质量源于设计(Quality by Design),缩写为QbD。QbD概念应用于药物研发,最早是在2004年由美国FDA提出[1],后来用到人用药品注册技术要求国际协调会(ICH)质量体系中并成为指导原则和指南。ICH质量体系中Q8(药物研发)、Q9(质量风险管理)和Q10(药物质量系统)贯穿于小试研发、工艺开发和生产管理。
一、QbD定义
根据ICH Q8对QbD的定义我们可以知道:是一种系统的研发方法,其以预先设定目标为起始,基于可靠的科学和质量风险管理,强调对目标产品和生产过程的理解及对工艺的控制[2]。
二、QbD的关键要素
图1 QbD的关键要素[3]
如图1所示,QbD理念包括目标产品质量概况(QTPP)、关键质量属性(CQA)、关键物质属性(CMA)、关键工艺参数(CPP)、设计空间(Design Space)、风险评估(Risk Assessment)和控制策略(Control Strategy)等关键要素。
三、QbD的关键要素的关系
根据QbD关键要素中的定义,关键工艺参数(CPP)和关键物料属性(CMA)的波动或变化对目标产品的关键质量属性(CQAs)有显著影响。
关系示意图如图2所示,其基本内容为:以预先设定的目标产品质量概况(QTPP)作为研发的起点,在确定产品关键质量属性(CQA)基础上,基于风险评估和试验研究,确定关键物料属性(CMA)和关键工艺参数(CPP),进而建立能满足产品性能且工艺稳健的控制策略,并实施产品和工艺生命周期管理(包括持续改进)[4]。
图2 CMA、CPP与CQAs关系示意图[5]
CPP和CMA的确定是多方面、系统综合的评估研究结论,仅基于风险评估的结论是不够充分的,通常需要结合经验知识和一些测量或实验工具/方法加以验证确认。试验模拟和实验设计(DOE)是分析评估并确认CPP和CMA的有效方法和核心工具。
四、QbD应用的案例
天津生物工程职业技术学院陈静[6]通过DOE的方法进行试验设计,以期寻找出提高原料转化率,减少杂质生成的最优工艺,更好的应用于工业化大生产,生产出成本低廉、优质的药品。
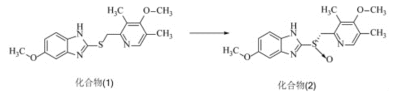
化合物(2)为S-奥美拉唑,其是由原来化合物(1)通过一步氧化反应制备,本步反应中存在的主要问题是化合物1反应不完全,以及以下氧化杂质较大,不易除去,从而严重影响产品质量。
化合物(2)合成,采用DOE设计10组不同投料比的进行投料,分别以监控反应2h后的杂质生成量及原料剩余量为指标,HPLC结果见表1。
表1 DOE设计10组实验的HPLC结果
经过DOE软件分析(等值线图)可以确定的配比为化合物(1):D酒石酸二乙酯∶钛酸异丙酯∶N,N-二异丙基乙胺∶过氧化氢异丙苯∶纯化水=1.0∶1.10∶0.55∶1.13∶1.37∶0.33。通过优化后的实验进一步验证了该投料比反应液中氧化杂质的产生明显减小,降低了反应液中氧化杂质大的风险,同时使原料反应更彻底,可以极好的降低成本,提高转化率及收率,更有利于工业化大生产。
2022年,David H. Thompson等[7]人通过实验设计和高通量研究指导N-视黄亚基-N-视黄基乙醇胺(A2E)(如图3所示)连续流动合成。
图3 A2E的合成路线图
通过用实验设计(DoE)和高通量方法重新优化了A2E的合成,旨在确定变量(温度、溶剂和试剂当量)的最佳组合,以优化A2E产量。他们的DoE结果分析表明,乙醇胺与乙酸和ATR的相互作用对于高产率A2E的形成至关重要,表明亚胺的形成是反应中的关键步骤。有了这些DoE的结果,他们能够使用微流体反应器系统优化方法,然后再扩大这些条件以进行A2E的连续流动合成。这种改进的方法使材料生产更加高效,从48小时的反应时间到33分钟的停留时间,同时产量从49%提高到78%。
当然,对这方面感兴趣,或者想了解更多案例的朋友可以在Organic Process Research & Development期刊搜索Quality by Design。
五、QbD小结
尽管21世纪初,在美国FDA的推动下,QbD的概念开始成为制药行业关注的热点,但这方面国内依然薄弱,更多的研发人员还是采用先前的那套理论方法进行药物工艺研究,甚至一些药物研发人员并没有听过QbD的概念。
根据QbD的概念药品从研发开始就要考虑最终产品的质量。在配方设计、工艺路线确定、工艺参数选择、物料控制等各个方面都要进行深入地研究,积累翔实的数据,在透彻理解的基础上确定最佳的产品配方和生产工艺。
再往细点说,QbD是非常适合于原料药工艺开发的。因为,原料药工艺开发的目的是通过科学合理的方法,建立能够持续生产出预期质量的工业化生产工艺。QbD理念强调要制定目标,即在原料药工艺开发的早期环节,就强调质量控制需在可靠的科学和风险的管理基础上,对产品和工艺具有深刻的理解并加以控制,是一个系统的药物开发方法[8]。我个人是赞同王春山先生说的那句话,QbD理念应用于原料药的工艺开发,必将为原料药工艺开发的整个过程提供更加充分、科学、有针对性的方法和理论指导[3]。
参考文献
[1]WEISSMAN S A, ANDERSON N G. Design of Experiments (DoE) and Process Optimization. A Review of Recent Publications[J]. Organic Process Research & Development, 2015, 19(11):1605-1633.
[2]METIL D S, SONAWANE S P, PACHORE S S, et al. Synthesis and Optimization of Canagliflozin by Employing Quality by Design (QbD) Principles[J]. Organic Process Research & Development, 2018, 22(1):27-39.
[3]王春山. 基于质量源于设计(QbD)理念的原料药工艺开发思路和方法[J]. 化工与医药工程, 2021, 42(06):30-33.
[4]郭六一. 基于质量源于设计理念的非洛地平片一致性评价研究[D]. 浙江大学, 2020.
[5]王明娟, 胡晓茹, 戴忠, et al. 新型的药品质量管理理念“质量源于设计”[J]. 中国新药杂志, 2014, 23(08):948-954.
[6]陈静. DOE(试验设计)在原料药工艺优化中的应用[J]. 天津化工, 2021, 35(03):61-63.
[7]MURBACH-OLIVEIRA G, BANERJEE K, NOCIARI M M, et al. Continuous Flow Synthesis of A2E Guided by Design of Experiments and High-Throughput Studies[J]. ACS Bio & Med Chem Au, 2022, 2(3):297-306.
[8]刘理文. QbD在仿制药工程的应用路径设计[D]. 厦门大学, 2014.
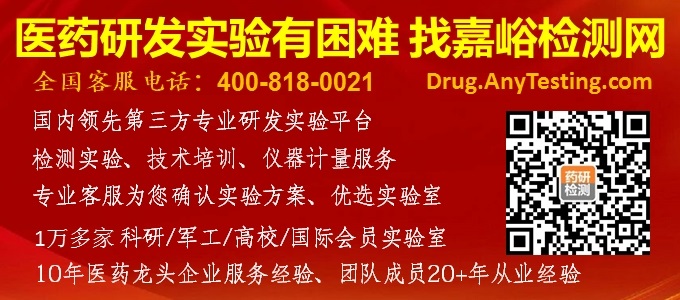