航空发动机作为航空飞行器的核心部件,其结构特别复杂,需要产生足够的动力支撑航空飞行器的飞行安全。航空发动机工作时主要靠涡轮叶片的旋转做功,涡轮叶片的正常运转对整个航空飞行器的安全至关重要。
由于长期工作在高温、高压、强烈气流冲击、巨大离心力环境下,涡轮叶片需具有高强度、高韧性、抗压能力,更重要的是能抗高温和高压。涡轮叶片的燃气温度从最初的1150 K增长至2000 K,高温引起的氧化腐蚀是叶片损伤的主要形式之一,为提高叶片的使用寿命,需要在叶片表面喷涂耐高温涂覆层。裂纹是涡轮叶片最致命的缺陷,如果不能及时检测出裂纹,将给航空飞行器带来极大的威胁。
目前,检测涡轮叶片缺陷主要采用传统的无损检测技术,例如射线检测、超声检测、渗透检测、涡流检测、目视检测等。射线检测一般用于叶片内部气孔、砂眼检测;超声检测一般用于锻造叶片的毛坯内部质量检测;渗透检测用于叶片表面裂纹的检测,型腔清洗不彻底会形成大量的荧光背景;目视检测仅能检测叶片表面缺陷。
综上可见,传统的无损检测技术对涡轮叶片裂纹检测存在不同程度的灵敏度低、检测周期长、操作过程复杂等局限,特别是当叶片形状复杂,裂纹细小,表面有涂层覆盖等情况时,检测就变得更加困难。
超声红外热成像技术一般应用于金属裂纹的检测。有研究表明,采用超声红外热成像技术可以有效检测出复杂型面叶片裂纹缺陷;对铝金属的疲劳微裂纹进行检测,可检出微裂纹最小宽度为20 μm;对航空发动机未喷涂前的叶片裂纹进行检测,最小检测裂纹宽度为0.5 μm。
1、超声红外热成像技术的检测原理
超声红外热成像检测过程包括超声波能量产生和传播、裂纹摩擦生热、能量热扩散、涡轮叶片表面温度采集等。
超声红外热成像检测系统主要包括超声激励装置、红外热像仪、图像控制和处理系统、被测试件共4部分。
其检测原理是以超声波发生器产生的高频超声波(20~40 kHz)作为激励源,将高频超声波耦合到涡轮叶片内部,当高频超声波传播到涡轮叶片裂纹位置时,裂纹位置处由于塑性变形、摩擦作用、粘弹性效应等产生热量,温度升高;又由于三维热扩散,热量可从裂纹位置传播到涡轮叶片表面对应的位置,利用红外热像仪采集涡轮叶片表面的红外序列图像,对红外序列图像进行处理便可得到内部或者表面裂纹信息。
红外热成像技术中常用的热激励方式包括闪光灯激励、激光激励、卤素灯激励、超声激励等。超声激励相对于其他激励方式,有如下特点:
① 属于选择性激励,仅对裂纹缺陷区域激励,对非裂纹区域不激励,可避免缺陷周围热波信号的干扰;
② 不用考虑热激励均匀性,对复杂异形结构试件可以取得较好的检测效果;
③ 属于内部激励、体激励方式,而热激励是通过摩擦生热,发热区域比实际裂纹区域要大。因此,超声激励方式将有助于微小裂纹的检测。
2、试验系统与试验制备
No.1 超声红外热成像系统
超声红外热成像系统主要由超声激励系统、红外热像仪、预紧力系统、夹具、图像处理与控制系统组成;其中超声激励系统包括超声枪(由工具杆、换能器、调幅杆、枪头组成)和超声电源。红外热像仪型号为FLIR A655sc,属于非制冷型红外热像仪,工作波段为7.5~14 μm,室温下等效噪声温差为0.04 K,图像分辨率为640×480。超声激励系统最大功率为1200 W,超声频率为20 kHz,超声系统激励时间为0.2~20 s。预紧力系统通过旋转预紧力手柄迫使预紧力单元向前移动,内部弹簧挤压对超声枪头产生压力,预紧力可调范围为0~1000 N。夹具用于将超声换能器的能量耦合到涡轮叶片中,使涡轮叶片中的声场均匀分布,呈混沌状态,需要在激励头与叶片间施加恒定的初始静力。夹具需承受一定的预紧力,同时还需保护受检叶片不受损伤。
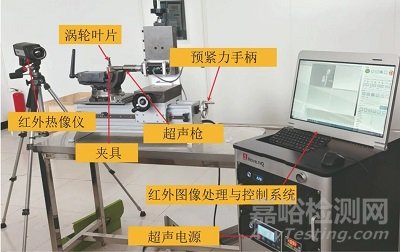
图1 超声红外热成像系统
No.2 涡轮叶片
涡轮叶片是航空发动机的核心组成部件,采用高温合金制造,对叶片表面喷涂耐高温、耐磨涂覆层后,更能延长其在极端环境中的寿命。选取某涡轮叶片,该叶片存在一处裂纹,喷涂前后涡轮叶片的光学图像如下图所示,光学图像仅显示试件裂纹区域的局部轮廓,涂覆层为镍铬铝钇材料(采用等离子喷涂工艺)。
图2 喷涂前后涡轮叶片的光学图像
3、试验与结果分析
超声波在涡轮叶片内部传播,遇到裂纹缺陷时,发生散射,使得裂纹两边界面产生振动,裂纹位置处产生热量,温度升高。在超声激励时间内,裂纹位置温度持续升高并向周围热扩散,在裂纹位置处形成亮斑,实际裂纹尺寸比亮光斑区域要小。超声最大功率为1200 W,激励频率为20 kHz,激励时间为0.5 s,红外热像仪分辨率为640×480,采集频率为50 Hz,采集时间为2 s,共采集100帧图像。超声激励后裂纹以光斑的形式显示出来,在实际检测过程中,预紧力大小和超声激励位置对检测结果影响比较大,需要通过多次试验确定预紧力大小和超声激励位置,最终预紧力大小设置为200 N。
1)涡轮叶片喷涂前检测
在超声激励前采集背景图像(下图中0 s对应的图像),此时叶片基本处于稳态,叶片表面温度基本一致,看不出缺陷信息;超声激励后,裂纹区域温度开始升高,随着持续加载超声激励,裂纹区域温度持续升高,形成亮斑区域,伴随三维热扩散,裂纹区域亮斑逐渐增大,约至0.6 s时,裂纹亮斑区域达到最大,之后亮斑逐渐变暗直到消失。由于温升比较小,直接采用原始图像不容易看出裂纹缺陷信息,采用背景差分法,对原始图像进行减背景图像操作,可以得到温升信息,很好地识别出缺陷信息。
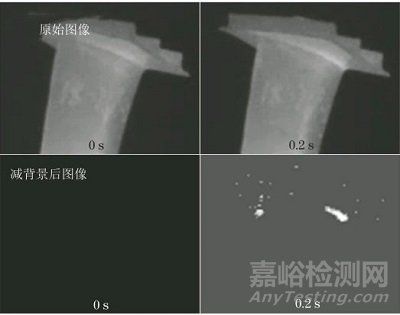
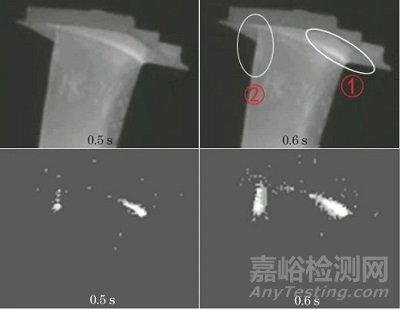
图3 涡轮叶片喷涂前的红外序列图像
从图3(图中上部分为原始图像,下部分为相应的减背景后图像)可以看出,未激励图像减去背景信息,温升图像为全黑,从0.2,0.5,0.6 s的温升图像可以看出,该叶片含有两处裂纹缺陷,且裂纹区域面积逐渐增加。裂纹缺陷①为进气边与上缘板转接R处裂纹,缺陷②为排气边与上缘板转接R处裂纹。
2)涡轮叶片喷涂后检测
涡轮叶片喷涂镍铬铝钇涂覆层后,采用上述同一系统、相同参数对其进行超声红外热成像检测,检测结果如图4所示,0 s时为背景图像,此时还未进行超声激励;超声激励后,裂纹区域温度开始升高,此时裂纹不在表面,而是在涂层之下。超声持续激励过程中,裂纹区域近似于一个热源,持续生热,由于三维热传导,热量传播到裂纹区域相对应的涂层表面位置,于是涂层表面出现亮斑。对比0.2,0.5,0.6 s的红外图像,裂纹区域对应的亮斑面积逐渐增大。依然采用背景差分法处理图像使裂纹缺陷区域更加明显。
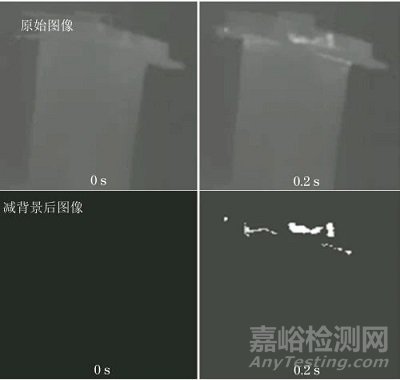
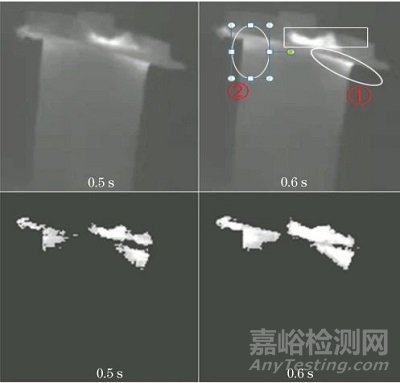
图4 涡轮叶片喷涂后的红外序列图像
由图4可知,上缘板肋板区域有亮斑,图中矩形框对应的区域为等离子喷涂区域的边缘,在超声激励下,涂层喷涂不均和喷涂不牢,以及涂层粘接不牢也会形成亮斑区域。涂层粘接不牢一般呈现区域性,热斑区域呈面分布;裂纹一般较细,热斑区域更多呈线分布,需要辅助目视检测加以区分。在超声激励过程中,涂层与涡轮叶片产生相对运动,摩擦生热等造成温度升高。从图4可以看出两处裂纹缺陷,裂纹缺陷①为进气边与上缘板转接R处裂纹,裂纹②为排气边与上缘板转接R处裂纹,裂纹区域与喷涂前基本一致。
3)渗透检测效果对比
渗透检测采用荧光渗透剂覆盖在涡轮叶片表面,喷涂前先清洗涡轮叶片,防止杂质影响判定结果。由于表面开口的缺陷区域被荧光渗透液渗透,在清洗去除后依然存在,在涡轮叶片表面喷涂显影剂,在一定的光源下荧光渗透痕迹显示出来,发亮的区域就是缺陷位置。渗透检测只能用于检测试件表面开口缺陷,且要求试件本身具有致密特性。试验采用4级灵敏度(德国凯密特尔981系列)乳化型荧光渗透剂及德国凯密特尔9D4A系列显影剂。
涡轮叶片没有喷涂镍铬铝钇涂覆层前,表面光滑,叶片表面致密性高,采用渗透检测可以发现一处裂纹,是进气边与上缘板R处裂纹,如图5a所示;当涡轮叶片喷涂镍铬铝钇涂覆层后,涂层表面状态相对松散,致密性低,荧光渗透剂可以渗透到涂层内部,清洗不彻底会形成大量的荧光背景而影响评定,当用显影剂显示时,镍铬铝钇涂覆层表面都是亮斑,无法发现缺陷,渗透检测失效,如图5b所示。
图5 涡轮叶片渗透检测结果
4)金相验证结果
制作了涡轮叶片试件,用超声红外热成像技术对该试件完成检测后,采用等离子喷涂法喷涂镍铬铝钇涂覆层,并对比了喷涂前、后叶片的渗透检测结果,同时采用金相显微镜进一步验证。使用金相显微镜对涡轮叶片喷涂后的裂纹缺陷区域进行放大显示,检查需要对涡轮叶片进行剖切。图6为涡轮叶片裂纹①处的基体贯穿裂纹,叶片表面涂层厚度为0.45 mm,裂纹开口宽为8.6 μm。
图6 涡轮叶片裂纹①处显微金相组织
图7为涡轮叶片裂纹②处的基体内部裂纹,裂纹开口宽约0.6 μm,长0.14 mm,表面涂层厚度为0.5 mm。
图7 涡轮叶片裂纹②处显微金相组织
5)结果对比分析
由于试件制作困难,仅使用一个叶片进行试验,试件喷涂前已经存在裂纹,大部分裂纹是喷涂后才出现的。喷涂后产生的叶片裂纹较大概率会延伸到涂层面,涂层面也会产生裂纹;相对于涂层完整的情况,试件检测的难度可能会更大。文章主要验证服役后带涂层叶片的裂纹检测。
对图2所示的某涡轮叶片,采用超声红外热成像技术进行检测,不论是喷涂前,还是喷涂后,均发现了两处裂纹。
渗透检测时,没有喷涂涂层的情况下可以检测到一处表面裂纹信息,喷涂涂层后,无法发现裂纹信息,渗透检测失效。
对喷涂镍铬铝钇涂覆层的涡轮叶片进行剖切,采用金相显微镜技术对检测的两处裂纹进行观察,叶片裂纹①对应的裂纹开口宽度为8.6 μm,叶片裂纹②对应的开口宽度为0.6 μm;进一步验证了采用超声红外热成像技术可实现喷涂前和喷涂后涡轮叶片裂纹缺陷的检测。
结语
选取某涡轮叶片,采用等离子喷涂工艺对该涡轮叶片喷涂了0.5 mm厚的镍铬铝钇涂覆层,开展了涡轮叶片喷涂涂层前、后的超声红外热成像试验。试验结果表明,超声红外热成像技术能检测出叶片喷涂前、后的两处裂纹;采用渗透检测进行对比研究,渗透检测仅能检测出涡轮叶片喷涂前的一处裂纹,无法检测叶片喷涂后的裂纹;最后使用金相显微技术进一步验证,发现两处裂纹信息,与超声红外热成像技术检测出的位置一致,验证了超声红外热成像技术可有效检测喷涂前和喷涂后涡轮叶片裂纹缺陷。
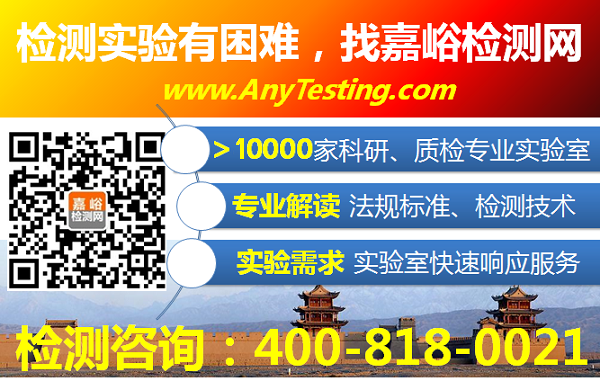