPs/Cu复合材料,发现在石墨烯表面化学镀铜能有效改善石墨烯与铜的润湿性,片状铜粉颗粒较球状铜粉颗粒具有更好的几何匹配度,有利于石墨烯的吸附与均匀分散。静电自组装法能够在对石墨烯结构不造成破坏的情况下完成石墨烯与铜的吸附结合,有利于改善石墨烯在基体中的分散情况。
1.6 变形复合法
变形复合法是通过对复合坯料进行高变形量的塑性变形,如累积叠轧、高压扭转等,利用变形力的作用完成复合材料的致密化并细化晶粒的一种工艺。
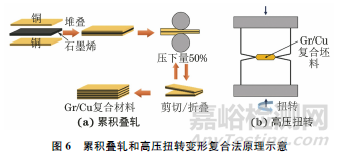
CHEN等通过累积叠轧方法对复合坯料施加高周期的塑性变形,使得石墨箔在强剪应力作用下原位剥离分层为石墨烯,并分散在铜基体中,所制备的复合材料硬度与抗拉强度均达到退火纯铜的3倍以上,原位剥离形成的石墨烯对复合材料的强度贡献极高,并与基体形成了较强的界面结合。KIM等以等速常规轧制与高速率差速轧制的组合工艺获得了高度致密的石墨烯/铜复合板料,在差速轧制剪切力的作用下基体中的石墨烯发生碎裂,形成纳米石墨烯颗粒并均匀分散在基体中。KORZNIKOVA等探索了采用高压扭转方式制备块体石墨烯/铜复合材料的工艺,经过限定与非限定型两步法高压扭转变形后的复合材料的硬度与纯铜相比显著提高,并且形成了心部硬度低、边缘硬度高的梯度分布;在扭转过程中石墨烯得到细化并分散在晶界处形成钉扎作用,复合材料脆性断裂特征明显,表现出类似陶瓷材料的超高硬度、低强度与低塑性的特征。
变形复合法可使复合材料中的孔隙闭合消失,晶粒显著细化,在变形力的作用下石墨烯片发生剥离、破碎,使石墨烯与铜基体之间的机械结合得到增强,提高了载荷的传递能力,在牺牲一定塑性的前提下大幅提升复合材料的强度。
1.7 其他制备方法
除上述制备工艺外,电泳沉积法、搅拌摩擦法、喷涂法等也常用于制备石墨烯增强铜基复合材料。SINGH等通过电泳沉积法在极间电场的作用下使石墨烯在溶液中产生定向移动并在铜板表面沉积形成致密均匀的薄膜,提高了铜板表面的耐腐蚀性能。NAIK等通过搅拌摩擦的方式制备了石墨烯增强铜基复合材料,在搅拌摩擦的作用下石墨烯被分散到基体表面层中,搅拌区发生再结晶,晶粒尺寸细化幅度达94%以上,复合材料硬度得到了提高,同时导电率保持在97%IACS以上。CHOI等通过化学气相沉积法在铜颗粒表面制备了石墨烯层,再用冷喷涂技术沉积了石墨烯/铜复合层,石墨烯结构损伤程度较低,有效降低了铜表面的摩擦因数与磨损率。为实现高自由度的复合材料构型设计,不少学者采用模板法制备出继承模板结构的三维网络增强体或多孔基体,再通过浸渗铜或原位生成石墨烯进行填充来制备复合材料。管振宏等使用纳米多孔铜为基体制备了石墨烯增强铜基复合材料,石墨烯网络的生成使复合材料的抗拉强度较纯铜提升了34.69%,并保持了93.5%IACS的高导电率。
2、 综合性能与强韧化
2.1 力学性能
寻求材料强度的大幅度提升是石墨烯增强铜基复合材料的主要研究方向,表1列举了采用不同工艺制备的石墨烯增强铜基复合材料的力学性能参数。复合材料的力学性能随不同制备工艺有不同程度的提升,其中:分子级水平混合法、湿法混合、静电自组装法等对石墨烯结构损伤小,石墨烯的分散效果好,所制备复合材料的力学性能优异;差速轧制等塑性变形工艺有利于破碎并分散基体中的石墨烯,通过强烈的位错钉扎与细晶强化获得具有高强度、较低塑性的块体材料;模板辅助原位合成法以及片状粉末冶金工艺则通过复合材料组织构型设计,形成三维石墨烯网络与层状结构,使复合材料的强度得到进一步提高。石墨烯的添加能有效细化晶粒、阻碍位错运动,达到提高强度的目的;添加石墨烯对于屈服强度的提升效果较为明显,赋予复合材料较高的屈强比;石墨烯或其衍生物的本征参数,如平面尺寸、层数等以及石墨烯的质量及其在基体中的分散情况、界面结合情况都是影响复合材料力学性能的重要因素,一般石墨烯层数越少、结构损伤越小,则强化效果越好,同时小的平面尺寸有利于实现石墨烯在基体中的均匀分散,从而提高复合材料力学性能。研究表明,在变形过程中剪切行为除了发生在界面处,还可能发生在石墨烯的层间,而带有空位型缺陷的石墨烯在剪切变形中表现出较强的剪切应变协调能力,使复合材料的强度与韧性得到提升;同时石墨烯因范德华力作用易于团聚、堆叠,团聚后的石墨烯所发挥的强化作用十分有限,并且会削弱复合材料的界面强度,使界面在外加载荷作用下易发生脱落并产生裂纹,最终导致复合材料力学性能的大幅度下降。
表1 不同工艺制备得到不同石墨烯增强铜基复合材料的力学性能
2.2 强韧化
2.2.1 强化机制
石墨烯在基体中的强化机制包括载荷转移强化、细晶强化、热失配强化与Orowan强化四大类。载荷转移强化是指当复合材料受力时,载荷将通过界面被直接传递到石墨烯增强体上,使得复合材料的整体强度提高;该机制是复合材料最主要的强化机制,对复合材料强度提升的贡献占比可达30%以上。复合材料屈服强度σs与基体材料屈服强度σsm的关系可采用修正后的shear-lag模型表示:
细晶强化是指在金属中引入石墨烯,诱导晶粒细化从而提升复合材料强度。不同制备工艺对于基体晶粒细化程度的影响不同,如粉末冶金法、电化学沉积法均能实现石墨烯在晶界处钉扎从而阻碍晶粒长大。所制备的复合材料的屈服强度与晶粒尺寸之间满足Hall-Petch关系:
热失配强化是指复合材料在烧结或热加工过程中因基体与石墨烯热膨胀系数不匹配而发生局部塑性变形,在石墨烯周围产生较高位错密度的区域来阻碍位错运动的一种强化机制。热失配强化效果ΔσCET的表达式为:
Orowan强化是指由于石墨烯对铜基体的物理分隔阻碍了位错运动,使位错在石墨烯附近堆积分布,从而提高材料强度的一种强化机制。要使Orowan强化充分发挥作用,需要增强体尺寸为纳米或亚微米级,并且分布在晶粒内部以限制晶内位错移动,但石墨烯一般分布于晶界处,因此Orowan强化对于复合材料强度的提升作用较小。Orowan强化带来的强度提升ΔσOrowan可由Orowan-Ashby公式表示:
2.2.2 构型设计
通过增强体结构改进与复合材料构型设计可以进一步实现复合材料的强韧化。YANG等将多壁碳纳米管剪切展开制备了近一维的石墨烯纳米带(GNRs),采用放电等离子烧结制得石墨烯增强铜基复合材料;经过轧制后组织中的纳米带与轧制方向平行,大角度晶界和孪晶的数量都明显高于纯铜,复合材料具有较高的应变硬化率与均匀延伸率。同时,受叶片结构的启发,将多壁碳纳米管外壁部分展开得到以中心碳纳米管为脉、展开石墨烯纳米带为叶的仿生叶片状复合增强体,该结构有助于提升载荷转移效率,同时加剧变形的能量消耗,模拟结果表明纳米带部分所承受的载荷比脉部高出约10%。
在组织结构设计的探索方面,目前主要有仿生珍珠层状结构、三维石墨烯增强体网络结构、石墨烯定向排列结构等。XIONG等制备了仿杉木的多孔状铜预制件,再通过石墨烯溶液浸渍预制件的方式,实现了仿生珍珠层状复合材料的制备;通过石墨烯的拔出机制以及模仿珍珠贝所具有的“砖-泥”结构,使裂纹在材料层间偏转来增加材料破坏时能量的耗散,复合材料断裂时所需的能量可达相同工艺纯铜的1.8倍,其韧性得到显著增强。CHEN等以PMMA为碳源,通过化学气相沉积法在铜粉上生长石墨烯并使其保留了基底铜粉的形貌,从而制备了具有连续三维石墨烯网络的复合材料,其屈服强度为290MPa,较纯铜提高了233.3%,增强体强化效率达116.1,该方法适用于制备各向同性的块体材料。ZHANG等通过铜粒子修饰石墨烯并采用原位合成方法制备了具有非连续的三维石墨烯网络结构的铜基复合材料;与连续网络结构复合材料相比,该复合材料的晶粒细化效果更明显,石墨烯的弥散分布造成的强度提升效果更为显著,断裂总延伸率较纯铜提升了近40%。ZHANG等还在非连续石墨烯网络结构基础上进一步添加碳纳米管,制备出由铜颗粒、碳纳米管与石墨烯组成的混合增强体,进一步强化了载荷转移与晶粒细化效果。CHU等则采用真空抽滤法制备了GNPs/Cu复合薄片,使基体中的石墨烯具有高度取向,复合材料力学性能表现出显著的各向异性,复合材料在平行于石墨烯面内方向的强度达到垂直方向的2倍左右。轧制变形与热压烧结都有助于实现石墨烯的定向排列;复合材料在平行于排列方向的力学性能显著高于垂直方向。
2.3 导电和导热性能
石墨烯具有远高于金属铜的导电、导热性能,可以作为功能性增强体以进一步提高材料的综合性能,表2给出已有报道中不同石墨烯增强铜基复合材料的导电和导热性能参数。采用化学气相沉积方法制备的复合材料具有较优异的导电和导热性能,这是由于化学气相沉积法制备的石墨烯缺陷少,二维平面尺寸大,有利于电子的传输。石墨烯面内与层间热导率具有极大差异,通过真空抽滤制备的复合材料中石墨烯具有高度的取向,能充分发挥石墨烯面内高热导率的特点,使复合材料在特定方向获得较优异的导热性能。
表2 不同工艺制备得到不同石墨烯增强铜基复合材料的导电和导热性能
石墨烯与铜之间的界面是影响复合材料导电、导热性能的关键。与金属依靠电子导热不同,石墨烯的导热载体为声子;石墨烯与铜的非相干界面会减小声子的平均自由程并影响电子的传输。由于石墨烯易团聚且与基体间润湿性差,复合界面处会形成纳米孔洞,影响电子与声子的传导,导致复合材料的导电、导热性能大大降低。LI等采用4-乙炔基苯胺对石墨烯进行功能化处理,成功在石墨烯/铜界面上建立了离域共轭π键,形成了新的电子传热路径,赋予复合材料优异的导热性能,在100℃时的热导率可达497W·m-1·K-1,为纯铜的1.61倍。YANG等通过化学气相沉积法制备了石墨烯平行分布的铜基复合材料,通过调整石墨烯层数控制材料热导率各向异性,在石墨烯层数为5~6层时的热导率可达394W·m-1·K-1。LEE等受海星表面结构的启发,制备了海星表面状石墨烯-铜微粒,使材料内部构建了垂直散热网络,极大提高了复合材料的垂直热导率。QIAN等通过浸渍还原与原位生长法在GNPs/Cu复合界面处插入了低含量的稀土元素,生成的氧化钇牢固嵌入到石墨烯片上,界面处微量的氧化钇改善了GNPs/Cu的界面结合,使复合材料导电率从纯铜的84.5%IACS上升到90%IACS。
基体金属取向对复合材料导电、导热性能的影响也是至关重要的。研究表明:采用化学气相沉积法在铜箔上沉积石墨烯并堆叠烧结为具有微米/纳米层状结构的复合材料,有利于改善石墨烯在基体中的取向性,由于石墨烯的二维特征,复合材料沿石墨烯/铜界面方向获得了较高的导电性;与多晶铜箔相比,采用单晶(111)铜箔作为基体制备的复合材料具有较优异的电子传输能力。
3、 制备技术难点及解决措施
3.1 石墨烯的分散性
石墨烯的比表面积大,表面能高,易在溶液中团聚,使其强化效果发挥不完全,严重影响复合材料的综合性能。为解决这一问题,制备中常用带有含氧基团的GO,其良好的亲水性能提高石墨烯在溶液中的分散性。但在制备GO过程中,石墨烯的本征结构会受到破坏,导致其强化效果下降,且后续的还原工艺无法彻底消除由制备过程引入的缺陷。除了上述方法,还可通过对石墨烯进行表面纳米粒子修饰、改良混料过程来提高石墨烯分散性或用静电自组装法、分子级水平混合法等有利于改善石墨烯分散性的制备工艺。
TANG等以GNSs-Ni复合粉为增强体,采用放电等离子烧结制备了复合材料,镍粒子可作为间隔颗粒阻碍石墨烯团聚。ZHAO等则采用化学镀铜的方法改善GNPs在复合材料中的分散情况,从而制备出力学性能优异的复合材料。SABOORI等研究发现,湿法混合后石墨烯均匀分布于基体晶粒的晶界处,引起晶粒细化,同时石墨烯的结构在混料前后基本没有变化,而球磨会使石墨烯中引入大量结构缺陷,因此湿法混合更适用于复合材料的制备。对有石墨烯的溶液体系进行超声处理,借助超声空化效应产生的冲击波与剪切力可使团聚在一起的石墨烯分散开来;超声功率越大,分散效果越好,但同时也容易使石墨烯表面产生空位缺陷。除此之外,还可通过在溶液中添加如CTAB、十二烷基硫酸钠(SDS)、十二烷基苯磺酸钠(SDBS)等表面活性剂来改善石墨烯在溶液中的分散性。采用静电自组装法、分子水平混合法等制备工艺,依靠电荷作用与金属粒子阻隔的方式也可有效改善石墨烯在基体中的团聚倾向。
3.2 石墨烯与铜的界面结合情况
石墨烯与铜之间的润湿性较差,难以形成强界面结合,导致载荷转移强化效果减弱。当界面结合较弱时,界面易在载荷作用下先开裂并破坏材料内部组织连续性,使材料综合性能下降。大多数制备工艺通过单一的烧结完成材料的致密化,石墨烯与铜之间形成单纯的机械结合。目前主要采用基体合金化、石墨烯表面处理或化学气相沉积法、变形复合法等制备工艺来提高界面结合强度。
基体合金化一般利用合金与石墨烯在界面处形成的新过渡层来改善界面结合情况,提高载荷传递的能力。CHU等在铜基体中加入原子分数约0.2%的铬后,rGO/CuCr界面处原位形成了Cr7C3的中间层,提高了载荷传递的效率,增强了石墨烯的钉扎作用。LUO等制备了Ag-rGO增强体,通过纳米银粒子修饰石墨烯的方式改善了石墨烯与铜基体的界面结合情况,所制备复合材料的导电、导热性能均有明显提高。采用金属粒子修饰石墨烯时,要求所用的金属粒子与石墨烯、铜之间均具有良好的润湿性,因此常采用与铜可形成固溶体的镍与银粒子。但是基体合金化与纳米粒子修饰在改善复合材料界面结合情况的同时,会影响电子、声子的传输,因此仅允许添加少量的合金元素与修饰粒子。CHU等将石墨烯进行等离子体处理。使石墨烯表面产生若干直径为5~10nm的孔洞,烧结时孔洞处原位生成铜氧化物,从而改善石墨烯与基体的界面结合情况,提升了复合材料的力学性能。使用聚乙烯醇(PVA)对铜粉进行化学改性,GO上的含氧基团与铜粉上PVA分子所带的-OH有较强的结合力;以PVA分子为中间桥梁连接铜粉与石墨烯,可以实现良好的界面结合。参考化学气相沉积法与变形复合法,可采用在基体上直接生长增强体的方式或引入轧制、挤压、扭转等变形方法有效增强界面处的机械结合。
4、 结束语
将石墨烯应用于制备金属基复合材料有望实现金属材料综合性能的全面提升,有助于金属材料应用领域的拓宽,满足日趋严苛的性能要求。目前,石墨烯增强铜基复合材料的实际性能均低于理论预测数值,并且存在较大的差距,其原因包括:(1)石墨烯在球磨、酸洗氧化、超声处理等过程中易发生结构损伤,导致本征强度降低,强化效果弱化;(2)石墨烯易发生团聚,现有的分散方法主要为机械分散方法,如超声处理、机械球磨等,在溶液环境中添加表面活性剂虽有助于石墨烯的分散与悬浮液的稳定,但活性剂的添加将会影响界面的结合强度;(3)石墨烯与铜的润湿性较差,现有工艺制备的复合材料在石墨烯/铜界面处的结合依然以结合强度较差的机械结合为主;(4)石墨烯具有显著的各向异性,面内与层间的性能截然不同,制备的复合材料中石墨烯分布常呈现混乱无序的状态,无法完全发挥石墨烯的强化效果。
针对目前存在的问题,考虑到现有的制备工艺,未来还需进一步改善石墨烯的分散工艺,保证石墨烯的结构完整,并通过在石墨烯/铜界面处引入较多的反应类型键合,以改善因润湿性差而造成的低界面强度,同时应避免反应过程中极脆相的生成所造成的材料塑韧性的大幅下降。在构型方面,应参照自然界中的高强韧结构进行构型设计,从粗犷的结构模仿逐步向精细的强化机理模仿转变,尽可能地将自然结构的强化效应在复合材料中复现,进一步提高复合材料的性能。
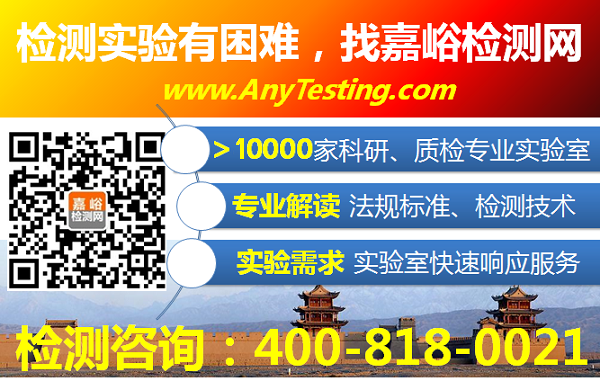