采用等离子喷涂技术在发动机活塞用ZL109铝合金表面制备Ni60CuMo合金涂层,研究了涂层的微观形貌、物相组成、显微硬度以及不同条件下的耐磨性能。结果表明:涂层由富铬区和富镍区交替重叠构成,与基体间的结合方式为机械结合;涂层的孔隙率为2.48%,平均显微硬度为792.91HV,约为基体的6倍以上;随试验温度由25℃升高至450℃,涂层的摩擦因数和磨损质量损失均降低,450℃油润滑下涂层的平均摩擦因数为0.037,磨损质量损失为7.35mg,仅为基体的1/4左右;随试验温度的升高,干摩擦下涂层的磨损机制由剥落失效转变为氧化磨损与黏着磨损,油润滑下由磨粒磨损转变为磨粒磨损和黏着磨损,最后转变为黏着磨损。
PART 01
试样制备与试验方法
基体材料选用铸态ZL109铝合金,涂层原料粉选用Ni60CuMo合金粉末,平均粒径约为95μm,微观形貌如图1所示,可知颗粒的形貌近似球形。对基体进行超声清洗,再进行喷砂处理后,采用等离子喷涂设备在其表面制备Ni60CuMo合金涂层,以氩气作为主要保护气体,氢气作为次要保护气体,基于前期工作得到等离子喷涂工艺参数进行探究。
采用扫描电子显微镜(SEM)观察涂层的表面和截面微观形貌,并用SEM附带能谱仪(EDS)进行微区成分分析。利用单晶X射线衍射仪(XRD)对粉体与涂层的物相组成进行分析。采用数显显微硬度仪测涂层的截面显微硬度分布。在800倍放大倍数下随机选取5张涂层SEM截面图像,并对涂层截面孔隙进行灰度处理,用ImageJ2x图像处理软件计算孔隙率。在涂层试样上截取尺寸为20mm×10mm×5mm的磨损试样,经400# 、600# 、800# 、1000#的碳化硅砂纸依次打磨处理,并用酒精超声清洗后,选用高温摩擦磨损试验机对涂层进行圆环式滑动磨损试验,接触形式为点接触,对磨件为直径5mm的GCr15钢球,磨损载荷为50N,转速为200 r·min-1,磨损时间为20min,磨损半径为1.5mm;由于活塞服役于高温、贫/富油状态下,最高服役温度在326~426℃间,因此选用温度区间内的375℃,室温(25℃)及苛刻服役温度450℃作为涂层磨损试验温度,具体润滑条件和试验温度如表1所示,润滑油选用汽油机油,相同试验条件下进行2次平行试验,使用电子天平对磨损前后试样的质量进行称量,计算磨损质量损失。选用三维形貌仪对磨损后试样表面三维形貌进行观察,并采用扫描电镜观察磨损形貌。
表1 磨损试验的润滑条件和试验温度
PART 02
试验结果与讨论
2.1 微观形貌与物相组成
由图2可知:所制备涂层表面熔滴铺展状况良好,熔融粒子撞击至基体表面后经堆垛、铺展后以放射形式、破碎形式凝固,部分熔滴包裹着未熔颗粒,而这些未熔颗粒表面熔滴的冷却凝固使颗粒间相互结合从而形成典型层状结构的涂层;由于部分未熔颗粒堆叠,后续的熔融粒子未能完全润湿填充这些不规则区域,从而在涂层内部形成孔隙。基体与涂层界面处结合较致密,涂层厚度约为300μm,高倍下观察发现涂层内部由2种颜色(深灰色、浅灰色)区域交替重叠构成,经EDS分析发现深灰色区域为富铬区,浅灰色区域为富镍区。由EDS分析发现涂层截面无明显的元素扩散现象,因此涂层与基体间的结合方式为机械结合;同时选区中未检测出氧元素,说明在熔滴飞行过程中未出现氧化现象,工作气体对熔滴起到了良好的保护作用。涂层保留了原料粉末的物相组成,均主要由γ-(Ni,Cr,Fe,Cu)固溶体、FeNi3、Cr7C3、Cr23C6、Mo2C、MoSi2、Fe2Mo等组成。
图3为涂层截面孔隙形貌及对应的灰度图,统计得到涂层的平均孔隙率为2.48%。涂层中孔隙形态多样,除了分布广泛的独立闭合微孔外,还有少量由多个微孔交互连通的通孔。由于喷涂时熔滴包裹未熔颗粒周围,其堆积和搭接具有随机性,因此涂层中极易出现因填充不充分而形成的孔隙聚集现象。
2.2 硬度分布
由图4可知,涂层截面显微硬度呈小范围波动,其中最高硬度可达874HV,最低硬度为735HV,平均硬度为792.91HV,基体的平均硬度约为123HV,涂层的硬度为基体的6倍以上。在涂层中分富镍区与富铬区,富铬区分布不均匀,硬度测试时压痕的随机性使得显微硬度出现波动。在施加载荷初期,压痕处孔隙等微缺陷处产生应力集中而出现裂纹,在压应力作用下压痕长度增加,因此硬度较小。涂层的孔隙等微缺陷主要集中在涂层中间部分,因此中间部分的硬度较低。在粒子撞击的夯实作用下涂层近表层处的加工硬化效果增强,因此显微硬度较高。
2.3 摩擦磨损性能
由图5可知:在不同润滑条件下涂层在试验前期0~150s时间内的摩擦因数急剧增加并随之在短时间内达到平稳状态,而后又出现波动现象,其中干摩擦条件下涂层的摩擦因数较大,且波动较大,这是因为此时涂层与对磨件间无润滑液和保护膜,表面直接接触,磨损剧烈。随着试验温度由25℃升高至450℃,涂层的平均摩擦因数降低。油润滑条件下涂层的摩擦因数更加平稳,平均摩擦因数偏低,并且摩擦因数达到平稳阶段所需时间较短,短于100s,说明润滑油在涂层与对磨件之间形成的油膜起到了减摩耐磨的效果;油膜使涂层与对磨件表面分离,发生流体润滑,在压力作用下,部分润滑油进入涂层孔隙中起到了储油作用,为摩擦表面持续提供油膜所需的润滑油,使表面油膜不易破损;450℃时涂层的平均摩擦因数最低,表现出优异的减摩效果。
由图6可以看出:涂层的磨损质量损失随试验温度的升高和油润滑条件的施加而减小,而基体的磨损质量损失随试验温度升高而增大,但施加润滑油后磨损质量损失略微减小,对比发现施加润滑油后涂层耐磨性提升的程度比基体显著;相同试验温度和润滑条件下涂层的磨损质量损失明显低于基体,在450℃油润滑条件下涂层的磨损质量损失仅为7.35mg,为基体的1/4左右,说明涂层具有优异的耐磨性能。
由图7可以发现,在450℃油润滑条件下涂层磨痕的最大峰高为46.9μm,基体磨痕的最大峰高为155.7μm,涂层磨痕很浅,进一步说明涂层在高温下具有优异的耐磨性能。
由图8可知,在25℃干摩擦条件下涂层表面磨损严重,涂层剥落痕迹明显,并且因涂层内硬质相分布不均匀造成其表面磨痕较粗糙。当干摩擦条件下的试验温度升至375℃时,对表面磨损产生的零星分布的深灰色区域进行EDS分析后,发现该区域主要为铁的氧化物,由于涂层中铁含量较少,而经磨损后表面铁元素含量显著增加,说明磨损过程中涂层表面与对磨件出现了材料转移,随磨损时间延长,转移的材料逐渐积聚而形成含铁氧化物转移层;虽然该转移层能够在一定程度上缓解涂层的磨损,但由于氧化物在硬度高的同时,其脆性也较大,在高温下的相对切向运动中易使涂层发生断裂,转移层也会出现剪切断裂,从而在涂层磨损表面出现氧化物剥落的痕迹以及因切向应力作用而形成的垂直于摩擦方向的微裂纹。随着干摩擦条件下的试验温度升高至450℃,磨损表面转移层面积较大,垂直于滑动方向的裂纹宽度减小,因转移层的磨损而在涂层表面形成碎屑。氧化物转移层的形成说明在高温干摩擦下涂层表现出黏着磨损与氧化磨损的复合特征。
在油润滑条件下涂层表面的磨损程度较轻,在25℃和375℃下磨损表面出现犁沟、划痕以及剥落颗粒损伤痕迹,在对磨件剪切应力循环作用下颗粒剥落,并在润滑油的包裹下以及对磨件施加的正应力作用下,对涂层表面进行研磨,起到了磨料的作用;375℃下磨损表面还出现了橘皮状氧化物碎片,这是由于在喷涂过程中部分熔滴动能不足而撞击基体不充分,层间内聚力较差,在磨损中易发生片层状剥落,但对磨件部分正应力发挥的“夯实”效应使橘皮状氧化物碎片未彻底剥离于涂层表面。因此,在油润滑条件下25℃时涂层的磨损机制为磨粒磨损,而375℃下的磨损机制为磨粒磨损及黏着磨损。450℃时涂层磨损表面更加平整,没有明显的犁沟、划痕等磨粒磨损的痕迹,磨损程度最轻,此时涂层的磨损机制以黏着磨损为主。
PART 03
结 论
(1) 采用等离子喷涂技术在ZL109铝合金表面制备的Ni60CuMo合金涂层由富铬区和富镍区交替重叠构成,与基体间无明显的元素扩散现象,涂层与基体间的结合方式为机械结合;涂层的物相组成与Ni60CuMo合金粉末相同,主要由γ-(Ni,Cr,Fe,Cu)固溶体、FeNi3、Cr7C3、Cr23C6、Mo2C、MoSi2、Fe2Mo等组成;涂层结构致密,孔隙率为2.48%;涂层的平均显微硬度为792.91HV,为铝合金基体的6倍以上。
(2) 与干摩擦条件相比,油润滑条件下涂层具备更平稳的摩擦因数以及更低的磨损质量损失,且随试验温度的升高,摩擦因数和磨损质量损失均降低,耐磨性能更好;450℃油润滑条件下涂层的平均摩擦因数为0.037,磨损质量损失为7.35mg,仅为基体的1/4左右,涂层具有优异的耐磨性能。
(3) 干摩擦条件下25℃磨损时涂层出现剥落失效,375,450℃磨损时涂层磨损机制为氧化磨损与黏着磨损;油润滑条件下25℃磨损时涂层主要发生磨粒磨损,375℃磨损时的磨损机制为磨粒磨损及黏着磨损,450℃时涂层磨损表面平整,磨损机制以黏着磨损为主。
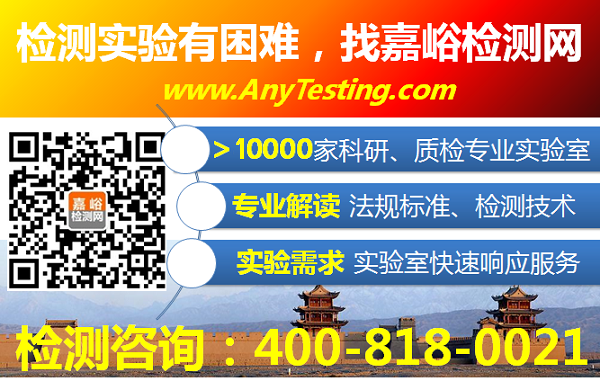